Die Blechumformung ist ein grundlegender Aspekt bei der Herstellung von Autos bis hin zu Haushaltsgeräten und erfordert eine Kombination aus Fachwissen, Erfahrung und fortschrittlichen Blechumformungsanlagen. Dieser Artikel befasst sich mit den komplexen Prozessen und beleuchtet die Techniken, mit denen Metalle zu hochwertigen Komponenten geformt werden. Von der Auswahl der richtigen Materialien bis hin zum Einsatz präziser Formgebungsmethoden ist die Blechumformung ein anspruchsvolles Handwerk, das langlebige und robuste Produkte für eine Vielzahl von Anwendungen liefert.
Die wichtigsten Erkenntnisse
- Um flache Bleche in kompliziert geformte Bauteile umzuwandeln, werden grundlegende Blechumformungstechniken wie Biegen, Kräuseln und Abstrecken eingesetzt.
- Fortschrittliche Werkzeuge und Technologien in der Blechumformung sorgen für mehr Produktivität, Kosteneffizienz, Flexibilität und Sicherheit.
- Durch optimale Vorgehensweisen bei der Materialauswahl und der Auswahl von Werkzeugen/Geräten können Hersteller Abfall reduzieren und gleichzeitig Qualitätsstandards einhalten.
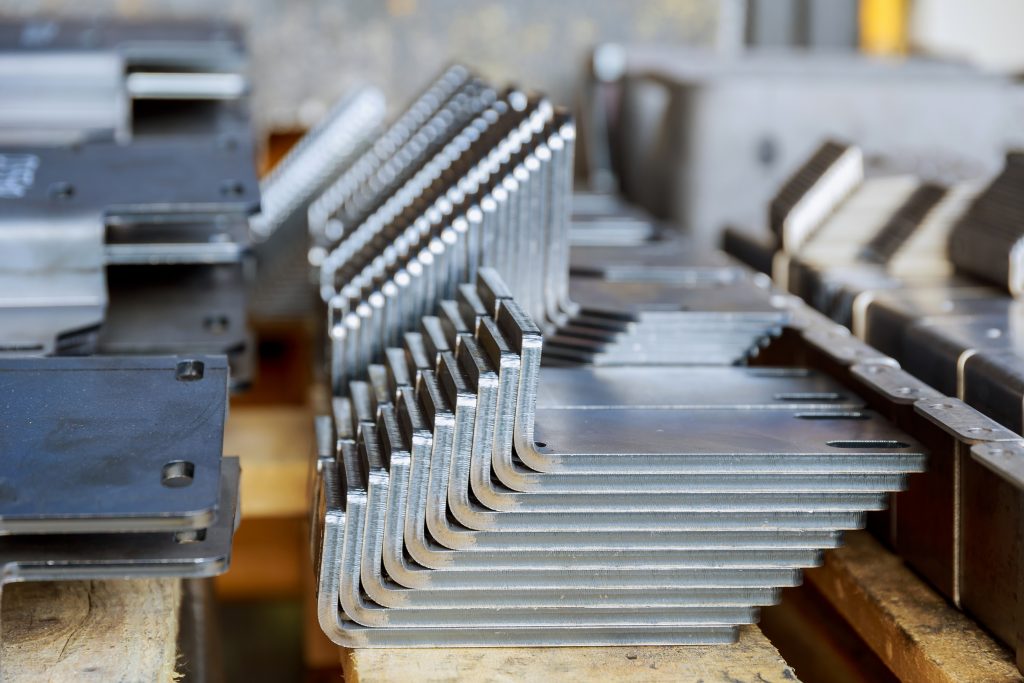
Grundlegende Techniken zur Blechumformung
Beim Blechumformungsprozess werden flache Metallbleche in verschiedene Teile mit komplizierten Formen umgewandelt, die in verschiedenen Branchen wie der Automobil-, Luftfahrt- und Baubranche zum Einsatz kommen. Bei dieser Methode der Metallumformung ist der Einsatz einiger Techniken wie Biegen, Kräuseln oder Bügeln unerlässlich, um die gewünschte Form zu erzielen. Kaltumformung und Streckformen sind einige Methoden, die häufig eingesetzt werden, um unterschiedliche Ergebnisse aus Komponenten zu erzielen, die zu Beginn der genannten Prozesse lediglich als Bleche begannen. Die Beherrschung dieser Techniken kann insgesamt funktionale und dennoch dekorativ geformte Produkte aus Metall für alle beabsichtigten Zwecke erzeugen, sei es für architektonische oder industrielle Anwendungen.
