Was ist ein Nutwerkzeug?
A Nutfräser, auch als Nutfräser oder Nuteinsatz bekannt, ist ein Schneidwerkzeug, das bei Bearbeitungsvorgängen zum Erzeugen von Nuten oder Kanälen in einem Werkstück verwendet wird. Diese Nuten können je nach Anwendung und Branche unterschiedlichen Zwecken dienen. Hier ist ein Überblick über Nutwerkzeuge und ihre üblichen Verwendungszwecke:
10 wichtige Überlegungen zur Verwendung eines Nutwerkzeugs.
Den Rillentyp verstehen
Es ist wichtig, die drei Haupttypen von Nutwerkzeugen zu verstehen: Außennut, Innenlochnut und Stirnflächennut.
Außennuten sind am einfachsten zu bearbeiten, da die Schwerkraft und der Einsatz von Kühlmittel die Spanabfuhr unterstützen können. Der Bediener kann die Bearbeitung von Außennuten direkt beobachten, wodurch sich die Qualität des Bearbeitungsprozesses relativ einfach überwachen lässt. Es ist jedoch wichtig, potenzielle Konstruktions- oder Spannprobleme mit dem Werkstück zu vermeiden. Um optimale Schnittergebnisse zu erzielen, ist es am besten, die Spitze des Nutwerkzeugs etwas unterhalb der Mittellinie zu halten.
Das Innenlochstechen ähnelt dem Außendurchmesserstechen, mit der Ausnahme, dass die Kühlmittelanwendung und die Spanabfuhr anspruchsvoller sein können. Die besten Ergebnisse werden erzielt, wenn die Spitzenposition beim Innenstechen leicht über der Mittellinie liegt.
Beim Einstechen der Stirnfläche muss sich das Werkzeug in axialer Richtung bewegen können und der Radius der Werkzeugflanke muss dem Radius der bearbeiteten Oberfläche entsprechen. Die Schneidkantenposition des Einstechwerkzeugs sollte leicht über der Mittellinie liegen.
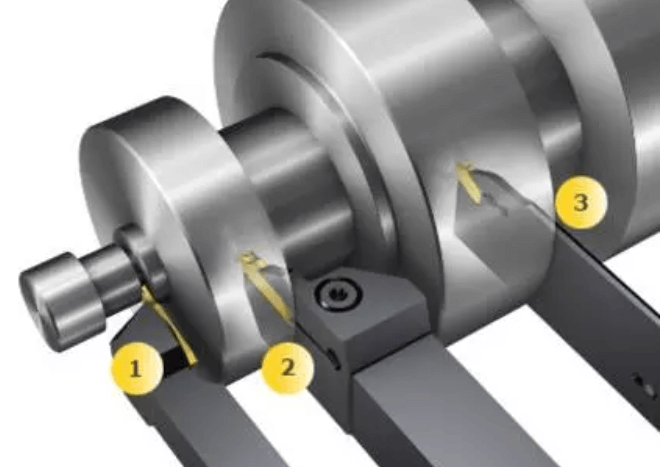
Bearbeitungsmaschinen und Anwendungen
Im Nutenverfahren, der Konstruktionstyp und die technischen Spezifikationen des Nutwerkzeugs sind ebenfalls wichtige Faktoren, die berücksichtigt werden müssen. Zu den wichtigsten Leistungsanforderungen an Werkzeugmaschinen gehören:
Über ausreichend Leistung verfügen, um sicherzustellen, dass das Werkzeug im richtigen Drehzahlbereich arbeitet, ohne abzuwürgen oder zu vibrieren;
Verfügt über eine hohe Steifigkeit, um die erforderlichen Schnitte ohne Rattern auszuführen;
Ein ausreichend hoher Kühlmitteldruck und -durchfluss muss vorhanden sein, um die Spanabfuhr zu erleichtern;
Verfügt über ein hohes Maß an Genauigkeit.
