Plasmaschneider sind in der Branche für ihre Fähigkeit bekannt, präzise und saubere Schnitte zu liefern. Das Erreichen optimaler Genauigkeit beim Plasmaschneiden hängt jedoch stark von der Einrichtung des Systems ab. Obwohl häufig Handbrenner verwendet werden, liefern sie im Vergleich zu automatisierten Plasmaschneidmaschinen mit numerischer Computersteuerung (CNC) in der Regel weniger genaue Schnitte. Selbst innerhalb CNC-Plasmaschneiden Technologie können verschiedene Faktoren die Genauigkeit beeinflussen.
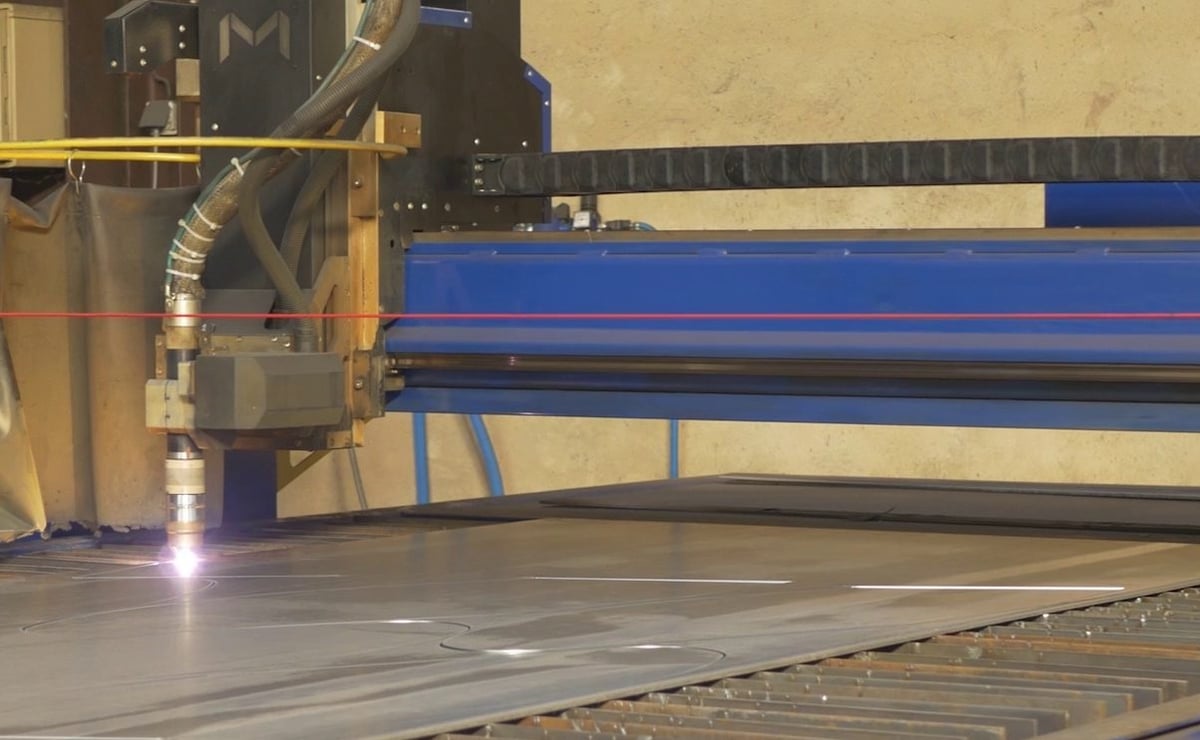
5 Faktoren, die die Präzision von Plasmaschneidern beeinflussen
Arbeitsgas
Das Arbeitsgas und die Durchflussrate sind die Hauptparameter, die die Schnittqualität beeinflussen. Derzeit ist die allgemeine Verwendung von Luftplasmaschneiden nur eines von vielen Arbeitsgasen. Es wird aufgrund der relativ geringen Nutzungskosten häufig verwendet. Die Wirkung fehlt tatsächlich. Das Arbeitsgas umfasst Gas und Hilfsgas. Einige Geräte erfordern auch Lichtbogenstartgas. Normalerweise wird das geeignete Arbeitsgas je nach Art des Schneidmaterials, Dicke und Schneidmethode ausgewählt.
