Metall schneiden mit Laser Die Laser-Schneidtechnologie ist eine hochentwickelte Technik, die die Kraft konzentrierter Laserstrahlen nutzt, um verschiedene Metallarten präzise zu schneiden. Diese Methode wird für ihre bemerkenswerte Präzision, Geschwindigkeit und Anpassungsfähigkeit geschätzt und ist daher die bevorzugte Wahl für eine Vielzahl von Branchen, von der Automobilherstellung bis hin zur Luft- und Raumfahrt und Elektronik.
Beim Laserschneiden wird ein Hochleistungslaser auf das Metall gerichtet, der das Material entlang eines bestimmten Pfads erhitzt, schmilzt oder verdampft, wodurch saubere und präzise Schnitte mit minimalem Abfall entstehen. In diesem Handbuch werden die umfassenden Aspekte des Metallschneidens mit dem Laser untersucht. Dabei werden die einzigartigen Fähigkeiten des Lasers, die Arten von Metallen, die geschnitten werden können, die Vorteile, die es bietet, gängige Anwendungen und wichtige Parameter beschrieben, die die Effizienz und Qualität des Schneidens beeinflussen.
Kann Metall mit einem Laser geschnitten werden?
Ja, Metall kann mit einem Laser geschnitten werden. Laserschneiden ist eine weit verbreitete Methode zum Schneiden verschiedener Metalle, darunter Stahl, Aluminium, Edelstahl, Messing und Kupfer. Bei diesem Verfahren wird ein hochfokussierter Laserstrahl verwendet, der das Metall schmilzt, verbrennt oder verdampft und so präzise Schnitte mit hoher Genauigkeit erzeugt. Es handelt sich um eine effiziente und vielseitige Technik, die dafür bekannt ist, saubere Kanten zu erzeugen, Materialabfall zu reduzieren und komplexe Formen zu erreichen, die mit herkömmlichen Schneidemethoden eine Herausforderung darstellen könnten.
Moderne Laserschneidmaschinen können unterschiedliche Stärken und Metallarten verarbeiten und erfreuen sich daher in Branchen wie der Automobil-, Luft- und Raumfahrt-, Elektronik- und Bauindustrie großer Beliebtheit.
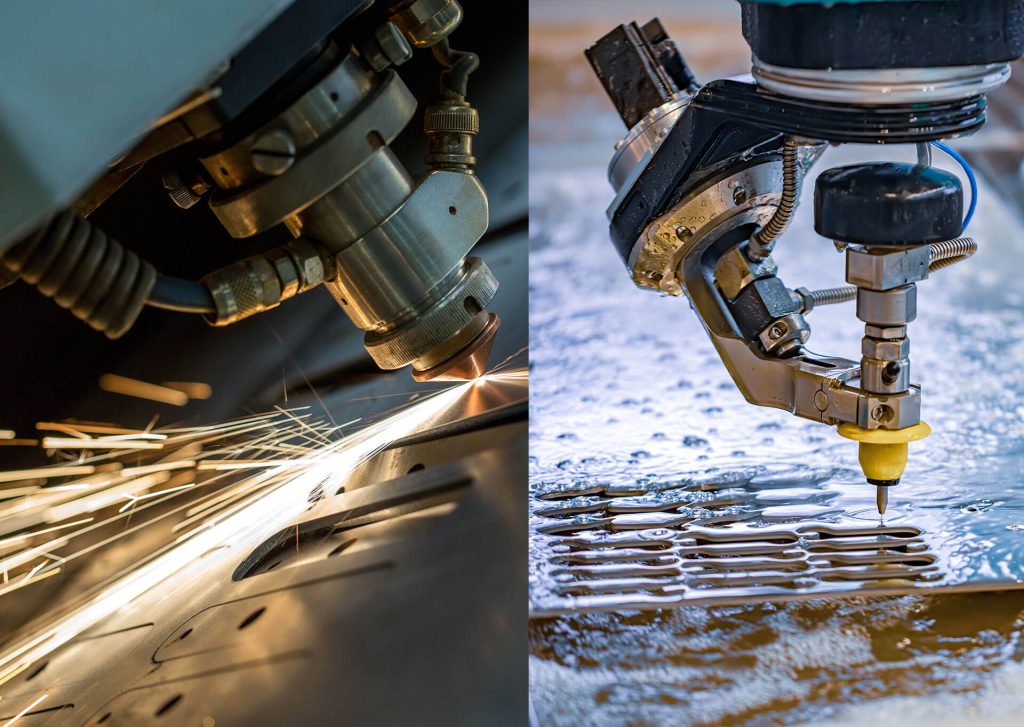
Wie funktioniert das Laserschneiden von Metall?
