Inhaltsverzeichnis
NC vs. CNC-Biegemaschine
NC und CNC-Biegemaschinen sind Maschinen, die in Biegeprozessen eingesetzt werden und von einem numerischen Steuerungssystem gesteuert werden. Numerische Steuerung (NC) bezeichnet die Fähigkeit dieser Maschinen, Biegevorgänge durch Computerprogramme oder vorgegebene Parameter ohne manuelles Eingreifen auszuführen. Im Gegensatz dazu verwendet die computergestützte numerische Steuerung (CNC) fortschrittliche Technologie, um Biegevorgänge zu steuern und auszuführen. Über CNC-Systeme können Bediener verschiedene Biegeparameter für das Werkstück eingeben, die die Steuerung dann anwendet, um eine präzise und effiziente Ausführung sich wiederholender Biegungen sicherzustellen.
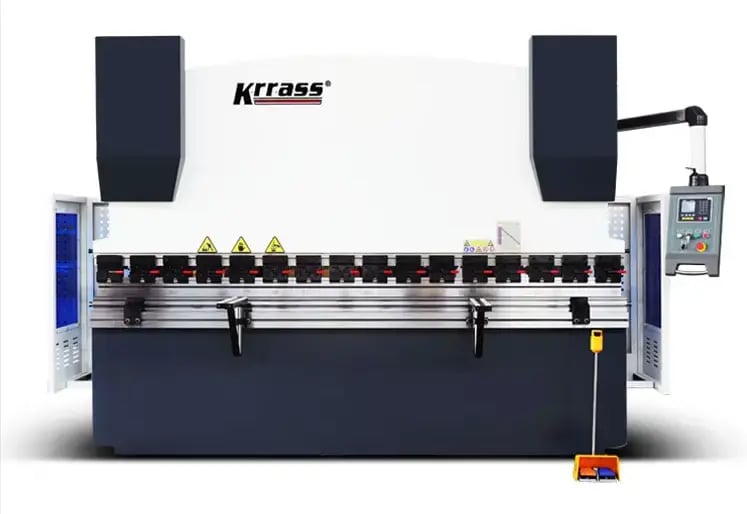
Im Vergleich zu herkömmlichen manuellen oder halbautomatischen Biegemaschinen bieten CNC-Abkantpressen ein höheres Maß an Automatisierung und Genauigkeit. Diese Maschinen können den gesamten Prozess selbstständig abschließen, ohne dass manuelle Eingriffe oder zusätzliche Geräte zum Zuführen von Blechen oder Drähten erforderlich sind, was letztendlich die Arbeitskosten senkt. Es ist erwähnenswert, dass NC-Abkantpressen in die Kategorie der CNC-Abkantpressen fallen.
