Inhaltsverzeichnis
Definition
A Ausklinkmaschinen, auch Kerber genannt, ist eine Werkzeugmaschine, die in der Metallbearbeitung zum Herstellen von Kerben, Schlitzen oder Rillen in Metallwerkstücken verwendet wird. Kerbmaschinen werden häufig in verschiedenen Branchen wie Fertigung, Bauwesen, Automobilbau und Metallverarbeitung eingesetzt.
Die Hauptfunktion einer Kerbmaschine besteht darin, Material von der Kante oder Oberfläche eines Metallwerkstücks zu schneiden oder zu entfernen, um eine Kerbe oder einen Schlitz zu erzeugen. Dieser Prozess ermöglicht die Erstellung präziser Formen und Winkel, die häufig bei der Herstellung von Metallkomponenten und -strukturen erforderlich sind.
Kerbmaschinen können je nach Komplexität des Werkstücks und gewünschtem Präzisionsgrad manuell, hydraulisch oder mithilfe von CNC-Technologie (Computer Numerical Control) betrieben werden. Es gibt sie in verschiedenen Typen und Konfigurationen, darunter manuelle Kerbmaschinen, hydraulische Kerbmaschinen und automatische CNC-Kerbmaschinen.
Anwendungen
Einige gängige Anwendungen von Ausklinkmaschinen enthalten:
Herstellung von Metallrahmen und -konstruktionen: Kerbschneider werden zum Kerben von Metallrohren, Leitungen und Profilen für die Montage von Rahmen, Strukturen und Gerüsten im Bauwesen und in der Fertigung verwendet.
Herstellung von Metallhalterungen und Beschlägen: Kerbschneider werden zum Anbringen präziser Kerben und Ausschnitte in Metallklammern, Beschlägen und Hardware für verschiedene Anwendungsbereiche eingesetzt.
Blechbearbeitung: Kerbmaschinen werden zum Kerben und Schneiden von Blechtafeln und -platten verwendet, um Verbindungen, Laschen und Flansche in Blechkomponenten und -baugruppen zu erzeugen.
Automobil- und Luftfahrtindustrie: Kerbschneider werden bei der Herstellung von Fahrzeugchassis, Flugzeugrahmen und anderen Spezialkomponenten verwendet, die präzise Kerben und Ausschnitte erfordern.
Funktionsprinzip
Das Funktionsprinzip einer Kerbmaschine besteht darin, Material von der Kante oder Oberfläche eines Metallwerkstücks zu schneiden oder zu entfernen, um Kerben, Schlitze oder Rillen zu erzeugen. Hier ist eine detaillierte Erklärung des Funktionsprinzips einer typischen Kerbmaschine:
Einspannen des Werkstückes: Das zu klinkende Metallwerkstück wird fest auf dem Arbeitstisch oder der Vorrichtung der Maschine eingespannt. Dies sorgt für Stabilität und verhindert Bewegungen während des Klinkvorgangs.
Positionierung und Ausrichtung: Der Bediener positioniert das Werkstück so, dass es mit dem Schneidmechanismus der Kerbmaschine ausgerichtet ist. Eine präzise Positionierung ist unerlässlich, um eine genaue Kerbung gemäß den erforderlichen Spezifikationen sicherzustellen.
Auswahl des Ausklinkwerkzeugs: Je nach Ausführung und Anforderungen der Kerbe wird das entsprechende Kerbwerkzeug ausgewählt. Kerbwerkzeuge gibt es in verschiedenen Formen und Größen, darunter Stempel, Matrizen, Schaftfräser und Sägeblätter, je nach Art der Kerbmaschine und dem zu schneidenden Material.
Schneidvorgang starten: Der Bediener aktiviert die Kerben und löst damit den Schneidmechanismus aus, der in das Werkstück eingreift. Das Schneidwerkzeug bewegt sich auf das Werkstück zu, gesteuert durch das Steuerungssystem der Maschine oder durch die Eingabe des Bedieners.
Materialabtrag: Wenn das Schneidwerkzeug in das Werkstück eingreift, entfernt es Material von der Kante oder Oberfläche, um die gewünschte Kerbe oder den gewünschten Schlitz zu erzeugen. Der Schneidvorgang kann je nach Art der Kerbmaschine und dem zu verarbeitenden Material Scheren, Fräsen, Schleifen oder andere Bearbeitungsprozesse umfassen.
Kontrollierte Vorschubgeschwindigkeit: Die Vorschubgeschwindigkeit des Schneidwerkzeugs wird sorgfältig kontrolliert, um einen gleichmäßigen und präzisen Materialabtrag zu gewährleisten. Dies hilft, Werkzeugverschleiß zu vermeiden, die Schnittgenauigkeit aufrechtzuerhalten und gleichmäßige Ergebnisse am gesamten Werkstück zu erzielen.
Wiederholbarer Prozess: Bei mehreren Kerben oder Schlitzen am selben Werkstück wird der Schneidvorgang nach Bedarf wiederholt. Der Bediener kann die Maschineneinstellungen anpassen oder das Werkstück neu positionieren, um zusätzliche Kerben gemäß den erforderlichen Spezifikationen zu erstellen.