Das Gas muss nicht nur die Bildung des Plasmastrahls gewährleisten, sondern auch sicherstellen, dass das geschmolzene Metall und Oxid im Schnitt entfernt werden. Ein übermäßiger Gasfluss führt dazu, dass mehr Lichtbogenwärme abgeführt wird, wodurch die Länge des Strahls kürzer wird, was zu einer verringerten Schneidleistung und Lichtbogeninstabilität führt; ein zu geringer Gasfluss führt dazu, dass der Plasmalichtbogen seine Geradlinigkeit und seinen Schnitt verliert.
Die Tiefe wird geringer und es entsteht auch leicht Schlacke. Daher muss der Gasfluss gut auf den Schneidstrom und die Geschwindigkeit abgestimmt sein. Die aktuellen Plasmaschneidmaschinen verlassen sich hauptsächlich auf den Gasdruck, um die Durchflussrate zu steuern, denn wenn die Brenneröffnung fixiert ist, steuert der Gasdruck auch die Durchflussrate. Der zum Schneiden einer bestimmten Materialdicke verwendete Gasdruck wird normalerweise entsprechend den vom Kunden bereitgestellten Daten ausgewählt. Bei anderen speziellen Anwendungen muss der Gasdruck durch den tatsächlichen Schneidtest bestimmt werden.
Die am häufigsten verwendeten Arbeitsgase sind: Argon, Stickstoff, Sauerstoff, Luft, H35, Argon-Stickstoff-Mischgas usw.
A. Die Luft enthält volumenmäßig etwa 781 TP3T Stickstoff, daher ist die beim Luftschneiden entstehende Schlacke der beim Schneiden mit Stickstoff entstehenden Schlacke sehr ähnlich; die Luft enthält außerdem volumenmäßig etwa 211 TP3T Sauerstoff.
Aufgrund des Sauerstoffs wird Luft zum Schneiden von kohlenstoffarmen Stahlmaterialien verwendet. Die Geschwindigkeit ist ebenfalls sehr hoch. Gleichzeitig ist Luft auch das wirtschaftlichste Arbeitsgas für CNC-Plasmaschneidmaschinen. Wenn jedoch nur Luft geschnitten wird, treten Probleme wie Schlackenbildung, Schnittoxidation, Stickstoffanstieg usw. auf. Die kürzere Lebensdauer der Elektrode und der Düse wirkt sich auch auf die Arbeitseffizienz und die Schneidkosten aus.
B. Sauerstoff kann die Schneidgeschwindigkeit von Weichstahl erhöhen. Beim Schneiden mit Sauerstoff ist der Schneidmodus dem Brennschneiden sehr ähnlich. Der Hochtemperatur- und Hochenergieplasmalichtbogen beschleunigt die Schneidgeschwindigkeit, muss jedoch mit einer Elektrode verwendet werden, die Hochtemperaturoxidation widersteht. Gleichzeitig ist die Elektrode während des Lichtbogens vor Stößen geschützt, um die Lebensdauer der Elektrode zu verlängern.
C. Wasserstoff wird normalerweise als Hilfsgas verwendet, um mit anderen Gasen gemischt zu werden. Beispielsweise ist das bekannte Gas H35 (Wasserstoffvolumenanteil beträgt 35%, der Rest ist Argon) eines der Gase mit der stärksten Plasmalichtbogenschneidfähigkeit, das hauptsächlich von Wasserstoff profitiert. Da Wasserstoff die Lichtbogenspannung erheblich erhöhen kann, hat der Wasserstoffplasmastrahl einen hohen Enthalpiewert. In Mischung mit Argon wird seine Plasmastrahlschneidfähigkeit erheblich verbessert. Im Allgemeinen wird für Metallmaterialien mit einer Dicke von mehr als 70 mm üblicherweise Argon + Wasserstoff als Schneidgas verwendet. Wenn ein Wasserstrahl verwendet wird, um den Argon + Wasserstoff-Plasmalichtbogen weiter zu komprimieren, kann auch eine höhere Schneidleistung erzielt werden.