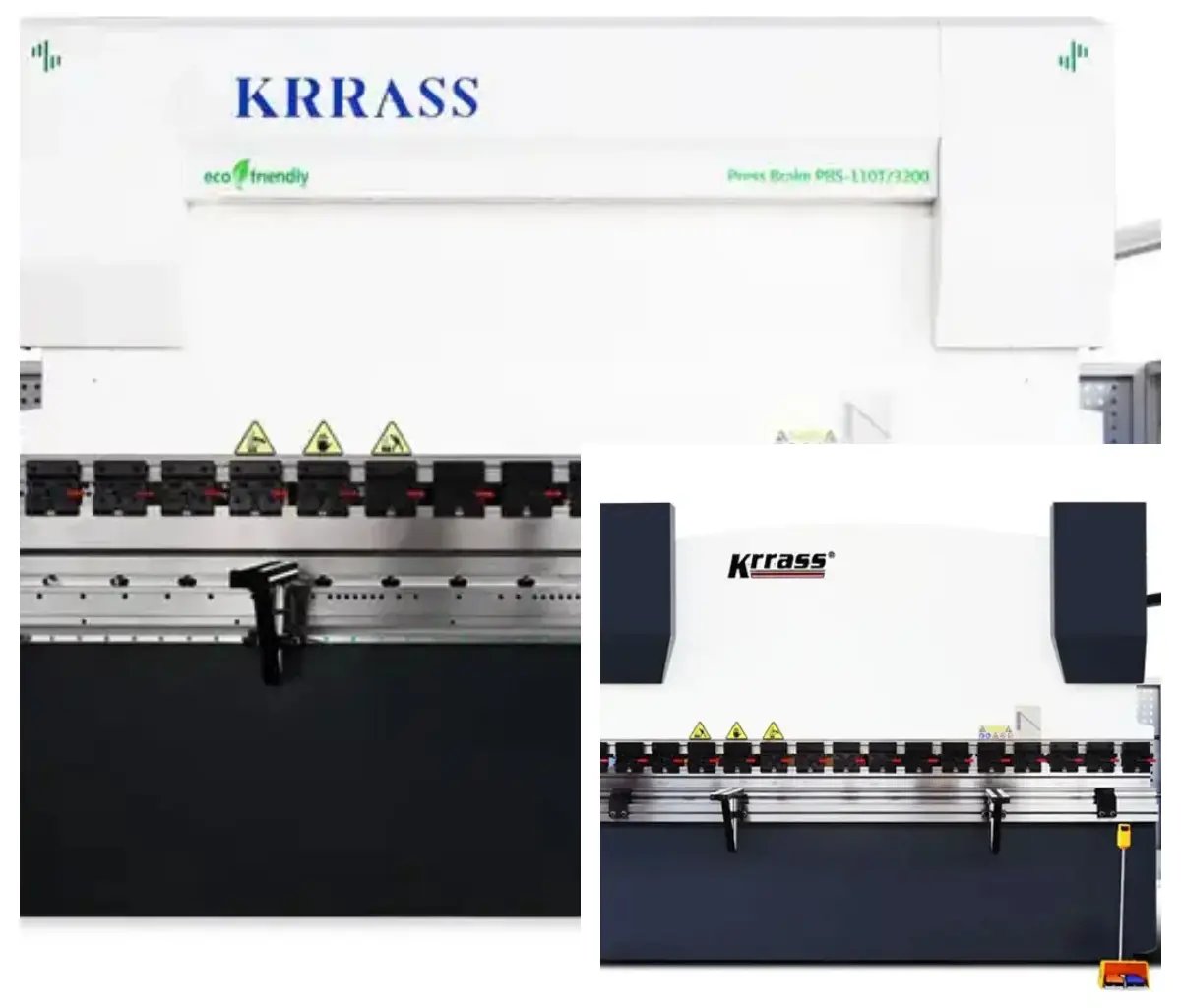
Um die Produktionseffizienz zu optimieren, Qualitätsstandards einzuhalten und die Kosten unter Kontrolle zu halten, müssen Unternehmen ihre Wahl der Biegemaschine sorgfältig abwägen.
Wie funktionieren NC- und CNC-Biegemaschinen?
NC-Abkantpressen verwenden eine mechanische Synchronisierungsmethode mit einer Y-Achse und einer X-Achse einer hinteren Messlehre für die Druckbewegung. Sie bestehen aus einem Arbeitstisch, einem Hydrauliksystem, Klemmen und einer hinteren Messlehre. NC-Abkantpressen verwenden eine mechanische Zwangssynchronisierungsmethode, und die Parallelität des Schlittens kann nicht selbst kalibriert und eingestellt werden. Der Hub des Schlittens kann manuell eingestellt werden, und eine Keilklemme gleicht eine höhere Biegepräzision aus. Bei CNC-Abkantpressen sind auf beiden Seiten der Maschine zwei Linearencoder installiert, und die CNC-Steuerung analysiert die Synchronisierung des Schlittens basierend auf dem Feedback dieser beiden Linearencoder. Wenn Fehler auftreten, nimmt die Steuerung Anpassungen über Proportionalventile vor, um die Schlittensynchronisierung aufrechtzuerhalten. Die CNC-Steuerung, das Hydrauliksystem und die Linearencoder bilden zusammen ein geschlossenes Regelsystem.
