Wenn Präzisionsschnitte wichtig sind, lautet eine häufig gestellte Frage: „Welche Dicke kann ein 3000-W-Faserlaser schneiden??" Diese Spitzentechnologie hat mit ihrer außergewöhnlichen Genauigkeit und Effizienz die Fertigungsindustrie verändert. Die Kenntnis der maximalen Schnittdicke eines 3000-W-Faserlasers ist entscheidend, um seine Wirksamkeit bei verschiedenen Anwendungen zu maximieren. In diesem Artikel untersuchen wir die Obergrenzen der mit einem 3000-W-Faserlaser erreichbaren Dicke, untersuchen die Faktoren, die seine Leistung beeinflussen, und bieten praktische Ratschläge für Benutzer.
Inhaltsverzeichnis
Einführung
Kurzer Überblick über die Faserlaserschneidtechnologie
Die Faserlaserschneidtechnologie hat sich aufgrund ihrer Präzision, Geschwindigkeit und Effizienz als bahnbrechende Neuerung in der Fertigungsindustrie erwiesen. Im Gegensatz zu herkömmlichen Schneidmethoden verwenden Faserlaser einen Hochleistungslichtstrahl, der von Dioden erzeugt und durch eine flexible Glasfaser übertragen wird. Dieser Strahl wird auf das Material fokussiert und schmilzt, verbrennt oder verdampft es, um präzise Schnitte zu erzielen. Die Technologie wird in verschiedenen Branchen häufig eingesetzt, darunter in der Automobil-, Luft- und Raumfahrt-, Elektronik- und Metallverarbeitung, da sie komplexe Formen mit hoher Genauigkeit und minimalem Abfall schneiden kann.
Bedeutung des Verständnisses der Schneidgrenzen eines 3000-W-Faserlasers
Das Verständnis der Schneidgrenzen eines 3000-W-Faserlasers ist wichtig, um seine Leistung zu optimieren und seinen effizienten Einsatz in verschiedenen Anwendungen sicherzustellen. Zu wissen, wie dick ein 3000-W-Faserlaser schneiden kann, hilft bei der Auswahl der geeigneten Materialien und der Anpassung der Schneidparameter, um die gewünschten Ergebnisse zu erzielen. Dieses Wissen ist für Hersteller von entscheidender Bedeutung, um die Produktivität zu maximieren, die Materialkosten zu senken und hohe Qualitätsstandards in ihren Produktionsprozessen einzuhalten. Darüber hinaus ermöglicht es eine bessere Planung und Entscheidungsfindung bei Investitionen in Faserlaserschneidtechnologie und stellt sicher, dass die gewählte Ausrüstung den spezifischen Anforderungen des Betriebs entspricht.
Faserlasertechnologie verstehen
Wie funktionieren Faserlaser?
Faserlaser funktionieren, indem sie durch die Lichtverstärkung in einem mit Seltenerdelementen wie Ytterbium dotierten Glasfaserkabel einen Hochleistungslichtstrahl erzeugen. Das Licht wird von Dioden erzeugt und dann durch die Glasfaser geleitet, die das Licht verstärken soll, ohne seine Kohärenz zu verlieren. Dieser hochfokussierte und intensive Strahl wird auf das zu schneidende Material gerichtet, wo er das Material bis zu seinem Schmelzpunkt erhitzt, was präzise Schnitte ermöglicht. Fokus und Intensität des Strahls können genau gesteuert werden, wodurch komplizierte Designs und Detailarbeiten mit minimaler Verzerrung oder thermischer Schädigung des umgebenden Materials möglich sind.
