Wofür wird eine Plattenschere verwendet?
Blech und Blechscheren werden in vielen Fertigungs- und Blechbearbeitungsvorgängen eingesetzt. Vor der Auswahl einer Schermaschine müssen verschiedene Faktoren bewertet werden, darunter der Scherentyp, die erforderliche Kapazität, Möglichkeiten zur Produktivitätssteigerung und die Sicherheit.
Der Scherentyp wird durch viele Faktoren bestimmt, unter anderem durch die Länge des Materials, das verarbeitet werden kann, sowie durch die Dicke und Art des Materials, das geschnitten werden kann.
Schermaschinen lassen sich nach ihrer Konstruktion und den verwendeten Antriebssystemen in verschiedene Typen unterteilen. Bei Kraftscheren sind zwei Konstruktionsarten üblich: die Guillotine (auch Schieberschere genannt) und die Schwenkbalkenschere.
Schervorgang einer herkömmlichen Blechschermaschine
Schubbemessung
Die Guillotine-Konstruktion (siehe Abbildung 1) nutzt ein Antriebssystem, um das bewegliche Messer während des gesamten Hubs nach unten zu drücken und in eine nahezu parallele Position zum festen Messer zu bringen. Guillotine-Maschinen benötigen ein Führungssystem, um die Messerbalken beim Vorbeilaufen in der richtigen Position zu halten.
Bei der Schwenkbalkenkonstruktion (siehe Abbildung 2) wird das bewegliche Blatt mithilfe eines Antriebssystems auf Rollenlagern nach unten geschwenkt. Dadurch entfallen Keile oder andere Vorrichtungen, um die Blätter beim Vorbeilaufen in der richtigen Position zu halten.
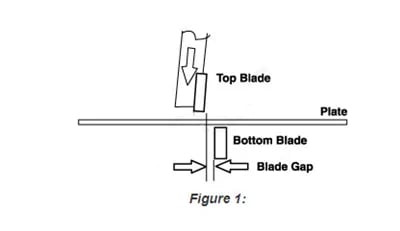
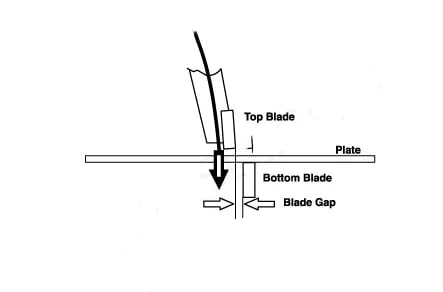
Scherenantriebssysteme
Das Antriebssystem treibt die Klinge durch das Material und führt so einen Schnitt aus. Antriebssysteme lassen sich in fünf Grundtypen unterteilen: Fuß- oder manuelle Antriebssysteme, pneumatische Antriebssysteme, mechanische Antriebssysteme, hydromechanische Antriebssysteme und hydraulische Antriebssysteme.
Fußschere
Eine Fußschere wird aktiviert, indem der Bediener auf ein Pedal tritt, um den Sägebalken nach unten zu bewegen und einen Schnitt auszuführen. Fußscheren werden häufig bei Blechbearbeitungen mit einer Kapazität von bis zu ca. 16 Gauge und Längen von bis zu 2,44 m eingesetzt, wobei Maschinen mit einer Kapazität von 2,44 m nicht so häufig sind wie solche mit kürzerer Kapazität.
Luftschere
Um eine Druckluftschere zu verwenden, tritt der Bediener auf ein Pedal, das die Druckluftzylinder aktiviert und einen Schnitt ausführt. Zum Antrieb einer Druckluftschere wird Werkstattluft oder ein freistehender Luftkompressor verwendet.
Druckluftscheren werden in Werkstätten zum Schneiden von Materialien bis zu einer Stärke von ca. 14 Gauge und einer Länge von bis zu 12 Fuß eingesetzt. Druckluftscheren verfügen über einen einfachen Antrieb und bieten einen Überlastschutz. Der Überlastschutz ist für einen ordnungsgemäßen Betrieb und in der Regel für senkrecht nach unten gerichtete Lasten ausgelegt. Selbst beim Schneiden einer Materialstärke, die innerhalb der Maschinenkapazität liegt, kann die Maschine beschädigt werden, wenn das Material ohne Niederhalter geschnitten wird oder der Klingenspalt nicht richtig eingestellt ist. Dies gilt auch für hydraulische Maschinen.
Mechanische Schere mit Direktantrieb
Diese Schere funktioniert, indem der Bediener ein Pedal betätigt, um den Motor einzuschalten, der den Balken zum Schneiden nach unten fährt. Am Ende des Zyklus schaltet sich der Motor ab, und der Sägebalken kehrt zum oberen Ende des Hubs zurück. Diese Konstruktion eignet sich für Scheren, die nicht ständig im Einsatz sind, da die Maschine nur bei Aktivierung Strom verbraucht.