Wie verwendet man CNC-Biegemaschinen?
Zunächst ist es wichtig, sich auf die Aufgabe vorzubereiten. Dazu gehört das Tragen geeigneter persönlicher Schutzausrüstung und die Gewährleistung eines sauberen und organisierten Arbeitsbereichs. Bereiten Sie die erforderlichen Metallmaterialien, Werkzeuge und Werkstücke vor und klemmen Sie das Werkstück sicher auf den Arbeitstisch der Maschine, um Stabilität zu gewährleisten.
Wählen Sie als Nächstes die richtigen Schneidwerkzeuge und Biegematrizen aus und installieren Sie sie auf der CNC-Biegemaschine. Geben Sie anschließend die Parameter des Werkstücks über die CNC-Programmierung ein, einschließlich Biegewinkel, Positionen und Biegekräfte, damit die Maschine weiß, wie sie zu arbeiten hat. Starten Sie die CNC-Maschine, laden Sie das CNC-Programm und geben Sie die relevanten Parameter über die Steuerungsschnittstelle ein. Die Maschine führt dann die Biegevorgänge basierend auf dem G-Code oder den CAM-Anweisungen aus und Sie können den Betrieb der Maschine über die Steuerungsschnittstelle überwachen.
Überprüfen Sie während des Betriebs regelmäßig die Qualität der Werkstücke, indem Sie mithilfe von Messgeräten die Abmessungen und Winkel überprüfen, um sicherzustellen, dass sie den Konstruktionsanforderungen entsprechen. Passen Sie bei Bedarf die Werkzeuge an oder programmieren Sie die Maschine neu.
Wenn alle Werkstücke hergestellt sind, stoppen Sie den Betrieb der Maschine, entnehmen Sie die Werkstücke, reinigen und markieren Sie sie (falls erforderlich) und schalten Sie die CNC-Biegemaschine ab. Führen Sie die erforderlichen Wartungsarbeiten durch, um den ordnungsgemäßen Betrieb und die Langlebigkeit der Maschine sicherzustellen.
Wie programmiert man CNC-Biegemaschinen?
Bei der CNC-Biegeprogrammierung wird ein Entwurf in eine Reihe von Anweisungen übersetzt, die die Maschine verstehen und ausführen kann. Hier sind die Schritte:
Beginnen Sie mit der Erstellung oder dem Importieren des CAD-Designs des Werkstücks und stellen Sie sicher, dass es die erforderlichen Abmessungen, Biegewinkel und Positionsinformationen enthält.
Als nächstes konvertieren Sie dieses Design in maschinenlesbaren G-Code. G-Code enthält detaillierte Anweisungen für Maschinenbewegungen und Biegevorgänge. Dieser Schritt kann mithilfe spezieller CAM-Software automatisiert oder manuell durch Schreiben von G-Code durchgeführt werden.
Wählen Sie vor dem Programmieren die entsprechenden Materialien und Schneidwerkzeuge aus, da diese Biegeparameter und -kräfte beeinflussen. Geben Sie beim Programmieren Biegewinkel, Biegepositionen, Werkzeugpositionen und erforderliche Biegekräfte an.
Sobald der G-Code generiert ist, laden Sie ihn auf die Steuerung der CNC-Biegemaschine hoch. Dazu wird die G-Code-Datei normalerweise auf einem USB-Laufwerk gespeichert oder über ein Netzwerk hochgeladen.
Richten Sie das Werkstück und die Werkzeuge auf der CNC-Biegemaschine ein, bevor Sie das Programm ausführen. Stellen Sie sicher, dass das Werkstück sicher eingespannt und richtig auf dem Arbeitstisch der Maschine positioniert ist und dass die Werkzeuge ordnungsgemäß installiert sind.
Starten Sie die CNC-Biegemaschine, laden Sie das G-Code-Programm und folgen Sie den Anweisungen auf der Steuerungsoberfläche. Die Maschine führt Bewegungen und Vorgänge basierend auf Ihrer Programmierung aus.
