Die Bedeutung von Brennpunktpositionen in Laserschneiden Operationen können nicht genug betont werden, da sie die Qualität, Effizienz und Präzision des Schneidprozesses direkt beeinflussen. Die Brennposition bezieht sich auf den genauen Punkt, an dem der Laserstrahl auf seinen kleinsten Durchmesser konvergiert, den sogenannten Brennfleck. An diesem Punkt liefert der Laserstrahl die maximale Energiedichte und ermöglicht so eine optimale Schneidleistung. Hier sind einige wichtige Gründe, die die Bedeutung der Brennpositionen bei Laserschneidvorgängen unterstreichen:
Fokussierung des Laserschneidens
Fokussierung von Laserstrahlen
Jeder Hersteller hat seine eigene Meinung darüber, was das wichtigste Element ist in Laserschneiden. Glauben Sie, dass es darum geht, die kleinste Punktgröße und eine Linsenausrichtung senkrecht zur Achse des Laserstrahls beizubehalten? Wenn Sie mit „Ja“ geantwortet haben, liegen Sie teilweise richtig, aber es müssen viele andere Faktoren in Bezug auf die Laserstrahleigenschaften und Schneidanwendungen berücksichtigt werden. Die Beibehaltung der Fokuspositionen innerhalb des Materials ist entscheidend für die Wiederholbarkeit der Laserschnittparameter und für die Erzeugung einer gleichbleibenden Kantenqualität.
Wenn Sie beispielsweise mit dicken Materialien arbeiten, ist es tatsächlich notwendig, ein größeres Brennmuster zu erzeugen, um einen breiteren Kanal zu erzeugen, der benötigt wird, um ein größeres Volumen an geschmolzenem Material aufzunehmen, das während des Schneidvorgangs ausgestoßen werden muss. Um dieses vergrößerte Brennmuster zu erzeugen, fokussieren Sie den Strahl je nach Hilfsgas entweder über oder unter der Oberfläche des Materials. Folglich ist die Fokussierung auf einen kleinen Punkt auf der Oberfläche bei dickerem Material normalerweise ein weniger erfolgreicher Ansatz.
Bei dünnerem Material ist jedoch ein kleiner, auf die Materialoberfläche fokussierter Punkt viel effektiver als ein größerer, da weniger Material beteiligt ist und folglich kein breiterer Kanal erforderlich ist.
Ein sehr wichtiger Faktor, der beim Laserschneiden berücksichtigt werden muss, ist die Verwendung eines Hilfsgases wie Sauerstoff, Stickstoff oder Druckluft. Jedes Gas hat spezifische Eigenschaften, die den Brennvorgang beschleunigen, das geschmolzene Material abführen oder beides bewirken.
Beim Laserschneiden unterstützen Hilfsgase zwei spezifische Reaktionen: exotherm oder endotherm. Die Fokussierungsregeln variieren je nach Reaktionstyp und verwendetem Gas.

Fokussierung auf exotherme Reaktionen
Exotherme Reaktionen werden durch die Verwendung eines Gases mit beschleunigenden Eigenschaften wie Sauerstoff erzeugt. Bei dieser Art von Reaktion verdampft – oder bringt buchstäblich – die intensive Energie des Laserstrahls das geschnittene Material, während der Sauerstoff heftig mit dem geschmolzenen Material in seinem flüssigen Zustand reagiert. Beim sauerstoffunterstützten Schneiden unter hohem Druck wird das Grundmaterial auf eine so extrem hohe Temperatur gebracht, dass die Umwandlung des Materials in einen thermischen Dampf nahezu vollständig ist.
Fokussierungsregeln zur Unterstützung exothermer Reaktionen erfordern Fokuspositionen, die bei dicken Materialien über der Oberfläche und bei dünneren Materialien knapp in der oberen Oberfläche liegen.
Wenn der Fokus über dem Material liegt, verwenden Sie normalerweise einen niedrigen Druck und ein niedriges Volumen, um das geschmolzene Material zu verflüssigen und dann auszustoßen (ungefähr 6 bis 8 Pfund pro Quadratzoll bei 40 Kubikfuß pro Stunde). Tatsächlich wird nur sehr wenig Material verdampft, da das kleine Sauerstoffvolumen nicht ausreicht, um eine vollständige Verdampfung zu unterstützen. Wenn der Fokus direkt auf der Oberfläche des Materials liegt, verwenden Sie normalerweise einen hohen Druck und ein hohes Volumen (ungefähr 60 PSI bei 80 CFH). Dies reicht aus, um eine kräftige Verdampfung des Materials zu unterstützen.
Deshalb sieht man bei der Inspektion der meisten Schneidetische, auf denen überwiegend dünneres Material geschnitten wird, nur sehr wenig Material, das sich auf den Tischstützen angesammelt hat. Im Gegensatz dazu ist bei Schneidetischen, die für die Verarbeitung dickerer Materialien verwendet werden, eine viel größere Materialmenge auf den Stützen angesammelt.