Das Laserschneiden von Metall ist ein anspruchsvoller Prozess, bei dem ein hochkonzentrierter Laserstrahl verwendet wird, um Metall präzise zu schneiden. Die intensive Hitze des Lasers schmilzt, verbrennt oder verdampft das Metall und erzeugt scharfe und saubere Kanten. Im Folgenden sind die erweiterten Schritte des Laserschneidens von Metall aufgeführt:
1. Schnittmuster entwerfen
Der erste Schritt besteht darin, mithilfe von CAD (Computer Aided Design) oder anderer Grafiksoftware ein präzises Design oder Schnittmuster zu erstellen. Diese Designs sind oft kompliziert und werden an die spezifischen Projektanforderungen angepasst, sodass Hersteller das Endprodukt bereits vor dem Schneiden visualisieren können. Die CAD-Datei wird dann in ein maschinenlesbares Format wie DXF oder DWG konvertiert, um den Laserschneider während des Prozesses zu steuern.
2. Konfigurieren des Laserschneiders
Sobald das Design fertig ist, muss der Laserschneider konfiguriert werden. Der Bediener passt mehrere wichtige Parameter je nach Metallart, Metalldicke und gewünschter Schnittqualität an:
- Energieeinstellungen: Bestimmt die Energieabgabe des Lasers, die sich auf Schnitttiefe und -geschwindigkeit auswirkt.
- Schnittgeschwindigkeit: Beeinflusst die Präzision und Kantenqualität; langsamere Geschwindigkeiten werden für dickere Metalle verwendet, während schnellere Geschwindigkeiten für dünnere Materialien geeignet sind.
- Fokuseinstellung: Stellt sicher, dass der Laserstrahl für optimale Genauigkeit auf den richtigen Punkt auf der Metalloberfläche konzentriert wird.
Moderne Laserschneider können außerdem über automatische Konfigurationsfunktionen verfügen, wodurch der Bedarf an manuellen Anpassungen reduziert und die Konsistenz verbessert wird.
3. Das Metall schneiden
Wenn der Laserschneider konfiguriert ist, beginnt die Maschine, das Metall zu schneiden, indem sie dem Designmuster folgt. Der Laserstrahl, der von einer CNC-Steuerung (Computerized Numerical Control) gesteuert wird, bewegt sich entlang des vordefinierten Pfads und schmilzt oder verdampft das Metall genau dort, wo es nötig ist. Dies führt zu glatten und präzisen Schnitten, selbst bei komplexen Formen oder detaillierten Designs. Hochleistungslaser wie Faser- oder CO2-Laser werden häufig verwendet, um verschiedene Metallarten und -dicken zu bearbeiten, von dünnen Aluminiumblechen bis hin zu dickem Edelstahl.
4. Kühlung und Nachbearbeitung
Nachdem das Metall geschnitten wurde, wird es abgekühlt, sodass das Material wieder eine stabile Temperatur erreicht. Dies verhindert Verformungen oder Deformationen durch Restwärme. Jeglicher Schmutz, Schlacke oder Bart (Rückstände vom Schneidprozess) wird sorgfältig entfernt, um ein sauberes Finish zu gewährleisten. Je nach Projekt können zusätzliche Nachbearbeitungsschritte Folgendes umfassen:
- Entgraten: Entfernen scharfer Kanten oder Grate aus dem Schneidevorgang, um Sicherheit und ein edles Erscheinungsbild zu gewährleisten.
- Auftragen von Schutzbeschichtungen: In einigen Fällen werden Schutzbeschichtungen oder Behandlungen aufgetragen, um die Korrosions- oder Verschleißbeständigkeit des Metalls zu verbessern.
- Qualitätskontrolle: Das Endprodukt wird auf Präzision und Qualität geprüft, um sicherzustellen, dass es die in der Entwurfsphase festgelegten Spezifikationen erfüllt.
Durch dieses detaillierte, schrittweise Vorgehen beim Laserschneiden von Metall entstehen hochwertige Komponenten mit hervorragender Maßgenauigkeit, minimalem Abfall und einer Oberfläche, die sofort einsatzbereit oder zur Weiterverarbeitung bereit ist.