Überwachen Sie den Biegevorgang, um sicherzustellen, dass alles reibungslos abläuft. Bei Bedarf können während des Vorgangs Anpassungen vorgenommen werden. Verwenden Sie die Steuerungsschnittstelle, um die Qualität und Abmessungen der Werkstücke zu überprüfen.
Wenn schließlich alle Werkstücke fertig sind, stoppen Sie die Maschine, entnehmen die Werkstücke, reinigen und markieren sie bei Bedarf und schalten die CNC-Biegemaschine ab.
Die CNC-Biegeprogrammierung erfordert Geschick und Erfahrung, um qualitativ hochwertige und präzise Biegevorgänge zu gewährleisten. Eine ordnungsgemäße Programmierung kann die Produktionseffizienz verbessern, Kosten senken und die Einhaltung der Konstruktionsanforderungen sicherstellen.
Vergleich numerischer Steuerungssysteme
Numerisches Steuerungssystem für Abkantpressen
NC-Bieger sind programmierbare Zweiachsenwerkzeuge, die Torsionsstäbe zur Synchronisierung verwenden. NC oder Numerische Steuerung beinhaltet die Verwendung eines numerischen Steuerungssystems zur Steuerung der Bewegungen der Maschine. NC-Abkantpressen verwenden normalerweise vorgefertigte numerische Programme zur Steuerung von Biegevorgängen. Diese Programme enthalten eine Reihe von Koordinaten und Bewegungsanweisungen, um die Form und die Biegewinkel des Werkstücks zu bestimmen. Die Bediener müssen diese numerischen Programme manuell eingeben, normalerweise über das Bedienfeld der Maschine oder einen externen Computer. NC-Abkantpressen sind im Allgemeinen günstiger als CNC-Abkantpressen, erfordern jedoch relativ höhere Bedienerkenntnisse. NC-Abkantpressensteuerungen können für komplexe Biegesequenzen programmiert werden, z. B. Delem 41, E21, Cyblec. Sie bieten dennoch eine genaue und kostengünstige Option.
CNC-Steuerungen ermöglichen 2D- und 3D-Simulationen, stellen sicher, dass komplexe Biegeformen gründlich berücksichtigt werden, und bieten optimierte Programmierlösungen, die die Produktionseffizienz und die Qualität der Werkstücke deutlich verbessern. CNC-Abkantpressen verwenden leistungsstarke Algorithmen im Steuerungssystem, um den Betriebszustand der Maschine zu analysieren, wodurch eine präzise Anpassung verschiedener Parameter möglich ist und Raum für Verbesserungen der Leistung der Abkantpresse bleibt. Kontinuierliche Innovationen in der Technologie numerischer Steuerungssysteme haben zu weit verbreiteten Anwendungen von CNC-Abkantpressen geführt, beispielsweise in Biegezellenzentren, die in Verbindung mit Robotern arbeiten können. Fortschrittliche CNC-Systeme bieten außerdem Sicherheitsfunktionen, Laserschutz, Lichtvorhänge, Winkelprüfungen, Laserprüfungen und Materialverfolgungsgeräte sowie mehrere Sprachoptionen und hochintelligente DXF-Dateieingaben. Diese Funktionen spielen bei praktischen Biegearbeiten eine entscheidende Rolle und unterstützen wirklich die Blechbiegevorgänge. Die CNC-Systeme von CNC-Abkantpressen ermöglichen mehrere Programmierungen und verfügen über Speicherfunktionen. Je größer die Speicherkapazität des Systems ist, desto mehr Programme kann die Maschine speichern. Wenn Hersteller verschiedene Spezifikationen oder komplexe Werkstücke biegen müssen, ist es besser, ein CNC-System zu wählen, um die Chargenproduktion effizient abzuschließen. NC-Systeme haben keine Speicherfunktion.