Fokussierung für endotherme Reaktionen
Endotherme Reaktionen entstehen dagegen, wenn Sie ein Gas verwenden, das inerte oder nicht reaktive Eigenschaften aufweist. Stickstoff und Argon fallen in diese Kategorie.
Bei dieser Art von Reaktion unterstützt das Gas nur die Evakuierung des geschmolzenen Materials durch den Schnittkanal. Der endotherme Prozess hängt stark von der Rohenergie des fokussierten Laserstrahls ab, um das Grundmetall schnell in einen geschmolzenen Zustand zu bringen und den richtigen Schnittkanal zu erzeugen. Dadurch kann das Inertgas das verflüssigte Material durch den Schnittkanal ausstoßen und eine sauber geschnittene Oberfläche ohne Schlackenanhaftung hinterlassen.
Fokussierungsregeln zur Unterstützung endothermer Reaktionen erfordern Fokuspositionen, die sich am oder knapp unter dem Boden des Materials befinden. Wenn der Fokus unter dem Material gehalten wird, entsteht innerhalb des Schnittkanals eine leichte V-Form, sodass das Hochdruckgas das geschmolzene Material mit hoher Geschwindigkeit durch den Schnittkanal komprimieren und durch die Basis des Kanals ausstoßen kann.
Endotherme Reaktionen erfordern ein hohes Volumen und einen hohen Druck, um eine schnelle Evakuierung des geschmolzenen Materials zu unterstützen. Typische Volumina können bei dünnen Materialien bei 350 CFH beginnen und bei dickeren Materialien mehr als 3.000 CFH erreichen. Der Druck kann bei dünnen Materialien bei 140 PSI beginnen und bei dickeren Materialien auf mehr als 300 PSI ansteigen.
Die Verwendung von Druckluft als Hilfsgas erzeugt tatsächlich sowohl endotherme als auch exotherme Reaktionen gleichzeitig. Da das Luftvolumen jedoch hauptsächlich aus Stickstoff besteht (ca. 78 Prozent), handelt es sich in erster Linie um eine endotherme Reaktion, wobei das geringe Sauerstoffvolumen (ca. 20 Prozent) eine gleichzeitige, aber geringere exotherme Reaktion erzeugt. Dies führt aufgrund der reaktiven Eigenschaften von Sauerstoff zu einem schnelleren Schmelzen des Grundmaterials. Der Rest der Luft ist in ihrer Zusammensetzung grundsätzlich inert und trägt nur zu der durch den Stickstoff erzeugten endothermen Reaktion bei.
Beim Druckluftschneiden werden die besten Ergebnisse erzielt, wenn die Fokuslage stets in der Mitte der Materialstärke bleibt.
Rohe Strahleneffekte
So wie die Intensität der Sonne die Fähigkeit der Lupe beeinflusst, zu fokussieren und eine effektive Punktgröße zu erzeugen, so beeinflusst auch der Rohlaserstrahl, wie gut Sie seine Energie fokussieren können und wie groß der resultierende fokussierte Punkt ist. Hier ist die allgemeine Regel: Je größer der Rohstrahldurchmesser, desto größer der resultierende Brennweitendurchmesser und desto weiter wird der Brennpunkt von der Linse projiziert.
Eine weitere Möglichkeit, die Punktgröße effektiv zu ändern, ist die Verwendung einer Linse mit einer anderen effektiven Brennweite (EFL). Dadurch entsteht nicht nur eine andere Punktgröße, sondern auch eine andere Tiefenschärfe (DOF), wie in Abbildung 3 dargestellt. Bedenken Sie, dass die Tiefenschärfe nicht nur dort liegt, wo der Strahl am kleinsten ist (Brennweite), sondern auch den Bereich unmittelbar vor und nach der kleinsten Punktgröße umfasst.
Als Beispiel für die Änderung der Punktgröße und Schärfentiefe betrachten wir einen CO2-Laserstrahl mit einer Wellenlänge von 10.600 nm, einem Rohstrahldurchmesser von 20 mm und einem M2 von 2. Wenn wir diesen Strahl durch eine 3,75-Zoll-Linse (95,25 mm) leiten, beträgt der Durchmesser an der Brennweite ungefähr 128 Mikrometer (0,128 mm). Wenn wir nun eine 5-Zoll-Linse (127 mm) verwenden und denselben 20-mm-Rohstrahl verwenden, beträgt der Durchmesser an der Brennweite 170 Mikrometer (0,170 mm). Gleichzeitig würde sich die Schärfentiefe zwischen den beiden Linsen ändern. Die 3,75-Zoll-Linse hätte eine Schärfentiefe von ungefähr 1,2 mm, verglichen mit einer Schärfentiefe von 2,16 mm bei der 5-Zoll-Linse.
