In der modernen Fertigungs- und Produktionslandschaft ist das Erreichen von Präzision und Effizienz nicht verhandelbar. Die Auswahl der geeigneten Schneidtechnologie spielt eine entscheidende Rolle bei der Bestimmung der Qualität und Kosteneffizienz Ihrer Produktionskapazitäten. Zu den verfügbaren Optionen gehören CNC-Faserlaserschneiden und Wasserstrahlschneiden kristallisieren sich als starke Konkurrenten heraus, die jeweils unterschiedliche Vorteile und Fähigkeiten bieten. In diesem Blogbeitrag führen wir eine vergleichende Analyse dieser Technologien durch, um Ihnen die notwendigen Erkenntnisse zu vermitteln, damit Sie eine fundierte Entscheidung treffen können, die auf Ihre spezifischen Anforderungen zugeschnitten ist.
Inhaltsverzeichnis
Unterschiede zwischen Wasserstrahlen und Faserlasern
Verstehen Sie die Unterschiede zwischen Wasserstrahlen und Faserlaser ist für fundierte Entscheidungen bei Fertigungs- und Schneidanwendungen unerlässlich. Wasserstrahlen basieren auf einem Hochdruckwasserstrahl, der manchmal mit Schleifpartikeln vermischt ist, um Materialien abzutragen und zu schneiden, was sie bemerkenswert vielseitig und ideal für hitzeempfindliche Substanzen macht. CNC-Faserlaser hingegen verwenden einen Hochleistungslaserstrahl, um Materialien mit außergewöhnlicher Präzision zu schmelzen oder zu verdampfen, was besonders für Metalle geeignet ist. Die Wahl zwischen diesen Technologien hängt von einer Reihe von Faktoren ab, darunter Materialart, Dicke, Präzisionsanforderungen, Geschwindigkeit, Hitzeempfindlichkeit, Umweltaspekte und Wartungskosten. Eine sorgfältige Bewertung dieser Faktoren hilft sicherzustellen, dass die ausgewählte Schneidmethode den Anforderungen Ihrer Produktion entspricht.
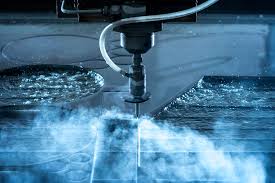
Vorteile des Wasserstrahlschneidens:
Vielseitigkeit: Wasserstrahlschneidemaschinen können eine Vielzahl von Materialien schneiden, darunter Metalle, Kunststoffe, Verbundwerkstoffe, Stein, Glas, Keramik und sogar Lebensmittel. Wasserstrahlen eignen sich für hitzeempfindliche Materialien.
Präzision: Wasserstrahlschneidemaschinen sind für ihre hohe Präzision bekannt, die komplizierte Designs und enge Toleranzen ermöglicht. Sie können präzise Schnitte mit minimalem Materialabfall erzeugen.
Keine Wärmeeinflusszone (WEZ): Da beim Wasserstrahlschneiden keine Wärme entsteht, gibt es keine Wärmeeinflusszone. Dies ist besonders wertvoll bei der Arbeit mit Materialien, die durch Hitzeeinwirkung beeinträchtigt werden können.
Reduzierter Materialabfall: Durch die geringe Schnittbreite beim Wasserstrahlschneiden entsteht nur minimaler Materialabfall, was im Laufe der Zeit zu Kosteneinsparungen führen kann.
Niedriger Geräuschpegel: Beim Wasserstrahlschneiden entsteht ein relativ niedriger Geräuschpegel, was es im Vergleich zu einigen anderen Schneideverfahren benutzerfreundlicher macht.
Keine Notwendigkeit für sekundäre Verarbeitung: Durch Wasserstrahlschneiden werden häufig fertige Kanten erzeugt, wodurch die Notwendigkeit sekundärer Endbearbeitungsvorgänge wie Entgraten reduziert wird.
Nachteile des Wasserstrahlschneidens:
Langsamere Schnittgeschwindigkeit: Wasserstrahlschneiden ist im Allgemeinen langsamer als andere Schneideverfahren wie Laserschneiden oder Plasmaschneiden. Dies kann sich auf die Gesamtproduktionsrate und -kosten auswirken.
Betriebskosten: Die beim Wasserstrahlschneiden verwendeten Hochdruckpumpen und Schleifmittel führen zu höheren Betriebskosten, einschließlich Wartung und Verbrauchsmaterial.
