A V-Nutfräser, auch V-Nutmaschine genannt oder V-Nutfräserist ein Spezialwerkzeug, das in der Blechbearbeitung verwendet wird, um präzise V-förmige Rillen oder Kerben entlang der Oberfläche eines Blechs zu erzeugen. Diese Rillen werden häufig für verschiedene Zwecke wie Biegen, Falten, Schweißen oder dekorative Zwecke verwendet.
Die Blechbearbeitung ist ein wesentlicher Aspekt der mechanischen Verarbeitung, insbesondere in Branchen wie der Luftfahrt, Haushaltsgeräten, Automobilen, Aufzügen und anderen. Blechteile werden in diesen Branchen häufig verwendet.
Das Biegen ist einer der entscheidendsten Prozesse bei der Blechbearbeitung und wird als ein einziger Umformungsprozess angesehen.
V-Nut-Technik
Die Qualität des Biegevorgangs beeinflusst maßgeblich die Größe und das Aussehen des Endprodukts.
Daher ist die Sicherstellung der Formmaße und -winkel des Werkstücks während des Biegeprozesses ein entscheidender Forschungsbereich der Biegetechnik.
Mit der wirtschaftlichen Entwicklung und der Verbesserung des Lebensstandards der Menschen werden ihre Sinnesbedürfnisse anspruchsvoller.
Je komplizierter die Form der Blechdekorationen ist, desto mehr spiegelt sie das Können und den modischen Stil des Designers wider und erregt so die Aufmerksamkeit der meisten Kunden.
Darüber hinaus muss das Werkstück technische Anforderungen erfüllen, wie zum Beispiel einen minimalen Kreisbogenradius an der Biegekante, keine Biegespuren auf der Oberfläche und keine Vertiefungen auf der Dekorfläche.
Die herkömmliche Abkantpresse konnte bestimmte technische Anforderungen nicht mehr erfüllen, was zur Entwicklung der Stechbiegetechnik für Bleche führte.
In diesem Artikel geht es um die Besonderheiten der Rilltechnik, Methoden zum Rillen von Blechen und Möglichkeiten zur Gewährleistung von Maß- und Winkelgenauigkeit beim Biegeprozess.
Traditionelle Biegemethoden und ihre Grenzen
Bei der herkömmlichen Biegemethode in der Blechbearbeitung wird Druck von den oberen und unteren Matrizen einer Abkantpresse verwendet.
Das Biegen des Blechs erfolgt durch die Öffnung des Unterwerkzeugs und die Oberkante des Oberwerkzeugs.
Die Metallplatte erfährt eine Umwandlung von einer elastischen Verformung zu einer plastischen Verformung.
Der Biegewinkel wird durch die Tiefe des oberen Gesenks im unteren Gesenk bestimmt und der Biegeradius (R) muss größer oder gleich der Plattendicke (t) sein, wie in Abbildung 1 dargestellt.
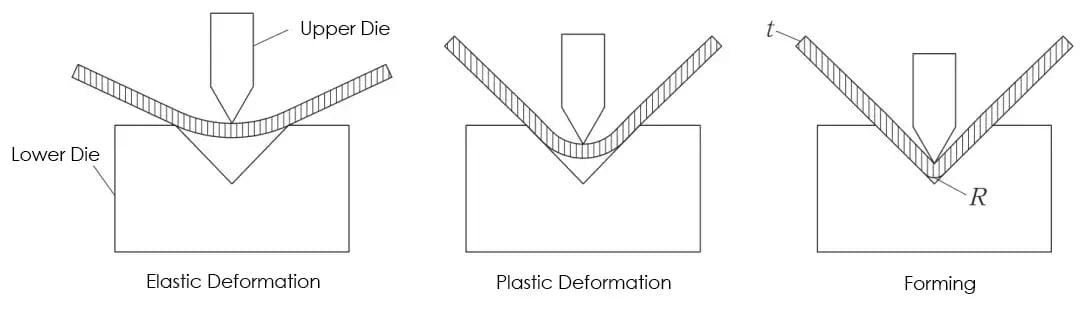
Allerdings werden die aktuellen Anforderungen an die Form der Werkstücke immer höher. Bei manchen Teilen mit komplexen Formen (siehe Abbildung 2) reichen herkömmliche Biegetechniken nicht aus, und der Biegeradius lässt sich mit der herkömmlichen Methode nicht steuern. Dadurch wird es schwierig, die technischen Anforderungen für das Biegen ohne Einkerbung zu erfüllen.