Parameter des Metallschneidens mit dem Laser
Beim Metallschneiden mit einem Laser müssen mehrere Schlüsselparameter genau kontrolliert werden, um optimale Schneidleistung und -qualität zu gewährleisten. Diese Parameter wirken sich direkt auf die Effizienz, Genauigkeit und das Finish des Schnitts aus:
1. Laserleistung
Die Laserleistung ist ein entscheidender Parameter, der die Energieabgabe des Lasers bestimmt und in Watt (W) oder Kilowatt (kW) gemessen wird. Eine höhere Laserleistung ermöglicht das Schneiden dickerer Metalle und erhöht die Schneidgeschwindigkeit, aber übermäßige Leistung kann zu rauen Kanten oder übermäßiger Hitze führen. Die richtige Leistungsstufe wird basierend auf der Art und Dicke des zu schneidenden Metalls ausgewählt, um optimale Ergebnisse zu erzielen.
2. Schnittgeschwindigkeit
Die Schnittgeschwindigkeit bezeichnet die Geschwindigkeit, mit der sich der Laserschneider über die Metalloberfläche bewegt. Sie hat direkte Auswirkungen auf die Schnittqualität und beeinflusst Faktoren wie Kantenglätte und Präzision. Niedrigere Geschwindigkeiten ermöglichen feinere, präzisere Schnitte, insbesondere bei dickeren Materialien, während höhere Geschwindigkeiten für dünnere Bleche geeignet sind und die Gesamtproduktionseffizienz verbessern können.
3. Pulsfrequenz
Die Pulsfrequenz oder die Anzahl der Laserpulse pro Sekunde beeinflusst die Schnittgeschwindigkeit, Präzision und Größe der Wärmeeinflusszone (WEZ). Eine höhere Pulsfrequenz kann die Schnittglätte verbessern und die Oberflächenrauheit verringern, während bei dickeren Materialien normalerweise eine niedrigere Frequenz verwendet wird, um einen ausreichenden Materialabtrag ohne Überhitzung sicherzustellen.
4. Fokusfleckgröße
Die Fokuspunktgröße stellt den Durchmesser des Laserstrahls an seinem Brennpunkt auf der Metalloberfläche dar. Ein kleinerer Fokuspunkt erzeugt einen schmaleren Schnitt mit mehr Details und Schärfe, was ihn ideal für komplizierte Designs macht. Größere Punktgrößen werden für eine höhere Schneidleistung verwendet und eignen sich besser für dickere Metalle, bei denen feine Details weniger wichtig sind.
5. Unterstützungsgasdruck
Der Druck des Hilfsgases spielt beim Laserschneiden eine entscheidende Rolle, da er dabei hilft, geschmolzenes Material aus dem Schneidbereich zu entfernen, das Metall abzukühlen und die Oxidation zu verringern. Der Druck und die Art des Hilfsgases – normalerweise Sauerstoff, Stickstoff oder Luft – hängen von den Eigenschaften und der Dicke des Metalls ab:
- Sauerstoff wird für schnellere Schnittgeschwindigkeiten und dickere Metalle verwendet, kann aber zu leichter Oxidation führen.
- Stickstoff verhindert Oxidation und wird bevorzugt bei Edelstahl und Aluminium verwendet um saubere Kanten zu erzielen.
- Luft ist eine kostengünstige Alternative für weniger kritische Anwendungen und bietet eine moderate Schneidleistung.
Durch das Ausbalancieren dieser Parameter wird sichergestellt, dass der Laserschneidvorgang hinsichtlich Effizienz, Präzision und Qualität optimiert ist und saubere und konsistente Ergebnisse bei verschiedenen Metallarten und -dicken erzielt werden.
Lasertypen zum Schneiden von Metallen
Es gibt verschiedene Arten von Laserschneidern, die häufig zum Metallschneiden verwendet werden. Jeder hat je nach Anwendung einzigartige Funktionen und Vorteile. Zu den wichtigsten Typen gehören:
1. Faserlaserschneider
Faserlaserschneider gehören zu den beliebtesten und modernsten Optionen für das Metallschneiden. Sie verwenden eine Festkörperlaserquelle, bei der der Laserstrahl von einem Seedlaser erzeugt und dann mithilfe von Glasfasern verstärkt wird. Diese Laser sind hocheffizient und bieten im Vergleich zu anderen Typen schnellere Schneidgeschwindigkeiten und niedrigere Betriebskosten.
Vorteile:
- Hervorragend geeignet zum Schneiden von Metallen, insbesondere reflektierenden Materialien wie Aluminium, Messing und Kupfer.
- Hohe Schnittgeschwindigkeit und Energieeffizienz.
- Langlebig und wartungsarm durch weniger bewegliche Teile.
Anwendungen: Ideal für Branchen wie die Automobil-, Luft- und Raumfahrt- und Elektronikindustrie, in denen hohe Präzision und schnelle Produktion unerlässlich sind.