Vergleich von Biegegenauigkeit und Geschwindigkeit
Biegegenauigkeit
Die Parallelität des Schlittens beeinflusst die Präzision des Werkstücks. NC-Abkantpressen verwenden eine mechanische Synchronisation, die durch einen Torsionsstab aufrechterhalten wird, und verfügen weder über eine Echtzeit-Fehlerrückmeldung noch können sie sich selbst einstellen, was zu einer geringeren Biegegenauigkeit führt. Bei CNC-Biegern hält die Steuerung die Schlittensynchronisation durch Proportionalventile aufrecht, die auf der Rückmeldung von Linearencodern basieren, die die Synchronisation auf beiden Seiten des Schlittens analysieren. Wenn ein Fehler auftritt, geben die Linearencoder eine Rückmeldung an die Steuerung, die dann Signale zur Anpassung an Proportionalventile sendet und so die Biegegenauigkeit verbessert.
Arbeitsgeschwindigkeit
Im Vergleich zu NC-Abkantpressen ist die Schlittenöffnungshöhe von NC-Abkantpressen fest und muss bei jedem Öffnen vom höchsten Punkt zum niedrigsten Punkt bewegt werden, was zu Effizienzproblemen führen kann. Die Absenkgeschwindigkeit des Schlittens bei NC-Abkantpressen beträgt ungefähr 80 mm/s und die Bewegungsgeschwindigkeit des hinteren Anschlags beträgt etwa 100 mm/s. Im Gegensatz dazu bieten CNC-Abkantpressen mehr Flexibilität. Die CNC-Steuerung ermöglicht eine präzise Steuerung der Schlittenöffnungshöhe mithilfe einer digitalen Steuerung, sodass nicht jedes Mal zum höchsten Punkt zurückgekehrt werden muss und Zeit gespart wird, was die Verarbeitungseffizienz verbessert. Die Schlittenabsenkgeschwindigkeit kann bei CNC-Abkantpressen bis zu 200 mm/s erreichen, mit gleichmäßiger Bewegung selbst an variablen Punkten. Die Geschwindigkeit des hinteren Anschlags kann 400 mm/s erreichen. Darüber hinaus verwenden NC-Abkantpressen in Bezug auf Hydraulikzylinder normalerweise Zylinder mit einem Verhältnis von 6:1 oder 8:1, während CNC-Abkantpressen Zylinder mit einem Verhältnis von 13:1 oder 15:1 verwenden. Infolgedessen haben CNC-Abkantpressen im Vergleich zu NC-Abkantpressen viel schnellere Leerlauf- und Rücklaufgeschwindigkeiten.
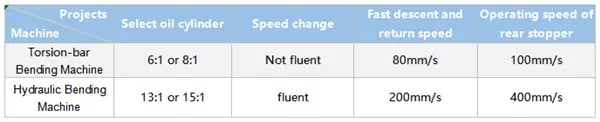
Vergleich der Biegewinkelkalibrierung
Biegewinkelkalibrierung in NC-Abkantpressen
NC-Abkantpressen verwenden relativ einfache numerische Steuerungssysteme (NC), denen häufig Echtzeitüberwachung und automatische Kalibrierungsfunktionen fehlen. Die Winkelkalibrierung erfordert in der Regel mehr manuelle Eingriffe und Geschick des Bedieners. Bediener müssen möglicherweise Winkelmessgeräte wie Winkelmesser oder Winkelmesser verwenden, um den Winkel des Werkstücks manuell zu messen und manuelle Anpassungen vorzunehmen. Die Genauigkeit dieses manuellen Kalibrierungsprozesses kann geringer sein und kann durch die Erfahrung und das Geschick des Bedieners beeinflusst werden.