Endbearbeitung und Kontrolle: Sobald der Kerbvorgang abgeschlossen ist, wird das Werkstück auf Qualität und Genauigkeit geprüft. Eventuelle Nachbearbeitungsvorgänge wie Entgraten oder Anfasen können durchgeführt werden, um scharfe Kanten zu entfernen und die Oberflächenglätte zu verbessern.
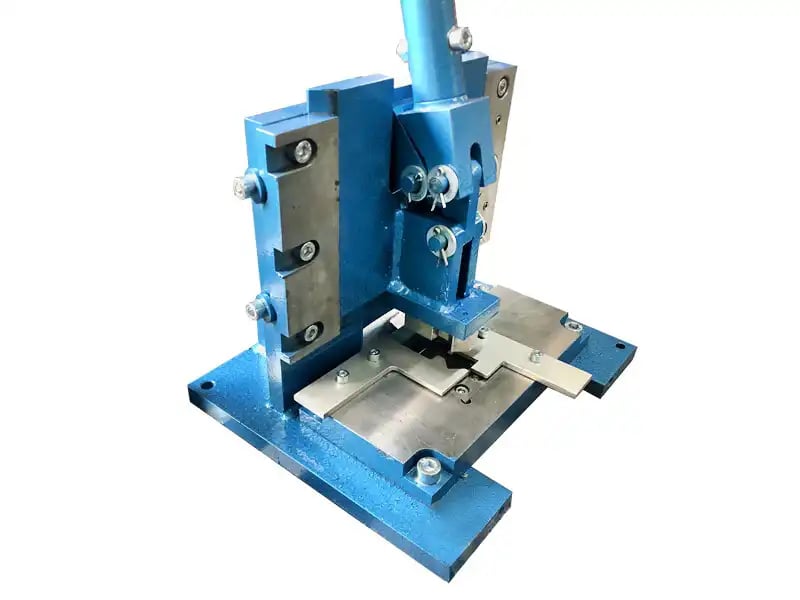
Arten von Kerbmaschinen
Manueller Typ:
Manuelle Kerbmaschinen werden von Hand bedient und erfordern, dass der Bediener das Werkstück manuell in den Schneidmechanismus einführt. Diese Maschinen werden typischerweise für die Produktion kleiner Stückzahlen oder für gelegentliche Kerbarbeiten verwendet.
Hydrauliktyp:
Hydraulische Kerbmaschinen nutzen Hydraulikkraft zum Antrieb des Schneidmechanismus. Sie bieten im Vergleich zu manuellen Maschinen eine höhere Schneidkraft und Präzision und sind daher für die Produktion mittlerer bis großer Stückzahlen und anspruchsvollere Kerbanwendungen geeignet.
CNC Typ:
CNC-Kerbmaschinen (Computer Numerical Control) sind automatisierte Systeme, die durch Computerprogramme gesteuert werden. Sie verfügen über programmierbare Schnittparameter und präzise Positionierung, was hochpräzise und wiederholbare Kerbvorgänge ermöglicht. CNC-Kerbmaschinen sind ideal für die Produktion großer Stückzahlen und komplexe Kerbaufgaben.
Schleifmitteltyp:
Schleifkerbmaschinen verwenden Schleifscheiben oder -räder, um Material vom Werkstück zu entfernen. Sie werden häufig zum Kerben von dicken oder harten Materialien wie Stahl, Edelstahl und Aluminium verwendet. Schleifkerbmaschinen eignen sich für Anwendungen, bei denen hohe Schnittgeschwindigkeiten und Effizienz erforderlich sind.
Schaftfräsertyp:
Schaftfräsmaschinen verwenden rotierende Schaftfräser, um Kerben oder Schlitze in das Werkstück zu schneiden. Es sind vielseitige Maschinen, mit denen sich präzise Kerben in verschiedenen Materialien, darunter Metalle, Kunststoffe und Verbundwerkstoffe, erzeugen lassen. Schaftfräsmaschinen werden häufig in Bearbeitungs- und Fertigungswerkstätten für eine Vielzahl von Anwendungen eingesetzt.
Stanzart:
Stanzkerben verwenden Stanz- und Matrizensätze, um Löcher zu stanzen oder Kerben in das Werkstück zu erzeugen. Sie werden häufig in der Blechbearbeitung verwendet, um Kerben, Lamellen und andere Merkmale in Blechkomponenten zu erzeugen. Stanzkerbenmaschinen bieten Hochgeschwindigkeitsbetrieb und können eine Vielzahl von Materialien und Dicken verarbeiten.
Dies sind nur einige Beispiele für die auf dem Markt erhältlichen Typen von Kerbmaschinen. Die Wahl des am besten geeigneten Typs hängt von Faktoren wie der spezifischen Anwendung, der Materialart und -dicke, dem Produktionsvolumen und dem erforderlichen Grad an Präzision und Automatisierung ab.
Zusammenfassung
Kerbmaschinen spielen in der Metallbearbeitung und bei Fertigungsprozessen eine entscheidende Rolle, da sie die Herstellung komplexer Formen und Profile in Metallwerkstücken für ein breites Anwendungsspektrum in unterschiedlichsten Branchen ermöglichen.