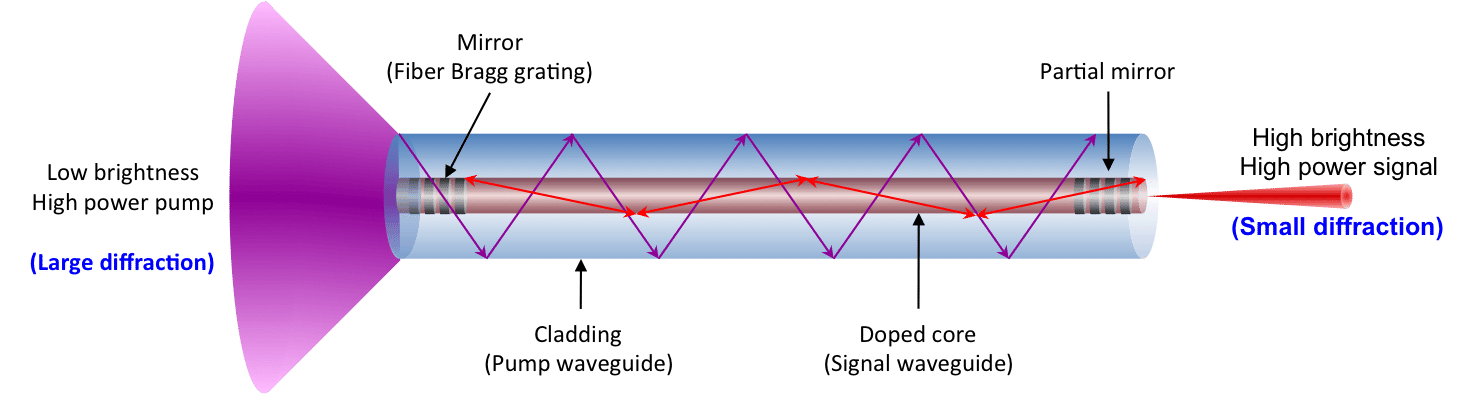
CO2-Laser vs. Faserlaser: Welcher ist besser zum Schneiden von Metall geeignet?
CO2-Laser:
- Vielseitigkeit: CO2-Laser sind äußerst vielseitig und können neben Metallen eine breite Palette von Materialien schneiden, darunter auch Kunststoffe, Holz und Keramik.
- Dickere Materialien: Sie eignen sich effektiv zum Schneiden dickerer Metalle wie Baustahl und Edelstahl mit einer Dicke von bis zu 25 mm, da sie die Strahlqualität auch über größere Entfernungen stabil halten können.
- Glatte Kanten: CO2-Laser können glattere Kanten auf dickeren Materialien erzeugen, was für Anwendungen von Vorteil ist, die eine hochwertige Oberflächenbearbeitung erfordern.
- Anschaffungskosten: Im Allgemeinen weisen CO2-Lasermaschinen im Vergleich zu Faserlasern geringere Anschaffungskosten auf, was sie für manche Unternehmen attraktiver macht.
Faserlaser:
- Geschwindigkeit und Effizienz: Faserlaser sind für ihre hohe Schneidgeschwindigkeit und Energieeffizienz bekannt und eignen sich daher ideal für Produktionsumgebungen mit hohen Stückzahlen.
- Präzision: Sie bieten hervorragende Präzision und Genauigkeit und eignen sich daher für komplizierte Designs und feine Details, selbst auf dünneren Materialien.
- Wartung: Aufgrund ihrer Festkörperkonstruktion und der geringeren Anzahl beweglicher Teile erfordern Faserlaser typischerweise weniger Wartung, was im Laufe der Zeit zu geringeren Betriebskosten führt.
- Reflektierende Materialien: Faserlaser eignen sich besonders gut zum Schneiden reflektierender Materialien wie Kupfer, Messing und Aluminium, die für CO2-Laser aufgrund ihrer Wellenlängenabsorptionseigenschaften eine Herausforderung darstellen können.
Auswahl der richtigen Technologie:
- Produktionsvolumen: Bei der Massenproduktion, bei der Geschwindigkeit und Effizienz erforderlich sind, werden häufig Faserlaser bevorzugt.
- Materialart: Wenn Sie neben Metallen auch andere Materialien schneiden müssen, bieten CO2-Laser eine größere Vielseitigkeit.
- Dicke und Präzision: Für dicke Metalle und Anwendungen, die präzises Schneiden erfordern, eignen sich CO2-Laser hervorragend, während Faserlaser bei Aufgaben glänzen, die komplizierte Detailarbeiten und Hochgeschwindigkeitsschneiden von dünnen bis mitteldicken Metallen erfordern.