Biegewinkelkalibrierung in CNC-Abkantpressen
CNC-Abkantpressen sind mit fortschrittlichen CNC-Systemen (Computer Numerical Control) ausgestattet, die Winkel während des Biegevorgangs in Echtzeit überwachen und anpassen können. CNC-Abkantpressen verfügen normalerweise über Winkelsensoren und Rückmeldesysteme, die den tatsächlichen Biegewinkel des Werkstücks messen und mit dem voreingestellten Winkel vergleichen. Wenn der tatsächliche Winkel nicht mit dem voreingestellten Winkel übereinstimmt, kann das CNC-System automatisch kleinere Anpassungen vornehmen, um sicherzustellen, dass das Werkstück den gewünschten Winkel erreicht. Dieser Automatisierungsprozess bietet häufig eine höhere Winkelkalibrierungsgenauigkeit und reduziert die Notwendigkeit eines Bedienereingriffs.
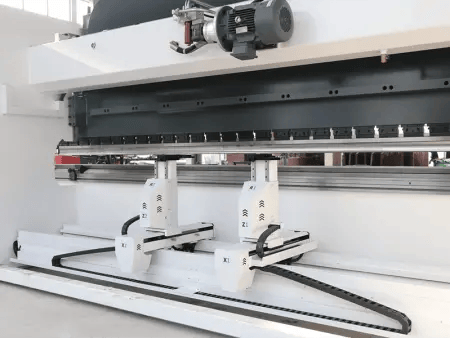
Funktionen der NC-Abkantpresse
- Traditionelle Struktur mit Torsionsstäben zur Y-Achsen-Synchronisierung
- Standard-X- und Y-Achsen
- ESTUN E21 NC-Steuergerät
- Motorisierter Hinteranschlag
- Oberstempelkompensation
- FIRST Valves (USA)
- Durchgehende Multi-V-Matrize, Oberstempel mit Segmentierung 835 mm
- NOK Dichtungsring
- Seitlicher und hinterer Sicherheitsschutz
- Mechanisches Bombierungssystem manuell bedient
- Schaltschrank mit Komponenten von Telemecanique Schneider, Esautomotion und ABB
Merkmale der CNC-Abkantpresse:
- ESA CNC-Steuereinheit S630 (OptionalDELEM DA53T, 58T, 66T, 69T, 66S, ESA 630, 640, 860)
- 4+1 oder mehr Achsen CNC-Steuerung
- Präzise Ram-Positionierung Y1 und Y2
- Standard-X- und R-Achsen
- CNC dynamische Bombierung
- Große Öffnungshöhe, Hub und Halstiefe
- NOK Dichtring
- Elektrische Komponenten von Schneider und ABB
- Siemens-Motor
- Seitlicher und hinterer Sicherheitsschutz
- Frontstützen aus Blech
- SUNNY Pumpe
- Kugelumlaufspindel und Linearführung
- Hinterer Anschlagfinger mit 3 Blöcken und doppelter Linearführung
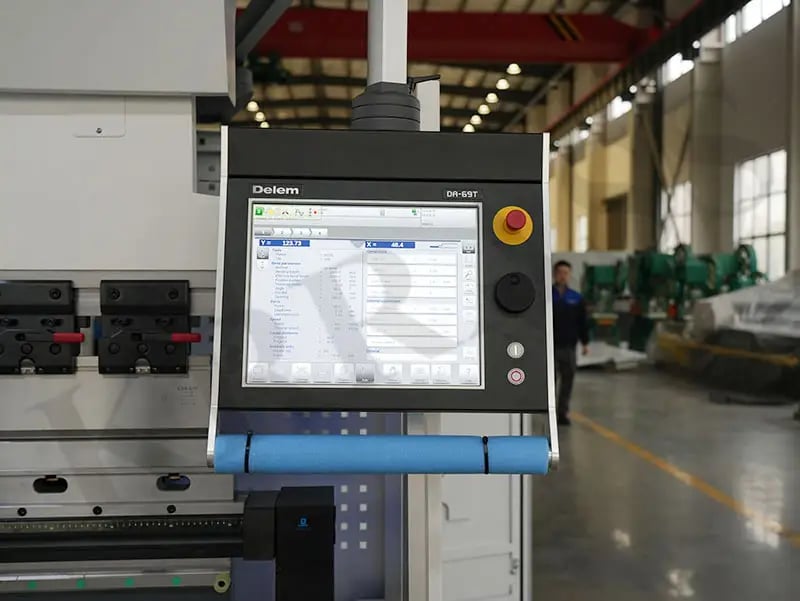
Praktische Bedienung
NC-Abkantpressen verfügen nicht über ein numerisches Steuerungssystem und eine V-Achsen-Kompensation. Beim Biegen neuer Werkstücke können erfahrene Bediener nur auf Probebiegen zurückgreifen, was Materialverschwendung sein kann und für erfahrene Bediener höhere Löhne erfordern kann. CNC-Abkantpressen, die mit CNC-Steuerungssystemen und V-Achsen-Kompensation ausgestattet sind, bieten eine einfachere Bedienung, die weniger Erfahrung des Bedieners erfordert. CNC-Steuerungen verfügen über analoge Biegefunktionen, wodurch Probebiegen überflüssig wird und direktes Biegen möglich ist.