Abrasive Wasserstrahlen: Wenn dem Wasserstrahl für härtere Materialien abrasive Partikel zugesetzt werden, führt dies mit der Zeit zu Verschleiß am Schneidkopf und der Ausrüstung.
Komplexe Einrichtung: Das Einrichten und Programmieren von Wasserstrahlschneidemaschinen kann komplex sein und erfordert erfahrene Bediener und eine präzise Kalibrierung für optimale Ergebnisse.
Wasserentsorgung: Die Behandlung des beim Schneidprozess entstehenden Abwassers kann besondere Handhabungs- und Entsorgungsverfahren erfordern, was die Betriebskosten erhöht.
Zusammenfassend lässt sich sagen, dass das Wasserstrahlschneiden Präzision und Vielseitigkeit bietet und sich daher für zahlreiche Anwendungen hervorragend eignet, insbesondere wenn es um hitzeempfindliche Materialien oder komplizierte Designs geht. Allerdings kann es hinsichtlich der Schnittgeschwindigkeit und der Betriebskosten Einschränkungen geben. Um festzustellen, ob das Wasserstrahlschneiden für Ihre Produktionsanforderungen die richtige Wahl ist, müssen Sie die jeweilige Anwendung und die Materialien sorgfältig prüfen.
Vor- und Nachteile von Faserlasern
Faserlaser erfreuen sich aufgrund ihrer Präzision und Effizienz in verschiedenen Branchen großer Beliebtheit. Wie jede Technologie haben sie jedoch ihre eigenen Vor- und Nachteile. Hier ist eine Übersicht der wichtigsten Vor- und Nachteile von Faserlasern:
Vorteile von Faserlasern:
Hohe Präzision: Faserlaser bieten außergewöhnliche Präzision und eignen sich daher für Schneid-, Gravur- und Markierungsanwendungen, die komplizierte Designs und enge Toleranzen erfordern.
Geschwindigkeit: Faserlaser sind für ihre hohen Schneid- und Markierungsgeschwindigkeiten bekannt. Sie können die Produktionsraten im Vergleich zu einigen anderen Schneidmethoden deutlich verbessern.
Vielseitigkeit beim Metallschneiden: Faserlaser eignen sich hervorragend zum Schneiden verschiedener Metalle, darunter Stahl, Aluminium und Kupfer. Sie gelten allgemein als die beste Option in der Metallverarbeitungsindustrie.
Minimale Wärmeeinflusszone (WEZ): Faserlaser erzeugen beim Schneidvorgang nur minimale Wärme, was zu einer kleinen Wärmeeinflusszone führt. Dies ist wichtig für Materialien, die sich durch Hitzeeinwirkung verziehen oder verformen können.
Energieeffizienz: Faserlaser sind energieeffizient und verbrauchen im Vergleich zu anderen Lasertypen weniger Strom. Dies führt im Laufe der Zeit zu Kosteneinsparungen.
Langlebigkeit: Faserlaserquellen haben eine lange Betriebslebensdauer und bieten über einen längeren Zeitraum eine gleichbleibende Leistung.
Geringer Wartungsaufwand: Faserlaser erfordern normalerweise nur minimalen Wartungsaufwand, was im Vergleich zu anderen Schneidmethoden zu weniger Ausfallzeiten und geringeren Betriebskosten führt.
Nachteile von Faserlasern:
Anschaffungskosten: Die Anschaffungskosten für ein Faserlasersystem können relativ hoch sein. Für kleinere Unternehmen kann dies eine Eintrittsbarriere darstellen. Mit unseren vielfältigen Finanzierungsmöglichkeiten HierMoore Machine Tools bietet erschwingliche Optionen, die Ihren Anforderungen entsprechen.
Materialbeschränkungen: Faserlaser eignen sich zwar hervorragend zum Schneiden von Metallen, sie sind jedoch bei der Bearbeitung nichtmetallischer Materialien wie Keramik, Glas oder Kunststoff möglicherweise nicht so vielseitig wie andere Schneidverfahren.
Begrenzte Dicke für einige Metalle: Faserlaser können beim Schneiden extrem dicker Metallmaterialien eingeschränkt sein.
Umweltbedenken: Beim Einsatz auf bestimmten Materialien können Faserlaser schädliche Dämpfe und Nebenprodukte erzeugen. Für einen sicheren Betrieb sind daher Absaug- und Filtersysteme erforderlich.