Vorteile von Faserlasern gegenüber anderen Schneidmethoden
Faserlaser zeichnen sich in der Fertigungsindustrie durch zahlreiche Vorteile gegenüber herkömmlichen Schneidverfahren und anderen Lasertechnologien aus:
Präzision und Genauigkeit
Faserlaser zeichnen sich durch präzise Schnitte mit schmalen Schnittbreiten aus, wodurch der Materialabfall erheblich reduziert wird. Diese Präzision ermöglicht komplizierte Designs und komplexe Geometrien, die in Branchen wie der Luft- und Raumfahrt und der Elektronik von entscheidender Bedeutung sind. Studien haben gezeigt, dass Faserlaser Positionierungsgenauigkeiten von bis zu ±0,05 mm erreichen können, wodurch bei jedem Schnitt gleichbleibende Qualität und Maßgenauigkeit gewährleistet werden.
Hohe Effizienz
Im Vergleich zu CO2-Lasern weisen Faserlaser eine höhere Effizienz auf, was zu niedrigeren Betriebskosten und einem geringeren Energieverbrauch führt. Untersuchungen zeigen, dass Faserlaser über 30% der elektrischen Eingangsenergie in nutzbare Laserleistung umwandeln können, während CO2-Laser typischerweise etwa 10-20% umwandeln. Diese Effizienz senkt nicht nur die Produktionskosten, sondern trägt auch zu nachhaltigen Herstellungsverfahren bei, indem sie den Energieverbrauch und den CO2-Fußabdruck minimiert.
Geschwindigkeit
Einer der größten Vorteile von Faserlasern ist ihre hohe Schneidgeschwindigkeit. Sie können Materialien bis zu dreimal schneller schneiden als CO2-Laser. Ein 3000-W-Faserlaser kann beispielsweise dünne Stahlbleche mit einer Geschwindigkeit von über 30 Metern pro Minute schneiden, was die Produktivität deutlich steigert und die Vorlaufzeiten in Fertigungsprozessen verkürzt.
Vielseitigkeit
Faserlaser sind vielseitig einsetzbar und können eine Vielzahl von Materialien mit unterschiedlichen Stärken schneiden. Sie können Metalle wie Stahl (bis zu 25 mm), Aluminium (bis zu 15 mm) und Kupfer (bis zu 12 mm) sowie Nichtmetalle wie Kunststoffe und Verbundwerkstoffe bearbeiten. Diese Vielseitigkeit macht Faserlaser für vielfältige Anwendungen in zahlreichen Branchen geeignet, von der Automobil- und Medizingeräteherstellung bis hin zur Architektur- und Schmuckindustrie.
Geringer Wartungsaufwand
Da Faserlaser weniger bewegliche Teile und einen abgedichteten Glasfaserweg haben, erfordern sie im Vergleich zu CO2-Lasern und mechanischen Schneidsystemen nur minimalen Wartungsaufwand. Studien zeigen, dass Faserlaser Tausende von Stunden im Dauerbetrieb laufen können, bevor sie gewartet werden müssen. Dadurch werden Ausfallzeiten und Wartungskosten im Vergleich zu herkömmlichen Lasersystemen reduziert.
Qualität der Schnitte
Die hohe Strahlqualität von Faserlasern sorgt für saubere, glatte Kanten ohne Grate oder thermische Verformungen, sodass keine Nachbearbeitungsprozesse erforderlich sind. Diese überragende Schnittqualität ist entscheidend für das Erreichen enger Toleranzen und die Einhaltung strenger Qualitätsstandards in der Fertigung.
Umweltauswirkungen
Faserlaser sind aufgrund ihrer hohen Energieeffizienz und minimalen Emissionen für ihre Umweltvorteile bekannt. Untersuchungen zeigen, dass Faserlaser bei denselben Schneidaufgaben bis zu 70 % weniger Energie verbrauchen als CO2-Laser, was zu geringeren Treibhausgasemissionen beiträgt und die Gesamtumweltbelastung durch Herstellungsprozesse verringert.
Zusammenfassend lässt sich sagen, dass Faserlaser einen technologischen Fortschritt darstellen, der nicht nur die Fertigungskapazitäten verbessert, sondern auch die Nachhaltigkeit und Kosteneffizienz im industriellen Betrieb fördert. Ihre Präzision, Effizienz, Geschwindigkeit, Vielseitigkeit, ihr geringer Wartungsaufwand, ihre hervorragende Schnittqualität und ihre Umweltvorteile machen sie zur bevorzugten Wahl für moderne Fertigungsanwendungen.
