Wartung von Hydrauliksystemen, insbesondere bei großen Biegemaschinen, übersteigt die Komplexität des Hydrauliksystems bei weitem die Vorstellungskraft der Menschen. Daher ist die Wartung solcher Geräte ein Problem, das das Wartungspersonal beunruhigt. Der Autor verwendet eine bestimmte Art von hydraulische Abkantpresse als Beispiel. Basierend auf der Analyse der häufigsten Ursachen von Maschinenausfällen werden beispielsweise einige Wartungstechniken anhand von Beispielen veranschaulicht.
Aufbau des Hydrauliksystems einer hydraulischen Abkantpresse?
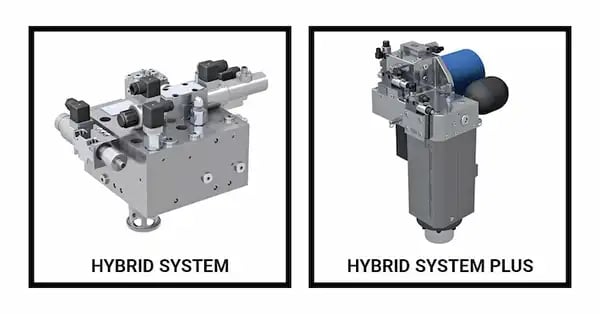
A hydraulische Abkantpresse ist eine Werkzeugmaschine zum Biegen von Blechen und Plattenmaterial. Ihr Hydrauliksystem spielt eine entscheidende Rolle bei der Durchführung des Biegeprozesses. Das Hydrauliksystem einer Abkantpresse besteht typischerweise aus mehreren Schlüsselkomponenten:
1. Hydraulikpumpe: Die Hydraulikpumpe ist für die Erzeugung von Hydraulikdruck verantwortlich, indem sie mechanische Energie (normalerweise von einem Elektromotor) in hydraulische Energie umwandelt. Sie liefert unter Druck stehende Hydraulikflüssigkeit an das System.
2. Hydraulikflüssigkeit: Hydraulikflüssigkeit, häufig Öl, wird zur Druckübertragung innerhalb des Hydrauliksystems verwendet. Sie muss gute Schmiereigenschaften und Beständigkeit gegen thermischen Abbau aufweisen.
3. Hydraulikbehälter: Der Behälter speichert die Hydraulikflüssigkeit und ermöglicht die Ableitung der während des Betriebs erzeugten Wärme. Er hilft auch dabei, Verunreinigungen aus der Flüssigkeit herauszufiltern.
4. Hydraulikventile: Verschiedene Arten von Hydraulikventilen steuern den Durchfluss und die Richtung der Hydraulikflüssigkeit im System. Zu diesen Ventilen gehören Wegeventile, Druckregelventile, Durchflussregelventile und Proportionalventile.
5. Hydraulikzylinder: Hydraulikzylinder sind die Antriebe, die für die Kraftausübung auf den Stößel oder Balken der Abkantpresse verantwortlich sind, der wiederum das Metall biegt. Diese Zylinder arbeiten nach dem Prinzip des hydraulischen Drucks, der auf einen Kolben in einem Zylinder wirkt.
6. Hydraulikleitungen und -schläuche: Dies sind die Kanäle, durch die die Hydraulikflüssigkeit zwischen den verschiedenen Komponenten des Hydrauliksystems wie Pumpe, Ventilen, Zylindern und Behälter fließt.
7. Überdruckventil: Das Überdruckventil ist eine Sicherheitsfunktion, die verhindert, dass das Hydrauliksystem seinen maximalen Druck überschreitet, und so die Komponenten vor Schäden schützt.
8. Steuerungssystem: Das Steuerungssystem der hydraulischen Abkantpresse umfasst elektronische Komponenten wie Sensoren, Schalter und eine speicherprogrammierbare Steuerung (SPS), die den Betrieb des Hydrauliksystems basierend auf Benutzereingaben und programmierten Parametern regeln.
Diese Komponenten arbeiten zusammen, um Hydraulikdruck zu erzeugen und zu steuern, sodass die Abkantpresse Metall gemäß den gewünschten Spezifikationen präzise biegen kann. Die ordnungsgemäße Wartung und Überwachung des Hydrauliksystems sind für den effizienten und sicheren Betrieb der Abkantpresse unerlässlich.
Wie funktioniert das Hydrauliksystem einer hydraulischen Abkantpresse?
Das Hydrauliksystem funktioniert nach den Prinzipien der Strömungsmechanik und dem Pascalschen Gesetz. Hier ist eine vereinfachte Erklärung der Funktionsweise:
1. Hydraulikpumpe: Der Prozess beginnt mit einer Hydraulikpumpe, die normalerweise von einem Elektromotor oder einem Verbrennungsmotor angetrieben wird. Die Pumpe saugt Hydraulikflüssigkeit (normalerweise Öl) aus einem Behälter an und setzt sie unter Druck.