2. CO2-Laserschneider
CO2-Laserschneider sind traditionelle Laserschneidmaschinen, die zur Erzeugung des Laserstrahls ein Gasgemisch (hauptsächlich Kohlendioxid) verwenden. Diese Laser sind für ihre Fähigkeit bekannt, nichtmetallische Materialien sowie Metalle zu schneiden.
Vorteile:
- Kann eine Vielzahl von Materialien schneiden, darunter Metalle, Holz, Kunststoffe und Glas.
- Hochwertige Schnitte für dickere Metalle.
- Vielseitig für Schneide- und Gravuranwendungen.
Anwendungen: Wird häufig in der Fertigungs-, Bau- und Dekorationsindustrie verwendet, insbesondere für dickere oder nichtmetallische Materialien.
3. Nd (Neodym-dotierter Yttrium-Aluminium-Granat) Laserschneider
Nd-Laser sind Festkörperlaser, die einen Kristall als Lasermedium verwenden. Diese Laser liefern hochintensive Strahlen mit kurzen Impulsen und eignen sich daher für bestimmte Schneide- und Gravuraufgaben.
Vorteile:
- Hohe Spitzenleistung, geeignet zum tiefen Schneiden und Schweißen von Metallen.
- Effektiv zum Markieren und Gravieren von Metallen mit komplizierten Details.
- Funktioniert gut mit Metallen, die kurze, intensive Energiestöße erfordern.
Anwendungen: Wird häufig für Spezialanwendungen wie Schweißen, Markieren und Gravieren in Branchen wie der Schmuck-, Elektronik- und Medizingerätebranche verwendet.
4. Scheibenlaserschneider
Scheibenlaserschneider sind eine Variante des Festkörperlasers, ähnlich wie Faserlaser, verwenden jedoch einen scheibenförmigen Kristall als Verstärkungsmedium. Sie bieten eine Kombination aus hoher Leistung und hervorragender Strahlqualität.
Vorteile:
- Stabile Leistungsabgabe und hohe Strahlqualität.
- Effizient für dicke Metalle und anspruchsvolle Schneidarbeiten.
- Hohe Energiedichte, die präzise und tiefe Schnitte ermöglicht.
Anwendungen: Geeignet für schwere Industrieanwendungen, insbesondere beim Bearbeiten von dicken oder harten Metallen.
5. Hybrid-Laserschneider
Hybrid-Laserschneider kombinieren verschiedene Lasertechnologien, wie beispielsweise die Integration von CO2- und Faserlasern, um eine vielseitige Maschine zu schaffen, die sowohl Metalle als auch Nichtmetalle mit hoher Effizienz schneiden kann. So können Hersteller von den Stärken jedes Typs profitieren.
Vorteile:
- Bietet Flexibilität beim Schneiden unterschiedlicher Materialarten.
- Kombiniert die Vorteile mehrerer Lasertypen und verbessert die Anpassungsfähigkeit.
- Kann verschiedene Schneide- und Gravurprojekte bewältigen.
Anwendungen: Wird in Branchen verwendet, in denen sowohl Metall- als auch Nichtmetall-Schneidfähigkeiten erforderlich sind, wie z. B. Beschilderung, Fertigung und Sonderanfertigung.
6. Direktdiodenlaserschneider (DDL)
Direkte Diodenlaser verwenden Dioden, um den Laserstrahl direkt zu erzeugen, ohne dass ein Verstärkungsmedium wie bei Faser- oder Scheibenlasern erforderlich ist. Dies führt zu einer effizienten und kompakten Maschine.
Vorteile:
- Hohe Effizienz bei geringem Stromverbrauch.
- Kompaktes und einfaches Design mit minimalem Wartungsaufwand.
- Geeignet für Metalle mit dünner und mittlerer Dicke.
Anwendungen: Häufig zu finden in Leichtindustrieanwendungen, im Automobilbau und in der Blechverarbeitung.
Die Auswahl der verschiedenen Laserschneidertypen erfolgt auf der Grundlage von Faktoren wie Materialart, Dicke, erforderlicher Präzision und spezifischen Industrieanforderungen, um für jede Metallschneidaufgabe optimale Ergebnisse zu gewährleisten.
Metallschneiden mit dem Laser: Detaillierte Erklärung
Verschiedene Metallarten haben einzigartige Eigenschaften, die sie zum Laserschneiden geeignet machen. Hier ist ein kurzer Überblick über jedes dieser Metalle und ihre physikalischen und chemischen Eigenschaften:
Weichstahl (Kohlenstoffstahl)
Weichstahl, auch Kohlenstoffstahl genannt, ist eine beliebte Wahl zum Laserschneiden. Er ist erschwinglich, langlebig und bietet hervorragende Schweißeigenschaften. Mit einem Kohlenstoffgehalt von bis zu 0,3% ist er nicht so spröde wie kohlenstoffreichere Stähle.
