A Abkantpresse ist eine Werkzeugmaschine, die in der Metallbearbeitung und Fertigung zum Biegen und Formen von Blechen eingesetzt wird. Sie wird häufig bei der Herstellung verschiedener Metallkomponenten und -strukturen eingesetzt. Die Hauptfunktion einer Abkantpresse besteht darin, Kraft auf ein Blechstück auszuüben, um es zu verformen und in einem vorgegebenen Winkel zu biegen.
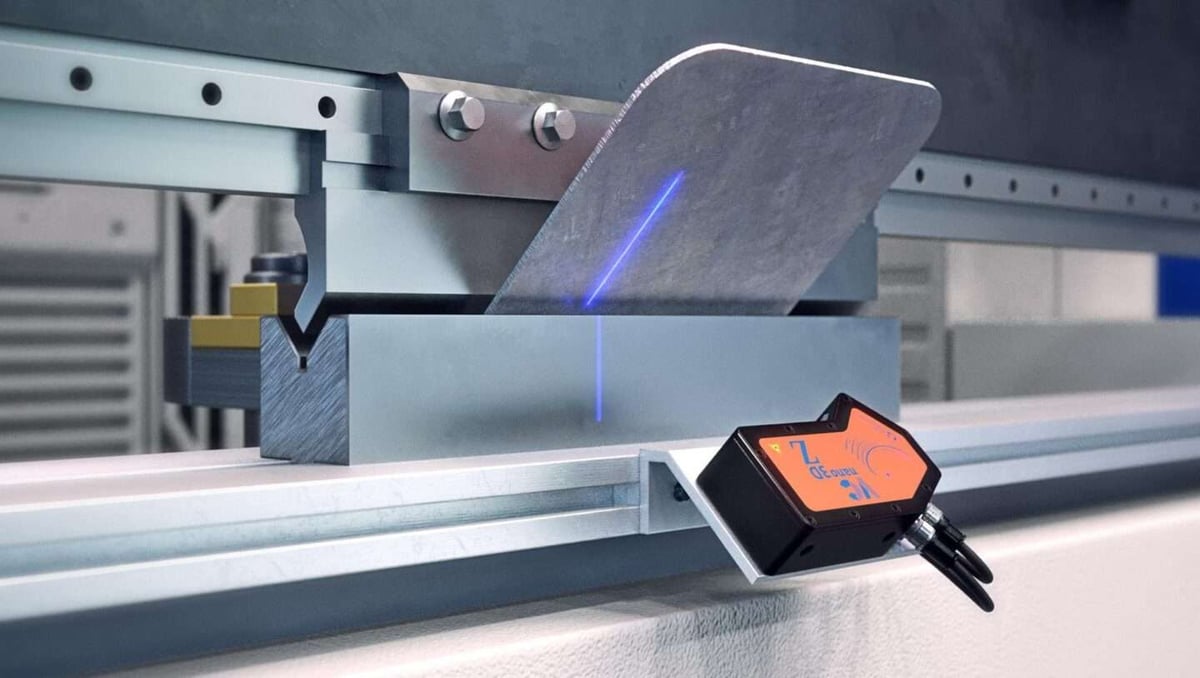
Hier ist ein grundlegender Überblick über die Funktionsweise einer Abkantpresse:
Einrichten: Der Bediener richtet die Abkantpresse ein, indem er die entsprechenden Werkzeuge (wie Matrizen und Stempel) auswählt und die Maschineneinstellungen an die spezifischen Biegeanforderungen anpasst.
Beladung: Ein flaches Blech wird zwischen die beiden Klemmbalken oder -platten der Abkantpresse gelegt.
Klemmen: Der Klemmmechanismus der Maschine hält das Blech sicher an seinem Platz, um eine Bewegung während des Biegevorgangs zu verhindern.
Biegen: Die Abkantpresse übt eine erhebliche Kraft auf das Blech aus, wodurch es je nach gewähltem Winkel und Werkzeugaufbau verformt und gebogen wird.
Entladen: Sobald der Biegevorgang abgeschlossen ist, wird der Klemmmechanismus gelöst und das gebogene Metall aus der Maschine entfernt.
Abkantpressen gibt es in verschiedenen Größen und Leistungsklassen, sodass sie Bleche unterschiedlicher Dicke und Länge bearbeiten können. Sie sind unverzichtbare Werkzeuge in Metallwerkstätten und Produktionsstätten zur Herstellung einer breiten Palette von Komponenten, darunter Halterungen, Gehäuse, Platten und andere Metallteile mit präzisen Biegungen und Formen. Moderne Abkantpressen verfügen häufig über integrierte CNC-Technologie (Computer Numerical Control), um den Biegeprozess mit hoher Präzision und Effizienz zu automatisieren und zu steuern.
Wie wird die Abkantpresse gewartet?
