Entdecken Sie die feinen Unterschiede zwischen horizontale und vertikale V-Nutmaschinen, unverzichtbare Werkzeuge in der Blechbearbeitung. Dieser Leitfaden befasst sich mit Verarbeitungsbereich, Leistungsverlust, Präzision, Verarbeitungstechnologie, Sicherheitsaspekten und Installationsüberlegungen, damit Sie fundierte Entscheidungen für Ihre spezifischen Anforderungen treffen können.
1. Besondere Merkmale und Fähigkeiten:
1.1 Verarbeitungsbereich:
- Vertikale V-Nutmaschine:
- Verfügt über mehrere Druckplatten und Klemmen, die das automatische Klemmen von Blättern in verschiedenen Größen ermöglichen.
- Verarbeitet Bleche von 3 bis 5 mm Dicke.
- Geeignet für horizontales und vertikales Nutenschneiden von Werkstücken bis zu einer Größe von 80 x 80 mm.
- Horizontale V-Nutmaschine:
- In erster Linie zum Nuten großer, dünner Bleche mit einer Dicke von normalerweise weniger als 3 mm konzipiert.
- Beim Versuch, nach dem Längsrillen eine horizontale Rillung vorzunehmen, kommt es aufgrund der Blechverformung zu Herausforderungen.
1.2 Leistungsverlust:
- Vertikales V-Nutwerkzeug: Bei der Hin- und Herbewegung ist ein Werkzeughalter von ca. 60 kg erforderlich.
- Horizontale V-Nutmaschine: Portal und Werkzeughalter bewegen sich gemeinsam hin und her und wiegen etwa 1.000 kg, wodurch ein zehnmal so hoher Energieverlust entsteht wie beim vertikalen Gegenstück.
1.3 Präzision:
- Vertikale V-Nutmaschine: Der feste Hobel ermöglicht eine präzise Kontrolle innerhalb von 0,02 mm.
- Horizontale V-Nutmaschine: Aufgrund der breiten Plattform ist es schwierig, die Genauigkeit im Bereich von 0,1 mm zu kontrollieren.
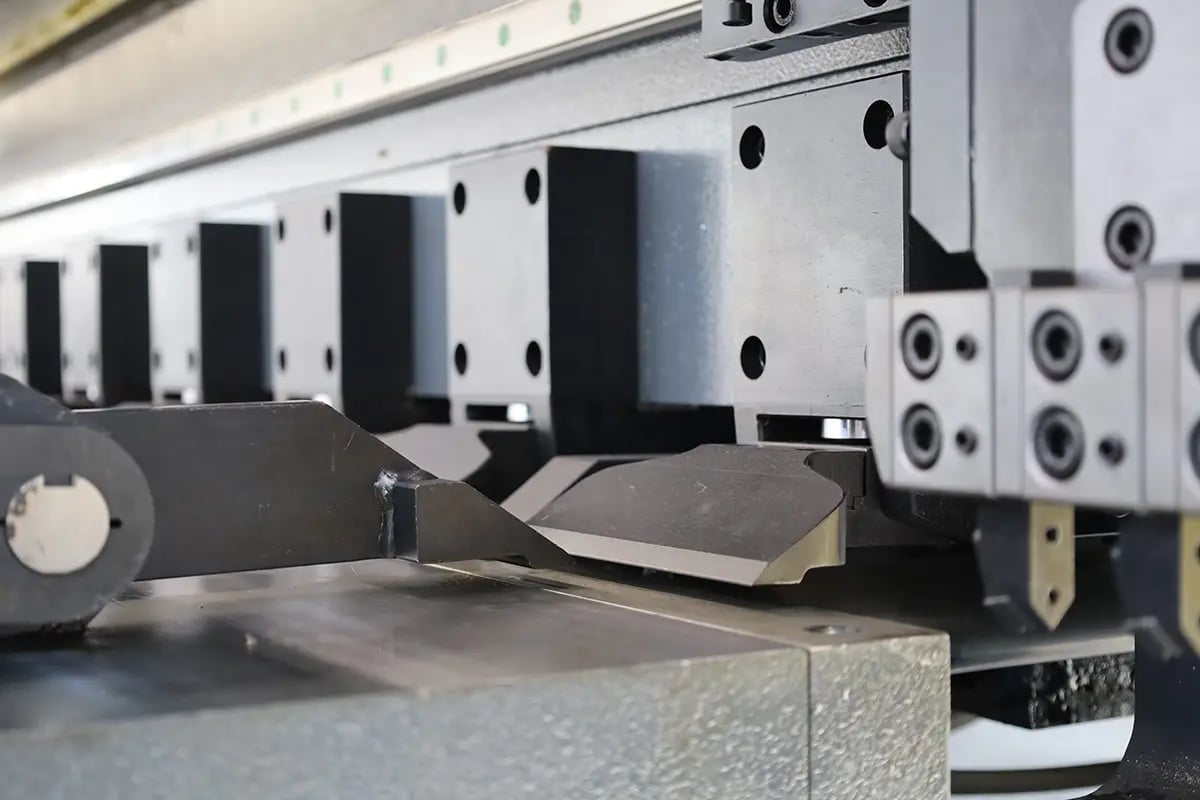
1.4 Verarbeitungstechnologie:
- Vertikale V-Nutmaschine: Verfügt über eine feine bis spiegelnde Oberfläche aus Matrizenstahl.
- Horizontale V-Nutmaschine: Verwendet geschweißte normale Eisenplatten, die beim Nutenschneiden von Edelstahl anfällig für Beschädigungen sind.
1.5 Sicherheit:
- Vertikale V-Nutmaschine: Nutzt hydraulisches automatisches Klemmen, automatisches Positionieren und automatischen Betrieb und erhöht so die Sicherheit des Bedieners.
- Horizontale V-Nutmaschine: Aufgrund des sich schnell bewegenden Portalkrans und der möglichen Nähe des Bedieners zu Maschinenteilen besteht ein Sicherheitsrisiko.
1.6 Installation:
- Vertikale V-Nutmaschine: Durch die Verschweißung mit hochfesten Stahlplatten ist eine Stabilität auf ebenem Betonboden gewährleistet.
- Horizontale V-Nutmaschine: Aufgrund der hohen Aufprallkräfte während des Portalbetriebs ist eine Verstärkung erforderlich.
2. Vorteile der vertikalen V-Nutmaschine:
2.1 Geeignet für Aluminiumplatten:
Bei der horizontalen Platzierung von Aluminiumplatten entstehen häufig unebene Oberflächen. Daher ist die vertikale Maschine praktischer und effektiver.
2.2 Energieeffizienz:
Vertikale V-Groover sparen mehr Energie, wobei der Energieverlust mehr als zehnmal geringer ist als bei horizontalen Gegenstücken.
2.3 Größerer Verarbeitungsbereich:
Vertikale Maschinen sind vielseitiger und können Platten jeder Größe effizienter handhaben als horizontale Maschinen.
2.4 Verbesserter Bearbeitungsprozess:
Die Verwendung von hochwertigem Matrizenstahl für den Arbeitstisch bei Vertikalmaschinen führt zu einem besseren Bearbeitungsprozess.
2.5 Sicherheit:
Bei vertikalen Maschinen sind die Bediener von beweglichen Teilen fern, was im Vergleich zu horizontalen Maschinen eine sicherere Arbeitsumgebung bietet.
Abschließend ist die Wahl zwischen vertikale und horizontale V-Nutmaschinen hängt von den spezifischen Verarbeitungsanforderungen, Sicherheitsaspekten und der gewünschten Präzision ab. Vertikale Maschinen bieten überlegene Vielseitigkeit, Energieeffizienz und Sicherheit und sind daher die bevorzugte Wahl für verschiedene Anwendungen in der Blechverarbeitung. Kunden können fundierte Entscheidungen auf der Grundlage ihrer spezifischen Anforderungen und Prioritäten treffen. Krrass steht bereit, um professionelle Beratung und Dienstleistungen für diejenigen bereitzustellen, die CNC-Nutmaschinen suchen.