Im komplexen Tanz der Metallverarbeitung, wo Präzision auf Produktivität trifft, erweist sich die Abkantpresse als zuverlässiger Leistungsträger. Da die Hersteller bestrebt sind, den ständig steigenden Anforderungen an Qualität und Effizienz gerecht zu werden, ist es von größter Bedeutung, die wesentlichen Optionen für diese Maschinen zu verstehen. In diesem umfassenden Leitfaden gehen wir auf die unverzichtbaren Optionen ein, die eine Abkantpresse von einem bloßen Werkzeug zu einem Kraftwerk der Feinmechanik. Egal, ob Sie ein erfahrener Bediener oder ein Neuling in der Welt der Metallbearbeitung sind, dieser Leitfaden beleuchtet die entscheidenden Optionen, die zur Maximierung des Potenzials Ihrer Abkantpresse.
Inhaltsverzeichnis
Abkantpresse: 5 unverzichtbare Optionen
1. CNC-Steuerungen: So werden Bediener zu Experten
Die Einführung der CNC-Technologie (Computer Numerically Controlled) hat den Betrieb von Abkantpressen revolutioniert. CNC-Steuerungen automatisieren den Biegeprozess und ermöglichen präzise Anpassungen und Wiederholgenauigkeiten, die mit manuellen Systemen undenkbar waren. Diese Automatisierung macht jeden Bediener zum Experten, indem sie ihm intuitive Schnittstellen und vorprogrammierte Verfahren für verschiedene Biegeaufgaben bietet. Die Präzision von CNC-Steuerungen liegt in ihrer Fähigkeit, komplexe Biegesequenzen zu verwalten, Parameter in Echtzeit anzupassen und Daten für die zukünftige Verwendung zu speichern, wodurch der gesamte Prozess effizienter wird und weniger von den Fähigkeiten des Bedieners abhängt. Einfach ausgedrückt machen CNC-Steuerungen die Bedienung einer Abkantpresse einfacher und präziser.
2. Y1- und Y2-Achsenfunktionen: Beherrschung der Ram-Neigung für höchste Präzision
Die Achsen Y1 und Y2 repräsentieren die linke und rechte Seite des Pressenstößels. Die unabhängige Steuerung dieser Achsen ermöglicht die Anpassung der Stößelneigung, ein entscheidender Faktor für die Herstellung perfekt präziser Teile. Diese Funktion stellt sicher, dass der Biegewinkel über die gesamte Länge der Abkantpresse hinweg konstant ist und jede mögliche Durchbiegung unter Last ausgeglichen wird. Diese Kontrollmöglichkeit ermöglicht es Herstellern, Teile mit beispielloser Präzision herzustellen und dabei die strengsten Toleranzanforderungen zu erfüllen, ohne dass manuelle Nacharbeit erforderlich ist. Außerdem können bei Bedarf leichte Verjüngungen in die Biegungen eingefügt werden.
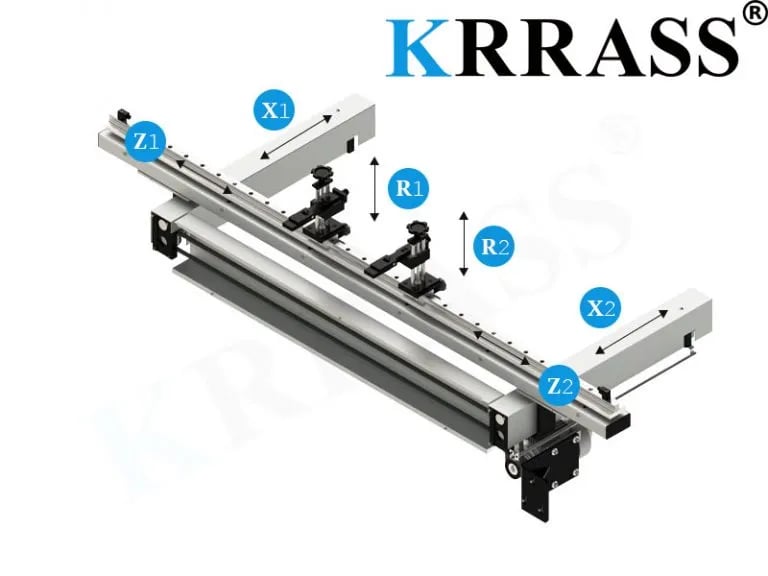
3. X- und R-Achsen-Rückmesstechnik: Messen und Unterstützen für eine einwandfreie Ausführung
Ein Hinteranschlag ist unerlässlich, um ein Werkstück vor Beginn des Biegevorgangs genau zu positionieren. Die X-Achse steuert die Vorwärts- und Rückwärtsbewegung des Hinteranschlags und sorgt so für den richtigen Abstand zum Werkzeug, während die R-Achse die Höhe anpasst und das Teil während der Biegung effektiv misst und stützt. Diese Kombination garantiert nicht nur eine präzise Positionierung für jede Biegung, sondern reduziert auch die Bearbeitungszeit und steigert so die Gesamtproduktivität. Durch die genaue Messung des Flansches und die Unterstützung des Teils während des gesamten Prozesses trägt die Hintermessung der X- und R-Achse erheblich zur Effizienz und Qualität des Ergebnisses bei.