Preis und Kosten
Tatsächlich können CNC-Abkantpressen bei einer Maschinenkapazität von weniger als 200 Tonnen mehr als doppelt so teuer sein wie NC-Abkantpressen. Wenn die Biegemaschinenkapazität jedoch 200 Tonnen übersteigt, können CNC-Abkantpressen bis zur Hälfte günstiger sein als NC-Abkantpressen. Wenn die Abkantpresse also eine höhere Produktionskapazität hat, ist die Entscheidung für eine CNC-Abkantpresse oft die bessere Wahl. Insgesamt sind CNC-Abkantpressen aufgrund ihrer fortschrittlichen Steuerungssysteme, höheren Automatisierungsgrade und verbesserten Leistung in der Regel teurer als NC-Abkantpressen. Der genaue Preisunterschied hängt vom Modell, den Spezifikationen und Funktionen der Maschine sowie vom Marktwettbewerb und den Angebots- und Nachfragebedingungen ab. Beim Kauf einer Abkantpresse ist es wichtig, Preis und Leistung entsprechend Ihrem Budget und Ihren Produktionsanforderungen abzuwägen.
Anwendungen von Abkantpressen
Anwendungen von NC-Abkantpressen
Kleinserienfertigung: NC-Abkantpressen eignen sich typischerweise für die Fertigung relativ kleiner Stückzahlen, etwa für spezielle Sonderanfertigungen oder Kleinprojekte.
Geringere Präzisionsanforderungen: NC-Abkantpressen sind eine kostengünstige Wahl für Anwendungen, bei denen keine hohe Präzision erforderlich ist.
Einfache Teile: Sie werden häufig zur Herstellung einfacher Metallteile wie flacher Platten, gerader Winkel und einfacher Biegungen verwendet.
Manuelle Programmierung: Bediener müssen Koordinaten und Programme manuell eingeben, weshalb sie für Benutzer mit etwas Erfahrung in der numerischen Steuerungsprogrammierung geeignet sind.
Kosteneffizienz: NC-Abkantpressen sind im Allgemeinen kostengünstiger und eignen sich für Situationen mit Budgetbeschränkungen.
Anwendungen von CNC-Abkantpressen
Großserienproduktion: CNC-Abkantpressen eignen sich für die Produktion im großen Maßstab, da sie die Produktionseffizienz und -konsistenz verbessern können.
Hohe Präzisionsanforderungen: Für Branchen, die hohe Präzision und Genauigkeit bei der Teilefertigung erfordern, wie etwa die Luft- und Raumfahrt, der Schiffbau, die Automobilindustrie und die Elektronik, sind CNC-Abkantpressen die bevorzugte Wahl.
Komplexe Teile: CNC-Abkantpressen können komplexe Teilebiegevorgänge bewältigen, darunter auch Teile mit mehreren Biegewinkeln und Kurven.
Automatisierung: Sie bieten typischerweise einen höheren Automatisierungsgrad und können Biegeaufgaben automatisch ausführen, wodurch die Notwendigkeit eines Eingriffs durch den Bediener reduziert wird.