Die ordnungsgemäße Wartung einer Abkantpresse ist entscheidend für ihre Langlebigkeit, Genauigkeit und Sicherheit. Hier sind einige allgemeine Richtlinien zur Wartung einer Abkantpresse:
Regelmäßige Inspektionen:
Führen Sie regelmäßige Sichtprüfungen der Maschine durch, um Anzeichen von Verschleiß, Beschädigung oder losen Komponenten zu erkennen.
Prüfen Sie Hydrauliksysteme auf Lecks, überprüfen Sie Schläuche und tauschen Sie beschädigte oder verschlissene Teile umgehend aus.
Schmierung:
Befolgen Sie die Schmierplanempfehlungen des Herstellers. Schmieren Sie bewegliche Teile, Lager und andere wichtige Komponenten regelmäßig, um Reibung zu reduzieren und Verschleiß vorzubeugen.
Stellen Sie sicher, dass die Schmierstellen sauber und frei von Schmutz sind.
Sauberkeit:
Halten Sie die Abkantpresse und ihre Umgebung sauber. Entfernen Sie regelmäßig Staub, Späne und Schmutz, um zu verhindern, dass diese die Leistung der Maschine beeinträchtigen.
Reinigen und überprüfen Sie die Werkzeuge, da Schmutz und Ablagerungen auf den Werkzeugen zu Unregelmäßigkeiten bei den Biegungen führen können.
Wartung des Hydrauliksystems:
Überprüfen Sie regelmäßig den Stand der Hydraulikflüssigkeit und füllen Sie bei Bedarf Flüssigkeit nach oder ersetzen Sie sie.
Hydraulikschläuche auf Verschleiß, Leckagen oder Beschädigungen prüfen. Beschädigte Schläuche umgehend austauschen.
Hydraulikfilter regelmäßig prüfen und reinigen.
Elektrische Anlage:
Überprüfen Sie elektrische Komponenten auf Anzeichen von Verschleiß, Beschädigung oder losen Verbindungen.
Halten Sie die Schalttafeln sauber und staubfrei.
Werkzeuginspektion:
Überprüfen Sie regelmäßig den Zustand der Werkzeuge, einschließlich Stempel und Matrizen. Ersetzen oder schärfen Sie sie bei Bedarf, um präzise und hochwertige Biegungen zu gewährleisten.
Stellen Sie sicher, dass das Werkzeug richtig ausgerichtet und sicher befestigt ist.
Hinteranschlag und Steuerungssystem:
Wenn Ihr Abkantpresse verfügt über einen Hinteranschlag und ein Kontrollsystem, kalibrieren Sie regelmäßig und überprüfen Sie deren Genauigkeit.
Halten Sie das Bedienfeld sauber und staubfrei.
Schulung des Bedieners:
Schulen Sie die Bediener im ordnungsgemäßen Umgang mit der Maschine, einschließlich Sicherheitsverfahren und grundlegenden Wartungsaufgaben.
Fordern Sie die Bediener auf, ungewöhnliche Geräusche, Vibrationen oder Probleme mit der Maschine unverzüglich zu melden.
Ausrichtungen und Anpassungen:
Überprüfen und justieren Sie regelmäßig die Ausrichtung der Abkantpresse, um genaue und gleichmäßige Biegungen sicherzustellen.
Überprüfen Sie die Parallelität der Spannbalken und die Genauigkeit des Hinteranschlags.
Aufzeichnungen:
Führen Sie ein Wartungsprotokoll, um Inspektionen, Schmierpläne, Reparaturen und alle anderen relevanten Informationen aufzuzeichnen.
Beachten Sie stets die Richtlinien und Dokumentationen des Herstellers hinsichtlich der spezifischen Wartungsanforderungen für Ihr Abkantpressenmodell. Planen Sie außerdem regelmäßig professionelle Inspektionen und Wartungsarbeiten ein, um komplexere Aufgaben zu bewältigen und die optimale Leistung der Abkantpresse sicherzustellen.
Auswahl der Abkantwerkzeuge?