- Schmelzpunkt: 2.600 bis 2.800 Grad Fahrenheit
- Zugfestigkeit: 370-500 MPa
- Spezifisches Gewicht: 7,85
Edelstahl
Edelstahl ist eine korrosionsbeständige Legierung, die sich ideal für eine Vielzahl von Anwendungen zum Laserschneiden von Edelstahl eignet. Er bietet eine gute Festigkeit und eine ausgezeichnete Oxidationsbeständigkeit.
- Schmelzpunkt: 2.550 bis 2.750 Grad Fahrenheit
- Zugfestigkeit: 515 MPa
- Spezifisches Gewicht: 7,93
Aluminium
Aluminium ist ein leichtes, weiches und dehnbares Metall mit hervorragender Korrosionsbeständigkeit, weshalb sich das Laserschneiden von Aluminium ideal für eine Reihe industrieller Anwendungen eignet.
- Schmelzpunkt: 1.220 Grad Fahrenheit
- Zugfestigkeit: 90-140 MPa
- Spezifisches Gewicht: 2,70
Messing
Messing ist eine Legierung aus Kupfer und Zink. Es lässt sich leicht bearbeiten, ist korrosionsbeständig und eignet sich hervorragend für dekorative Zwecke.
- Schmelzpunkt: 1.650 bis 1.720 Grad Fahrenheit
- Zugfestigkeit: 345-470 MPa
- Spezifisches Gewicht: 8,4-8,73
Kupfer
Kupfer hat eine ausgezeichnete Wärme- und Stromleitfähigkeit. Es ist zäh, dehnbar und lässt sich gut schweißen und löten.
- Schmelzpunkt: 1.984 Grad Fahrenheit
- Zugfestigkeit: 210-360 MPa
- Spezifisches Gewicht: 8,96
Verzinkter Stahl
Bei verzinktem Stahl handelt es sich um Stahl, der zur Verbesserung seiner Korrosionsbeständigkeit mit einer Zinkschicht überzogen wurde.
- Schmelzpunkt: 2.600 bis 2.800 Grad Fahrenheit
- Zugfestigkeit: 330-505 MPa
- Spezifisches Gewicht: 7,85
Titan
Titan ist für seine Festigkeit, Leichtigkeit und Korrosionsbeständigkeit bekannt. Es ist eines der am schwierigsten zu schneidenden Metalle, kann aber durch Laserschneiden effizient bearbeitet werden.
- Schmelzpunkt: 3.034 Grad Fahrenheit
- Zugfestigkeit: 240-370 MPa
- Spezifisches Gewicht: 4,506
Nickellegierungen
Nickellegierungen sind korrosionsbeständig und können ihre strukturelle Integrität bei hohen Temperaturen beibehalten, was sie ideal für den Einsatz in rauen Umgebungen macht.
- Schmelzpunkt: Variiert je nach Legierung
- Zugfestigkeit: Variiert je nach Legierung
- Spezifisches Gewicht: Variiert je nach Legierung
Silber
Silber ist ein weiches, weißes, glänzendes Metall mit der höchsten elektrischen und thermischen Leitfähigkeit aller Metalle.
- Schmelzpunkt: 1.762 Grad Fahrenheit
- Zugfestigkeit: 170 MPa
- Spezifisches Gewicht: 10,49
Gold
Gold ist ein dichtes, weiches, glänzendes Metall und von allen bekannten Metallen am formbarsten und dehnbarsten.
- Schmelzpunkt: 1.948 Grad Fahrenheit
- Zugfestigkeit: 120 MPa
- Spezifisches Gewicht: 19,32
Platin
Platin ist ein dichtes, formbares, dehnbares, äußerst reaktionsträges Edelmetall mit einer silberweißen Farbe.
- Schmelzpunkt: 3.215 Grad Fahrenheit
- Zugfestigkeit: 125-240 MPa
- Spezifisches Gewicht: 21,45
Zink
Zink ist ein bläulich-weißes, glänzendes, diamagnetisches Metall. Es hat eine etwas geringere Dichte als Eisen und eine hexagonale Kristallstruktur.
- Schmelzpunkt: 787,15 Grad Fahrenheit
- Zugfestigkeit: 110-200 MPa
- Spezifisches Gewicht: 7,14
Zinn
Zinn ist ein formbares, dehnbares, hochkristallines, silberweißes Metall. Seine Hauptanwendung ist der Korrosionsschutz.