Biegen
Das Metallbiegeverfahren wird in einer Vielzahl von Branchen eingesetzt, beispielsweise in der Automobil-, Bau- und Luftfahrtindustrie. In der Fertigungsindustrie werden in der Regel Abkantpressen oder Stanzpressen verwendet, um den erforderlichen Winkel und Biegeradius für komplexe Formen in Blechen mit Materialstärken, die ihre Walzrichtung bestimmen, präzise zu steuern. So können aus Metallstücken hochwertige Blechteile hergestellt und gleichzeitig Abfall minimiert werden. Außerdem können diese Materialien in funktionale Komponenten mit ansprechendem Aussehen umgewandelt werden. Durch Biegen können die Festigkeit, Steifigkeit oder die Ästhetik verbessert werden, je nachdem, wie es während der Formgebung angewendet wird.
Eisstockschießen
Bei der Blechumformung handelt es sich um einen Prozess, der als Kräuseln bezeichnet wird. Dabei werden Blechkomponenten durch das Entfernen scharfer Kanten oder Grate glatte Kanten und zylindrische Formen verliehen. Das Kräuseln bietet zusätzliche Sicherheit, da raue Bereiche entfernt werden, die bei der Handhabung oder Verwendung potenziell gefährlich sein könnten. Es gibt eine große Auswahl an Werkzeugen, die speziell für diesen Zweck entwickelt wurden, darunter Hämmer, Holzbretter, Hörner, Messeisen und mehr. Kohlenstoffstahl, Edelstahl, Aluminium und Kupfer gelten als die besten Materialien für diese Art der Verarbeitung, da sie nicht nur die Haltbarkeit erhöhen, sondern auch die Ästhetik des Produkts verbessern, bis es vor dem Verlassen der Produktionslinie hohe Qualitätsstandards erfüllt.
Bügeln
Mithilfe eines Stempels und einer Matrize können Blechwerkstücke geformt werden, indem das Material durchgepresst wird, um die gewünschte Form zu erhalten. Dieser Vorgang wird Abstrecken genannt und sorgt für eine gleichmäßige Wandstärke bei der Herstellung von Aluminiumdosen oder beim Tiefziehen. Er hilft auch, Materialabfall sowie durch dünne Bereiche verursachte Schwachstellen zu minimieren und gleichzeitig eine nahezu endkonturnahe Formgebung von Weichmetallen wie Aluminiumblechen mit hervorragender Oberflächenbeschaffenheit zu erreichen. Abstrecken hat viele Vorteile, die in zahlreichen Industriebereichen genutzt werden, von der Baubranche über die Luft- und Raumfahrt bis hin zur Automobilherstellung, wo präzise Ergebnisse bei der Komponentenherstellung erforderlich sind.
Hydroforming
Hydroforming ist eine einzigartige Blechumformungstechnik, bei der Metall mit unter Druck stehender Flüssigkeit geformt wird. Dieses Verfahren ist besonders bei der Herstellung komplexer Formen und Strukturen nützlich, da es eine größere Flexibilität beim Design ermöglicht und glattere, gleichmäßigere Formen erzeugen kann als herkömmliche mechanische Umformungsmethoden.
Beim Hydroforming wird ein Stück Blech in eine Matrize gelegt und dann mit einer Hochdruck-Hydraulikflüssigkeit in die Form der Matrize gepresst. Mit diesem Verfahren können viele verschiedene Formen hergestellt werden. In der Automobil- und Luftfahrtindustrie wird es häufig zur Herstellung von Teilen mit komplexen Geometrien eingesetzt.
Einer der Hauptvorteile des Hydroformings besteht darin, dass es Teile mit einem höheren Festigkeits-Gewichts-Verhältnis als andere Formverfahren herstellen kann. Dies liegt daran, dass der Druck der Hydraulikflüssigkeit gleichmäßig auf das gesamte Metallstück ausgeübt wird, wodurch das Risiko von Schwachstellen oder Defekten im fertigen Produkt verringert wird.
Darüber hinaus ist Hydroforming oft eine kostengünstigere Produktionsmethode, da es weniger Werkzeuge und weniger Material erfordert als andere Methoden. Es ist jedoch zu beachten, dass die anfänglichen Einrichtungskosten aufgrund der Notwendigkeit spezieller Geräte und Formen höher sein können.
