Was ist eine hydraulische Presse?
Hydraulische Presse, auch als Ölhydraulikpresse bekannt, ist eine Art Maschine, die mit Hilfe von Flüssigkeitsdruck Metall, Kunststoff, Gummi, Holz, Pulver und andere Produkte verarbeitet. Sie wird häufig in Press- und Pressformprozessen verwendet, wie z. B. Schmieden, Stanzen, Kaltfließpressen, Richten, Biegen, Bördeln, Dünnblechziehen, Pulvermetallurgie, Presspassung usw.
Sein Prinzip beruht auf der Anwendung des Pascalschen Gesetzes durch den Einsatz von Flüssigkeitsdruckübertragungsmaschinen vieler Art. Natürlich richtet sich die Anwendung auch nach dem Bedarf für verschiedene Dinge.
Beispielsweise gibt es je nach Art der Flüssigkeit, die zur Druckübertragung verwendet wird, zwei Kategorien von Hydraulikpressen und Hydraulikpressen. Der von Hydraulikpressen erzeugte Gesamtdruck ist höher und wird häufig zum Schmieden und Stanzen verwendet.
Hydraulische Schmiedepressen werden in zwei Typen unterteilt: hydraulische Gesenkschmiedepressen und hydraulische Freischmiedepressen. Gesenkschmiedepressen verwenden Formen, während Freischmiedepressen keine Formen verwenden. Die erste in China hergestellte 10.000-Tonnen-Hydraulikpresse ist eine Freischmiede-Hydraulikpresse.
Anwendungsbereich
Das hydraulische Umformungsverfahren hat ein breites Anwendungsspektrum in der Automobil-, Luftfahrt-, Raumfahrt- und Rohrleitungsindustrie, hauptsächlich für: runde, rechteckige oder geformte Strukturteile mit unterschiedlichem Querschnitt entlang der Komponentenachse, wie geformte Rohrverbindungen für Autoauspuffsysteme; hohle Rahmen mit nicht-rundem Querschnitt, wie Motorräume, Instrumententafelhalterungen, Karosserierahmen (machen etwa 111–151 t der Masse von Autos aus); hohle wellenartige Teile und komplexe Rohrverbindungen usw.
Die für den hydraulischen Umformungsprozess geeigneten Materialien umfassen Kohlenstoffstahl, Edelstahl, Aluminiumlegierungen, Kupferlegierungen und Nickellegierungen usw. Im Prinzip sind alle für die Kaltumformung geeigneten Materialien auch für den hydraulischen Umformungsprozess geeignet. Hauptsächlich für Fabriken für Autoteile, Elektronikfabriken, Elektrofabriken, Wärmebehandlungsfabriken, Fabriken für Fahrzeugteile, Getriebefabriken und Fabriken für Klimaanlagenteile.
Sicherer Betrieb
- Wer die strukturelle Leistung oder die Betriebsverfahren der Maschine nicht versteht, sollte die Maschine nicht ohne Erlaubnis starten.
- Eine Überholung der Maschine und eine Anpassung der Form sollte während des Arbeitsprozesses nicht notwendig sein.
- Wenn festgestellt wird, dass die Maschine schwerwiegende Öllecks aufweist oder andere Anomalien aufweist (z. B. unzuverlässiger Betrieb, hoher Lärmpegel, Vibrationen usw.), muss sie angehalten werden, um die Ursachen zu analysieren und zu versuchen, sie zu beseitigen. Sie darf nicht im Krankheitsfall wieder in Produktion gehen.
- darf nicht überlastet werden oder den maximal verwendeten Exzenterabstand überschreiten.
- Es ist strengstens verboten, den maximalen Hub des Schiebers zu überschreiten. Die Mindesthöhe des Formschlusses darf nicht weniger als 600 mm betragen.
- Die Erdung elektrischer Geräte muss solide und zuverlässig sein.
- Am Ende jedes Arbeitstages stelle ich den Schieber in die unterste Position.
Wartungssystem
- Als Arbeitsöl wird das verschleißfeste Hydrauliköl Nr. 32 oder 46 empfohlen. Die Öltemperatur sollte zwischen 15 und 60 Grad Celsius liegen.
- Das Öl wird streng gefiltert, bevor es in den Öltank gegeben werden darf.
- Das Arbeitsfluid sollte einmal jährlich ausgetauscht werden. Der erste Austausch sollte innerhalb von drei Monaten erfolgen.
- Der Schieber sollte häufig geschmiert werden, die freiliegende Oberfläche der Säule sollte häufig sauber gehalten werden und vor jeder Arbeit sollte Öl aufgesprüht werden.
- Die maximal zulässige Exzentrizität der konzentrierten Last beträgt 40 mm bei einem Nenndruck von 500 T. Die Exzentrizität ist zu groß, um eine Säulenbelastung oder andere unerwünschte Phänomene zu verursachen.
- Kalibrieren und überprüfen Sie das Manometer alle sechs Monate.
- Wenn die Maschine längere Zeit nicht verwendet wird, sollte die Oberfläche jedes Teils sauber geschrubbt und mit Rostschutzöl beschichtet werden.
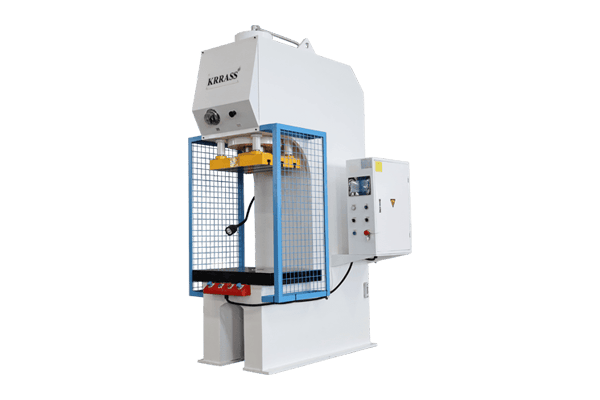
Sekundärwartung
- Werkzeugmaschinen werden 5000 Stunden lang für die sekundäre Wartung betrieben. Wartungspersonal ist das wichtigste, Bedienpersonal ist beteiligt. Neben der Durchführung der Wartungsinhalte der ersten Stufe müssen folgende Arbeiten durchgeführt und Verschleißteile und Ersatzteile zugeordnet werden.
