So verhindern Sie Grate beim Laserschneiden? Wenn einige Kunden CNC-Faserlaserschneidmaschinen zur Bearbeitung von Blechteilen verwenden, ist die Schneidwirkung des Werkstücks sehr unbefriedigend und es entstehen viele Grate. Grate beziehen sich auf verschiedene unregelmäßige Metallteile, die beim Laserschneiden auftreten. Grate sind eines der häufigsten Phänomene, die bei der Bearbeitung mit Laserschneidmaschinen auftreten. Grate wirken sich direkt auf die Qualität des zu bearbeitenden Werkstücks aus.
Daher werden viele Benutzer die Qualität der Geräte bei der Verwendung in Frage stellen. Tatsächlich ist dies jedoch nicht der Fall. Beim Schneiden von Blechen entstehen aufgrund unsachgemäßer Bedienung Grate in den von der Laserschneidmaschine verarbeiteten Materialien. Der Umgang mit Graten beim Laserschneiden hat schon immer alle beunruhigt.
Gratproblem beim Laserschneiden
Grate sind verschiedene scharfe Ecken, Grate und andere unregelmäßige Metallteile, die beim Laserschneiden am Übergangspunkt der Werkstückoberfläche auftreten. Grate sind eines der häufigsten Phänomene bei der Verarbeitung mit Laserschneidmaschinen. Dies sind auch zwei große Probleme, die in der theoretischen Forschung zum Metallschneiden bisher nicht gelöst wurden: die Entstehung und Kontrolle von Graten.
Grate wirken sich direkt auf die Maßgenauigkeit, Formgenauigkeit und Oberflächenrauheit des zu bearbeitenden Werkstücks aus. Wie entstehen Grate? Tatsächlich sind Grate übermäßige Restpartikel auf der Oberfläche von Metallmaterialien. Wenn das Material Grate aufweist, kann festgestellt werden, dass das Material defekt ist. Je mehr Grate, desto geringer die Qualität. Was verursacht Grate, wenn Laserschneidmaschinen Metallbleche bearbeiten?
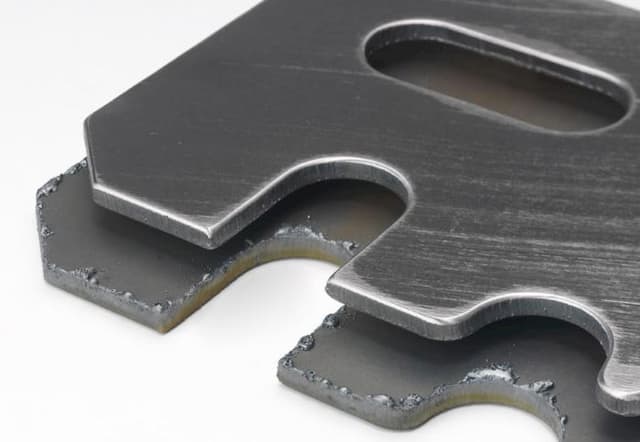
Was sind die Ursachen für Grate beim Laserschneiden?
Laserschneiden verwendet einen Fokussierspiegel, um den Laserstrahl auf die Oberfläche des Materials zu fokussieren und das Material zu schmelzen, zu verdampfen und abzutragen. Gleichzeitig wird koaxial zum Laserstrahl komprimiertes Gas verwendet, um das geschmolzene Material auszublasen, und der Laserstrahl und das Material bewegen sich entlang einer bestimmten Flugbahn entgegengesetzt. Bewegung, um eine Schneidnaht einer bestimmten Form zu bilden und das Schneiden des Materials abzuschließen. Das Laserschneiden bietet die Vorteile hoher Präzision, schmaler Schneidschlitze, glatter Schnittflächen, hoher Geschwindigkeit, guter Verarbeitungsqualität und einer großen Auswahl an Verarbeitungsmaterialien.