D. Stickstoff ist ein häufig verwendetes Arbeitsgas. Unter der Bedingung einer höheren Versorgungsspannung hat der Stickstoffplasmalichtbogen eine bessere Stabilität und eine höhere Strahlenergie als Argon, selbst beim Schneiden von flüssigem Metall mit hochviskosen Materialien wie Edelstahl und Nickellegierungen ist auch die Menge an Schlacke an der unteren Kante des Schnitts gering.
Stickstoff kann allein oder gemischt mit anderen Gasen verwendet werden. Beispielsweise werden beim automatischen Schneiden häufig Stickstoff oder Luft als Arbeitsgase verwendet. Diese beiden Gase sind zum Standardgas für das Hochgeschwindigkeitsschneiden von Kohlenstoffstahl geworden. Manchmal wird Stickstoff auch als Startgas für das Sauerstoffplasmalichtbogenschneiden verwendet.
E. Argongas reagiert bei hohen Temperaturen kaum mit Metallen und der Argonplasmalichtbogen ist sehr stabil. Darüber hinaus haben die verwendeten Düsen und Elektroden eine lange Lebensdauer. Allerdings ist die Spannung des Argonplasmalichtbogens niedrig, der Enthalpiewert nicht hoch und die Schneidfähigkeit begrenzt. Im Vergleich zum Luftschneiden wird die Schnittdicke um etwa 25% reduziert.
Darüber hinaus ist die Oberflächenspannung des geschmolzenen Metalls in der Argongasschutzumgebung relativ groß, sie ist etwa 30% höher als in der Stickstoffumgebung, sodass es mehr Probleme mit hängenden Schlacken gibt. Sogar beim Schneiden mit einer Mischung aus Argon und anderen Gasen besteht die Tendenz, dass die Schlacke anhaftet. Daher wird reines Argon allein zum Plasmaschneiden nur noch selten verwendet.
Plasmaschneidgeschwindigkeit
Neben dem Einfluss des Arbeitsgases auf die Schnittqualität ist auch der Einfluss der Schnittgeschwindigkeit auf die Verarbeitungsqualität der CNC-Plasmaschneidmaschine sehr wichtig. Schnittgeschwindigkeit: Der optimale Schnittgeschwindigkeitsbereich kann gemäß der Gerätebeschreibung ausgewählt oder experimentell ermittelt werden. Aufgrund der Materialdicke, der unterschiedlichen Materialien, des Schmelzpunkts, der Wärmeleitfähigkeit und der Oberflächenspannung nach dem Schmelzen ist auch die Schnittgeschwindigkeit entsprechend. Vielfalt. Hauptleistung:
A. Eine moderate Erhöhung der Schnittgeschwindigkeit kann die Schnittqualität verbessern, d. h. der Schnitt ist etwas schmaler, die Schnittfläche ist glatter und Verformungen können reduziert werden.
B. Die Schnittgeschwindigkeit ist zu hoch, sodass die lineare Energie des Schnitts unter dem erforderlichen Wert liegt. Der Strahl im Schlitz kann die geschmolzene Schneidschmelze nicht schnell wegblasen und bildet sofort einen großen Schleppwiderstand. Rückgang.
C. Wenn die Schnittgeschwindigkeit zu niedrig ist, muss der CNC-Punkt zwangsläufig den Leitungsstrom in der Nähe des Schlitzes finden, der dem Lichtbogen am nächsten ist, da die Schneidstelle die Anode des Plasmalichtbogens ist. Dies ist notwendig, um die Stabilität des Lichtbogens selbst aufrechtzuerhalten. Die radiale Richtung des Strahls überträgt mehr Wärme, sodass der Einschnitt breiter wird. Das geschmolzene Material auf beiden Seiten des Einschnitts sammelt sich und verfestigt sich an der Unterkante, wodurch eine Schlacke entsteht, die nicht leicht zu reinigen ist. Die Oberkante des Einschnitts wird erhitzt und geschmolzen, wodurch eine abgerundete Ecke entsteht.
