Inhaltsverzeichnis
Entwicklung des Laserschneidens
Die Entwicklung der Laserschneidtechnologie war ein bedeutender Fortschritt in den Herstellungs- und Fertigungsprozessen. Hier ist ein kurzer Überblick über die wichtigsten Phasen in der Entwicklung von Laserschneiden:
Erfindung des Lasers (1960er Jahre): Das Konzept des Lasers (Light Amplification by Stimulated Emission of Radiation, Lichtverstärkung durch stimulierte Emission von Strahlung) wurde erstmals in den 1950er Jahren von Wissenschaftlern vorgeschlagen und der erste funktionsfähige Laser wurde 1960 entwickelt. Diese bahnbrechende Erfindung ebnete den Weg für zahlreiche Anwendungen, darunter auch das Laserschneiden.
Frühe Experimente (1960er-1970er Jahre): In den Anfangsjahren der Lasertechnologie führten Forscher Experimente durch, um ihre möglichen Anwendungen zu erkunden. Bei den ersten Laserschneidversuchen wurden CO2-Laser zum Schneiden von Materialien wie Metallen, Kunststoffen und Stoffen verwendet.
Industrielle Einführung (1980er Jahre): In den 1980er Jahren führten Fortschritte in der Lasertechnologie zur Kommerzialisierung von Laserschneidsystemen für industrielle Anwendungen. CO2-Laser erwiesen sich als bevorzugte Wahl für das industrielle Laserschneiden, da sie eine breite Palette von Materialien mit hoher Präzision und Effizienz schneiden konnten.
Fortschritte in der Lasertechnologie (1990er-2000er Jahre): In den 1990er und 2000er Jahren wurden in der Lasertechnologie bedeutende Fortschritte erzielt, die zu Verbesserungen bei Schnittgeschwindigkeit, Genauigkeit und Vielseitigkeit führten. Faserlaser, die optische Fasern zur Erzeugung von Laserstrahlen verwenden, entwickelten sich als Alternative zu CO2-Lasern und bieten Vorteile wie höhere Schnittgeschwindigkeiten und niedrigere Betriebskosten.
Integration von CNC-Technologie: Die Integration der CNC-Technologie (Computerized Numerical Control) in Laserschneidsysteme revolutionierte die Branche. CNC-Steuerungen ermöglichten eine präzise Kontrolle des Schneidevorgangs, sodass komplexe Formen und Designs problemlos geschnitten werden konnten.
Diversifizierung der Anwendungen: Mit der Weiterentwicklung der Laserschneidtechnologie wurden ihre Anwendungsgebiete vielfältiger und erstreckten sich über verschiedene Branchen, darunter Automobilbau, Luft- und Raumfahrt, Elektronik, Medizintechnik und Architekturdesign. In diesen Branchen entwickelte sich das Laserschneiden zur bevorzugten Methode zum Schneiden komplexer Muster, Konturen und Prototypen.
Fortschritte in der Automatisierung und Robotik: In den letzten Jahren gab es einen Trend zur Automatisierung und Integration von Robotern in Laserschneidsysteme. Automatisiertes Materialhandling, Teilesortierung und robotergestütztes Be- und Entladen haben die Produktivität und Effizienz bei Laserschneidvorgängen weiter verbessert.
Neue Trends: Auch in Zukunft werden laufende Forschungs- und Entwicklungsanstrengungen die Innovation in der Laserschneidtechnologie vorantreiben. Zu den neuen Trends zählen die Entwicklung hybrider Laserschneidsysteme, additive Fertigung mittels Laserabscheidung und Fortschritte bei Laserquellen und Optiken für eine verbesserte Schneidleistung.
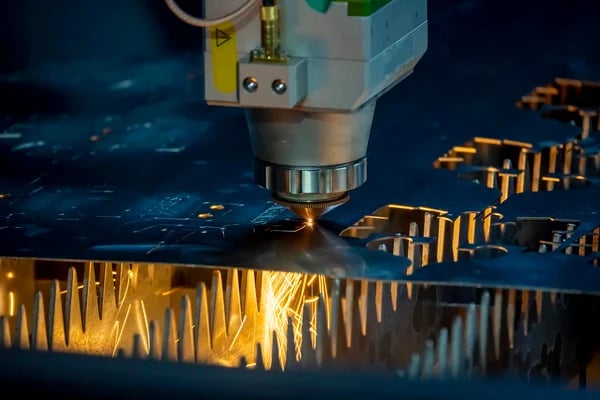
Was ist Laserschneiden und wie funktioniert es?