Als Ergebnis entstand eine neue Biegetechnik namens Rillenbiegen.
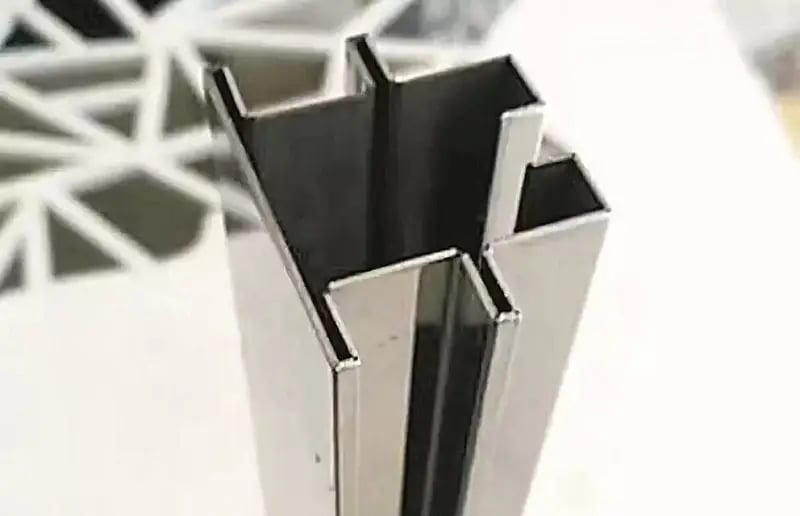
Merkmale des Nutbiegens
Beginnen wir mit der Definition von Groove Bending.
Beim Nutbiegen handelt es sich um eine Technik, bei der mit einer Nutmaschine eine Reihe von V-Schlitzen in das zu biegende Blech eingebracht und das Blech anschließend auf einer Abkantpresse gebogen wird, um den spezifischen Anforderungen zu entsprechen.
Die Hauptmerkmale des Nutbiegeverfahrens sind folgende:
Kleiner Bogenradius und keine Biegespuren am Werkstück
Der maximale Bogenradius der Werkstückkante ist direkt proportional zur Plattendicke nach dem Biegen. Je dicker die Platte, desto größer der Bogenradius.
Nach dem V-Nuten des Blechs beträgt die verbleibende Dicke jedoch nur noch die Hälfte oder ist sogar noch geringer. Dadurch wird der Bogenradius nach dem Biegen erheblich reduziert.
Darüber hinaus wird durch die reduzierte Dicke an der Biegestelle nach dem Nuten die Verformungskraft beim Biegen verringert, die sich nicht auf den Rückbiegebereich auswirkt. Dadurch entstehen nach dem Biegen keine Biegespuren auf der Werkstückoberfläche.
Mit dieser Technik können die technischen Anforderungen erfüllt werden, die einen kleinen Bogenradius, keine Biegespuren und keine Einkerbungen auf dekorativen Oberflächen in hochwertigen Umgebungen wie Hotels, Banken, Einkaufszentren und Flughäfen erfordern.
Reduzierung der zum Blechbiegen auf einer Abkantpresse erforderlichen Tonnage
Beim Biegen ist die zum Biegen von Blech erforderliche Kraft proportional zu dessen Dicke. Je dicker das Blech, desto größer ist die erforderliche Biegekraft und desto mehr Tonnage ist an der Abkantpresse erforderlich.