Trotz dieser potenziellen Nachteile ist Hydroforming eine vielseitige und wertvolle Technik in der Blechumformung, die eine einzigartige Kombination aus Präzision, Effizienz und Flexibilität bietet.
Stanzen
Stanzen ist eine weitere grundlegende Technik bei der Blechumformung. Bei diesem Verfahren werden Löcher in das Blech gebohrt, indem mithilfe eines Stempels und einer Matrize eine hohe Kraft auf das Blech ausgeübt wird. Der Stempel ist das Werkzeug, das das Metall durchdringt, um das Loch zu erzeugen, während sich die Matrize auf der gegenüberliegenden Seite des Blechs befindet, das Material stützt und dem Loch seine Form und Größe verleiht.
Diese Methode ist für die Massenproduktion äußerst effizient, da sie die Herstellung mehrerer identischer Löcher in kurzer Zeit ermöglicht. Sie ist besonders nützlich in Branchen wie der Automobil- und Luftfahrtindustrie, in denen Präzision und Konsistenz entscheidend sind.
Das Stanzen hat jedoch auch seine Grenzen. Der Prozess kann Verformungen an den Rändern des Lochs verursachen, die als „Überschlag“ bezeichnet werden, und kann bei unsachgemäßer Ausführung auch zu Rissen im Metall führen. Die Qualität von Stempel und Matrize sowie die richtige Ausrichtung und Kontrolle der Stanzkraft sind entscheidende Faktoren für einen erfolgreichen Stanzprozess.
Trotz dieser Herausforderungen bleibt das Stanzen eine weit verbreitete und wertvolle Technik in der Blechumformung, da es eine Kombination aus Geschwindigkeit, Genauigkeit und Effizienz bietet.
Geräte zur Blechumformung
Ausrüstung | Beschreibung | Anwendung |
---|---|---|
Abkantpressen | Abkantpressen werden verwendet, um Blech in die gewünschte Form zu biegen. Sie ermöglichen eine präzise Kontrolle über den Winkel und Radius der Biegung. | Wird normalerweise in der Fertigungsindustrie verwendet, um komplexe Formen in Platten zu erzeugen. |
CNC-Maschinen | CNC-Maschinen sind automatisierte Werkzeuge, die Schneid- und Formprozesse präzise steuern können. | Ideal für die Blechbearbeitung, da damit komplexe Komponenten schnell und hochpräzise hergestellt werden können. |
Hydraulische Pressen | Hydraulische Pressen formen Metall mithilfe von Flüssigkeit unter Druck. Dies ermöglicht eine größere Flexibilität beim Design und glattere, gleichmäßigere Formen. | Besonders nützlich bei der Herstellung komplexer Formen und Strukturen. |
Walzen | Walzen dienen dazu, Bleche in zylindrische Formen zu biegen oder zu glätten. | Wird in verschiedenen Branchen, einschließlich der Automobil- und Luftfahrtindustrie, zum Erzeugen gekrümmter Oberflächen und zum Entfernen von Falten aus Blechen verwendet. |
Stanzpressen | Stanzpressen werden verwendet, um Löcher oder Vertiefungen in das Blech zu bohren. Sie bieten hohe Kraft und Präzision. | Wird in Branchen wie der Automobil- und Luftfahrtindustrie verwendet, in denen es auf Präzision und Konsistenz ankommt. |
Schere | Scheren werden verwendet, um gerade Schnitte in flaches Metall zu machen. Sie funktionieren, indem man das flache Metall zwischen die Klingen legt und Kraft anwendet. | Wird in vielen Metallverarbeitungswerkstätten zum Schneiden und Trimmen von Metallblechen verwendet. |
Biegemaschinen | Biegemaschinen werden zum Biegen von Metall durch Kraft, Druck, Hitze oder auf andere Weise verwendet. | Wird in verschiedenen Branchen, einschließlich der Automobil-, Luft- und Raumfahrt- und Bauindustrie, zum Biegen von Metallblechen in die gewünschte Form verwendet. |
Revolverschläge | Revolverstanzen werden verwendet, um verschiedene Formen in Metall zu erzeugen. Sie funktionieren, indem sie das Metallblech an Ort und Stelle halten, während die Stanzen der Maschine verwendet werden, um die gewünschten Formen zu erzeugen. | Wird in Branchen wie der Fertigungs- und Baubranche verwendet, in denen hohe Geschwindigkeit und Präzision bei der Herstellung unterschiedlicher Formen in Metallblechen erforderlich sind. |
Arten von Blechumformungsgeräten
- Abkantpressen:
- Funktion: Abkantpressen sind unerlässlich, um Blech in bestimmte Winkel und Formen zu biegen. Sie funktionieren, indem sie mithilfe eines Stempel- und Matrizensystems eine kontrollierte Kraft anwenden und so eine präzise Metallformung ermöglichen.