Zusammenfassend lässt sich sagen, dass Faserlaser eine hohe Präzision, Geschwindigkeit und Effizienz bieten und daher für eine Vielzahl von Anwendungen, insbesondere in der Metallverarbeitung, die erste Wahl sind. Allerdings können sie hinsichtlich der Materialvielfalt und der Anschaffungskosten Einschränkungen aufweisen. Um festzustellen, ob Faserlaser für Sie die richtige Wahl sind, ist eine sorgfältige Prüfung der spezifischen Anwendung und der Materialanforderungen unerlässlich.
Vergleich zwischen Wasserstrahlen und Faserlasern
1. Schneidmechanismus:
Wasserstrahlschneiden: Verwendet einen Hochdruckwasserstrahl, der mit Schleifpartikeln oder reinem Wasser vermischt wird, um Materialien abzutragen und zu schneiden. Es ist vielseitig und ideal für hitzeempfindliche Materialien.
Faserlaserschneiden: Verwendet einen Hochleistungslaserstrahl, um das zu schneidende Material zu schmelzen oder zu verdampfen. Es ist äußerst präzise und für Metalle und andere Materialien geeignet.
2. Materialverträglichkeit:
Wasserstrahlschneiden: Kompatibel mit einer Vielzahl von Materialien, darunter Metalle, Stein, Glas, Keramik, Kunststoffe und Verbundwerkstoffe. Ideal für wärmeempfindliche Materialien.
Faserlaserschneiden: Wird hauptsächlich für Metalle wie Stahl, Aluminium, Kupfer und einige nichtmetallische Materialien verwendet. Bei nichtmetallischen Materialien ist die Vielseitigkeit geringer.
3. Materialstärke:
Wasserstrahlschneiden: Geeignet für eine große Bandbreite an Materialstärken, von dünn bis zu mehreren Zentimetern, und daher ideal für dicke Materialien.
Faserlaserschneiden: Gut geeignet für dünne bis mitteldicke Materialien, bei extrem dicken Materialien kann es jedoch Einschränkungen geben.
4. Präzision und Toleranz:
Wasserstrahlschneiden: Bietet hohe Präzision, kann aber im Vergleich zu Faserlasern etwas größere Toleranzen aufweisen. Gut geeignet für komplizierte Designs und enge Toleranzen.
Faserlaserschneiden: Bekannt für außergewöhnliche Präzision, ermöglicht das Erreichen sehr enger Toleranzen. Ideal für komplizierte und detaillierte Arbeiten.
5. Geschwindigkeit:
Wasserstrahlschneiden: Im Allgemeinen langsamer als das Faserlaserschneiden, was bei einigen Anwendungen die Produktionsraten beeinträchtigen kann.
Faserlaserschneiden: Bekannt für seine hohe Schneidgeschwindigkeit und Effizienz, daher ideal für Anwendungen, bei denen es auf die Geschwindigkeit ankommt.
6. Wärmeeinflusszone (WEZ):
Wasserstrahlschneiden: Erzeugt keine Hitze, daher entsteht keine Hitzeeinflusszone. Geeignet für hitzeempfindliche Materialien.
Faserlaserschneiden: Obwohl dabei Hitze erzeugt wird, ist die Wärmeeinwirkungszone im Vergleich zu anderen hitzebasierten Schneideverfahren minimal.
7. Geräuschpegel:
Wasserstrahlschneiden: Erzeugt einen relativ niedrigen Geräuschpegel und ist daher bedienerfreundlicher.
Faserlaserschneiden: Kann aufgrund des Laserstrahls lauter sein, in manchen Fällen ist ein Gehörschutz erforderlich.
Hauptfaktoren bei der Wahl von Wasserstrahl- oder Faserlasern
Bei der Entscheidung zwischen Wasserstrahlschneiden und Faserlaserschneiden müssen mehrere Faktoren sorgfältig geprüft werden, um sicherzustellen, dass die ausgewählte Methode Ihren spezifischen Anwendungs- und Produktionsanforderungen entspricht. Hier sind die wichtigsten Faktoren, die bei dieser Entscheidung berücksichtigt werden sollten:
1. Materialtyp:
Überlegen Sie, welche Materialien Sie schneiden oder bearbeiten möchten. Wasserstrahlschneiden ist vielseitig und kann eine breite Palette von Materialien verarbeiten, darunter Metalle, Stein, Glas, Keramik, Kunststoffe und Verbundwerkstoffe. Faserlaserschneiden eignet sich in erster Linie für Metalle (z. B. Stahl, Aluminium, Kupfer), ist aber für nichtmetallische Materialien möglicherweise nicht so vielseitig.
