A Laserschneidmaschine ist ein Werkzeug, das einen Laserstrahl zum Schneiden oder Gravieren von Materialien verwendet. Es handelt sich um eine vielseitige und präzise Methode der Materialbearbeitung, die in verschiedenen Branchen zum Schneiden einer Vielzahl von Materialien, darunter Metalle, Kunststoffe, Holz und mehr, weit verbreitet ist. Beim Laserschneiden wird ein Hochleistungslaserstrahl durch eine Optik geleitet und auf die Oberfläche des Materials fokussiert.
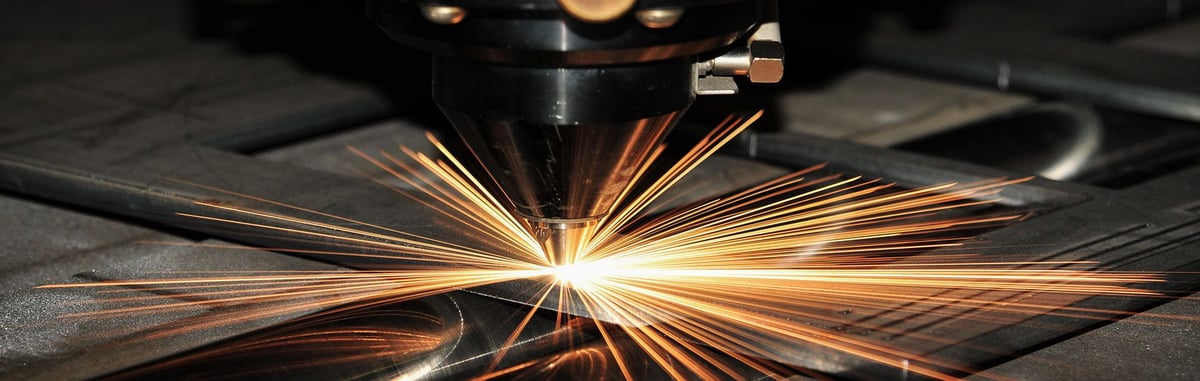
Hier ist ein grundlegender Überblick über die Funktionsweise von Laserschneidmaschinen:
Lasererzeugung: Die Maschine erzeugt einen Laserstrahl mithilfe eines Laserresonators, der das Licht verstärkt und intensiviert.
Strahlführungssystem: Der Laserstrahl wird durch ein System aus Spiegeln und Linsen geleitet, um ihn auf einen kleinen, leistungsstarken Punkt zu fokussieren.
Materialinteraktion: Wenn der fokussierte Laserstrahl mit der Materialoberfläche interagiert, erhitzt er sich und verdampft oder schmilzt das Material an der Kontaktstelle.
Computergestützte numerische Steuerung (CNC): Der gesamte Prozess wird durch ein computergestütztes numerisches Steuerungssystem gesteuert, das einem digitalen Entwurf oder Muster folgt, um den Laser über das Material zu führen und es entsprechend den programmierten Spezifikationen zu schneiden oder zu gravieren.
Zu den Vorteilen des Laserschneidens gehören hohe Präzision, schnelle Verarbeitungsgeschwindigkeiten und die Möglichkeit, komplizierte Designs zu schneiden. Es wird häufig in der Fertigung, Herstellung, Beschilderung, Elektronik, Automobilindustrie, Luft- und Raumfahrt und anderen Branchen eingesetzt, in denen präzises und kompliziertes Schneiden oder Gravieren erforderlich ist. Darüber hinaus ist das Laserschneiden ein berührungsloser Prozess, der den Verschleiß der Maschinen reduziert.
Je nach Material und Anwendungsanforderungen werden unterschiedliche Lasertypen wie CO2-Laser und Faserlaser verwendet. CO2-Laser werden häufig für nichtmetallische Materialien verwendet, während Faserlaser besser zum Schneiden von Metallen geeignet sind.
Soll ich eine Laserschneidmaschine verwenden?
