Was ist eine Plattenwalzmaschine?
Eine Blechbiegemaschine, auch Blechwalze oder Walzmaschine genannt, ist ein mechanisches Gerät, das in der Metallverarbeitung verwendet wird, um flache Bleche oder Metallplatten in gebogene oder zylindrische Formen zu biegen. Diese Maschinen werden häufig in Branchen wie Fertigung, Bauwesen, Schiffbau und Metallverarbeitung eingesetzt.
Die Hauptfunktion einer Blechwalzmaschine besteht darin, Kraft auf eine flache Metallplatte oder ein Blech auszuüben, sodass es sich um eine Mittelachse biegt. Bei diesem Verfahren wird das Metall zwischen einer Reihe von Walzen hindurchgeführt, die Druck auf das Material ausüben und es nach und nach in die gewünschte Form bringen. Blechwalzmaschinen können je nach Konfiguration der Walzen und den Spezifikationen der Maschine eine Vielzahl von Formen erzeugen, darunter Zylinder, Kegel und Bögen.
Blechwalzmaschinen gibt es in verschiedenen Typen und Größen, um verschiedenen Anwendungen und Materialstärken gerecht zu werden. Einige Maschinen werden manuell bedient, d. h. der Bediener muss die Walzen einstellen und das Material von Hand zuführen, während andere voll- oder halbautomatisch sind und über hydraulische oder elektrische Steuerungen für präzises Biegen und Formen verfügen.
Diese Maschinen sind in Branchen unverzichtbar, in denen gebogene oder zylindrische Metallkomponenten benötigt werden, beispielsweise bei der Herstellung von Tanks, Rohren, Druckbehältern und Strukturkomponenten. Blechwalzmaschinen ermöglichen es Herstellern, komplexe Formen mit hoher Genauigkeit und Effizienz herzustellen, was sie zu unverzichtbaren Werkzeugen in der modernen Metallverarbeitung macht.
Walzenbrüche können jedoch den Betrieb stören und zu kostspieligen Ausfallzeiten führen. Um die Effizienz und Produktivität der Maschine aufrechtzuerhalten, ist es wichtig, die Ursachen, Präventivmaßnahmen und Lösungen zu verstehen.
Einführung:
Blechwalzmaschinen sind in vielen Branchen unverzichtbare Geräte, die die Formung von Metallen in die gewünschte Form ermöglichen. Walzenbrüche können jedoch den Betrieb stören und zu kostspieligen Ausfallzeiten führen. Das Verständnis der Ursachen, vorbeugenden Maßnahmen und Lösungen ist für die Aufrechterhaltung der Maschineneffizienz und -produktivität von entscheidender Bedeutung.
Ursachen für Rollenbrüche:
Materialqualität: Bei der Herstellung von Rollen können minderwertige Materialien zu vorzeitigen Brüchen führen. Hochwertige Rollen aus langlebigen Materialien wie gehärtetem Stahl sind weniger bruchanfällig.
Überlastung: Übermäßiger Druck oder eine Belastung der Rollen über ihre Kapazität hinaus kann zu Spannungen und schließlich zu Brüchen führen. Die Einhaltung der empfohlenen Belastungsgrenzen ist entscheidend, um durch Überlastung bedingte Brüche zu vermeiden.
Ermüdung: Dauerhafter Gebrauch kann die Rollen über einen längeren Zeitraum schwächen und zu Ermüdungsbrüchen führen. Regelmäßige Wartung und Inspektion helfen dabei, Ermüdungsprobleme zu erkennen, bevor sie eskalieren.
Fehlausrichtung: Eine falsche Ausrichtung der Rollen kann zu einer ungleichmäßigen Spannungsverteilung und damit zu Brüchen führen. Um dieses Problem zu vermeiden, sind regelmäßige Überprüfungen und Anpassungen der Ausrichtung erforderlich.
Korrosion: Der Kontakt mit korrosiven Elementen kann das Walzenmaterial beschädigen und das Risiko von Brüchen erhöhen. Korrekte Lagerung und Schutzmaßnahmen wie Beschichtungen oder Schmiermittel können korrosionsbedingte Schäden mindern.