Um die gewünschte Nutform und -größe zu erzeugen, ist es außerdem wichtig, die Werkzeugmaschine richtig einzustellen und zu kalibrieren.
Verstehen Sie die Materialeigenschaften des Werkstücks
Um die Auswirkungen des Werkstücks auf das Werkzeug zu verstehen, ist es wichtig, die Eigenschaften des Werkstückmaterials wie Zugfestigkeit, Kaltverfestigungseigenschaften und Zähigkeit zu kennen. Bei der Bearbeitung unterschiedlicher Werkstückmaterialien sind unterschiedliche Kombinationen aus Schnittgeschwindigkeit, Vorschubgeschwindigkeit und Werkzeugeigenschaften erforderlich. Unterschiedliche Werkstückmaterialien können auch spezifische Werkzeuggeometrien erfordern, um Absplitterungen vorzubeugen, oder den Einsatz spezifischer Beschichtungen, um die Lebensdauer des Werkzeugs zu verlängern.
Wählen Sie das richtige Nutwerkzeug
Die Wirtschaftlichkeit der Bearbeitung hängt maßgeblich von der richtigen Auswahl und Nutzung der Stechwerkzeuge ab.
Mit dem Stechwerkzeug kann die Werkstückgeometrie auf zwei Arten bearbeitet werden:
Die erste besteht darin, die gesamte Rillenform durch einen einzigen Schnitt zu bearbeiten.
Die zweite Möglichkeit besteht darin, die endgültige Größe der Nut durch Schneiden in mehreren Schritten grob herauszuarbeiten.
Nachdem die Werkzeuggeometrie festgelegt wurde, kann es von Vorteil sein, über eine Werkzeugbeschichtung nachzudenken, die die Spanabfuhrleistung verbessert.
Formularwerkzeuge
Bei der Zerspanung großer Stückzahlen kann es vorteilhaft sein, über den Einsatz von Umformwerkzeugen nachzudenken.
Das Formwerkzeug kann alle oder die meisten Nutformen in einem einzigen Arbeitsgang schneiden, wodurch die Position des Werkzeugs freigegeben und die Verarbeitungszykluszeit verkürzt wird.
Ein Nachteil von Formwerkzeugen ohne Klinge besteht darin, dass das gesamte Werkzeug ausgetauscht werden muss, wenn einer der Zähne bricht oder sich schneller abnutzt als die anderen Zähne.
Wichtig ist die Kontrolle der vom Werkzeug erzeugten Späne und der für die Formbearbeitung erforderlichen Maschinenleistung. Dies muss berücksichtigt werden.
Wählen Sie Single Point Multifunktionswerkzeug
Durch den Einsatz von Multifunktionswerkzeugen können Werkzeugbahnen sowohl in axialer als auch in radialer Richtung erzeugt werden.
Mit diesem Werkzeugtyp können nicht nur Nuten bearbeitet, sondern auch Durchmesser gedreht, Radius und Winkel interpoliert sowie Mehrrichtungsdrehungen durchgeführt werden.
Sobald die Klinge mit dem Schneiden beginnt, bewegt sie sich axial von einem Ende zum anderen Ende des Werkstücks, während der Kontakt mit dem Werkstück erhalten bleibt.
Durch den Einsatz eines Multifunktionswerkzeugs bleibt mehr Zeit für das Schneiden des Werkstücks, anstatt Werkzeuge zu wechseln oder Leerhubbewegungen auszuführen.
Multifunktionswerkzeuge tragen zudem dazu bei, den Bearbeitungsprozess des gesamten Werkstücks zu optimieren.
Verwenden Sie die richtige Verarbeitungsreihenfolge
Bei einer rationalen Planung der optimalen Bearbeitungsreihenfolge müssen mehrere Faktoren berücksichtigt werden, beispielsweise die Veränderung der Werkstückfestigkeit vor und nach der Bearbeitung der Nut, da die Festigkeit des Werkstücks nach der ersten Bearbeitung der Nut abnimmt.