Die Wahl einer Laserschneidmaschine hängt von verschiedenen Faktoren ab, darunter die Materialien, mit denen Sie arbeiten möchten, die Materialstärke, der erforderliche Präzisionsgrad, das Produktionsvolumen und Ihr Budget. Hier sind einige gängige Typen von Laserschneidmaschinen:
CO2-Laserschneidmaschinen:
Materialien: Geeignet für nichtmetallische Materialien wie Holz, Acryl, Kunststoff, Gummi und Stoffe.
Vorteile: Vielseitig für eine große Bandbreite an Materialien, gut für komplizierte Designs, kostengünstig.
Einschränkungen: Nicht ideal zum Schneiden dicker Metalle.
Faserlaser-Schneidemaschinen:
Materialien: Besonders effektiv zum Schneiden von Metallen, einschließlich Stahl, Aluminium und Messing.
Vorteile: Hohe Geschwindigkeit und Effizienz beim Metallschneiden, präzise Ergebnisse.
Einschränkungen: Weniger effektiv bei nichtmetallischen Materialien.
Nd:YAG-Laserschneidmaschinen:
Materialien: Wird sowohl für metallische als auch für nichtmetallische Materialien verwendet.
Vorteile: Im Vergleich zu CO2-Lasern gut zum Schneiden dickerer Metalle geeignet.
Einschränkungen: Höhere Kosten, weniger verbreitet als CO2- und Faserlaser.
Lasergravurmaschinen:
Materialien: Wird zum Gravieren und Markieren verschiedener Materialien verwendet, darunter Holz, Acryl, Glas, Leder und einige Metalle.
Vorteile: Ideal für detaillierte Gravur- und Markierungsanwendungen.
Einschränkungen: Möglicherweise nicht so gut für schwere Schnitte geeignet.
Berücksichtigen Sie bei der Auswahl einer Laserschneidmaschine die folgenden Faktoren:
Materialkompatibilität: Stellen Sie sicher, dass die Maschine für die Materialien geeignet ist, mit denen Sie arbeiten möchten.
Schnittdicke: Verschiedene Maschinen haben unterschiedliche Fähigkeiten hinsichtlich der Schnittdicke. Wenn Sie dickere Materialien schneiden müssen, benötigen Sie möglicherweise einen leistungsstärkeren Laser.
Präzisionsanforderungen: Überlegen Sie, welche Präzision Ihre Anwendung erfordert. Einige Projekte erfordern möglicherweise eine höhere Präzision, und bestimmte Maschinen zeichnen sich in dieser Hinsicht aus.
Produktionsvolumen: Wenn Sie ein hohes Produktionsvolumen haben, benötigen Sie möglicherweise eine Maschine mit höherer Geschwindigkeit und Effizienz.
Budget: Laserschneidmaschinen variieren im Preis, daher ist es wichtig, Ihre Budgetbeschränkungen zu berücksichtigen.
Benutzerfreundlichkeit: Überprüfen Sie die Benutzerfreundlichkeit der Maschine und der zugehörigen Software, insbesondere wenn Sie oder Ihr Team nicht über viel Erfahrung in der Bedienung von Laserschneidgeräten verfügen.
Lassen Sie sich stets von Herstellern oder Lieferanten beraten und sehen Sie sich, wenn möglich, Vorführungen oder Benutzerberichte an, um sich ein besseres Bild von der Leistung einer bestimmten Laserschneidmaschine im Praxiseinsatz zu machen.
Wartung der Laserschneidmaschine?
Die richtige Wartung ist entscheidend, um die Langlebigkeit und optimale Leistung einer Laserschneidmaschine sicherzustellen. Regelmäßige Wartung kann helfen, Ausfälle zu vermeiden, Ausfallzeiten zu reduzieren und gleichbleibende und präzise Schneidergebnisse sicherzustellen. Hier sind einige allgemeine Richtlinien für die Wartung von Laserschneidmaschinen:
Reinigen der Optik:
Reinigen Sie Linsen, Spiegel und andere optische Komponenten regelmäßig, um Staub, Schmutz und Rückstände zu entfernen. Verwenden Sie fusselfreie Tücher und vom Gerätehersteller empfohlene Linsenreinigungslösungen.
