Seit der Blechwalzmaschine Da es während des Betriebs erheblichen Belastungen ausgesetzt ist, ist es während der Verwendung anfällig für verschiedene Fehler. Im folgenden Abschnitt werden zwei häufige Fehler und ihre jeweiligen Lösungen erläutert.
Bruch und Reparatur der Hauptwelle einer Blechwalzmaschine
A 50×3000 Blechwalzmaschine In einer Maschinenfabrik traten nach einem Jahr Betrieb Risse an der Hauptwelle auf. Bei der Durchführung einer Ultraschall-Fehlerprüfung wurde festgestellt, dass die Struktur der Hauptwelle in zwei Teile geteilt war: einen geschmiedeten Abschnitt und einen gegossenen Abschnitt, der nicht dem nationalen Standard für die Fehlerprüfung der Klasse II entsprach.
Um die Schadensursache genauer zu ermitteln, sezierte das Wartungspersonal die Hauptwelle und stellte fest, dass die Erkennungsergebnisse genau waren. Nach ihrer Analyse kam man zu dem Schluss, dass der Hauptgrund für den Bruch der Hauptwelle schlechte Schweißarbeiten waren. Der Schweißbereich war klein, der Prozess war grob und es gab Schweißschlackeneinschlüsse, was zu Mängeln mit geringer Festigkeit führte.
1.1 Reparaturschema.
Aufgrund der Spannungsbedingungen der Hauptwelle haben wir eine Stumpfschweißtechnik verwendet. Dazu wurden an der Schweißstelle zwei U-förmige Nuten angebracht und in der Mitte der gebrochenen Welle jeweils eine Vertiefung und ein Vorsprung mit einer Toleranzpassung von H7/H7 bearbeitet.
Um die Koaxialität der Schweißnaht sicherzustellen, wurden als Teil der Konfiguration ein V-förmiger Kalibrierblock und ein Ring mit gleichem Durchmesser entworfen.
1.2 Schweißmaterialien und -verfahren.
Bei der Überprüfung des Hauptwellenmaterials mithilfe von Prüfgeräten wurde festgestellt, dass es aus Stahl Nr. 45 besteht. Dieser Stahl weist jedoch eine schlechte Schweißleistung auf, was beim Schweißen zahlreiche Herausforderungen mit sich bringt.
Aufgrund des großen Durchmessers der Hauptwelle ist außerdem vor dem Schweißen ein Vorwärmen erforderlich. Als Schweißgerät wird das Kohlendioxid-Schutzgasschweißgerät XC500 verwendet. Der verwendete Schweißdraht ist ER50-6 mit einem Durchmesser von 1,2 mm.
Während des Schweißvorgangs wird die Spannung bei etwa 35 V gehalten, der Strom reicht von 220–250 A und die Geschwindigkeit beträgt zwischen 15–25 cm/min.
Um eine vollständige Durchdringung der Hauptwelle zu gewährleisten, muss die Geschwindigkeit während der anfänglichen Schweißphase verringert werden und es sollte die geradlinige Streifentransportmethode angewendet werden. Mit zunehmender Breite der Nut sollte die Schweißbewegung in eine Sägezahnform geändert werden, um die Verformung zu minimieren.
Darüber hinaus sollte die Schweißung von zwei Personen gleichzeitig durchgeführt werden, wobei abwechselnd eine Aufwärts- und eine Abwärtsrotation erfolgen sollte.
1.3 Schweißen.
Vor dem Schweißen müssen einige Vorbehandlungsschritte durchgeführt werden.
Zunächst muss die Hauptwelle demontiert werden und es müssen bestimmte Bearbeitungsvorgänge, wie z. B. Vertiefungen und Nuten, an der Hauptwelle gemäß den Zeichnungen durchgeführt werden. Auch die beiden gebrochenen Wellen müssen auf ordnungsgemäße Montage geprüft werden.
Um zu verhindern, dass Schweißschlacke die Baugruppe beeinträchtigt, muss der Bereich in der Nähe der Schweißnaht mit einem Schlackenentferner gereinigt werden, um die bei der Bearbeitung entstehende Schlacke zu entfernen.
Anschließend werden die gebrochenen Wellen auf die Bohrmaschine T20 gelegt und mithilfe eines V-förmigen Kalibrierblocks ausgerichtet, um den horizontalen Höhenunterschied auszugleichen. Anschließend werden die beiden Wellen mithilfe einer Rolle verbunden und mithilfe eines Schneidlineals auf Koaxialität geprüft. Feineinstellungen werden mithilfe eines dünnen Kupferblechs vorgenommen, um sicherzustellen, dass der Koaxialitätsfehler 0,05 mm nicht überschreitet.
Zum Schluss werden die vier Enden noch mit Winkeleisen verstärkt.
Um die Verformung der Hauptwelle während des Schweißens zu verringern, wird die Methode verwendet, bei der zwei Personen gleichzeitig schweißen. Die auf der Hauptwelle installierte Rolle wird symmetrisch in vier Positionen geschweißt: oben, unten, links und rechts, wobei die Schweißlänge allmählich zunimmt.
Nach jedem Schweißvorgang muss die Schweißschlacke umgehend entfernt und die Schweißspannungen durch Abklopfen der Schweißnaht gelöst werden.