Drei Faktoren, die die Schnittdicke beeinflussen
Um mit einem Faserlaser eine optimale Schnittstärke zu erreichen, ist ein differenziertes Verständnis mehrerer kritischer Faktoren erforderlich, die sich auf seine Leistung und Fähigkeiten auswirken:
Materialtyp
Verschiedene Materialien reagieren aufgrund ihrer Zusammensetzung und Eigenschaften unterschiedlich auf das Laserschneiden:
- Stahl: Faserlaser können abhängig von der jeweiligen Legierungszusammensetzung und -sorte effektiv Baustahl mit einer Dicke von bis zu 25 mm und Edelstahl mit einer Dicke von bis zu 20 mm schneiden.
- Aluminium: Aufgrund der im Vergleich zu Stahl geringeren Dichte, aber höheren Wärmeleitfähigkeit kann Aluminium mit Faserlasern bis zu einer Dicke von etwa 15 mm geschnitten werden.
- Kupfer und Messing: Diese Materialien sind aufgrund ihrer hohen Reflektivität gegenüber Infrarotwellenlängen schwieriger zu schneiden. Faserlaser begrenzen die Schnittdicke für Kupfer und Messing normalerweise auf etwa 12 mm.
Materialeigenschaften
Verschiedene Materialeigenschaften beeinflussen die Schneidfähigkeit maßgeblich:
- Dichte: Materialien mit höherer Dichte erfordern mehr Laserleistung, um tiefere Schnitte zu erzielen. Beispielsweise kann das Schneiden dickerer Abschnitte von Materialien mit hoher Dichte wie Stahl höhere Leistungseinstellungen erfordern.
- Wärmeleitfähigkeit: Materialien mit hoher Wärmeleitfähigkeit, wie Kupfer, leiten Wärme schnell ab. Diese Eigenschaft kann den Schneidvorgang beeinträchtigen und erfordert Anpassungen der Laserparameter, um Effizienz und Qualität aufrechtzuerhalten.
- Reflexionsvermögen: Bei reflektierenden Materialien wie Aluminium und Kupfer kann eine Optimierung der Laserparameter erforderlich sein, um die Schneidleistung zu verbessern. Die Steuerung der Reflektivität ist entscheidend, um saubere Schnitte zu erzielen, ohne Geschwindigkeit oder Qualität zu beeinträchtigen.
Anforderungen an Schnittgeschwindigkeit und -qualität
Um optimale Ergebnisse zu erzielen, ist es wichtig, die Schnittgeschwindigkeit mit Qualitätsaspekten in Einklang zu bringen:
- Geschwindigkeit: Faserlaser können hohe Schnittgeschwindigkeiten erreichen, die bei dünnen Materialien 30 Meter pro Minute überschreiten. Beim Schneiden dickerer Abschnitte sind jedoch möglicherweise geringere Geschwindigkeiten erforderlich, um die Präzision beizubehalten und thermische Verformungen zu vermeiden.
- Qualitätsanforderungen: Um strenge Qualitätsstandards zu erfüllen, müssen Schneidparameter wie Leistung, Fokus und Geschwindigkeit angepasst werden. Die Feinabstimmung dieser Parameter gewährleistet saubere Kanten, minimale Grate und Maßgenauigkeit, insbesondere bei Anwendungen, die enge Toleranzen erfordern.
Das Verständnis dieser Faktoren ermöglicht es den Bedienern, Schneidprozesse zu optimieren, geeignete Materialien auszuwählen und Parameter mithilfe der Faserlasertechnologie effektiv anzupassen. Dieser umfassende Ansatz gewährleistet einen effizienten Betrieb und qualitativ hochwertige Ergebnisse in einer Reihe von industriellen Anwendungen.