- Schmelzpunkt: 449,47 Grad Fahrenheit
- Zugfestigkeit: 9-14 MPa
- Spezifisches Gewicht: 7,265
Führen
Blei ist ein Schwermetall, das eine höhere Dichte als die meisten üblichen Materialien aufweist. Es ist weich und formbar und hat einen relativ niedrigen Schmelzpunkt.
- Schmelzpunkt: 621,43 Grad Fahrenheit
- Zugfestigkeit: 17 MPa
- Spezifisches Gewicht: 11,34
Inconel
Inconel ist eine Familie austenitischer Superlegierungen auf Nickel-Chrom-Basis. Es ist oxidations- und korrosionsbeständig und weist auch bei hohen Temperaturen eine gute Leistung auf.
- Schmelzpunkt: 2.350 bis 2.500 Grad Fahrenheit
- Zugfestigkeit: 690-965 MPa
- Spezifisches Gewicht: 8,2
Welches Metall eignet sich am besten zum Laserschneiden?
Welches Metall sich am besten zum Laserschneiden eignet, hängt von der jeweiligen Anwendung und den Anforderungen ab. Am häufigsten werden jedoch aufgrund ihrer hervorragenden Bearbeitbarkeit und Kompatibilität mit dem Laserschneiden Weichstahl, Edelstahl und Aluminium verwendet.
Methoden, die bei Laserschneidprozessen verwendet werden
Beim Laserschneiden gibt es verschiedene Methoden, um unterschiedliche Materialien zu schneiden. Im Folgenden werden einige gängige Methoden des Laserschneidens vorgestellt, darunter Verdampfen, Schmelzen und Blasen, thermische Spannungsrissbildung, Stealth-Dicing und brennstabilisiertes Laserschneiden.
Verdampfungsschneiden
Beim Verdampfungsschneiden erhitzt der fokussierte Strahl die Oberfläche des Materials bis zu einem Flammpunkt und erzeugt ein Schlüsselloch. Das Schlüsselloch verursacht einen abrupten Anstieg der Absorption, wodurch das Loch schnell tiefer wird. Während das Loch tiefer wird und das Material siedet, erodiert der erzeugte Dampf die geschmolzenen Wände, bläst den Auswurf heraus und vergrößert das Loch noch weiter. Mit diesem Verfahren werden üblicherweise nicht schmelzende Materialien wie Holz, Kohlenstoff und Duroplaste geschnitten.
Reaktives Schneiden/Brennschneiden
Reaktives Schneiden ist auch als „Brennschneiden“ und „brennend stabilisiertes Lasergasschneiden“ bekannt. Reaktives Schneiden ähnelt dem Sauerstoffbrennschneiden, außer dass der Laserstrahl die Zündquelle ist. Dieses Verfahren ist häufig zum Schneiden von Kohlenstoffstahl mit Dicken über 1 mm vorgesehen. Darüber hinaus kann es zum Schneiden sehr dicker Stahlplatten mit relativ geringer Laserleistung eingesetzt werden.
Schmelz- und Blasschneiden/Fusionsschneiden
Beim Schmelz- und Blasschneiden, auch Schmelzschneiden genannt, wird unter hohem Druck stehendes Gas verwendet, um geschmolzenes Material aus dem Schnittbereich wegzublasen, wodurch der Energiebedarf erheblich gesenkt wird. Das Material wird zunächst bis zu seinem Schmelzpunkt erhitzt. Ein Gasstrahl bläst das geschmolzene Material aus dem Schnitt, sodass die Temperatur des Materials nicht mehr erhöht werden muss. Mit dieser Methode werden häufig Metalle geschnitten.
Thermisches Spannungsrissschneiden
Beim thermischen Spannungsrissschneiden wird die Eigenschaft ausgenutzt, dass spröde Materialien besonders anfällig für thermische Brüche sind. Ein konzentrierter Strahl wird auf die Oberfläche gerichtet, was zu lokaler Erwärmung und thermischer Ausdehnung führt. Dadurch entsteht ein Riss, der durch Bewegen des Strahls gerichtet werden kann. Der Riss kann in m/s bewegt werden. Thermisches Spannungsrissschneiden wird häufig beim Glasschneiden verwendet.
Stealth-Dicing-Schneiden von Silizium-Wafern
Beim Stealth-Dicing-Verfahren werden bei der Herstellung von Halbleiterbauelementen Mikroelektronikchips von Siliziumwafern getrennt. Dabei kommt ein gepulster Nd:YAG-Laser zum Einsatz, dessen Wellenlänge perfekt an die elektronische Bandlücke von Silizium angepasst ist.