Um die Koaxialität sicherzustellen, sollte das Schweißen bei Erreichen von 3/5 der Nuttiefe gestoppt und die Koaxialitätsabweichung überprüft werden, um die Richtung der nächsten Biegung zu bestimmen. Die Spindel kann durch entsprechendes Erhöhen der Länge des Schweißlichtbogens und des Stroms begradigt werden.
1.4 Wirkung.
Statistiken zeigen, dass nach dieser Spindelreparatur in den letzten drei Jahren keine Risse in der Spindel aufgetreten sind.
Der gesamte Schweißreparaturprozess dauerte vier Tage und erforderte 15 kg Schweißdraht. Die Gesamtkosten der Reparatur, einschließlich Bearbeitungs- und Materialkosten, betrugen 5788 Yuan.
Der Kauf einer neuen Spindel würde 220.000 Yuan kosten und 35 Tage für Transport und Installation benötigen.
Im Vergleich dazu spart eine Spindelreparatur nicht nur Kosten, sondern reduziert auch den Zeitaufwand und erhöht die Effizienz.
Reparatur eines Motorausfalls an einer Blechwalzmaschine
Eine in Italien hergestellte Dreiwalzen-Druckplattenbiegemaschine Em040-160 stellte während des Betriebs plötzlich den Betrieb ein.
Bei der Überprüfung stellte sich heraus, dass das elektrische Signal normal war, und zunächst wurde festgestellt, dass es sich um ein mechanisches Problem handelte.
Der Wartungsarbeiter entfernte zunächst den Motor vom Ende der oberen Walze und drehte die Eingangswelle des Untersetzungsgetriebes der oberen Walze manuell, um zu bestätigen, dass das Untersetzungsgetriebe ordnungsgemäß funktionierte.
Beim Zerlegen des Motors wurde festgestellt, dass die bewegliche Abdeckplatte an der Stirnseite der Ölverteilerplatte an der Öleinlassseite des Motors gebrochen war und der Dichtungsring unter der Abdeckplatte ebenfalls beschädigt war. Die durch die Beschädigung entstandenen Rückstände waren in den Kolben eingedrungen, wodurch Öl sowohl innerhalb als auch außerhalb der Ölverteilerplatte kanalisiert wurde, was die Erzeugung von Arbeitsdruck verhinderte.
Der in dieser Biegemaschine verwendete Hydraulikmotor ist ein importierter Fünfstern-Radialkolbenmotor der Marke Sai S7b3000. Der Kauf neuer Motorteile beim Hersteller wäre zeitaufwändig und teuer.
Daher hat die Gerätewartungsabteilung beschlossen, den Motor intern zu reparieren, basierend auf der Produktionsaufgabe und dem Produktionsfortschritt der Fabrik.
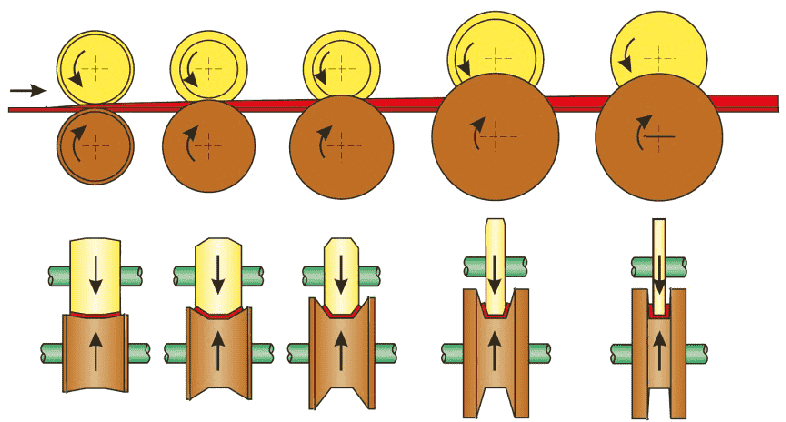
Eine neue bewegliche Abdeckplatte wurde auf die Größe der Ölverteilerplatte zugeschnitten und ein Dichtungsring wurde aus einem Öldichtungsmittel bezogen. Die ursprünglichen Dichtungen waren ein O-Ring und ein Ring mit kreisförmiger Nut.
Allerdings verfügte das Mittel nur über O-Ringe und Gleitringe, wobei die Originalgrößen 2,5 und 1,9 mm betrugen und die verfügbaren Größen 2,5 und 1,4 mm waren, welche für den Einsatz nicht geeignet waren.
Als Lösung wurde anstelle des 1,9-mm-Sicherungsrings ein 3-mm-Sicherungsring verwendet. Da die Öldichtungsnut der Ölverteilungsplatte 3,6 mm tief und 3,2 mm breit war, hatte der 3,0-O-Ring einen kleinen Spalt in der Nut zur Kompression, und der 1,4-Ebenen-Sicherungsring konnte sicher in der Nut platziert werden.
Der Motor wurde zusammengebaut und die Maschine zurückgesetzt, so dass sich die obere Walze frei drehen konnte. Nach einem Monat Betrieb funktionierte der Motor immer noch normal.