- Vorteile: Hohe Flexibilität für individuelle Biegeaufgaben, geeignet für eine Vielzahl von Materialien und Stärken. Moderne CNC-Abkantpressen bieten höhere Genauigkeit, Geschwindigkeit und Programmierbarkeit.
- Anwendungen: Wird häufig in der Automobil-, Luft- und Raumfahrt- und Bauindustrie zur Herstellung von Metallteilen wie Halterungen, Gehäusen und Rahmen verwendet.
- Hydraulische Pressen:
- Funktion: Hydraulische Pressen erzeugen durch Flüssigkeitsdruck hohe Kräfte, wodurch sie Bleche mit größerer Kraft und Präzision formen können. Diese Maschinen sind ideal für Tiefzieh- und Stanzvorgänge, bei denen Metalle in komplexe Formen gezogen werden.
- Vorteile: Sie können große Kraft ausüben und sind daher ideal für dickere Metalle. Hydraulische Systeme sorgen für eine gleichmäßige, kontrollierte Bewegung und damit für gleichbleibende Ergebnisse.
- Anwendungen: Wird häufig im Automobilbau zur Produktion von Karosserieteilen sowie in der Metallverarbeitung verwendet, wo Hochleistungsformung erforderlich ist.
- Stanzmaschinen:
- Funktion: Stanzmaschinen führen Hochgeschwindigkeitsvorgänge mit Matrizen und Stempeln aus, um Blech in sich wiederholenden Zyklen zu formen, zu schneiden oder zu prägen. Diese Maschinen sind für die Massenproduktion ausgelegt und können verschiedene Formprozesse wie Stanzen, Stanzen und Prägen durchführen.
- Vorteile: Hohe Produktionseffizienz und die Fähigkeit, komplexe Formen mit minimalem Abfall zu verarbeiten. Beim Stanzen können große Mengen zu geringeren Stückkosten verarbeitet werden.
- Anwendungen: Wird häufig bei der Herstellung von Komponenten für die Elektronik-, Haushaltsgeräte- und Automobilindustrie verwendet, wie beispielsweise Metallverbinder, Halterungen und Abdeckungen.
- Rollformmaschinen:
- Funktion: Rollformmaschinen biegen lange Metallstreifen kontinuierlich in einen gleichmäßigen Querschnitt. Das Metall durchläuft eine Reihe von Walzen, die es nach und nach formen, wodurch lange Profile wie Kanäle, Balken oder Dachplatten entstehen.
- Vorteile: Kontinuierliche Produktion gleichmäßiger Profile mit minimalem Abfall und hoher Präzision. Es ist effizient für die Produktion großer Stückzahlen und verarbeitet ein breites Spektrum an Metalldicken.
- Anwendungen: Beliebt im Bau- und Infrastruktursektor zur Herstellung von Strukturkomponenten wie Stahlträgern, Dachplatten und Metallverkleidungen.
- Stanzpressen:
- Funktion: Stanzpressen erzeugen Löcher, Schlitze oder komplizierte Formen in Blech, indem sie einen Stempel durch das Material in eine Matrize drücken. Diese Maschinen können manuell bedient oder für höhere Präzision durch CNC-Technologie automatisiert werden.
- Vorteile: Hochgeschwindigkeitsproduktion sich wiederholender Designs mit außergewöhnlicher Genauigkeit. CNC-Stanzpressen bieten flexible Programmierung für benutzerdefinierte Designs.
- Anwendungen: Wird häufig in Branchen verwendet, in denen perforierte oder kundenspezifische Metallbleche benötigt werden, beispielsweise bei der Herstellung von Schaltschränken, Maschinenteilen und Belüftungssystemen.