4. Krönungsvorrichtung: Gewährleistung gleichmäßiger Biegungen über die gesamte Länge
Eine der Herausforderungen beim Betrieb einer Abkantpresse ist die Kompensation der Maschinendurchbiegung, die zu Inkonsistenzen im Biegewinkel führen kann, insbesondere bei langen Biegungen. Die Bombierungsvorrichtung ist die Lösung für dieses Problem, da sie das manuelle Unterlegen der Matrizen überflüssig macht. Sie passt das Bett der Abkantpresse automatisch an, um der Durchbiegung entgegenzuwirken und eine gleichmäßige Biegung über die gesamte Länge der Presse sicherzustellen. Dies verbessert nicht nur die Genauigkeit jedes Teils, sondern reduziert auch die Rüstzeit erheblich, da die Bediener Maschinenfehler nicht mehr manuell ausgleichen müssen. Als Bonus sind diese auch als CNC-Achse der Abkantpresse erhältlich, die eine in Echtzeit programmierbare Anpassung zwischen den Biegungen ermöglicht.
5. Funktionen der Z1- und Z2-Hinteranschlagachsen: Produktivitätssteigerung bei komplexen Teilen
Die Achsen Z1 und Z2 verleihen Abkantpressen eine weitere Ebene der Vielseitigkeit. Diese Achsen steuern die Bewegung der Messfinger links und rechts entlang des Hinteranschlagarms. Diese Fähigkeit ist besonders nützlich beim Formen langer Teile oder komplexer kleinerer Teile, die mehrere Messpunkte erfordern. Durch die schnelle und präzise Positionierung der Hinteranschlagfinger ermöglichen die Achsen Z1 und Z2 die effiziente Ausführung komplexer Biegefolgen, ohne dass das Teil manuell neu positioniert werden muss. Dies führt zu einer deutlichen Produktivitätssteigerung, insbesondere bei Aufträgen mit komplizierten Teilen oder hohen Produktionsmengen.
Fazit: Die Metallverarbeitung auf ein neues Niveau heben
Die Integration dieser fünf wesentlichen Abkantpressenoptionen – CNC-Steuerung, Y1- und Y2-Achsenfunktionen, X- und R-Achsen-Hinteranschlag, Bombierungsvorrichtungen und Z1- und Z2-Hinteranschlagachsenfunktionen – stellt einen bedeutenden Fortschritt in der Metallverarbeitungstechnologie dar. Durch verbesserte Präzision, kürzere Rüstzeiten und höhere Gesamteffizienz ermöglichen diese Optionen es Herstellern, die steigenden Anforderungen an Qualität und Komplexität von Metallteilen zu erfüllen. Egal, ob Sie lange Teile oder komplexe kleinere Teile formen, die mehrere Messpunkte erfordern, diese Funktionen stellen sicher, dass Ihre Abkantpresse die Aufgabe mit unübertroffener Genauigkeit und Produktivität bewältigen kann.
Entdecken Sie die wichtigsten Abkantpressenoptionen bei KRRASS
Auf der Suche nach fortschrittlichen Möglichkeiten in der Metallverarbeitung ist die Wahl der richtigen Abkantpresse von größter Bedeutung. Krrass ist ein Leuchtturm für Hersteller, die nach Maschinen mit modernsten Funktionen suchen. Mit einer vielfältigen Auswahl an Abkantpressen mit wichtigen Optionen bietet Krrass maßgeschneiderte Lösungen für die Anforderungen der modernen Metallverarbeitung. Entdecken Sie, wie unser Fachwissen und unser umfangreicher Lagerbestand Ihre Fertigungsprozesse verbessern, den Bedienern mehr Möglichkeiten geben und Präzision bei jedem Teil gewährleisten können.