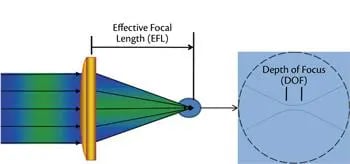
Ein weiterer Aspekt, der die Brennpunktprojektion des Strahls verändern kann, ist eine Änderung der Wellenfront des Strahls, bevor dieser auf die Linse trifft. Die Wellenfront des Rohstrahls kann als konvergierend, parallel oder divergierend beschrieben werden. Bei einer konvergierenden Wellenfront wird der Strahl während seiner Ausbreitung im Wesentlichen kleiner. Wenn diese konvergierende Wellenfront auf die Linse trifft, ist die resultierende Fokusprojektion kürzer als bei einer parallelen Wellenfront, da die Strahldurchmesserprojektion an der Oberseite der Linse kleiner ist. Umgekehrt führt die Fokussierung einer divergierenden Wellenfront zu einer längeren Brennpunktprojektion als bei einer parallelen Wellenfront, da der Strahldurchmesser an der Oberseite der Linse größer ist.
Anwendungen in der Praxis
Es ist wichtig, jeden Aspekt zu kontrollieren, der mit der Aufrechterhaltung der richtigen Fokuspunktprojektionen zusammenhängt. Sie müssen sicherstellen, dass der Rohstrahl am optischen Resonator in gutem Zustand ist und dass der Strahl richtig an die Linse geliefert wird. Die Verwendung einer Linse mit der richtigen Brennweite kann die Schmelzgeschwindigkeit des Materials und die bearbeitbare Dicke verändern. Eine Linse mit kurzer Brennweite, wie z. B. eine 3,75-Zoll-EFL, ist bis zu einer Dicke von 12 Gauge oder 0,104 Zoll am effektivsten. Eine 5-Zoll-Linse ist bis zu einer Dicke von 0,250 Zoll am effektivsten. Verwenden Sie für dickere Materialien eine 7,5-Zoll-Linse bis maximal 1,25 Zoll und eine 10-Zoll-Linse bis maximal 1,312 Zoll, um den effektivsten Schnitt zu erzielen.
Eine wirklich zeitsparende Methode ist die Verwendung einer EFL, mit der Sie den Großteil Ihrer täglichen Produktion abdecken können, ohne auf ein anderes Objektiv umsteigen zu müssen. Mit einem 7,5-Zoll-Objektiv können Sie im Laufe der täglichen Produktion größtenteils alle Ziele erreichen, die mit der Beibehaltung des richtigen Fokus verbunden sind, von 16 ga. bis 1 Zoll Dicke.
Wie bereits erwähnt, hat die Wahl des Hilfsgases viel damit zu tun, wie Ihre Brennpunktposition im Material bestimmt wird. Sauerstoffunterstütztes Laserschneiden (exotherm) erfordert Brennpunktpositionen, die knapp in der Oberfläche oder über der Oberfläche des Materials liegen. Es sind nur sehr wenige Brennpunktänderungen erforderlich, es sei denn, Sie wechseln von Hochdruck- zu Niederdruckschneiden, da der Brennpunkt immer auf oder nahe der Oberfläche des Materials liegt und folglich von Änderungen der Materialdicke nicht beeinflusst wird. Stickstoffunterstütztes Laserschneiden (endotherm) hingegen ist stark brennpunktabhängig und basiert auf der zu verarbeitenden Materialdicke, da der Brennpunkt an oder nahe der Unterseite des Materials liegt.
In beiden Fällen können alle grundlegenden Brennpunkte durch die Verwendung eines CNC-Autofokusgeräts, beispielsweise eines adaptiven Spiegels, erreicht werden.
Ein adaptiver Spiegel funktioniert, indem er die Form der Spiegeloberfläche durch Druck auf die Rückseite des Spiegels verändert. Im Normalzustand, ohne Druck, ist die Oberfläche des adaptiven Spiegels konkav. Wenn Druck auf den Spiegel ausgeübt wird, ändert sich die Oberfläche von konkav zu flach und dann zu konvex. Durch die Veränderung der Spiegelform ändert sich die Wellenfront des Strahls und damit auch die Größe des Strahls auf der Linse und die Stelle, an der die Brennpunktposition innerhalb des Materials projiziert wird.
Ein weiterer großer Vorteil des Autofokus ist die Möglichkeit, die Fokusposition während des Einstechvorgangs dynamisch zu ändern, was eine maximale Energiezufuhr innerhalb der Materialdicke ermöglicht und die Gesamteinstechzeit verkürzt.
Bis heute werden Fortschritte in der Laserschneidtechnologie erzielt, die Durchsatz und Produktivität verbessern. Entscheidend bleibt jedoch die Zuführung des Rohstrahls zur Linse und die Einhaltung der richtigen Brennpunktpositionen, je nach Anwendung.
Wenn die richtige Fokusposition und die richtigen Projektionsformen im zu bearbeitenden Material beibehalten werden, werden die restlichen Anforderungen, die für einen konsistenten, qualitativ hochwertigen Schnitt erforderlich sind, minimiert. Dies spart Rüstzeit und sorgt gleichzeitig für gleichbleibende Produktivität und Durchsatz.