- Laserschneidmaschinen:
- Funktion: Laserschneidmaschinen verwenden fokussierte Laserstrahlen, um Metallbleche mit äußerster Präzision zu schneiden, oft ohne physischen Kontakt. Dies ermöglicht das Schneiden komplizierter Designs und feiner Details.
- Vorteile: Bietet höchste Präzision und Flexibilität und eignet sich zum Schneiden komplexer Formen, Kurven und dünner Materialien mit minimaler Verzerrung. Laserschneiden sorgt außerdem für glatte Kanten und reduziert den Nachbearbeitungsaufwand.
- Anwendungen: Perfekt für Branchen wie die Luft- und Raumfahrt, Elektronik und Automobilindustrie, in denen Präzision von entscheidender Bedeutung ist. Zu den üblichen Verwendungszwecken gehören das Schneiden von Metallteilen, dekorativen Paneelen und komplizierten Metallkomponenten.
- Schermaschinen:
- Funktion: Schermaschinen sind dafür ausgelegt, gerade Linien präzise in Bleche zu schneiden. Sie funktionieren, indem sie eine Klinge gegen das Blech drücken und so saubere Schnitte ohne zusätzliche Nachbearbeitung erzeugen.
- Vorteile: Effizient und kostengünstig für gerade Schnitte mit minimalem Materialabfall. Scheren ist ideal für die Produktion großer Stückzahlen mit gleichbleibenden Ergebnissen.
- Anwendungen: Wird bei der Herstellung von Metallblechen für das Bauwesen, den Schiffsbau und Herstellungsprozesse verwendet, die präzise zugeschnittene Metallbleche erfordern.
- Blechbiegemaschinen:
- Funktion: Automatische Plattenbiegemaschinen sind für das effiziente Biegen großer Metallplatten ausgelegt. Durch die Anwendung einer gleichmäßigen Kraft werden Biegungen auf allen Seiten der Platte erzeugt, ohne dass das Material neu positioniert werden muss.
- Vorteile: Hochgeschwindigkeitsbiegen mit Automatisierung reduziert die Arbeitskosten und verbessert die Konsistenz. Plattenbiegemaschinen können große Bleche problemlos verarbeiten und sind daher ideal für die Herstellung von Teilen mit mehreren Biegungen.
- Anwendungen: Häufig in Branchen wie dem Elektroschrankbau, der Herstellung von Heizungs-, Lüftungs- und Klimatechnik und der Metallverarbeitung im großen Maßstab, in denen schnelles und gleichmäßiges Biegen von Platten entscheidend ist.
Jeder Typ von Blechumformungsanlagen spielt eine entscheidende Rolle in der modernen Fertigung, vom Präzisionsbiegen bis zum Schneiden und Formen großer Stückzahlen. Durch die Auswahl der richtigen Ausrüstung können Hersteller ihre Produktionskapazitäten verbessern, die Effizienz steigern und hochwertige Metallkomponenten herstellen, die den hohen Standards der heutigen Industrien entsprechen.
Materialien für die Blechumformung
Blechumformung kann mit einer Vielzahl von Metallen und Legierungen durchgeführt werden, je nach den spezifischen Anforderungen der Anwendung. Häufig verwendete Materialien sind Stahl, Aluminium, Edelstahl, Kupfer und Messing. Die Wahl des Materials hängt von Faktoren wie Festigkeit, Korrosionsbeständigkeit, Formbarkeit und Kosten ab.
Häufig verwendete Metalle und Legierungen
- Stahl: Stahl ist aufgrund seiner hohen Festigkeit, Haltbarkeit und Erschwinglichkeit eine beliebte Wahl für die Blechumformung. Er wird häufig in der Automobil-, Bau- und Geräteindustrie verwendet.
- Aluminium: Aluminium bietet eine hervorragende Korrosionsbeständigkeit, ist leicht und gut verformbar. Es wird häufig in der Luft- und Raumfahrt, der Automobilindustrie und der Elektronikindustrie verwendet.
- Edelstahl: Edelstahl bietet hervorragende Korrosionsbeständigkeit und hohe Festigkeit. Er wird häufig in Anwendungen eingesetzt, bei denen hygienische und ästhetische Eigenschaften erforderlich sind, wie etwa bei Küchengeschirr und medizinischen Geräten.
- Kupfer: Kupfer verfügt über eine ausgezeichnete elektrische Leitfähigkeit und hervorragende thermische Eigenschaften und eignet sich daher für elektrische Anwendungen und Wärmeübertragungsanwendungen.