2. Unter Druck stehende Hydraulikflüssigkeit: Die unter Druck stehende Hydraulikflüssigkeit wird dann durch Hydraulikleitungen oder -schläuche zu verschiedenen Hydraulikkomponenten im System gedrückt.
3. Hydraulikzylinder: Wenn Hydraulikflüssigkeit in einen Hydraulikzylinder geleitet wird, tritt sie in eine Seite des Zylinders ein und übt Druck auf einen Kolben oder Stößel im Inneren aus. Der auf diesen Kolben ausgeübte Druck erzeugt eine Kraft, die den Kolben und jede daran befestigte Last bewegen kann. Hydraulikzylinder werden häufig als Antriebe in Maschinen verwendet, um lineare Bewegungen zu erzeugen.
4. Steuerventile: Steuerventile im Hydrauliksystem regeln den Durchfluss der Hydraulikflüssigkeit und steuern die Bewegungsrichtung hydraulischer Antriebe, wie z. B. Zylinder. Diese Ventile können je nach Anwendung manuell oder automatisiert betrieben werden.
5. Rücklaufleitung: Nachdem die Hydraulikflüssigkeit ihre Arbeit verrichtet hat, fließt sie über eine Rücklaufleitung zurück in den Behälter. Dadurch kann die Hydraulikflüssigkeit innerhalb des Systems wieder in Umlauf gebracht werden.
6. Druckbegrenzungsventil: Normalerweise wird im Hydrauliksystem ein Druckbegrenzungsventil installiert, um einen übermäßigen Druckaufbau zu verhindern. Wenn der Druck einen vorgegebenen Grenzwert überschreitet, öffnet sich das Begrenzungsventil, sodass überschüssige Flüssigkeit umgeleitet und in den Behälter zurückgeführt werden kann. Auf diese Weise wird das System vor Schäden geschützt.
7. Filter und Behälter: Das Hydrauliksystem enthält oft einen Filter, der Verunreinigungen aus der Hydraulikflüssigkeit entfernt, einen reibungslosen Betrieb gewährleistet und die Lebensdauer der Komponenten verlängert. Der Behälter speichert die Hydraulikflüssigkeit und hilft, während des Betriebs erzeugte Wärme abzuleiten.
8. Insgesamt wandelt das Hydrauliksystem mechanische Energie durch die Pumpe in hydraulische Energie um, die dann zur Erzeugung von Kräften und Bewegungen durch hydraulische Antriebe wie Zylinder verwendet wird. Dieses System wird aufgrund seiner Fähigkeit, eine hohe Leistungsdichte, präzise Steuerung und Vielseitigkeit zu bieten, in verschiedenen Anwendungen eingesetzt, darunter Schwermaschinen, Automobilsysteme, Industrieanlagen und mehr.
9. Analyse der Ursachen für den Ausfall des hydraulischen Steuersystems
Der häufigste Fehler des Hydrauliksteuersystems besteht darin, dass die Schieberdruckkraft unzureichend ist und die Rücklaufgeschwindigkeit langsam ist, wenn der Hydraulikzylinder unter Druck steht. Dieser Fehler führt nicht nur dazu, dass die Handhabungsleistung des Hydrauliksystems stark reduziert wird, sondern verschlechtert auch die Stabilität des gesamten Systems. Weitere Fehler in der Reihe. Die Hauptgründe für solche Fehler sind folgende: Erstens sind der Kolben und die Endkappe des Hydraulikzylinders nicht gut abgedichtet, was zu schweren Undichtigkeiten innerhalb und außerhalb des Zylinders führt. Der Grund, warum das Hydrauliksystem die Funktion nicht ausführen kann, besteht darin, dass der Hydraulikzylinder die Flüssigkeit unter Druck setzt, wodurch der Kolben oder die Endkappendichtung nicht richtig funktionieren. Die Flüssigkeit im Hydraulikzylinder tritt aus und der Innendruck wird niedriger. Der Strand führt normale externe Arbeit aus, was zu einer erheblichen Verringerung der Effizienz des Hydrauliksystems oder sogar zu einer vollständigen Lähmung führt. Zweitens reguliert das Überdruckventil unzureichenden Druck. Die Hauptfunktion des Überdruckventils besteht darin, die Funktionskraft des Hydrauliksystems zu steuern, indem das Überdruckventil so eingestellt wird, dass die nach außen gerichtete Ausgabe der unter Druck stehenden Flüssigkeit gesteuert wird, wenn die Flüssigkeit im Hydraulikzylinder auf den Arbeitsdruck gebracht wird. Wenn ein Problem mit der Druckregulierung vorliegt, ist die Einstellung im Allgemeinen niedrig, sodass