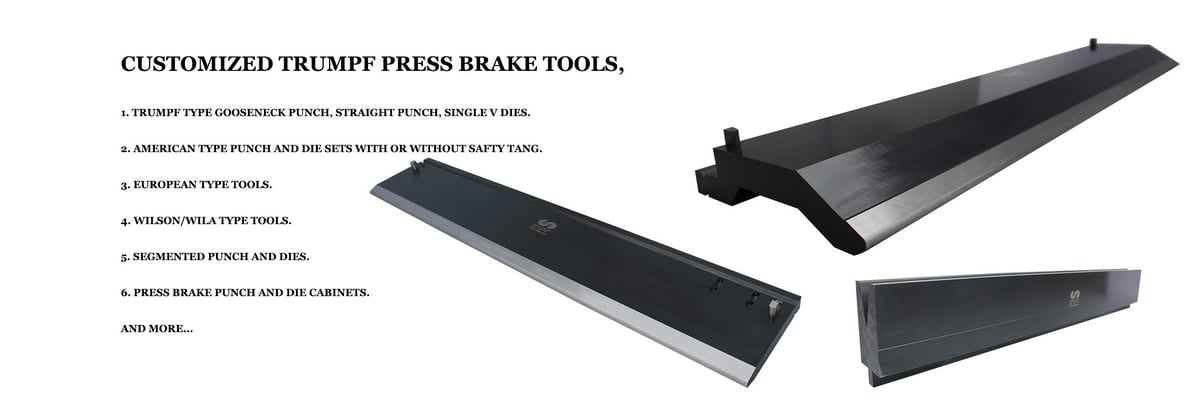
Die Wahl der Abkantwerkzeuge, auch Stempel und Matrizen genannt, ist entscheidend für präzise und hochwertige Blechbiegungen. Die Auswahl hängt von verschiedenen Faktoren ab, darunter dem zu verarbeitenden Material, dem gewünschten Biegewinkel, der Blechdicke und der spezifischen Anwendung. Hier sind einige Überlegungen zur Auswahl von Abkantwerkzeugen:
Materialart:
Verschiedene Materialien weisen unterschiedliche Eigenschaften wie Härte und Duktilität auf. Berücksichtigen Sie bei der Werkzeugauswahl die Materialart (z. B. Baustahl, Edelstahl, Aluminium), um Kompatibilität und optimale Leistung zu gewährleisten.
Biegeradius und Winkel:
Der für Ihre Anwendung erforderliche Biegeradius und -winkel beeinflussen die Wahl des Werkzeugs. Verschiedene Stempel- und Matrizenkonfigurationen ermöglichen die Herstellung spezifischer Biegeradien und -winkel.
Blechdicke:
Die Dicke des zu biegenden Blechs ist ein entscheidender Faktor. Es sollten Werkzeuge mit der richtigen Kapazität gewählt werden, um die erforderliche Dicke zu bewältigen, ohne die Qualität der Biegung zu beeinträchtigen.
Werkzeugstil:
Abkantwerkzeuge gibt es in verschiedenen Ausführungen, darunter V-Matrizen, Falzwerkzeuge, Radiuswerkzeuge und mehr. Die Wahl hängt von den spezifischen Biegeanforderungen Ihrer Anwendung ab.
Werkzeugbeschichtung:
Einige Werkzeuge verfügen über Beschichtungen oder Oberflächenbehandlungen, die die Reibung reduzieren, Fressen verhindern und die Werkzeuglebensdauer verlängern. Erwägen Sie Beschichtungen wie Nitrieren oder Beschichtungen mit geringen Reibungseigenschaften für eine verbesserte Leistung.
Materialhärte:
Werkzeugmaterialien mit höherer Härte sind im Allgemeinen verschleißfester und eignen sich für die Bearbeitung härterer Materialien. Berücksichtigen Sie die Härte des Werkzeugmaterials anhand der Härte des zu biegenden Blechs.
Multi-V-Matrizensätze:
Multi-V-Matrizensätze ermöglichen das Biegen verschiedener Winkel und Radien ohne häufigen Werkzeugwechsel. Sie eignen sich für Anwendungen mit unterschiedlichen Biegeanforderungen.
Präzisions- und Toleranzanforderungen:
Wenn Ihre Anwendung hohe Präzision und enge Toleranzen erfordert, wählen Sie Werkzeuge, die diese Anforderungen erfüllen. Präzisionsgeschliffene Werkzeuge sorgen für gleichmäßige und präzise Biegungen.
Werkzeugkompatibilität:
Stellen Sie sicher, dass die gewählten Abkantwerkzeuge mit Ihrem spezifischen Abkantpressenmodell und -design kompatibel sind. Achten Sie auf Werkzeugstandards wie europäische (Promecam/Amada) oder amerikanische (Trumpf) Ausführung.
Spezialwerkzeuge:
Erwägen Sie für einzigartige oder spezielle Anwendungen die Verwendung von benutzerdefinierten oder speziellen Werkzeugen, die für bestimmte Biegeherausforderungen entwickelt wurden.
Beachten Sie unbedingt die Richtlinien und Empfehlungen des Abkantpressenherstellers zur Werkzeugauswahl. Erfahrene Bediener und Werkzeugspezialisten können aufgrund ihrer Kenntnisse über Anwendung und Materialeigenschaften wertvolle Hinweise zur Auswahl der richtigen Werkzeuge geben. Überprüfen und warten Sie die Abkantpressenwerkzeuge regelmäßig, um optimale Leistung und Langlebigkeit zu gewährleisten.