- Messing: Messing ist eine Kupfer-Zink-Legierung, die sich gut formen lässt, korrosionsbeständig ist und ein attraktives Aussehen hat. Es wird häufig in dekorativen und architektonischen Anwendungen verwendet.
Zusammenfassend lässt sich sagen, dass die Blechumformung ein vielseitiger Prozess ist, der die Herstellung komplexer Komponenten und Strukturen ermöglicht. Das Verständnis der verschiedenen Prozessarten und verwendeten Materialien ist für die Erzielung einer präzisen Fertigung von entscheidender Bedeutung. Durch den Einsatz der richtigen Techniken und Materialien können Hersteller hochwertige Blechkomponenten für eine breite Palette von Anwendungen in verschiedenen Branchen herstellen.
Fallstudie: Automobilindustrie – Optimierung der Blechumformung für Kosteneffizienz
In der Automobilindustrie sind Präzision und Kosteneffizienz bei der Blechumformung entscheidende Faktoren. Werfen wir einen Blick auf eine Fallstudie aus der Praxis, die die Bedeutung der Optimierung des Umformungsprozesses unterstreicht.
Unternehmen: ABC Auto Manufacturing Herausforderung: Produktionseffizienz steigern und Kosten senken in der Blechumformung
ABC Auto Manufacturing, ein führender Automobilhersteller, stand vor Herausforderungen bei seinen Blechumformungsprozessen. Das Unternehmen hatte mit hohen Produktionskosten und zeitaufwändigen Abläufen aufgrund häufiger Werkzeugwechsel und Materialabfällen zu kämpfen.
Um diese Herausforderungen zu meistern, entschied sich ABC Auto Manufacturing für eine Zusammenarbeit mit einem auf Blechumformung spezialisierten Unternehmen, XYZ Fabrications. XYZ Fabrications verfügte über Erfahrung in der Optimierung von Blechumformungsprozessen durch moderne Simulationstools und Verfahren zur Prozessoptimierung.
Lösung: Simulationsbasierte Prozessoptimierung
XYZ Fabrications führte eine gründliche Analyse der Produktionslinie von ABC Auto Manufacturing durch und identifizierte Verbesserungsbereiche. Durch den Einsatz moderner Simulationssoftware konnten sie das Verhalten des Blechs während des Umformungsprozesses genau vorhersagen, wodurch der Bedarf an physischen Prototypen und Versuch-und-Irrtum-Iterationen reduziert wurde.
Mit dem simulationsgesteuerten Ansatz optimierte XYZ Fabrications das Werkzeugdesign, die Matrizengeometrie und die Prozessparameter, um Materialabfall zu minimieren, Zykluszeiten zu verkürzen und die Gesamtproduktionseffizienz zu verbessern. Durch die Feinabstimmung des Prozesses konnten sie die gewünschte Präzision erreichen und gleichzeitig die Kosten deutlich senken.
Ergebnisse: Höhere Effizienz und Kosteneinsparungen
Die Zusammenarbeit zwischen ABC Auto Manufacturing und XYZ Fabrications brachte beeindruckende Ergebnisse hervor. Durch die Implementierung der optimierten Blechumformungsprozesse erreichte ABC Auto Manufacturing:
- Weniger Ausschuss und Materialverschwendung: Der simulationsgesteuerte Ansatz trug dazu bei, den Materialabfall zu minimieren, was zu erheblichen Kosteneinsparungen für das Unternehmen führte.
- Verbesserte Produktionseffizienz: Durch die Optimierung der Prozessparameter und des Werkzeugdesigns wurden die Zykluszeiten reduziert, was höhere Produktionsraten und eine verbesserte Effizienz ermöglichte.
- Verbesserte Komponentenqualität: Die optimierten Umformungsprozesse gewährleisteten gleichbleibende und hochwertige Komponenten, die den strengen Anforderungen der Automobilindustrie entsprachen.
Anhand dieser Fallstudie können wir die konkreten Vorteile der Optimierung erkennen. Blechumformungsverfahren in der Automobilindustrie. Durch den Einsatz fortschrittlicher Simulationstools und Prozessoptimierungstechniken können Unternehmen Kosteneinsparungen erzielen, die Produktionseffizienz verbessern und hochwertige Komponenten für verschiedene Branchen liefern.