Höhere Kosten: CNC-Abkantpressen sind aufgrund ihrer fortschrittlichen Steuerungssysteme und Funktionen im Allgemeinen teurer. Sie eignen sich normalerweise für Anwendungen mit hohen Produktionsanforderungen und Präzisionsanforderungen.
Natürlich kann jede Fabrik, die eine Biegemaschine benötigt, eine CNC-Abkantpresse wählen, da diese für verschiedene Arten von Blechbiegeprozessen geeignet ist.
Dekorative Industrie: Schränke, Regale, Aufzüge, Türen, Fenster, Vorhangwände usw.
Bauindustrie: Stahlkonstruktionen, Türme, Brücken usw.
Maschinenbau: Umweltschutzausrüstung, Viehzuchtausrüstung, Solarausrüstung, Isoliermaterialien, Transformatoren usw.
Elektro- und Energieindustrie: Strommasten, Laternenpfähle, elektrische Geräte, elektronische Geräte usw.
Abschluss
CNC-Abkantpressen bieten hohe Präzision, Fehlerrückmeldung in Echtzeit und eine robuste Widerstandsfähigkeit gegen außermittige Belastungen in Biegeschlitten. NC-Abkantpressen hingegen bieten eine geringere Präzision, keine Fehlerrückmeldung und eine schwächere Widerstandsfähigkeit gegen außermittige Belastungen in Biegeschlitten. Darüber hinaus sind CNC-Abkantpressen im Vergleich zu NC-Abkantpressen komplexer und teurer. Zusammenfassend lässt sich sagen, dass die Wahl einer Abkantpresse von den spezifischen Bearbeitungsanforderungen abhängt. Wenn Sie weitere Fragen dazu haben, ob Sie eine NC- oder CNC-Abkantpresse wählen sollen, wenden Sie sich bitte an KRRASS.
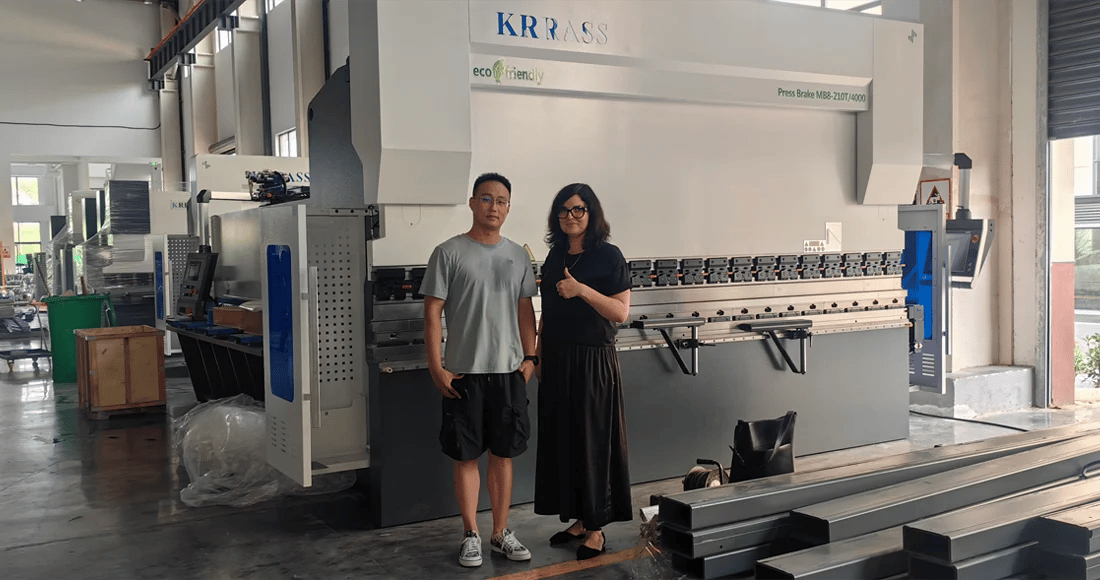