Laserschneiden verwendet einen Hochleistungslaser, der durch Optik und computergestützte numerische Steuerung (CNC) geleitet wird, um den Strahl oder das Material zu lenken. Normalerweise verwendet der Prozess ein Bewegungssteuerungssystem, um einem CNC- oder G-Code des Musters zu folgen, das in das Material geschnitten werden soll. Der fokussierte Laserstrahl brennt, schmilzt, verdampft oder wird von einem Gasstrahl weggeblasen, um eine hochwertige Oberflächenkante zu hinterlassen.
Der Laserstrahl wird durch die Stimulation von Lasermaterialien durch elektrische Entladungen oder Lampen in einem geschlossenen Behälter erzeugt. Das Lasermaterial wird verstärkt, indem es intern über einen Teilspiegel reflektiert wird, bis seine Energie ausreicht, um als Strom kohärenten monochromatischen Lichts auszutreten. Dieses Licht wird durch Spiegel oder Glasfasern auf den Arbeitsbereich fokussiert, die den Strahl durch eine Linse leiten, die ihn verstärkt.
An seiner schmalsten Stelle beträgt der Durchmesser eines Laserstrahls typischerweise weniger als 0,0125 Zoll (0,32 mm), je nach Materialstärke sind jedoch auch Schnittbreiten von nur 0,004 Zoll (0,10 mm) möglich.
Wenn der Laserschneidvorgang an einer anderen Stelle als an der Materialkante beginnen muss, wird ein Stechverfahren verwendet, bei dem ein gepulster Hochleistungslaser ein Loch in das Material bohrt. Beispielsweise benötigt er 5 bis 15 Sekunden, um ein 0,5 Zoll (13 mm) dickes Edelstahlblech zu durchbrennen.
Beim Laserschneiden wird ein Hochleistungslaser verwendet, der durch Optiken und eine CNC-Steuerung (Computerized Numerical Control) geleitet wird, um den Strahl oder das Material zu lenken. Normalerweise wird bei diesem Verfahren ein Bewegungssteuerungssystem verwendet, um einem CNC- oder G-Code des Musters zu folgen, das in das Material geschnitten werden soll. Der fokussierte Laserstrahl brennt, schmilzt, verdampft oder wird von einem Gasstrahl weggeblasen, um eine hochwertige Oberflächenkante zu hinterlassen.
Der Laserstrahl wird durch die Stimulation von Lasermaterialien durch elektrische Entladungen oder Lampen in einem geschlossenen Behälter erzeugt. Das Lasermaterial wird verstärkt, indem es intern über einen Teilspiegel reflektiert wird, bis seine Energie ausreicht, um als Strom kohärenten monochromatischen Lichts auszutreten. Dieses Licht wird durch Spiegel oder Glasfasern auf den Arbeitsbereich fokussiert, die den Strahl durch eine Linse leiten, die ihn verstärkt.
An seiner schmalsten Stelle beträgt der Durchmesser eines Laserstrahls typischerweise weniger als 0,0125 Zoll (0,32 mm), je nach Materialstärke sind jedoch auch Schnittbreiten von nur 0,004 Zoll (0,10 mm) möglich.
Wenn der Laserschneidvorgang an einer anderen Stelle als an der Materialkante beginnen muss, wird ein Stechverfahren verwendet, bei dem ein gepulster Hochleistungslaser ein Loch in das Material bohrt. Beispielsweise benötigt er 5 bis 15 Sekunden, um ein 0,5 Zoll (13 mm) dickes Edelstahlblech zu durchbrennen.
Art des Laserschneidens
Dieser Prozess kann in drei Haupttechniken unterteilt werden – CO2-Laser (zum Schneiden, Bohren und Gravieren) sowie Neodym (Nd) und Neodym-Yttrium-Aluminium-Granat (Nd:YAG), die im Stil identisch sind, wobei Nd für energiereiches Bohren mit geringer Wiederholungszahl und Nd:YAG für Bohren und Gravieren mit sehr hoher Leistung verwendet wird.