- Für Wartungsarbeiten zunächst die Stromzufuhr unterbrechen.
- Querträgersäulenführung: Überprüfen und justieren Sie die Querträgerebene, die Säulenführung, die Führungsbuchse, den Schieber und die Platte, damit eine reibungslose Bewegung möglich ist und die Prozessanforderungen erfüllt werden. Reparieren oder ersetzen Sie defekte Teile.
- Hydraulikschmierung: zerlegen und reinigen, Magnetventil überholen, Ventil schleifen, Spule. Dann reinigen und prüfen, ob der Kolben des Ölpumpenzylinders leichte Grate aufweist, Öldichtung ersetzen. Dann das Druckmessgerät kalibrieren. Je nach tatsächlicher Situation stark verschleißende Teile reparieren oder ersetzen. Zum Schluss fahren, um den Ölzylinder zu prüfen, ob der Kolben reibungslos läuft, kein Kriechen. Das Stützventil kann den beweglichen Balken an jeder Position genau anhalten lassen und der Druck entspricht den Prozessanforderungen.
- Elektrizität: Reinigen Sie zuerst den Motor, überprüfen Sie die Lager und erneuern Sie das Fett. Reparieren oder ersetzen Sie dann beschädigte Komponenten. Stellen Sie sicher, dass die Elektrik den Anforderungen des Geräteintegritätsstandards entspricht.
- Genauigkeit: Kalibrieren Sie die Maschinenebene und überprüfen und passen Sie die Reparaturgenauigkeit an. Stellen Sie sicher, dass die Genauigkeit den Anforderungen der Geräteintegritätsstandards entspricht.
Die Wartung und Instandhaltung hydraulischer Maschinen erfordert eine engagierte, professionelle Vollzeit-Instandhaltung, damit Sie sie länger nutzen können!
Häufige Fehler
Metallextrusion hydraulische Presse Während des Betriebs fallen manchmal Bolzen ab und fallen in den Hydraulikzylinder an die Kolbenwand, was zu ernsthaften Kratzern führt. Wenn das Problem auftritt, ist eine Reparatur vor Ort mit der herkömmlichen Methode einfach nicht möglich. Es bleibt nur die Möglichkeit, die Bolzen zu zerlegen und zum Hersteller zu transportieren, um sie zu flicken oder durch Schrott zu ersetzen.
Da es keine Ersatzteile zum Austauschen gibt, lässt sich die Zeit für die Neuproduktion von Teilen oder die Rücksendung an das Werk zur Reparatur nicht kontrollieren. Die langen Ausfallzeiten verursachen dem Unternehmen erhebliche wirtschaftliche Verluste und verursachen zudem hohe Bearbeitungs- oder Reparaturkosten. Um den Anforderungen einer kontinuierlichen Produktion gerecht zu werden, müssen bequeme, einfache und effektive Wartungsmethoden gefunden werden, um das Geräteproblem zu lösen, Ausfallzeiten zu minimieren und Reparatur- und Wartungskosten zu senken. Für die Reparatur vor Ort kann die Polymerverbundmethode verwendet werden.
Bedienungsschritte
- Durch Brennen mit einer Acetylen-Sauerstoff-Flamme werden die Teile zerkratzt (die Temperatur muss kontrolliert werden, um ein Ausglühen der Oberfläche zu vermeiden). Das aus der Metalloberfläche austretende Öl wird ausgebacken und so gebacken, dass keine Funken entstehen.
- Oberflächenbearbeitung des zerkratzten Teils mit Winkelschleifer, Schleiftiefe mehr als 1 mm, und entlang der Außenwand des Zylinderlaufs Schleifnut, vorzugsweise Schwalbenschwanznut. Bohren Sie an beiden Enden des Kratzers tiefer, um die Kraft zu ändern.
- Reinigen Sie die Oberfläche mit in Aceton oder wasserfreiem Ethanol getauchter Fettentfernungswatte.
- Tragen Sie das gemischte Reparaturmaterial auf die zerkratzte Oberfläche auf. Die erste Schicht sollte dünn und gleichmäßig sein und die gesamte zerkratzte Oberfläche bedecken, um eine optimale Bindung zwischen dem Material und der Metalloberfläche sicherzustellen. Tragen Sie das Material anschließend auf die gesamte Reparaturstelle auf und drücken Sie wiederholt darauf, um sicherzustellen, dass das Material ausgefüllt ist und die erforderliche Dicke erreicht, sodass es etwas höher ist als die Oberfläche der Außenwand des Zylinders.
- Bei 24 °C dauert es 24 Stunden, bis das Material alle Eigenschaften erreicht. Um Zeit zu sparen, können Sie die Temperatur mit einer Wolfram-Halogenlampe erhöhen. Bei jeder Temperaturerhöhung um 11 °C verkürzt sich die Aushärtungszeit um die Hälfte. Die beste Aushärtungstemperatur beträgt 70 °C.
- Nachdem das Material ausgehärtet ist, verwenden Sie einen feinen Schleifstein oder Schaber, um das Material, das über die Oberfläche der Außenwand des Zylinders hinausgeht, zu reparieren. Die Konstruktion ist fertig.