Derzeit wird die Laserschneidtechnologie in vielen Bereichen weit verbreitet eingesetzt. Komplette Sätze von Elektrogehäusen bestehen meist aus Blechteilen. Das Laserschneiden hat sich aufgrund seiner Vorteile wie niedrige Verarbeitungskosten, hohe Effizienz und eine große Vielfalt an Verarbeitungsmaterialien zu einer gängigen Verarbeitungsmethode in der Blechindustrie entwickelt. Die während der Verarbeitung entstehende Schlacke und die damit verbundenen Grate sind jedoch für die Manager vor Ort ärgerlich.
Beim Laserschneiden einiger Bleche entstehen leicht Grate. Das Auftreten von Graten beeinträchtigt die Genauigkeit des bearbeiteten Werkstücks und die Glätte der Materialoberfläche und verringert sogar die Qualität des Produkts, was bei nachfolgenden Inspektions- und Abnahmearbeiten zu erheblichen Unannehmlichkeiten führt.
Was genau verursacht die Entstehung von Graten beim Laserschneiden?
Durch das Verständnis des Funktionsprinzips und der täglichen Praxis des Laserschneidens haben die Hersteller von SC-Laserschneidmaschinen die Ursachen für Grate zusammengefasst, die hauptsächlich die folgenden 7 Aspekte umfassen:
1) Falsche Materialauswahl. Wenn das ausgewählte Material nicht zum Laserschneiden geeignet ist, entstehen leicht Grate. Einige Materialien lassen sich beispielsweise leicht mit dem Laser schneiden, und es entstehen Grate.
2) Abweichungen in der oberen und unteren Position des Laserstrahlfokus führen dazu, dass die Energie unkonzentriert ist. Das Werkstück wird nicht ausreichend verdampft. Die angesammelte Schlacke fällt nicht leicht ab und erzeugt leicht Grate.
3) Die Laserleistung ist falsch eingestellt. Die Ausgangsleistung des Lichts reicht nicht aus, um das Metall effektiv zu verdampfen, was zu einer großen Menge an Schlacke und Graten führt.
4) Art, Reinheit und Blasdruck des Hilfsgases der Laserschneidmaschine entsprechen nicht den Anforderungen.
5) Die Schnittgeschwindigkeit beim Laserschneiden ist zu niedrig, wodurch die Oberflächenqualität der Schnittfläche zerstört wird und Grate entstehen.
6) Die Arbeitszeit der Laserschneidmaschine ist zu lang, was zu Instabilität des Geräts und zur Entstehung von Graten führt.
7) Die Laserschneidausrüstung weist Mängel auf. Beispielsweise weist die Sägezahnplatte der Laserbasis eine geringe Verzahnungstiefe und eine unzureichende Verjüngung auf. Daher ist die Kontaktfläche mit der Platte zu groß, was zu einer Behinderung des Laserdurchschlags und des Gasflusses während der Verarbeitung führt, was leicht zu Schlackenanhaftung, Schlackenrückprall und Gratbildung führen kann.
Ein weiterer Aspekt ist die Qualität der Ausrüstung selbst sowie die Parametereinstellung. Wenn Kunden eine Laserschneidmaschine kaufen, müssen sie die Ausrüstung von einem professionellen Bediener debuggen lassen.
Die negativen Auswirkungen von Graten beim Laserschneiden
Das Vorhandensein von Graten in den Ecken des Werkstücks beeinträchtigt die Genauigkeit nachfolgender Biege-, Schweiß- und Montagevorgänge erheblich und birgt zudem gewisse Sicherheitsrisiken für die Bediener.
Wenn das Werkstück mit Graten auf den Luftkasten der Ringhaupteinheit aufgebracht wird, hat dies große Auswirkungen auf die Luftdichtheit. Bei Verwendung im elektrischen System fallen die Grate ab und verursachen einen Kurzschluss im Stromkreis oder eine Beschädigung des Magnetfelds, wodurch der normale Betrieb des Systems beeinträchtigt wird oder andere Gefahren entstehen.
Wie löst man Gratprobleme beim Laserschneiden?
Während des Blechbearbeitungsprozesses beeinflussen die Parametereinstellungen der Laserschneidmaschine und die Reinheit des Gases die Bearbeitungsqualität. Verwenden Sie geeignetes und qualifiziertes Gas, konfigurieren Sie die Maschine und passen Sie die Parameter so an, dass das geschnittene Werkstück keine Grate aufweist.