D. Wenn die Geschwindigkeit extrem niedrig ist, erlischt der Lichtbogen sogar, weil der Schnitt zu breit ist. Dies zeigt, dass gute Schnittqualität und Schnittgeschwindigkeit untrennbar miteinander verbunden sind.
Plasmaschneidstrom
Der Schneidstrom ist ein wichtiger Parameter des Schneidprozesses, der direkt die Dicke und Geschwindigkeit des Schnitts bestimmt, d. h. die Schneidfähigkeit, die den richtigen Einsatz der Plasmaschneidmaschine für qualitativ hochwertiges, schnelles Schneiden beeinflusst. Die Parameter des Schneidprozesses müssen gründlich verstanden und beherrscht werden.
A. Mit zunehmendem Schneidstrom erhöht sich die Lichtbogenenergie, die Schneidkapazität erhöht sich und die Schneidgeschwindigkeit erhöht sich entsprechend.
B. Mit zunehmendem Schneidstrom vergrößert sich der Durchmesser des Lichtbogens und der Lichtbogen wird dicker, wodurch der Schnitt breiter wird.
C. Übermäßiger Schneidstrom erhöht die thermische Belastung der Düse, die Düse wird vorzeitig beschädigt und die Schnittqualität nimmt natürlich ab, und auch ein normaler Schnitt kann nicht durchgeführt werden.
Wenn Sie vor dem Plasmaschneiden ein Netzteil auswählen, dürfen Sie kein zu großes oder zu kleines Netzteil wählen. Bei einem zu großen Netzteil ist es Verschwendung, die Schneidkosten zu berücksichtigen, da ein so großer Strom überhaupt nicht verwendet werden kann.
Außerdem wird bei der Auswahl der Plasmastromversorgung aufgrund der Kosteneinsparungen beim Schneiden ein zu geringer Strom gewählt, sodass der eigentliche Schneidbedarf beim Schneiden nicht gedeckt werden kann, was der CNC-Schneidemaschine selbst großen Schaden zufügt. Gabortech empfiehlt, den Schneidstrom und die entsprechende Düse entsprechend der Materialdicke auszuwählen.
Düsenhöhe
Die Düsenhöhe bezeichnet den Abstand zwischen der Düsenstirnfläche und der Schneidfläche, der einen Teil der gesamten Lichtbogenlänge ausmacht. Beim Plasmalichtbogenschneiden wird im Allgemeinen eine externe Stromversorgung mit konstantem Strom oder steilem Abfall verwendet.
Wenn die Düsenhöhe erhöht wird, ändert sich der Strom kaum, aber die Lichtbogenlänge nimmt zu und die Lichtbogenspannung steigt, wodurch die Lichtbogenleistung zunimmt. Gleichzeitig steigt jedoch mit zunehmender der Umgebung ausgesetzter Lichtbogenlänge der Energieverlust der Lichtbogensäule.
Im Falle der kombinierten Wirkung der beiden Faktoren wird die Rolle des ersteren oft vollständig durch den letzteren aufgehoben, aber die effektive Schneidenergie wird reduziert, was zu einer Verringerung der Schneidleistung führt. Dies zeigt normalerweise, dass die Blaskraft des Schneidstrahls geschwächt wird, die Restschlacke am unteren Teil des Einschnitts zunimmt und die Oberkante überschmilzt, wodurch abgerundete Ecken entstehen.
Hinzu kommt, dass sich der Durchmesser des Plasmastrahls aufgrund seiner Form nach außen vergrößert, nachdem er die Brennermündung verlassen hat, und eine Vergrößerung der Düsenhöhe zwangsläufig eine Vergrößerung der Schnittbreite bewirkt.
Daher ist es vorteilhaft, die Schnittgeschwindigkeit und Schnittqualität zu verbessern, indem man die Düsenhöhe so klein wie möglich wählt. Wenn die Düsenhöhe jedoch zu niedrig ist, kann dies zum Doppelbogenphänomen führen. Durch die Verwendung der Keramik-Außendüse kann die Düsenhöhe auf Null gesetzt werden, d. h. die Endfläche der Düse berührt direkt die zu schneidende Oberfläche, und es kann ein guter Effekt erzielt werden.
