Die Qualität von Laserschneiden Die Leistung von Laserschneidmaschinen hängt von einer Vielzahl von Faktoren ab und ist daher ein komplexes Zusammenspiel. Im Mittelpunkt des Laserschneidprozesses steht die Wechselwirkung zwischen dem Laserstrahl und den zu schneidenden Materialien, die in zwei Hauptphänomene unterteilt werden kann: mikroskopisch und makroskopisch.
Mikroskopische Phänomene befassen sich mit den komplexen Quantenreaktionsprozessen, die bei der Wechselwirkung zwischen Laser und Material auftreten. Makroskopische Phänomene umfassen dagegen die Absorption, Reflexion und Brechung von Materialien sowie die Energieumwandlung und -übertragung von Laserstrahlen.
Neben den intrinsischen Eigenschaften des zu bearbeitenden Materials haben auch hardwarebezogene Faktoren Einfluss auf die Schnittqualität. Lassen Sie uns diese Faktoren gemeinsam untersuchen.
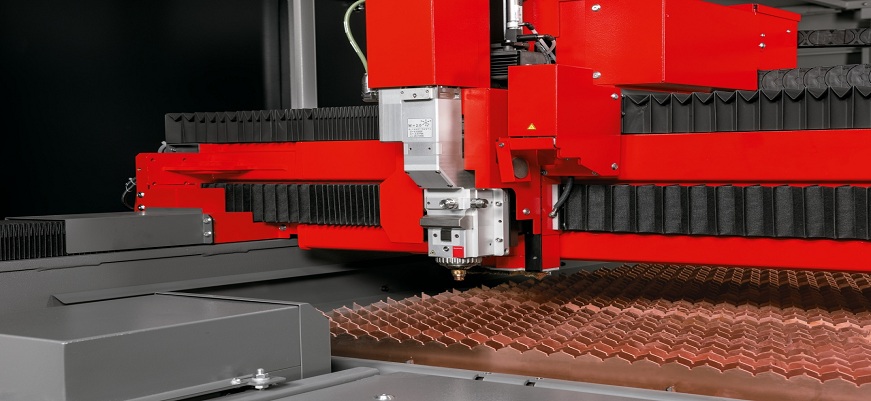
Bedeutung der Qualitätskontrolle
Die Qualitätskontrolle spielt in der Wirtschaft eine unersetzliche Rolle. Durch Probenahme und Prozesskontrolle können Unternehmen ihre Leistung verbessern. Dasselbe gilt für den Laserschneidprozess. Es stellt sich jedoch die Frage, wie sich die Qualität des Lasermetallschneidens messen lässt.
In den vorherigen Texten haben wir die Bedeutung der Optimierung der Laserschneidparameter, d. h. der Durchführung einer vorbeugenden Wartung des Laserschneiders, betont. Bei guten und hochwertigen Laserschneidern ist die Möglichkeit von Anomalien im Schneidprozess auf ein Minimum reduziert. Es sollte jedoch auf andere wichtige Key Performance Indicators (KPI) geachtet werden, die Feedback zum Qualitätsniveau des Laserschneidens geben.
Normen zum Laserschneiden
Da ein großer Teil der Geschäftstätigkeit und Prozesse in heutigen Organisationen standardisiert und normiert ist, wurden Normen entwickelt, die Qualitätsparameter für das Laserschneiden vorschreiben. Die ISO-Norm DIN EN ISO 9013:2002 definiert die Anforderungen an das Laserschneiden und andere Arten des thermischen Schneidens. Die Norm schreibt die Kontrolle der folgenden Schneidparameter vor:
- geschmolzenes Metall
- der Einschnitt
- die Punktion des Schnitts
- Schnittlinien
- Rauheit
Qualitätskontrollparameter
- Bildung des geschmolzenen Metalls – die Kontrolle dieses Parameters erfolgt normalerweise durch visuelle Inspektion des zu schneidenden Metalls. Die durch die Überprüfung erhaltenen Informationen beziehen sich auf den Fokus des Laserstrahls oder die Optik des Laserschneiders.