Durch das Rillen des Biegeteils der Metallplatte vor dem Biegen wird die verbleibende Dicke jedoch erheblich reduziert. Diese Dickenreduzierung verringert entsprechend die erforderliche Biegekraft, sodass die Platte auf einer Biegemaschine mit geringerer Tonnage gebogen werden kann.
Dadurch sinken nicht nur die Gerätekosten, sondern es wird auch Energie und Platz gespart.
Biegen komplex geformter Werkstücke und Kontrolle der Elastizität
Das in Abbildung 2 dargestellte Teil kann nicht auf einer herkömmlichen Biegemaschine gebogen und geformt werden. Dies ist jedoch manuell möglich, nachdem an der Biegestelle eine V-Form eingekerbt wurde.
Darüber hinaus können durch die Steuerung der verbleibenden Blechdicke die Rückfederkraft und der Rückfederwinkel gesteuert werden.
Wenn die verbleibende Plattendicke nach dem Nuten bei etwa 0,3 mm gehalten wird, kann der Rückfederungswinkel erheblich reduziert werden und die Rückfederung kann im Wesentlichen vernachlässigt werden.
V-Nut-Methode
In der Blechfertigung kommen häufig Portalhobelmaschinen und Blechnutmaschinen zum Einsatz, um V-förmige Schlitze in Bleche zu erzeugen.
RGHK-1500x4000 Horizontale CNC-V-Nutmaschine
Positionieren Sie die gebogene Platte zur Ausrichtung in der Nutmaschine und geben Sie die Plattendicke für das automatische Nuten ein.
Beim Nuten ist auf folgende zwei Aspekte zu achten.
Nuttiefe und Restdicke
Bei einer gegebenen Plattendicke stehen die Nuttiefe und die verbleibende Dicke in einem entsprechenden Verhältnis.
Gemäß den Anforderungen der Biegetechnik wird ein Restdickenwert festgelegt, der standardmäßig typischerweise bei 0,8 mm liegt und mindestens 0,3 mm nicht unterschreiten sollte.
Anschließend werden die Nutanzahl und die Nuttiefe in Abhängigkeit von der Plattendicke eingestellt.
Um Metallgrate zu vermeiden und die Messer zu schützen, sollte der Messervorschub nicht zu hoch sein.
Normalerweise darf die Tiefe der ersten Rille 0,8 mm nicht überschreiten und der Rillvorgang sollte in mindestens zwei Schnitten durchgeführt werden. Ein Schnitt ist nicht angemessen.
Wenn Sie beispielsweise ein 1,2 mm dickes Edelstahlblech nuten, beträgt die verbleibende Dicke nach dem Nuten 0,5 mm.
Wenn der erste Nutvorschub auf 0,5 mm und der zweite Nutvorschub auf 0,2 mm eingestellt ist, beträgt die verbleibende Dicke des Blechs 0,5 mm mit minimalem Metallgrat, wie in Abbildung 3 gezeigt.
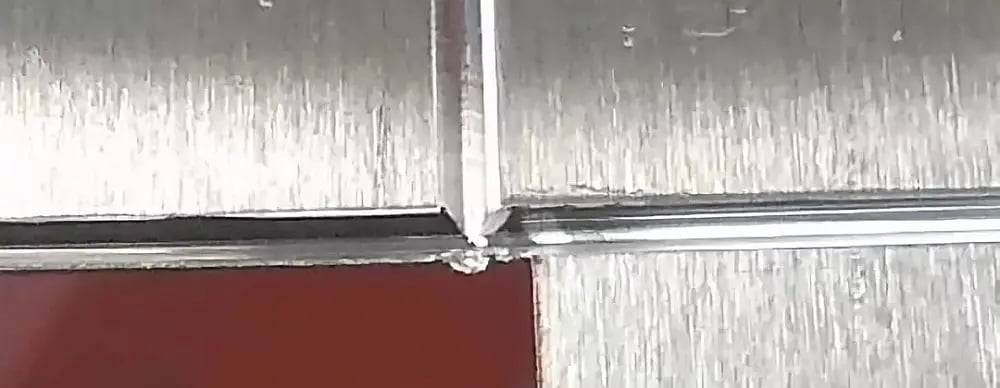
Die Einstellung des Einstechwinkels
Aus dem Biegeprozess ist bekannt, dass Bleche beim Biegen eine unterschiedlich starke Rückfederung erfahren und es dadurch zu Abweichungen im Biegewinkel kommt.
