Mit der kontinuierlichen Weiterentwicklung der Plasmaschneidtechnologie ist die Nutzung von CNC-Plasmaschneidmaschinen wird immer weiter verbreitet.
Was ist eine CNC-Plasmaschneidmaschine?
Der CNC-Plasmaschneidmaschine ist eines der wichtigsten Schneid- und Stanzgeräte für Platten mittlerer und geringer Dicke. Es bietet zahlreiche Vorteile, wie einfache Bedienung, hohe Genauigkeit, hohe Arbeitseffizienz und geringe Arbeitsintensität.
Es wird in zahlreichen Branchen eingesetzt, unter anderem in der Chemieindustrie, der Automobilindustrie, dem Maschinenbau und der Schienenverkehrsbranche.
Wenn herkömmliche Schneidverfahren beim Schneiden von zähen Materialien versagen, sind CNC-Plasmaschneidmaschinen praktisch.
Was die Schnittgeschwindigkeit betrifft, ist die CNC-Plasmaschneidgeschwindigkeit beim Schneiden von Kohlenstoffstahlplatten mittlerer und geringer Dicke höher als die herkömmliche Brennschneidgeschwindigkeit und die Schnittoberfläche bleibt glatt mit minimaler Warmverformung.
Darüber hinaus ist das CNC-Plasmaschneidverfahren eine kostengünstigere Option als das Laserschneiden.
Prinzip des Plasmaschneidens
Ein Plasmaschneider funktioniert, indem er ein Gasgemisch durch einen Hochfrequenzlichtbogen ionisiert. Dieses ionisierte Gas oder Plasma wird dann aufgrund des Gasdrucks aus der Schneiddüse ausgestoßen.
Die Temperatur des Plasmas ist extrem hoch und übersteigt den Schmelzpunkt des zu schneidenden Materials bei weitem.
Dadurch schmilzt das Material schnell und das geschmolzene Material wird dann durch das Hochdruckgas aus der Düse weggeblasen. Bei diesem Vorgang entstehen erhebliche Mengen Rauch und geschmolzene Schlacke.
Daher benötigen Plasmaschneider Systeme zur Staub- und Schlackenentfernung. Durch die Verwendung verschiedener Gasgemische kann Plasma Metalle aus verschiedenen Materialien und Stärken schneiden und eignet sich besonders gut zum Schneiden von Nichteisenmetallen.
Auswahl des Plasmaschneidverfahrens
Beim CNC-Betrieb (Computer Numerical Control) mit einem Plasmaschneider ist die Programmierung der erste Schritt. Der Bearbeitungsprozess folgt einer vorprogrammierten Abfolge.
In dieser Programmierphase spielen Faktoren wie Schnittgeschwindigkeit, Schnittreihenfolge und Startpunkt eine entscheidende Rolle für die Qualität des Schnitts.
Auswahl des Startpunktes
Der Startpunkt für den Schnitt sollte idealerweise an der Kante des Blechs oder innerhalb einer zuvor geschnittenen Naht liegen. Wenn die Düse zu weit vom Material entfernt ist, ist der Schnitt unvollständig, was zu unnötiger Materialverschwendung führt.
Umgekehrt kann es bei zu geringer Nähe der Düse zu einem Kurzschluss kommen. Dieser schädigt nicht nur das Material und beeinträchtigt die Schnittqualität, sondern kann auch der Düse schaden.
Die Wahl der Schnittrichtung
Die Schnittrichtung sollte sicherstellen, dass die endgültige Schnittkante weitgehend vom Hauptmaterial getrennt ist.
Bei vorzeitiger Ablösung hält der dünne Rahmen um das Werkstück der thermischen Belastung durch den Schnitt möglicherweise nicht stand, sodass sich das Werkstück während des Prozesses verschiebt. Diese Verschiebung kann zu Maßungenauigkeiten führen und die Schnittqualität beeinträchtigen.
Auswählen der Schnittreihenfolge
Um die Materialausnutzung zu maximieren, wird das Werkstück beim Programmieren häufig innerhalb des Blechs verschachtelt.
Die Schnittfolge bestimmt somit die Reihenfolge des Materialabtrags. Generell folgt die Reihenfolge dem Prinzip, kleinere Teile vor größeren und Innenkonturen vor Außenkonturen zu schneiden.
Andernfalls kann es durch die beim Schneiden von Innenkonturen oder kleineren Teilen entstehende Spannung zu Spannungskonzentrationen kommen und das Werkstück wird zum Ausschuss.
Auswahl der Schnittgeschwindigkeit
Die Wahl der Schneidgeschwindigkeit wird von verschiedenen Faktoren beeinflusst, wie etwa Materialart und -dicke, Düsendesign, Schneidstrom und gewähltes Gas.
Bei gleicher Leistung und gleichen Bedingungen führt eine schnellere Schnittgeschwindigkeit jedoch zu einer größeren Fase am Werkstück.