2. Materialstärke:
Die Dicke der Materialien, mit denen Sie arbeiten, ist entscheidend. Wasserstrahlschneiden eignet sich für dünne bis dicke Materialien, auch für Materialien mit einer Dicke von mehreren Zentimetern. Faserlaserschneiden ist ideal für dünne bis mitteldicke Materialien, kann aber bei extrem dicken Materialien Einschränkungen aufweisen.
3. Präzision und Toleranzen:
Überlegen Sie, wie hoch die Präzision und die engen Toleranzen sein müssen, die Sie benötigen. Faserlaserschneiden ist für seine außerordentliche Präzision bekannt und eignet sich ideal für Anwendungen, die komplizierte Designs und feine Details erfordern. Wasserstrahlschneiden ist präzise, kann aber etwas größere Toleranzen aufweisen.
4. Geschwindigkeit und Produktionseffizienz:
Bewerten Sie die Geschwindigkeits- und Effizienzanforderungen für Ihre Produktionsanforderungen. Das Faserlaserschneiden ist schneller und effizienter als das Wasserstrahlschneiden und eignet sich daher für Anwendungen, bei denen Geschwindigkeit entscheidend ist.
5. Wärmeempfindlichkeit:
Stellen Sie fest, ob die Materialien, mit denen Sie arbeiten, hitzeempfindlich sind. Wasserstrahlschneiden erzeugt keine Hitze und ist für hitzeempfindliche Materialien geeignet. Beim Faserlaserschneiden wird zwar nur minimale Hitze erzeugt, es kann aber dennoch eine hitzebeeinflusste Zone geben, was bei manchen Materialien ein Problem darstellen kann.
6. Kantenqualität:
Beurteilen Sie die gewünschte Kantenqualität Ihrer Schnittteile. Faserlaserschneiden liefert in der Regel hochwertige Kantenoberflächen mit minimalen bis keinen Graten. Wasserstrahlschneiden bietet ebenfalls eine gute Kantenqualität, die Ergebnisse können jedoch je nach Material und Schnittparametern variieren.
7. Geräuschpegel:
Berücksichtigen Sie den Geräuschpegel, der bei jeder Methode entsteht, da dieser die Arbeitsumgebung beeinträchtigen kann. Wasserstrahlschneiden erzeugt relativ niedrige Geräuschpegel, während Faserlaserschneiden aufgrund des Laserstrahlbetriebs lauter sein kann und in einigen Fällen möglicherweise einen Gehörschutz erforderlich macht.
8. Erstinvestition:
Bewerten Sie die für jede Technologie erforderliche Anfangsinvestition, einschließlich der Kosten für den Kauf und die Einrichtung der Ausrüstung. Wasserstrahlschneidsysteme können im Vergleich zu Faserlasersystemen geringere Anschaffungskosten haben.
9. Besondere Bewerbungsvoraussetzungen:
Ihre Wahl sollte letztlich auf Ihre spezifischen Anwendungs- und Produktionsanforderungen abgestimmt sein. Faktoren wie die gewünschte Schnittqualität, Materialvielfalt und Teilemengen spielen eine wichtige Rolle bei der Bestimmung der am besten geeigneten Technologie.
Durch sorgfältige Abwägung dieser Faktoren können Sie eine fundierte Entscheidung zwischen Wasserstrahlschneiden und Faserlaserschneiden treffen und sicherstellen, dass die gewählte Methode Ihren individuellen Anforderungen und Einschränkungen entspricht.
Abschluss
Zusammenfassend lässt sich sagen, dass die Wahl zwischen Wasserstrahl- und Faserlaserverfahren bei Schneid- und Bearbeitungsanwendungen letztlich von Ihren individuellen Anforderungen abhängt. Wasserstrahlverfahren bieten Vielseitigkeit, minimale Wärmeentwicklung und Präzision. Faserlaser hingegen bieten außergewöhnliche Geschwindigkeit, höhere Präzision und Kantenqualität. Jede Technologie hat ihre eigenen Vorteile und Einschränkungen, und es ist wichtig, Faktoren wie Materialart, Dicke, Präzisionsanforderungen und Geschwindigkeit sorgfältig zu berücksichtigen. Wir empfehlen Ihnen, sich an ein vertrauenswürdiges Team von Industriemaschinenspezialisten zu wenden, das Sie bei der Auswahl der Maschine unterstützt, die für Ihre spezifischen Produktionsanforderungen am besten geeignet ist.