Der V-Nut-Prozess kann ordnungsgemäß durchgeführt werden, indem sichergestellt wird, dass der Nutwinkel dem erforderlichen Biegewinkel des Werkstücks entspricht.
Normalerweise ist der V-Nut-Winkel 1–2° größer als der Biegewinkel.
Wenn Sie beispielsweise ein Werkstück in einem Winkel von 90° biegen, kann der V-Nutwinkel auf 92° eingestellt werden (siehe Abbildung 4).
Auf diese Weise kann der durch die Rückfederung beim Biegen verursachte Winkelfehler wirksam behoben werden (siehe Abbildung 5).
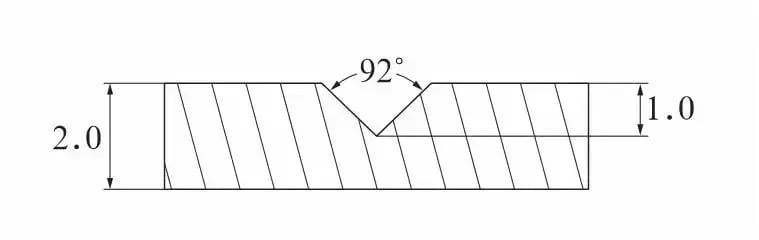
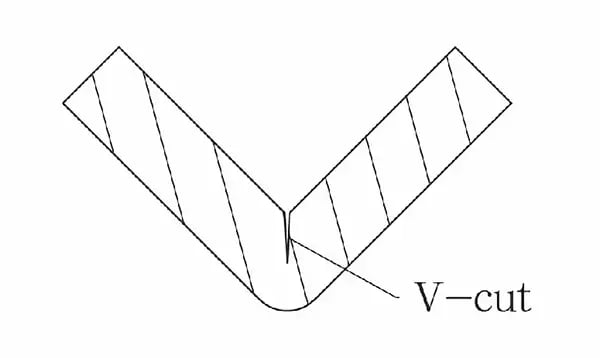
Auswahl der Nutmesser und Mengeneinstellung
Die Nutmesser Typen und Auswahl
Bei den Nutmessertypen unterscheidet man im Wesentlichen zwischen rhombischen Nutmessern mit oberem Winkel, quadratischen Nutmessern, dreieckigen Nutmessern und kreisförmigen Nutmessern (siehe Abbildung 6).
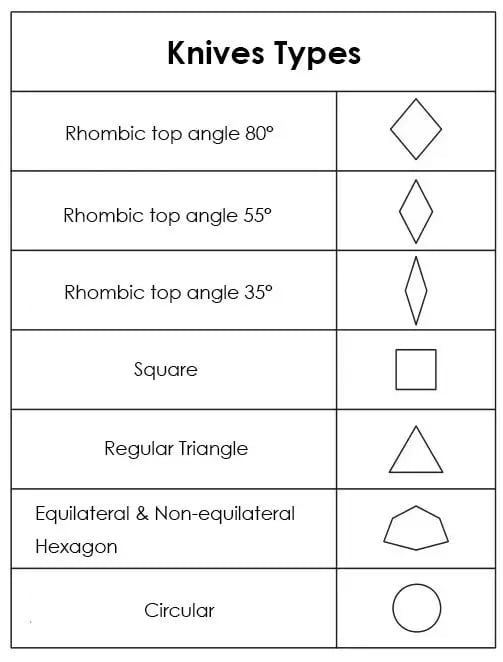
Anhand der Form und des Winkels der V-Nut können geeignete Messer ausgewählt werden.