Daher sollte die Düse beim Schneiden senkrecht zum Material stehen, um eine schnelle Entfernung der Schlacke zu ermöglichen. Um die Effizienz zu gewährleisten, sollte die maximale Schnittgeschwindigkeit gewählt werden, ohne die Schnittqualität zu beeinträchtigen.
Optimierung des Plasmaschneidens
Optimierung des Schneidetisches
Der Schneidetisch der Schneidemaschine wird von mehreren Blenden getragen. Wie in Abbildung 1 dargestellt, beträgt der Abstand zwischen zwei Blenden 110 mm.
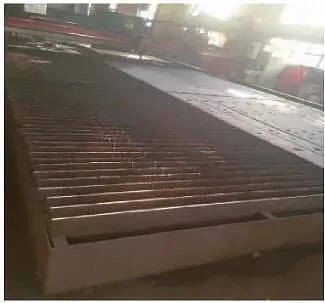
Beim Schneiden kleiner Teile fällt das Werkstück häufig zwischen die Membranen, sodass es nur schwer wieder herausgeholt werden kann. Die Membran selbst ist eine gerade, flache Stahlplatte mit den Abmessungen 8 mm × 190 mm × 4600 mm. Durch häufiges Schneiden sammelt sich in der unteren Membran eine erhebliche Menge an Oxidschlacke an, was sich negativ auf die Schnittqualität auswirken kann. Daher muss sie häufig gereinigt oder ausgetauscht werden, um den normalen Schneidbetrieb aufrechtzuerhalten.
Optimierungsschema und Implementierung des Schneidearbeitstisches
In der Industrie sind Produktstrukturen und Chargen oft nicht festgelegt, sodass zur Materialeinsparung Nesting eingesetzt wird. Dabei wird der Satz großer und kleiner Materialien aufeinander abgestimmt.
Derzeit müssen wir uns mit der Frage befassen, wie wir durch Prozessinnovationen im Plasmaschneidbereich die Auslastung von Plasmaschneidmaschinen steigern und die Lebensdauer von Schneidtischen verlängern können.
Um diese Herausforderung zu meistern, analysieren und kategorisieren wir zunächst die vorhandenen Stanzprodukte. Anschließend wählen wir das kleinste Schneidteil aus, bestimmen seine Größe und entwerfen ein neues Werkbankset entsprechend den Bedingungen vor Ort, wie in Abbildung 2 dargestellt.
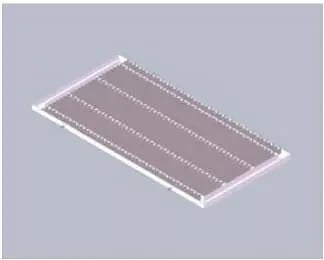
(1) Besondere Regelung.
Die Plattform hat eine Größe von 1500mm x 3000mm und kann mit mehreren Plattformen kombiniert werden.
Der Außenrahmen der Plattform besteht aus 4 mm starken Platten, die in U-förmige Teile gefaltet und zu einer rechteckigen Rahmenstruktur verschweißt sind. Diese Konstruktion gewährleistet die Steifigkeit des Rahmens und verhindert Verformungen beim Anheben.
Im Inneren des Rahmens befinden sich 2-3 V-förmige Teile, die durch 4mm starke Bleche gefaltet und längs im Rahmen eingeknickt sind. Zusätzlich ist am Längsträger eine 3,5mm breite Kerbe angebracht, um das Einlegen der Membrane zu erleichtern.
Die Membran besteht aus einer 1500 mm x 200 mm großen Platte, die auf einer Seite eine gezackte Struktur aufweist.
(2) Konkreter Umsetzungsprozess.
Konstruieren Sie Länge, Breite, Höhe und Trennwandabstand der Schneidwerkbank entsprechend den Geräteparametern und der Größe der benötigten Schneidteile.
Fertigen Sie die Schneidwerkbank nach der Konstruktionszeichnung an.
Alle Teile des Schneidetisches werden mithilfe einer CNC-Schneidemaschine auf einmal ausgeschnitten, wodurch genaue Größen erreicht werden und die Membran bequem ausgetauscht werden kann.
Der Schneidetischrahmen wird mithilfe einer CNC-Biegemaschine programmiert und gebogen, wodurch eine genaue Positionsgröße und eine gute Formbarkeit erreicht werden.
Den Rahmen der Schneidwerkbank zusammenbauen, schweißen und konstruieren.
Legen Sie die Membran in den Schneidetisch ein.
Platzieren Sie den Schneidetisch auf dem Original-Schneidetisch. Legen Sie das Material beim Schneiden auf den beweglichen Schneidetisch, wie in Abbildung 3 gezeigt.