die anderen Teile nicht die für den normalen Arbeitsschritt erforderliche Energie erhalten. Dann besteht das Problem, dass die Gleitkraft des Schiebers nicht ausreicht und die Rücklaufgeschwindigkeit langsam ist. Wenn die Einstellung jedoch zu hoch ist, nimmt der Verschleiß des Schiebers zu und der Schaden am Hydrauliksystem wird schwerwiegender. Drittens ist die Oberfläche der männlichen Ventilspule stark abgenutzt, was zu einem dichten Verschluss am Ventilanschluss führt. Das Kegelventil ist ein wichtiger Bestandteil der Aufrechterhaltung der hydraulischen Stabilität im System und eine „robuste Verteidigungslinie“, die den internen und externen Druckaustausch blockiert. Wenn die Kegelventilspule ausfällt, führt dies zu einem Austreten von Flüssigkeit mit hohem Druck im Inneren und einem Ausfall des Schiebers. Die Oberfläche des Ventilkörpers des vierten Umkehrventils ist abgenutzt, was die Bewegung des Ventilkerns im Ventilkörper erschwert. Der Einwegverschluss des Ventils ist nicht streng oder der Spalt zwischen der Ventiloberfläche und dem Ventilkörper ist zu groß. Infolgedessen führt das Austreten von Innendruck auch zu einer Fehlfunktion des Schiebers.
10. Methode und Schlussfolgerung zur Diagnose von Hydraulikfehlern
Unmittelbar nach dem Ausfall des hydraulischen Betriebssystems müssen die Fehlersuche, -bestimmung und -wartungsarbeiten eingestellt werden. Zur Fehlererkennung gibt es hauptsächlich die folgenden Methoden: Die erste Methode. Die Beobachtungsmethode dient hauptsächlich dazu, das Druckmessgerät und den Hydraulikzylinder des hydraulischen Steuersystems zu überprüfen, um zu prüfen, ob der Anzeigedruck des Hydraulikmessgeräts normal ist, wodurch die Fehlerursache und die Fehlerrichtung ermittelt werden. Die Beobachtung des Hydraulikzylinders dient hauptsächlich dazu, festzustellen, ob der Hydraulikzylinder leckt. Denn das Austreten von Flüssigkeit hinterlässt eine sehr sichtbare Spur oder wird von Geräuschen begleitet. Wenn das Hydraulikmessgerät niedrig ist oder eine Spur einer offensichtlichen Leckage vorhanden ist, kann festgestellt werden, dass der Hydraulikzylinder defekt ist, und es können sofort Reparaturarbeiten durchgeführt werden. Die zweite Methode wurde beobachtet und es wurden keine offensichtlichen Fehler oder Fehler gefunden, die nicht direkt mit dem Auge erkennbar waren, wie z. B. Verschleiß des Ventilkerns oder Perlen. Zur Erkennung müssen Instrumente wie optische Bildgebungsgeräte oder Partikelstrahl-Fehlerdetektoren verwendet werden. Diese Art von Instrument kann Fehler wie Fehlausrichtung oder Verschleiß im Hydrauliksystem erkennen, indem es hochenergetische Partikel aussendet.
11. Entsorgungsmethode für Hydraulikzylinderlecks
Da der Hydraulikzylinder das Herzstück des gesamten hydraulischen Steuersystems ist, müssen Wartungsmaßnahmen ergriffen werden, sobald Flüssigkeit und Druck austreten. Im Allgemeinen werden zwei Methoden angewendet: Schweißen und Austauschen. Die Schweißmethode ist hauptsächlich für leichte Risse oder kleine Löcher im Hydraulikzylinder geeignet. Beim Schweißen sollte eine Kombination aus Innen- und Außenschweißen angewendet werden, um sicherzustellen, dass das Schweißen vollständig ist. Insbesondere muss darauf geachtet werden, dass während des Schweißvorgangs die Restspannung beseitigt wird, da sonst der Schaden an der Schweißverbindung sehr groß wird. Bei unsachgemäßer Handhabung kann der Fehler nicht nur repariert werden, sondern er wird noch schwerwiegender. Bei der Austauschmethode müssen nur die defekten Hydraulikzylinderanschlüsse ausgetauscht werden. Diese Entsorgungsmethode ist jedoch einfach, aber kostspielig. Diese Entsorgungsmethode ist nur möglich, wenn ein großer Fehler vorliegt, der in kurzer Zeit nur schwer zu reparieren ist.
12.Fazit
Das Hydrauliksystem der hydraulischen Biegemaschine ist kompliziert, so dass auch die Fehlersuche schwierig ist. Das Gesichtsreparaturpersonal muss