Beim Formen einer Standard-V-Nut sollte der Winkel der Messer kleiner sein als der Winkel des V-Schlitzes.
Liegt der V-Nut-Winkel beispielsweise zwischen 45° und 60°, sollten Rautenmesser mit einem Spitzenwinkel von 35° verwendet werden.
Für V-Nuten zwischen 60° und 80° sind Dreiecksnutmesser die bevorzugte Wahl.
Beim V-Nuten zwischen 80° und 90° sollten Rautenmesser mit einem Spitzenwinkel von 80° verwendet werden.
Wenn der V-Nutwinkel größer als 90° ist, sind quadratische Messer die empfohlene Wahl.
Darüber hinaus sollten zum Einstechen runder Formen Kreismesser verwendet werden.
Die Einstellung der Messeranzahl
Beim Nuten langer Bleche mit großer Tiefe kann die kontinuierliche Verwendung nur eines Messers zu Schäden durch übermäßige Hitze führen. Dies kann auch zu schlechter Nutqualität, vermehrten Metallgraten und anderen Problemen führen.
Wenn Sie beispielsweise eine 2 m lange Edelstahlplatte mit einer Tiefe von 2 mm einstechen, führt das Einstellen der anfänglichen Messervorschubmenge auf 0,5 mm und kontinuierliches Einstechen dazu, dass das Messer viel Wärme erzeugt und weich wird, was nach 1,5 m und einer größeren Gratgröße zu einer verringerten Einstechqualität führt.
Wenn der Messervorschub auf 0,2 mm eingestellt ist, sind 10 Rillenzyklen erforderlich, um das 2 mm dicke Metallblech fertigzustellen, was die Fertigungseffizienz erheblich beeinträchtigt.
Daher ist es beim Nuten längerer Platten wichtig, nicht nur die Messervorschubmenge, sondern auch die Anzahl der gleichzeitig arbeitenden Messer zu berücksichtigen.
Typischerweise werden 3 bis 4 Messer gleichzeitig verwendet (siehe Abbildung 7).
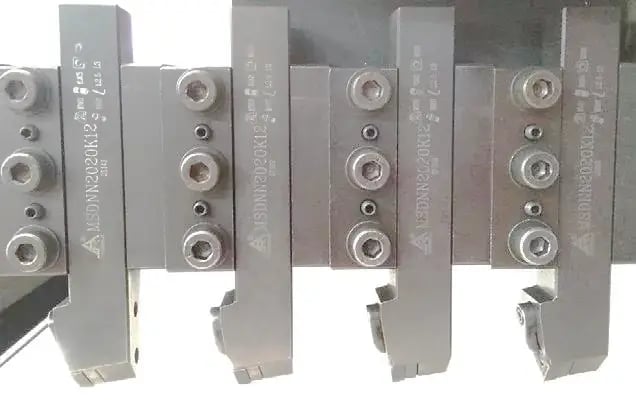
Jedes Messer hat einen leicht unterschiedlichen Vorschub. Wenn beispielsweise der erste Vorschub 5 mm beträgt, betragen der zweite, dritte und vierte Vorschub 7 mm, 9 mm bzw. 11 mm.
Dadurch wird nicht nur die Qualität der Nuten sichergestellt, sondern auch die Arbeitseffizienz verbessert.
So vermeiden Sie Biegewinkel- und Größenabweichungen
Beim Biegeprozess hängt die Qualität der Biegung im Wesentlichen von zwei entscheidenden Parametern ab: dem Biegewinkel und der Größe.
Um genaue Biegemaße und -winkel sicherzustellen, sollten die folgenden Überlegungen berücksichtigt werden:
(1) Wenn Oberstempel und Untermatrize nicht ausgerichtet sind, kommt es zu Fehlern bei der Biegegröße. Um dies zu verhindern, sollten Ober- und Untermatrize vor dem Biegen zentriert werden.