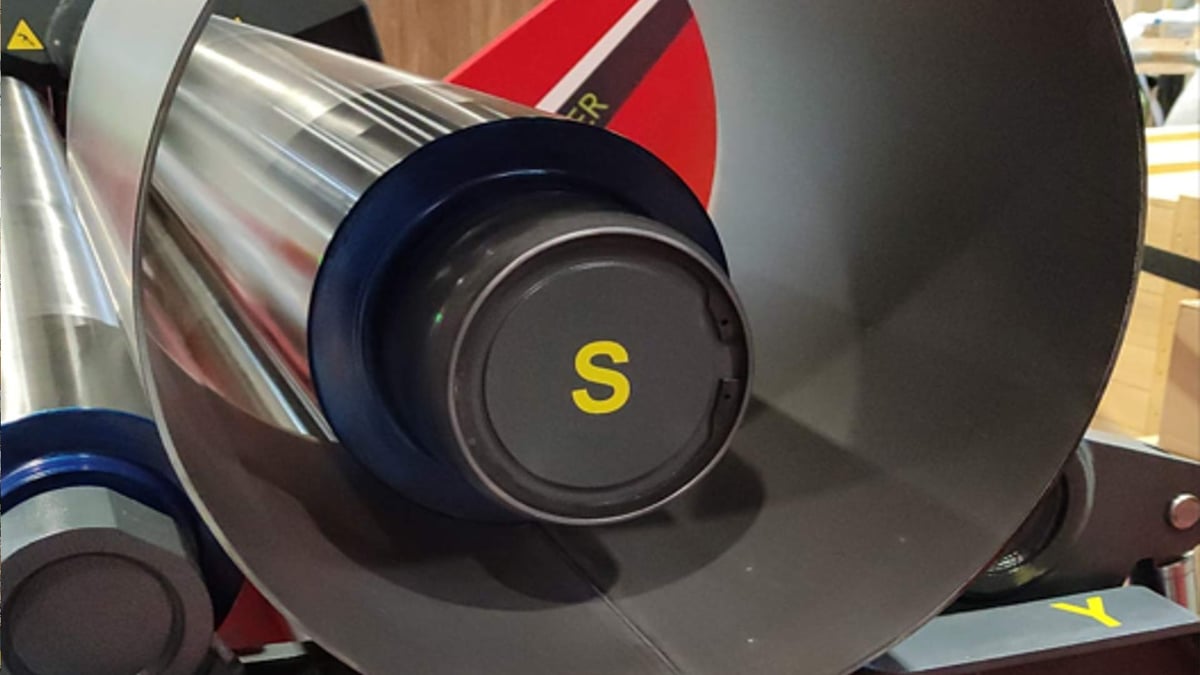
Vorbeugende Maßnahmen:
Qualitätsprüfung: Wählen Sie Rollen aus hochwertigen Materialien und führen Sie vor der Installation gründliche Überprüfungen durch, um deren Integrität sicherzustellen.
Lastmanagement: Halten Sie die empfohlenen Tragfähigkeiten ein und vermeiden Sie eine Überlastung der Maschine, um Spannungsbrüche vorzubeugen.
Regelmäßige Wartung: Führen Sie eine planmäßige Wartungsroutine durch, die Schmierung, Ausrichtungsprüfungen und Sichtprüfungen umfasst, um potenzielle Probleme frühzeitig zu erkennen.
Ausrichtungsprüfungen: Überprüfen und korrigieren Sie die Ausrichtung der Rollen regelmäßig, um eine gleichmäßige Spannungsverteilung zu gewährleisten und das Risiko von Brüchen zu minimieren.
Korrosionsschutz: Ergreifen Sie Maßnahmen zum Schutz der Walzen vor Korrosion, z. B. durch Aufbringen von Beschichtungen oder Verwendung korrosionsbeständiger Materialien.
Lösungen bei Rollenbrüchen:
Ersatz: Bei schwerwiegenden Brüchen oder Beschädigungen ist der Austausch der betroffenen Walzen durch hochwertige Ersatzteile erforderlich, um die Maschinenfunktionalität wiederherzustellen.
Reparieren: Kleinere Brüche können möglicherweise durch Schweißen oder maschinelle Bearbeitung repariert werden. Stellen Sie jedoch sicher, dass die Reparaturen den Sicherheits- und Qualitätsstandards entsprechen, um weitere Probleme zu vermeiden.
Verbesserungen: Erwägen Sie eine Aufrüstung auf stärkere oder haltbarere Walzenmaterialien, um das Risiko künftiger Brüche zu verringern und die Lebensdauer der Maschine zu verlängern.
Ausbildung: Bieten Sie den Bedienern eine angemessene Schulung im Umgang mit der Maschine, in der Wartung und in den Sicherheitsprotokollen an, um Missbrauch oder falsche Handhabung zu verhindern, die zu Knochenbrüchen führen könnten.
Abschluss:
Blechbiegemaschine Rollenbrüche können den Betrieb stören und erhebliche Kosten verursachen, wenn sie nicht umgehend behoben werden. Durch das Verständnis der Ursachen, die Umsetzung vorbeugender Maßnahmen und den Einsatz geeigneter Lösungen können Unternehmen Ausfallzeiten minimieren, die Produktivität steigern und die Lebensdauer ihrer Geräte verlängern. Die Priorisierung von Qualitäts-, Wartungs- und Sicherheitsprotokollen ist der Schlüssel zur Minderung des Risikos von Rollenbrüchen und zur Gewährleistung eines reibungslosen Betriebs in industriellen Umgebungen.