- Der Schnitteinschnitt – ein Parameter, der vom zu schneidenden Material abhängt und durch die Toleranz für jedes Metall unterschiedlich bestimmt wird. Die durch die Inspektion des Schnitts erhaltenen Informationen geben Aufschluss über die Größe der Eindringtiefe des Laserstrahls in das Metall.
- Der Einstich – Der Einstich im Metall entsteht durch Korrosion und kann die Qualität des Schnitts erheblich verändern. Dieser Parameter wird normalerweise visuell überprüft und qualitativ beschrieben.
- Schnittlinien – die Schnittlinien beim Laserschneiden werden durch die Geschwindigkeit bestimmt, mit der jede Position geschnitten wird. Dieser Parameter wird ebenfalls visuell überprüft, und die durch die Überprüfung gewonnenen Informationen geben Aufschluss über die Notwendigkeit, die Schnittparameter in Bezug auf Leistung und Geschwindigkeit anzupassen.
- Rauheit – ein Parameter, der den Bedarf an zusätzlicher Materialhandhabung nach dem Laserschneiden beeinflusst. Die Rauheit wird in Abhängigkeit von der Dicke des zu schneidenden Materials definiert.
Die Qualität von Laserschnitten lässt sich durch konsequente Wartung des Laserschneiders und Feinabstimmung der Schnittparameter verbessern. Qualitätskontrolle und Parameteroptimierung spielen zwar eine entscheidende Rolle, sind aber nur die ersten Schritte zum Erreichen optimaler Schnittergebnisse. Die Wirksamkeit der Qualitätskontrolle hängt von der Ausführung einer Reihe von Schnitten ab.
Wenn mehrere identische Schnitte durchgeführt werden, ist eine sorgfältige Kontrolle der Parameter unerlässlich, um die Wiederholung von Fehlern in der Serie zu verhindern. Daher gewährleistet die kontinuierliche Überwachung und Anpassung der Parameter konsistente und fehlerfreie Schneidvorgänge.
Faktoren, die die Laserschneidqualität von Laserschneidmaschinen beeinflussen
Strahleigenschaften:
Es besteht eine signifikante Beziehung zwischen der Schnittbreite beim Laserschneiden und dem Durchmesser des fokussierten Punkts. Da die Leistungsdichte und Energiedichte der Laserbestrahlung mit dem Durchmesser des Laserpunkts zusammenhängen, sollte der Durchmesser des Punkts beim Laserschneiden so klein wie möglich sein, um eine größere Leistungsdichte und Energieskala zu erhalten.
Laserleistung:
Die Stärke der Laserleistung wirkt sich direkt auf die Dicke der zu schneidenden Stahlplatte aus. Je höher die Leistung, desto dicker das zu schneidende Material. Darüber hinaus wirkt sie sich auch auf die Maßgenauigkeit des Werkstücks, die Breite der Schnittnaht, die Rauheit der Schnittfläche und die Breite der Wärmeeinflusszone aus.
Die Laserleistung hat einen erheblichen Einfluss auf Schnittgeschwindigkeit, Nahtbreite, Schnittdicke und Schnittqualität. Die Leistungsstufe wird durch die Materialeigenschaften und den Schneidmechanismus bestimmt. Materialien mit hohen Schmelzpunkten (wie Legierungen) und hoher Oberflächenreflexion (wie Kupfer und Aluminium) erfordern eine höhere Laserleistung.
Beispielsweise kann eine 1500-W-Faserlaserschneidmaschine für Metallbleche nicht die Leistung einer 6000-W-Laserschneidmaschine erreichen. Wenn Sie häufig feststellen, dass der Schneideffekt nicht optimal ist, ist es sehr wahrscheinlich, dass Sie das falsche Lasermodell gewählt haben.
Beim Laserschneiden gibt es eine Laserleistung, die die beste Schnittqualität erzielt. Bei dieser Laserleistung kann es zu unvollständigem Schneiden oder hängender Schlacke kommen. Bei höheren Leistungen kommt es zu Überhitzung.