- Geräteparameter anpassen: Fokusposition, Schnitteinlaufposition
Einige Parametereinstellungsfaktoren der Laserschneidmaschine beeinflussen auch das Auftreten von Schlacke, was zu Graten an der Metalllaserschneidmaschine führt. Daher müssen die Schneidparameter optimal eingestellt werden.
Wenn die Fokusposition zu hoch ist, werden die Grate größer, und die Grate werden sehr hart und die Seiten sind nicht glatt. Außerdem sind mehrere Fehlersuche erforderlich, um die Fokusposition zu finden. Der Zuleitungsdraht sollte vom Untermaterial ferngehalten werden, um eine lokale Überhitzung zu vermeiden.
Nach dem Kauf einer Laserschneidmaschine ist es am besten, wenn ein erfahrener Bediener die Fehlersuche am Gerät durchführt. Je nach Verarbeitungsmaterial werden Leistung, Luftdruck, Durchflussrate, Brennweite, Vorschubgeschwindigkeit und andere Parameter durch Übung wiederholt angepasst, bis sie optimal eingestellt sind. Speichern und zeichnen Sie die Daten auf, um die nachfolgende Stapelverarbeitung zu erleichtern. Es ist unmöglich, exquisite Werkstücke ausschließlich auf der Grundlage der von der Maschine bereitgestellten Parameter zu schneiden.
- Geeignetes Hilfsgas verwenden
Auch die Verwendung von Hilfsgasen wirkt sich auf die Verarbeitungsqualität aus. Daher sollten je nach Verarbeitungsmaterial unterschiedliche Hilfsgase ausgewählt werden.
Beim Schneiden von Edelstahl wird empfohlen, Stickstoff als Hilfsgas zu verwenden. Stickstoff wird üblicherweise als Inertgas bezeichnet. Bei der Laserbearbeitung verhindert Stickstoff nicht nur das Explosionspunktphänomen beim Laserschneiden, sondern verhindert auch eine sofortige Oxidation der erhitzten Endoberfläche. Die geschnittene Endoberfläche wird glatter und heller.
Auch die Reinheit des Gases ist entscheidend. Versuchen Sie, hochreines Gas zu wählen. Das Hilfsgas sollte auf einen Druck von 12-15 Kilogramm eingestellt werden. Der Stickstoff bei diesem Druck verhindert die Verbrennung nicht vollständig und kann auch Abfall und Verunreinigungen schnell wegblasen, um Grate zu entfernen.
Faserlaserschneidmaschine für Bleche und Rohre
- Gerätezubehör prüfen
Auch Geräte, die lange Zeit in schlechtem Zustand waren, mindern die Verarbeitungsqualität und erzeugen aufgrund von Alterung, Verschmutzung und Beschädigung wichtiger Teile Grate. Wenn die Linse mit Öl verunreinigt ist, kleine Risse aufweist oder die Schneiddüse beschädigt ist, wird die Übertragung der Laserleistung beeinträchtigt.
Dies lässt sich beurteilen, indem man beobachtet, ob der gebildete Lichtfleck rund ist. Wenn der Fleck rund ist, bedeutet dies, dass die Laserenergie gleichmäßig in seitlicher Richtung verteilt ist und die Schnittqualität hoch ist. Die Schnittqualität kann auch durch regelmäßige Überprüfung der Schlüsselkomponenten sichergestellt werden.
Die Laserschneidmaschine ist eine Präzisionsmaschine und ihre Bedienung ist ebenfalls eine heikle Angelegenheit. Oftmals führt ein Datenfehler dazu, dass die Arbeit nicht richtig abläuft. Daher müssen wir bei unserer Arbeit streng und gewissenhaft vorgehen, um Fehler zu reduzieren und zu vermeiden. Nur wenn wir streng und präzise vorgehen und die Geräte, Gase und Parameter optimal debuggen, kann das Laserschneiden von höherer Qualität sein.