Gehen Sie vorsichtig mit der Optik um, um Kratzer oder Beschädigungen zu vermeiden.
Überprüfen und Reinigen der Abgasanlage:
Überprüfen und reinigen Sie das Abgassystem einschließlich der Filter und Kanäle, um eine ausreichende Belüftung und Entfernung von Dämpfen und Partikeln sicherzustellen.
Ersetzen Sie die Filter gemäß den Empfehlungen des Herstellers.
Überprüfen und Reinigen des Schneidbetts:
Reinigen Sie das Schneidbett regelmäßig, um Schmutz und Materialrückstände zu entfernen. Ein sauberes Schneidbett sorgt für eine bessere Schnittqualität und verhindert Schäden an den Maschinenkomponenten.
Überprüfen und reinigen Sie die Lamellen bzw. die Stützstruktur des Schneidbetts.
Bewegliche Teile prüfen und schmieren:
Überprüfen und schmieren Sie die beweglichen Teile der Maschine wie Schienen, Lager und Kugelumlaufspindeln gemäß den Richtlinien des Herstellers.
Achten Sie darauf, dass die verwendeten Schmierstoffe für die jeweiligen Bauteile geeignet sind.
Riemen und Spannsysteme prüfen und einstellen:
Überprüfen Sie Riemen, Riemenscheiben und Spannsysteme auf Verschleiß. Passen Sie sie bei Bedarf an oder ersetzen Sie sie.
Für die präzise Bewegung des Laserschneidkopfes ist die richtige Spannung von entscheidender Bedeutung.
Kalibrieren des Lasersystems:
Kalibrieren Sie das Lasersystem regelmäßig, um die Schnittgenauigkeit aufrechtzuerhalten. Befolgen Sie die vom Hersteller bereitgestellten Kalibrierungsverfahren.
Überprüfen und justieren Sie die Ausrichtung des Laserstrahls.
Wasserkühlsystem prüfen:
Wenn die Laserschneidmaschine über eine Wasserkühlung verfügt, überprüfen Sie regelmäßig den Wasserstand, die Wasserqualität und die Temperatur. Reinigen oder ersetzen Sie die Filter nach Bedarf.
Stellen Sie eine effiziente Wasserzirkulation sicher, um eine Überhitzung zu vermeiden.
Gasversorgung überwachen und aufrechterhalten:
Überprüfen und überwachen Sie das Gasversorgungssystem, z. B. das Hilfsgas (z. B. Stickstoff oder Sauerstoff). Stellen Sie sicher, dass Druck und Durchflussraten innerhalb der empfohlenen Bereiche liegen.
Ersetzen Sie Gasflaschen oder füllen Sie sie nach Bedarf nach.
Software- und Steuerungssystem-Updates:
Halten Sie die Software und das Steuerungssystem der Maschine auf dem neuesten Stand, indem Sie alle verfügbaren Updates des Herstellers installieren.
Sichern Sie wichtige Maschineneinstellungen und -parameter, bevor Sie Software-Updates durchführen.
Schulung und Sensibilisierung des Bedieners:
Schulen Sie die Bediener im richtigen Umgang mit der Maschine und in der Wartung.
Fordern Sie die Bediener auf, ungewöhnliche Geräusche, Vibrationen oder Probleme unverzüglich zu melden.
Beachten Sie immer die Wartungsrichtlinien und Dokumentation des Herstellers für Ihr Laserschneidmaschinenmodell. Die Einhaltung eines regelmäßigen Wartungsplans trägt dazu bei, die Zuverlässigkeit und Langlebigkeit Ihrer Laserschneidanlage sicherzustellen.