Bewertung von Scheren
Ein wichtiger Aspekt bei der Bewertung von Scheren ist die für bestimmte Aufgaben erforderliche Kapazität. Die Maschinenspezifikationen fast aller Scheren geben die Kapazität für Baustahl und Edelstahl an. Um die Anforderungen des Herstellers mit denen der Maschine zu vergleichen, müssen die Materialspezifikationen des Herstellers mit der Kapazität der Maschine verglichen werden.
Einige Scherkapazitäten beziehen sich auf Baustahl mit einer Zugfestigkeit von 60.000 Pfund pro Quadratzoll (PSI), während andere auf A-36-Stahl mit einer Zugfestigkeit von 80.000 PSI ausgelegt sind. Die Kapazitäten für Edelstahl sind fast immer geringer als die für Baustahl oder A-36-Stahl. Manche Metallverarbeiter mögen überrascht sein, dass bestimmte Aluminiumsorten zum Scheren genauso viel Kraft benötigen wie zum Schneiden von Stahl. Bei Bedenken hinsichtlich der Kapazität ist es ratsam, sich immer an den Hersteller der Schere zu wenden.
Der Spanwinkel des Sägeblatts (der Winkel des beweglichen Sägeblatts beim Vorbeilaufen am festen Sägeblatt) ist entscheidend für die Schnittqualität. Generell gilt: Je niedriger der Spanwinkel, desto besser die Schnittqualität. Probleme mit der Schnittqualität, wie z. B. Krümmung, Verdrehung und Wölbung (siehe Abbildung 3), treten bei kürzeren Werkstücken (bis zu 10 cm Länge) auf, die nach dem Schneiden hinter die Schere fallen. Maschinen mit niedrigeren Spanwinkeln benötigen mehr Leistung als solche mit höherer Schnittgeschwindigkeit.
Einige Guillotine-Maschinen verfügen über einen variablen Spanwinkel, der an die Länge des zu schneidenden Werkstücks angepasst werden kann. Um zu beurteilen, ob diese variable Spanwinkelkonstruktion für einen Hersteller die bessere Option ist, müssen Art und Dicke des zu schneidenden Materials, die Schnittlänge, der Schnittanteil hinter der Schere und der für den jeweiligen Auftrag verfügbare Spanwinkel bestimmt werden.
Wenn beispielsweise ein fester Spanwinkel einen festen Spanwinkel von 1 1/3 Zoll hat und die Maschine mit verstellbarem Spanwinkel einen Bereich von 1 bis 3 Grad hat, wobei die 3-Grad-Einstellung für die 1/4-Zoll-Dicke verwendet wird, erzeugt der feste Spanwinkel einen qualitativ besseren Schnitt bei einem 3-Zoll-Streifen. Die Maschine mit variablem Spanwinkel hingegen kann einen qualitativ besseren Schnitt bei einem 1/2-Zoll-Streifen aus 24-Gauge-Material liefern.
Generell sollte man bei Streifen, die dünner als das Achtfache der Materialstärke sind (Beispiel: ein 5 cm breiter Streifen aus 6,35 mm starkem Stahl), keinen guten Schnitt erwarten. Maschinen mit variablem Spanwinkel finden sich in der Regel in Werkstätten mit höheren Kapazitätsanforderungen, z. B. ab 12,75 mm. Bei diesen schwereren Maschinen ermöglicht die Änderung des Spanwinkels bessere Schnitte bei unterschiedlichsten Materialstärken und -arten.
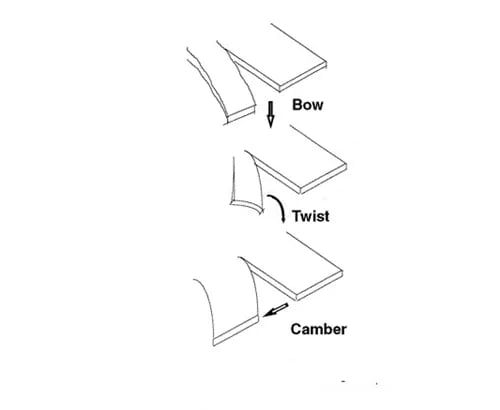
Schervorgang eines Plattenschermaschine ist eine einfache, aber unverzichtbare Methode zum präzisen und effizienten Schneiden von Metallplatten oder -blechen. Sie wird häufig in verschiedenen Branchen eingesetzt, darunter in der Fertigung, im Baugewerbe und in der Metallverarbeitung, um eine breite Palette von Komponenten und Teilen herzustellen.