Laserschneidgeschwindigkeit:
Die Schnittgeschwindigkeit hat einen erheblichen Einfluss auf die Schnittqualität. Die ideale Schnittgeschwindigkeit führt zu einer relativ glatten Linie auf der Schnittfläche, einem glatten Materialquerschnitt und keinen Graten. Wenn der Hilfsgasdruck und die Laserleistung konstant sind, besteht eine nichtlineare inverse Beziehung zwischen der Schnittgeschwindigkeit und der Schnittnahtbreite. Wenn die Schnittgeschwindigkeit zu langsam ist, kann es leicht zu einer Materialüberschmelzung kommen, die Schnittnaht wird breiter, die Wärmeeinflusszone vergrößert sich und sogar das Werkstück überschmilzt. Zu schnelles Schneiden kann dazu führen, dass das Material nicht durchgeschnitten wird, Funken spritzen, Schlacke in der unteren Hälfte entsteht und sogar die Linse verbrennt.
Düsen:
Die Öffnung der Düse und der Abstand zwischen Düsenauslass und Materialoberfläche können die Schneidwirkung beeinflussen.
Fokusposition:
Die Fokusposition beeinflusst direkt die Breite des Schnitts, die Rauheit des Querschnitts und die Anhaftung von Abfallrückständen. Die unterschiedlichen Fokuspositionen führen zu unterschiedlichen Strahldurchmessern und Brenntiefen auf der Oberfläche des bearbeiteten Materials, was zu Änderungen der Form der Schnittnaht führt und den Fluss des bearbeiteten Gases und des geschmolzenen Metalls innerhalb des Querschnitts beeinflusst.
Die Fokusposition ist der Abstand vom Laserfokus zur Oberfläche des Werkstücks, der sich direkt auf die Rauheit der Schnittfläche, die Neigung und Breite der Schnittnaht sowie den Haftstatus des geschmolzenen Rückstands auswirkt. Wenn die Fokusposition zu weit vorgerückt ist, erhöht dies die Wärmeaufnahme am unteren Ende des zu schneidenden Werkstücks.
Bei einer bestimmten Schnittgeschwindigkeit und einem bestimmten Hilfsluftdruck führt dies dazu, dass das zu schneidende Material und das geschmolzene Material in der Nähe der Schnittnaht in flüssigem Zustand auf die Unterseite fließen. Nach dem Abkühlen haftet das geschmolzene Material kugelförmig an der Unterseite des Werkstücks. Wenn die Position zurückbleibt, nimmt die von der unteren Endfläche des zu schneidenden Materials aufgenommene Wärme ab, so dass das Material in der Schnittnaht nicht vollständig schmelzen kann und einige scharfe und kurze Rückstände an der Unterseite der Platte haften bleiben.
Normalerweise sollte der Fokus auf der Oberfläche des Werkstücks oder etwas darunter liegen, aber unterschiedliche Materialien erfordern unterschiedliche Anforderungen. Beim Schneiden von Kohlenstoffstahl ist die Schnittqualität besser, wenn der Fokus auf der Oberfläche der Platte liegt. Beim Schneiden von Edelstahl sollte der Fokus für bessere Ergebnisse etwa bei der Hälfte der Plattendicke liegen.
Hilfsgas:
Beim Materialschneiden ist die Verwendung von Hilfsgas erforderlich. Dabei kommt es vor allem auf den Gasdruck und die Gasart an. Beides kann sich auf die Rauheit des Schneidbereichs und die Schlackenbildung auswirken.
Beim Laserschneiden spielt der Hilfsluftdruck eine Rolle beim Abblasen von Schlacke, beim Kühlen von Materialien und bei der Unterstützung der Verbrennung. Zu den Hilfsgasen zählen Sauerstoff, Druckluft, Stickstoff und Inertgase.
Sauerstoff kann an der Metallverbrennung teilnehmen und die Schneidleistung verbessern, sodass es zum Schneiden der meisten Metalle geeignet ist; Inertgase und Luft eignen sich zum Schneiden bestimmter Metallmaterialien (wie Aluminiumlegierungen) und nichtmetallischer Materialien, da sie eine Materialverbrennung verhindern können.