Vor- und Nachteile des Metall-Laserschneidens
Das Laserschneiden von Metall hat die Fertigungsindustrie revolutioniert und bietet präzise und effiziente Lösungen für verschiedene Anwendungen. Nachfolgend finden Sie die wichtigsten Vor- und Nachteile dieser Fertigungstechnik.
Vorteile des Metallschneidens mit dem Laser
Hohe Präzision und Genauigkeit
Das Laserschneiden von Metall ist für seine außergewöhnliche Präzision und Genauigkeit bekannt. Laserstrahlen können komplizierte Schnitte und Formen mit minimalen Abweichungen erzielen und so hochwertige Endteile gewährleisten. Im Allgemeinen können die Teile mit einer Toleranz von 0,2 mm lasergeschnitten werden. Die hohe Präzision des Laserschneidens ist besonders in Branchen wie der Luft- und Raumfahrt, der Elektronik und der Medizintechnik wertvoll, in denen Toleranzen von entscheidender Bedeutung sind.
Materialvielfalt
Laserschneiden kann verschiedene Metallmaterialien verarbeiten, darunter Edelstahl, Aluminium, Weichstahl, Legierungen und exotische Metalle. Diese Vielseitigkeit ermöglicht es Herstellern, unterschiedliche Projektanforderungen zu erfüllen, ohne dass Werkzeugwechsel erforderlich sind, was Rüstzeit und -kosten reduziert. Es ist auch für verschiedene Dicken geeignet und somit eine vielseitige Option für unterschiedliche Anwendungen.
Schneideflexibilität
Die Laserschneidverfahren sind äußerst vielseitig und flexibel. Ein einzelner Laserschneider kann verschiedene Schneidaufgaben ausführen, darunter einfache Schnitte, anspruchsvolle Schnitte mit komplexen Details, Markierungen, Bohrungen und sogar Gravuren. Daher müssen die Hersteller während des Prozesses nicht ständig die Werkzeuge austauschen.
Geschwindigkeit und Effizienz
Nach der Programmierung können Teile in Sekundenschnelle geschnitten werden, viel schneller als bei Plasma- oder Wasserstrahlschneidverfahren. Hohe Schnittgeschwindigkeiten, schnelles Durchstechen und Schnittbreiten führen zu kürzeren Produktionszyklen und erhöhtem Durchsatz.
Geringer Stromverbrauch
Im Gegensatz zu anderen Schneidgeräten müssen bei Laserschneidern keine einzelnen Teile des Geräts bewegt werden. Dadurch können sie Material mit minimalem Stromverbrauch schneiden. Während Laserschneider bis zu 10 kW Energie benötigen, können die meisten anderen Vorgänge bis zu fünfmal so viel Energie benötigen. Gleichzeitig schont der geringe Stromverbrauch auch den Geldbeutel.
Kontaktloser Prozess
Im Gegensatz zu mechanischen Schneidverfahren ist das Laserschneiden ein berührungsloser Prozess. Dadurch wird das Risiko einer Materialverunreinigung verringert und es kommt zu keinem Werkzeugverschleiß, was die Wartungs- und Austauschkosten minimiert.
Nachteile des Metallschneidens mit dem Laser
Hohe Anfangskapitalinvestition
Die Anschaffung und Einrichtung hochwertiger Laserschneider erfordert eine erhebliche Anfangsinvestition. Die Kosten eines typischen Laserschneiders können doppelt so hoch sein wie die Kosten eines Wasserstrahl- oder Plasmaschneiders. Für kleine Unternehmen oder Startups sind die Anschaffungskosten möglicherweise unerschwinglich, doch die langfristigen Vorteile können die anfänglichen Ausgaben überwiegen.
Betriebskosten
Obwohl Laserschneiden effizient ist, können sich im Laufe der Zeit Betriebskosten aufgrund von Stromverbrauch, Gasversorgung und Wartungsanforderungen ergeben. Regelmäßige Wartung und Instandhaltung sind unerlässlich, um eine gleichbleibende Leistung zu gewährleisten.
Einschränkungen bei reflektierendem Material
Während sich das Laserschneiden für eine Vielzahl von Metallen eignet, können bestimmte Materialien, wie reflektierende Metalle wie Messing oder polierter Edelstahl, aufgrund ihrer hohen Reflektivität eine größere Herausforderung darstellen. Um diese Einschränkungen zu überwinden, können zusätzliche Maßnahmen erforderlich sein, wie die Verwendung spezieller Gase oder Beschichtungen.
Wärmeeinflusszone (WEZ)
Beim Laserschneiden wird Hitze erzeugt, wodurch entlang der Schnittkanten eine hitzebeeinflusste Zone entsteht. Dies kann zu Materialverzerrungen führen, insbesondere bei dünneren Materialien, was möglicherweise die Integrität des Endprodukts beeinträchtigt. Daher kann in einigen Anwendungsfällen eine Nachbearbeitung erforderlich sein.