Physische Zeichnung des Arbeitstisches nach der Optimierung der CNC-Plasmaschneidmaschine
Abb. 3 Physikalische Zeichnung des Arbeitstisches nach der Optimierung der CNC-Plasmaschneidmaschine
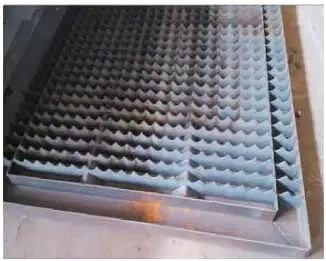
Bahnoptimierung im Schneidprozess
Während des Schneidvorgangs kommt es aufgrund der Wärmeausdehnung und Kaltkontraktion der Platte zu einer Relativbewegung zwischen dem bearbeiteten Teil und dem verbleibenden Material.
Die Relativbewegung kann basierend auf der Differenz zwischen dem Gewicht des bearbeiteten Teils und dem Gewicht des verbleibenden Materials in drei Situationen eingeteilt werden:
Wenn das Gewicht des bearbeiteten Teils größer ist als das Gewicht des restlichen Materials, bleibt das bearbeitete Teil stationär, während sich das restliche Material relativ zur Plattform bewegt. Dies hat keine Auswirkungen auf die Größe des bearbeiteten Teils.
Wenn das Gewicht des bearbeiteten Teils geringer ist als das Gewicht des restlichen Materials, bewegt sich das bearbeitete Teil relativ zur Plattform, während das restliche Material stationär bleibt. Dies führt zu einer gewissen Abweichung im bearbeiteten Teil.
Wenn das Gewicht des bearbeiteten Teils dem Gewicht des verbleibenden Materials entspricht, können sich sowohl das bearbeitete Teil als auch das verbleibende Material relativ zur Plattform bewegen, was die Größe des bearbeiteten Teils beeinträchtigen kann.
Die Praxis hat gezeigt, dass der Maßfehler bei bearbeiteten Teilen aufgrund der Relativbewegung des bearbeiteten Teils oder des verbleibenden Materials in Bezug auf die Plattform typischerweise zwischen 0,3 und 4 mm liegt.
Optimierung von Plasmaanlagen
Beim Schneidvorgang mit Luftplasma kommt es an der Oberseite des Elektrodenkerns zu einer Hochtemperatur-Oxidationsreaktion mit dem Sauerstoff der Luft, wodurch ein Elektrodenverschleiß unvermeidbar ist.
Die Lebensdauer einer Elektrode hängt von der Anzahl der Lichtbogenzündungen ab. Unter gleichen Bedingungen gilt: Je häufiger die Lichtbogenzündungen, desto stärker verschleißt die Elektrode. Häufige Lichtbogenzündungen verkürzen die Lebensdauer der Elektrode erheblich.
Der kontinuierliche Schneidprozess reduziert jedoch die Anzahl der Startpunkte für Werkstücke mit nicht gemeinsamer Kante, sodass Werkstücke mit gemeinsamer Kante nur einen Schneidstartpunkt haben.
Dadurch wird die Anzahl der Lichtbogenzündungen beim Schneiden verringert und die Lebensdauer der Elektrode erhöht.
Abschluss
Die Prozessinnovation hat mehrere positive Auswirkungen. Erstens verbessert sie die Auslastung der Plasmaschneidmaschine erheblich. Zweitens ist der Austausch der Arbeitstischmembran bequem und reduziert die Austauschrate um die Hälfte, wodurch die Austauschkosten gesenkt werden. Drittens kann sie den Schneidanforderungen kleiner Teile gerecht werden.
Derzeit wird diese Prozessinnovation häufig beim Stanzen von Stahlkonstruktionen für Eisenbahnwaggons eingesetzt. Da jeder Waggon viele kleine Teile hat, die geschnitten und gestanzt werden müssen, verbessert diese Innovation die Arbeitseffizienz und spart Kosten.
Beim Plasmaschneiden sollten die folgenden Probleme berücksichtigt werden: Das Verformungsgesetz und der Einfluss der Schneidteile von CNC-Plasmaschneidmaschinen sollten analysiert werden. Vor dem Schneiden sollte eine geeignete Plattennivellierungsbehandlung durchgeführt und die Platte fixiert werden, um die Bewegung der bearbeiteten Teile während des Schneidens zu verhindern.
Beim Erstellen des Schneidprogramms sollte ein angemessener Schneidprozess ausgewählt werden, um die maximal große Oberfläche des Werkstücks von der Hauptplatine zu trennen. Beim Schneiden schlanker oder speziell geformter Teile können Steuerungsmethoden wie das zweiteilige Paarschneiden die Verformung der Schneidteile wirksam verhindern oder verringern.
Im Vergleich zum Brennschneiden ist das CNC-Plasmaschneiden hinsichtlich Schnittqualität und Nutzen in der verarbeitenden Industrie überlegen. Es kann mit unterschiedlichen Arbeitsgasen alle Arten von Metallen schneiden, insbesondere Nichteisenmetalle.