Wenn der Hilfsgasdruck zu hoch ist, treten Wirbelströme auf der Oberfläche des Materials auf, die die Fähigkeit zum Entfernen geschmolzener Materialien schwächen, was zu einer Verbreiterung der Schnittnaht und einer rauen Schnittoberfläche führt. Wenn der Luftdruck zu niedrig ist, kann das geschmolzene Material nicht vollständig weggeblasen werden und Schlacke haftet an der Unterseite des Materials. Daher sollte der Hilfsgasdruck während des Schneidens angepasst werden, um die beste Schnittqualität zu erzielen.
Qualitätslösungen zum Laserschneiden für Faserlaserschneidmaschinen
- Optimale Energieeinstellungen: Die Anpassung der Laserleistungseinstellungen an Materialart und -dicke ist entscheidend für saubere und präzise Schnitte. Die Feinabstimmung der Leistungsparameter gewährleistet eine effiziente Materialbearbeitung, ohne dass übermäßige Wärmeeinflusszonen oder raue Kanten entstehen.
- Fokuseinstellung: Die richtige Fokussierung des Laserstrahls ist für die Aufrechterhaltung der Schnittqualität von entscheidender Bedeutung. Regelmäßiges Kalibrieren und Anpassen der Fokusposition gewährleistet optimale Strahlqualität und Schnittleistung.
- Gasauswahl und Druckregelung: Durch die Wahl des geeigneten Hilfsgases (wie Sauerstoff, Stickstoff oder Luft) und die Kontrolle seines Drucks wird geschmolzenes Material effektiv aus dem Schnitt entfernt und Oxidation während des Schneidens verhindert. Die richtige Gasauswahl und Druckeinstellung tragen zu einer verbesserten Kantenqualität und einer geringeren Bartbildung bei.
- Wartung der Düse und der Linse: Regelmäßige Reinigung und Inspektion von Schneiddüsen und Fokussierlinsen sind unerlässlich, um Schmutzablagerungen vorzubeugen und die Strahlqualität aufrechtzuerhalten. Ersetzen Sie abgenutzte oder beschädigte Komponenten umgehend, um eine gleichbleibende Schneidleistung sicherzustellen.
- Fortschrittliche Schneidkopftechnologie: Durch ein Upgrade auf Schneidköpfe mit erweiterten Funktionen wie automatischer Brennweiteneinstellung, Kollisionsschutz und Echtzeitüberwachung können Sie die Schneidpräzision und Produktivität verbessern.
- Dynamische Strahlsteuerung: Die Implementierung dynamischer Strahlsteuerungstechnologien wie Strahlformung und Strahlschwingung ermöglicht eine feinere Kontrolle der Intensitätsverteilung des Laserstrahls und verbessert die Schnittqualität, insbesondere bei komplexen Geometrien und engen Ecken.
- Materialhandhabung und Vorrichtung: Die richtige Materialhandhabung und Vorrichtungstechniken tragen dazu bei, Vibrationen und Materialverzerrungen während des Schneidens zu minimieren, was zu glatteren Schnitten und verbesserter Maßgenauigkeit führt.
- Optimierte Schnittparameter: Durch die Feinabstimmung von Schneidparametern wie Schnittgeschwindigkeit, Beschleunigung und Strahlausrichtung auf der Grundlage von Materialeigenschaften und Schneidanforderungen können Schnittqualität und -effizienz erheblich verbessert werden.
- Qualitätssicherungssysteme: Die Implementierung von Qualitätssicherungssystemen wie Echtzeitüberwachung, automatischer Fehlererkennung und Feedback-Mechanismen gewährleistet eine gleichbleibende und zuverlässige Schnittqualität während des gesamten Produktionsprozesses.
Durch die Implementierung dieser Lösungen können Betreiber die Leistung optimieren von Faserlaser-Schneidemaschinen und erzielen Sie eine überragende Schnittqualität bei einer breiten Palette von Materialien und Anwendungen.