Professionellen Bediener erforderlich
Um das Beste aus Ihren Laserschneidern herauszuholen, benötigen Sie möglicherweise einen professionellen und erfahrenen Bediener, der die Maschine während der Teilefertigung bedient. Auf diese Weise kann der Bediener schnell einen Fehler oder eine falsche Einrichtung erkennen, die den Fertigungsbetrieb oder die Integrität der Maschine beeinträchtigen könnte.
Einschränkungen hinsichtlich der Metalldicke
Obwohl das Laserschneiden bei einer Vielzahl von Materialien gut funktioniert, empfiehlt es sich, dicke Metalle mit alternativen Methoden zu schneiden. Herkömmliche Laserschneider eignen sich hervorragend zum Schneiden von Aluminiumblechen bis zu einer Dicke von 15 mm und Stahl bis zu einer Dicke von 6 mm.
Designtipps für das perfekte lasergeschnittene Metall
Hier sind einige Designtipps, die Ihnen dabei helfen, den bestmöglichen Laserschnitt zu erzielen:
- Schließen Sie die Kanten Ihres Designs. Alle Stellen, die offen oder frei von Metall sein sollen, müssen von einer vollständigen, geschlossenen Kontur umgeben sein. Wenn Sie beispielsweise einen Kreis aus einem Blech laserschneiden möchten, stellen Sie sicher, dass der Bogen in Ihrer Datei ein vollständig verbundener Kreis ist.
- Achten Sie auf die Metalllaschen und Kerben. Durch die richtige Verwendung von Laschen und Kerben bleibt die strukturelle Integrität des Metallblechs oder der Metallplatte während der Herstellung des Produkts erhalten.
- Linienstärke und -tiefe ermitteln. Klären und identifizieren Sie beim Senden Ihrer Datei, was jeder Linienstil bedeutet.
- Planen Sie präzise Löcher und lasern Sie entsprechend. Wenn Sie Löcher mit engen Toleranzen erzielen möchten, empfiehlt es sich, einen Laserschneider zu verwenden, um die vorgesehenen Stellen für die Löcher zu bohren und zu ätzen. Bohren Sie die Löcher anschließend gerade mit einem Bohrer.
- Entscheiden Sie sich für abgerundete Metallecken oder scharfe Winkel. Scharfe Ecken kommen bei Blechteilen häufig vor. Um die Sicherheit zu erhöhen, können scharfe Ecken abgerundet werden.
- Richten Sie Ihre Datei für mehrere Teile oder dünne Merkmale richtig aus. Beim Schneiden vieler Teile aus demselben Blech ist es häufig wünschenswert, zwischen ihnen einen Abstand von mindestens der Materialstärke zu lassen.
- Wählen Sie das richtige Material. Verschiedene Metalle weisen ein unterschiedliches Reflexionsvermögen und eine unterschiedliche Wärmeleitfähigkeit auf, was sich auf den Schneidvorgang auswirken kann.
- Ihre Details können nicht kleiner als die Metalldicke sein. Je größer die Dicke, desto weniger kann der Laser in das Material eindringen und es schneiden.
- Denken Sie an den Schnittpunkt. Mit Schnittfuge ist das Material gemeint, das verdampft, wenn der Laserstrahl auf das zu schneidende Material trifft.
Abschluss
Metall schneiden mit dem Laser ist eine äußerst effektive Technik zum Erzielen präziser und detaillierter Schnitte in Metallen und eignet sich daher für eine breite Palette von Materialien. Es ist jedoch wichtig zu beachten, dass der Kauf eines Laserschneiders eine erhebliche Anfangsinvestition erfordert, sodass das Outsourcing von Metallschneidediensten für viele eine praktische Wahl ist. Alternativen zum Laserschneiden von Blechen sind EDM, CNC-Fräsen, Stanzen, Wasserstrahl- und Plasmaschneiden – jede bietet einzigartige Vorteile basierend auf Ihren Fertigungsanforderungen.
Wenn Sie einen zuverlässigen Dienstleister für hochwertiges und präzises Metallschneiden suchen, ist KRRASS die Lösung. Wir sind Experten im Laserschneiden und stellen sicher, dass das Endprodukt genau Ihren Spezifikationen entspricht. Darüber hinaus bietet KRRASS eine Vielzahl von Prototyping-Diensten an, darunter CNC-Bearbeitung, 3D-Druck, Spritzguss und Urethanguss. Zögern Sie nicht – kontaktieren Sie uns noch heute!