Zum Schweißen können alle Lasertypen verwendet werden.
Bei CO2-Lasern wird Strom durch ein Gasgemisch geleitet (DC-angeregt) oder, was heutzutage beliebter ist, wird die neuere Technik der Hochfrequenzenergie (RF-angeregt) verwendet. Die RF-Methode verfügt über externe Elektroden und vermeidet dadurch Probleme im Zusammenhang mit Elektrodenerosion und Beschichtung des Elektrodenmaterials auf Glaswaren und Optiken, die bei DC auftreten können, bei dem eine Elektrode innerhalb des Hohlraums verwendet wird.
Ein weiterer Faktor, der die Laserleistung beeinflussen kann, ist die Art des Gasflusses. Zu den gängigen Varianten des CO2-Lasers gehören schneller Axialfluss, langsamer Axialfluss, Querfluss und Plattenlaser. Beim schnellen Axialfluss wird eine Mischung aus Kohlendioxid, Helium und Stickstoff verwendet, die von einer Turbine oder einem Gebläse mit hoher Geschwindigkeit zirkuliert wird. Querflusslaser verwenden ein einfaches Gebläse, um die Gasmischung mit niedrigerer Geschwindigkeit zirkulieren zu lassen, während Platten- oder Diffusionsresonatoren ein statisches Gasfeld verwenden, das weder Druck noch Glaswaren erfordert.
Je nach Systemgröße und -konfiguration werden auch unterschiedliche Techniken zum Kühlen des Lasergenerators und der externen Optik verwendet. Abwärme kann direkt an die Luft abgegeben werden, üblicherweise wird jedoch ein Kühlmittel verwendet. Wasser ist ein häufig verwendetes Kühlmittel, das oft durch ein Wärmeübertragungs- oder Kühlsystem zirkuliert.
Ein Beispiel für wassergekühlte Laserbearbeitung ist ein Lasermikrostrahlsystem, das einen gepulsten Laserstrahl mit einem Niederdruckwasserstrahl verbindet, um den Strahl auf die gleiche Weise wie eine Glasfaser zu führen. Das Wasser bietet außerdem den Vorteil, dass es Ablagerungen entfernt und das Material kühlt, während andere Vorteile gegenüber dem „trockenen“ Laserschneiden hohe Schneidgeschwindigkeiten, parallele Schnittfugen und omnidirektionales Schneiden sind.
Auch in der Metallschneideindustrie erfreuen sich Faserlaser zunehmender Beliebtheit. Bei dieser Technologie wird ein festes Verstärkungsmedium anstelle einer Flüssigkeit oder eines Gases verwendet. Der Laser wird in einer Glasfaser verstärkt, um eine weitaus kleinere Punktgröße zu erzeugen als bei CO2-Techniken. Dadurch eignet sich diese Technologie ideal zum Schneiden reflektierender Metalle.
Zu den Vorteilen des Laserschneidens gehören:
Präzision: Das Laserschneiden bietet ein hohes Maß an Genauigkeit und Wiederholbarkeit und eignet sich daher ideal für die Herstellung komplizierter und komplexer Formen mit engen Toleranzen.
Vielseitigkeit: Laserschneiden kann für eine Vielzahl von Materialien verwendet werden, darunter Metalle, Kunststoffe, Holz und mehr.
Geschwindigkeit: Das Laserschneiden ist ein schneller und effizienter Prozess, der eine rasche Herstellung von Teilen und Komponenten ermöglicht.
Minimaler Materialabfall: Beim Laserschneiden entstehen schmale Schnitte, was zu minimalem Materialabfall und höherer Materialausnutzung führt.
Saubere Kanten: Durch Laserschneiden entstehen saubere, glatte Kanten, ohne dass sekundäre Endbearbeitungsprozesse erforderlich sind.
Berührungsloses Schneiden: Da der Laserstrahl das Material nicht physisch berührt, besteht nur ein minimales Risiko einer Beschädigung oder Verformung des Werkstücks.
Automatisierung: Laserschneidsysteme können zur Steigerung der Produktivität und Effizienz problemlos in Automatisierung und Robotik integriert werden.