(2) Die relative Position der Platte und des Unterwerkzeugs kann sich ändern, wenn sich der hintere Anschlag nach links oder rechts bewegt, was sich auf die Biegegröße auswirkt. Um dies zu beheben, sollte der Positionsabstand des hinteren Anschlags vor dem Biegen erneut gemessen werden.
(3) Eine fehlende Parallelität zwischen dem Werkstück und dem Unterwerkzeug führt beim Biegen zu einem Rückfedern und hat Auswirkungen auf den Biegewinkel. Die Parallelität sollte vor dem Biegen gemessen und eingestellt werden.
(4) Wenn der Winkel der ersten Biegung nicht ausreicht, wirkt sich dies auf die nachfolgende Biegung aus. Die Anhäufung von Biegefehlern führt zu einer Vergrößerung des Fehlers bei der Formgröße und dem Winkel des Werkstücks. Daher ist es wichtig, die Genauigkeit jeder Biegung sicherzustellen.
(5) Beim Biegen ist die Größe der V-Öffnung im Untergesenk umgekehrt proportional zur Biegekraft. Bei der Bearbeitung von Metallplatten unterschiedlicher Dicke sollte die entsprechende V-Öffnung des Untergesenks gemäß den Vorschriften ausgewählt werden. Normalerweise ist das 6- bis 8-fache der Plattendicke die beste Wahl.
(6) Beim Biegen des Werkstücks auf einer Abkantpresse nach dem V-Nuten muss sichergestellt werden, dass die obere mehrdeutige Kante, die V-förmige Unterkante des Werkstücks und die V-förmige Unterkante des Unterwerkzeugs alle auf derselben vertikalen Oberfläche liegen.
⑺ Beim Biegen des Werkstücks nach dem Nuten sollte der Winkel des oberen Gesenks auf etwa 84° kontrolliert werden, um ein Einklemmen zu vermeiden.
Berechnung der Blechabwicklungslänge
Ich gehe davon aus, dass die meisten von Ihnen bereits mit der Berechnung der Abwicklungslänge vor dem Einstechen vertraut sind.
Aber wissen Sie, wie die Entfaltungslänge nach dem Nuten berechnet wird?
Lassen Sie mich dies anhand eines Beispiels demonstrieren.
Das Bild unten stellt die Abmessungen jeder Kante des Werkstücks dar. Das Blech hat eine Dicke von 3 mm.
Berechnung der Blechabwicklungslänge nach dem Nuten
Biegen nach dem Nuten:
Wenn der Kunde einen kleineren Radius anfordert und die verbleibende Blechdicke 0,5 mm beträgt, beträgt die Abwicklungslänge L = (40-0,5) + (30-2×0,5) + (30-2×0,5) + (10-0,5) = 107 mm.
Direktbiegen ohne Nuten:
Wenn die Biegung ohne Nut erfolgt und ein K-Faktor von 0,25 gewählt wird, beträgt die Entfaltungslänge L = (40-3+0,25) + (30-6+2×0,25) + (30-6+2×0,25) + (10-3+0,25) = 93,5 mm.
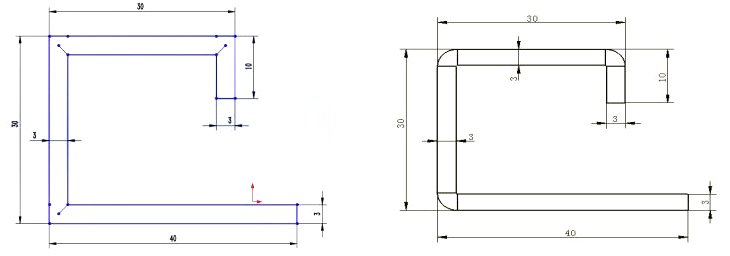
Abschluss
Das Nuten ist eine neue, vom Markt gewählte Biegetechnik.
Für die Herstellung hochwertiger Produkte ist die Beherrschung unterschiedlicher Verarbeitungstechniken unabdingbar.
Für die Herstellung noch besserer Produkte ist die kontinuierliche Erforschung und Einführung neuer Techniken von entscheidender Bedeutung.