Dies kann dazu führen, dass der Bediener eine niedrigere Vorschub- und Schnittgeschwindigkeit als optimal verwendet, um Rattern zu vermeiden. Das Verringern der Schnittparameter kann jedoch zu längeren Bearbeitungszeiten, kürzerer Werkzeuglebensdauer und instabiler Schnittleistung führen.
Darüber hinaus muss berücksichtigt werden, ob die Grate im nachfolgenden Prozess in die zuvor gefrästen Rillen gedrückt werden.
Als allgemeine Richtlinie empfiehlt es sich, mit dem vom Werkzeughalter am weitesten entfernten Punkt zu beginnen, nachdem das Drehen des Außendurchmessers (OD) und Innendurchmessers (ID) abgeschlossen ist, und anschließend die Nuten und andere Strukturmerkmale zu bearbeiten.
Die Rolle von Vorschub und Schnittgeschwindigkeit
Vorschub und Schnittgeschwindigkeit sind entscheidende Faktoren bei der Nutbearbeitung. Ungeeignete Vorschub- und Schnittgeschwindigkeiten können zu Rattern, verkürzter Werkzeuglebensdauer und längeren Bearbeitungszykluszeiten führen.
Verschiedene Faktoren, darunter das Werkstückmaterial, die Werkzeuggeometrie, Kühlmittelart und -konzentration, Wendeplattenbeschichtung und Maschinenleistung, können sich auf Vorschub und Schnittgeschwindigkeit auswirken.
Um Probleme zu beheben, die durch falsche Vorschub- und Schnittgeschwindigkeiten verursacht werden, ist häufig eine Nachbearbeitung erforderlich.
Zwar gibt es eine Fülle von Informationen zu den „optimalen“ Vorschub- und Schnittgeschwindigkeiten verschiedener Werkzeuge, die relevantesten und praktischsten Angaben werden jedoch in der Regel vom Werkzeughersteller bereitgestellt.
Auswahl der Klingenbeschichtung
Durch die Beschichtung einer Hartmetallklinge kann deren Lebensdauer erheblich verlängert werden.
Indem die Beschichtung eine Schmierschicht zwischen Werkzeug und Span bildet, verkürzt sie außerdem die Bearbeitungszeit und verbessert die Oberflächenbeschaffenheit des Werkstücks.
Zu den heute häufig verwendeten Beschichtungen zählen TiAlN, TiN und TiCN. Für eine optimale Leistung ist es wichtig, die Beschichtung auf das zu bearbeitende Material abzustimmen.
Schneidflüssigkeit
Bei der ordnungsgemäßen Anwendung der Schneidflüssigkeit geht es darum, an der Schnittstelle, wo die gerillte Wendeschneidplatte mit dem Werkstück in Kontakt kommt, ausreichend Flüssigkeit bereitzustellen.
Die Schneidflüssigkeit dient zwei Zwecken: Sie kühlt den Schneidbereich und unterstützt die Spanabfuhr.
Durch Erhöhen des Schneidflüssigkeitsdrucks an der Schnittstelle lässt sich die Spanabfuhr bei der Bearbeitung von Sacklochnuten im Innendurchmesser äußerst effektiv verbessern.
Beim Einstechen anspruchsvoller Materialien, beispielsweise mit hoher Zähigkeit oder Viskosität, bietet die Hochdruckkühlung erhebliche Vorteile.
Auch die Konzentration des wasserlöslichen Kühlmittels auf Ölbasis ist für das Graben von schwierigen Materialien von entscheidender Bedeutung.
Während die typische Kühlmittelkonzentration zwischen 3% und 5% liegt, können Sie auch eine Erhöhung der Konzentration (bis zu 30%) testen, um die Schmierfähigkeit des Kühlmittels zu verbessern und eine Schutzschicht für die Schaufelspitze bereitzustellen.