Lichtbogenleistung
Um einen hochkomprimierten Plasmalichtbogen zu erhalten, verwendet die Schneiddüse eine kleinere Düsenöffnung, eine längere Lochlänge und verstärkt den Kühleffekt, wodurch der durch den effektiven Querschnitt der Düse fließende Strom erhöht werden kann, d. h. die Leistungsdichte des Lichtbogens erhöht wird. Gleichzeitig erhöht die Kompression aber auch den Leistungsverlust des Lichtbogens.
Daher ist die tatsächlich zum Schneiden verwendete effektive Energie kleiner als die von der Stromversorgung abgegebene Leistung. Die Verlustrate liegt im Allgemeinen zwischen 25% und 50%. Bei einigen Verfahren wie dem Plasmalichtbogenschneiden mit Wasserkompression ist die Energieverlustrate höher. Dieses Problem sollte bei der Auslegung der Schneidprozessparameter oder der wirtschaftlichen Berechnung der Schneidkosten berücksichtigt werden.
Die Dicke der in der Industrie verwendeten Metallplatten liegt meist unter 50 mm. Beim Schneiden mit herkömmlichen Plasmabögen in diesem Dickenbereich treten häufig große und kleine Schnitte auf, und die obere Schnittkante führt auch zu einer Verringerung der Genauigkeit der Schnittgröße und erhöht den Aufwand für die nachfolgende Verarbeitung.
Beim Schneiden von Kohlenstoffstahl, Aluminium und Edelstahl mit Sauerstoff- und Stickstoffplasmalichtbogen und einer Plattendicke im Bereich von 10 bis 25 mm gilt normalerweise: Je dicker das Material, desto besser die Rechtwinkligkeit der Endkante, und der Winkelfehler der Schneide beträgt 1 bis 4 Grad. Wenn die Plattendicke weniger als 1 mm beträgt, erhöht sich der Schnittwinkelfehler mit abnehmender Plattendicke von 3 bis 4 Grad auf 15 bis 25 Grad.
Es wird allgemein angenommen, dass die Ursache für dieses Phänomen im Ungleichgewicht der Wärmezufuhr des Plasmastrahls auf der Schnittfläche liegt, das heißt, die Energie des Plasmalichtbogens wird im oberen Teil des Schnitts stärker freigesetzt als im unteren Teil.
Dieses Ungleichgewicht der Energiefreisetzung hängt eng mit vielen Prozessparametern zusammen, beispielsweise dem Grad der Plasmalichtbogenkompression, der Schneidgeschwindigkeit und dem Abstand zwischen Düse und Werkstück.
Durch Erhöhen der Lichtbogenkompression kann der Hochtemperaturplasmastrahl ausgedehnt werden, um einen gleichmäßigeren Hochtemperaturbereich zu bilden, und gleichzeitig die Geschwindigkeit des Strahls erhöhen, was den Breitenunterschied zwischen den oberen und unteren Schnitten verringern kann.
Bei zu starker Kompression herkömmlicher Düsen kommt es allerdings häufig zu einer Doppellichtbogenbildung, die nicht nur Elektroden und Düsen verbraucht und den Prozess unmöglich macht, sondern auch zu einer Verschlechterung der Schnittqualität führt.
Darüber hinaus vergrößern eine zu hohe Geschwindigkeit und eine zu große Düsenhöhe den Unterschied zwischen der oberen und unteren Schnittbreite.
Wählen Sie den richtigen CNC-Plasmaschneider für Ihre Werkstatt
KRRASS ist der führende Hersteller robuster CNC-Präzisions-Plasmaschneidmaschinen für kundenspezifische Fertigungen. Da wir uns der enormen Bedeutung von Genauigkeit bei der Teileproduktion bewusst sind, entwickeln wir Brenntische mit größter Sorgfalt, die Ihren Spezifikationen genau entsprechen. Kontaktieren Sie KRRASS noch heute, um mehr zu erfahren, und fragen Sie nach unserem kostenlosen und unbegrenzten lebenslangen Support, der bei jedem Kauf inbegriffen ist.