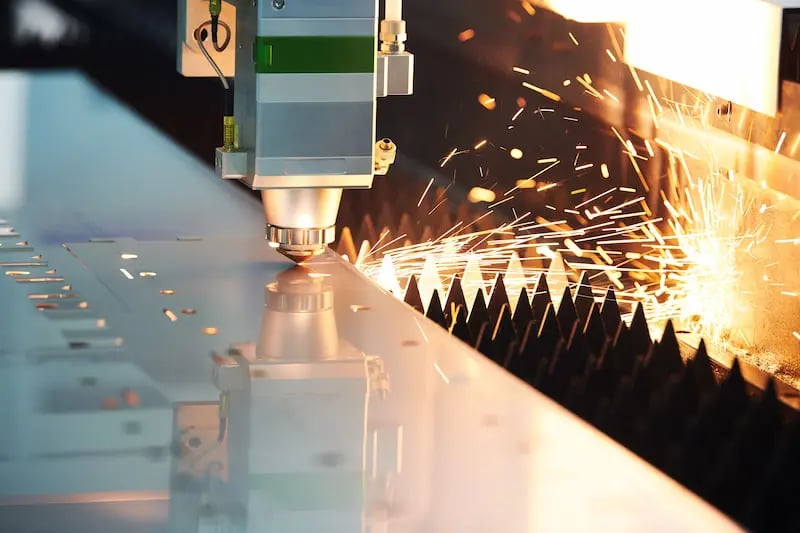
Maximale Schnittstärke für verschiedene Materialien
Metafaserlaserschneidmaschinen werden hauptsächlich zum Schneiden einer Vielzahl von Metallmaterialien verwendet, darunter Edelstahl, Kohlenstoffstahl, legierter Stahl, Aluminium, Silber, Kupfer, Titan und andere Metalle. Die wichtigsten Vorteile dieser Maschinen werden in ihrer praktischen Anwendung deutlich. Die Schneidleistung einer Faserlaserschneidmaschine hängt von Faktoren wie der Qualität der Maschine, dem verwendeten Lasertyp, der Schneidumgebung, der Schneidgeschwindigkeit und der Verwendung von Hilfsgasen ab, die die Schneidleistung verbessern können. Folglich gibt es keinen absoluten Standard zur Beurteilung der Schnittdicke. Im Allgemeinen stellen dickere Metallplatten größere Herausforderungen beim Schneiden dar. Beim Kauf von Laserschneidern müssen Benutzer ihre spezifischen Anforderungen sorgfältig berücksichtigen und dementsprechend die geeignete Laserkonfiguration auswählen.
Welche Dicken können also verschiedene Faserlaserschneidmaschinen effektiv durch Metallplatten schneiden?
Welche Dicke kann ein 500-W- bis 2000-W-Faserlaser schneiden?
1. Die maximale Schnittdicke verschiedener Materialien einer 500-W-Metall-Laserschneidmaschine: Die maximale Dicke von Kohlenstoffstahl beträgt 6 mm; Die maximale Dicke von Edelstahl beträgt 3 mm; Die maximale Dicke von Aluminiumplatten beträgt 2 mm; Die maximale Dicke von Kupferplatten beträgt 2 mm;
2. Die maximale Dicke der verschiedenen Materialien, die von einer 1000-W-Metall-Laserschneidmaschine geschnitten werden: Die maximale Dicke von Kohlenstoffstahl beträgt 10 mm; Die maximale Dicke von Edelstahl beträgt 5 mm; Die maximale Dicke von Aluminiumplatten beträgt 3 mm; Die maximale Dicke von Kupferplatten beträgt 3 mm;
3. Die maximale Dicke der verschiedenen Materialien, die von einer 2000-W-Metall-Laserschneidmaschine geschnitten werden: Die maximale Dicke von Kohlenstoffstahl beträgt 16 mm; Die maximale Dicke von Edelstahl beträgt 8 mm; Die maximale Dicke von Aluminiumplatten beträgt 5 mm; Die maximale Dicke von Kupferplatten beträgt 5 mm;
Welche Dicke kann ein 3000-W-Faserlaser schneiden?
Die maximale Dicke der verschiedenen Materialien, die von einer 3000 W-Metall-Laserschneidmaschine geschnitten werden: Die maximale Dicke von Kohlenstoffstahl beträgt 20 mm; Die maximale Dicke von Edelstahl beträgt 10 mm; Die maximale Dicke von Aluminiumplatten beträgt 8 mm; Die maximale Dicke von Kupferplatten beträgt 8 mm;
Welche Dicke kann ein 4000-W-Faserlaser schneiden?
Beim 4000-W-Laserschneiden von Edelstahl sind es höchstens 16 mm, aber die Qualität der Schnittfläche über 12 mm ist nicht garantiert, und die Schnittfläche unter 12 mm ist definitiv hell. Die Schneidleistung von 6000 W ist besser, aber der Preis ist auch höher.
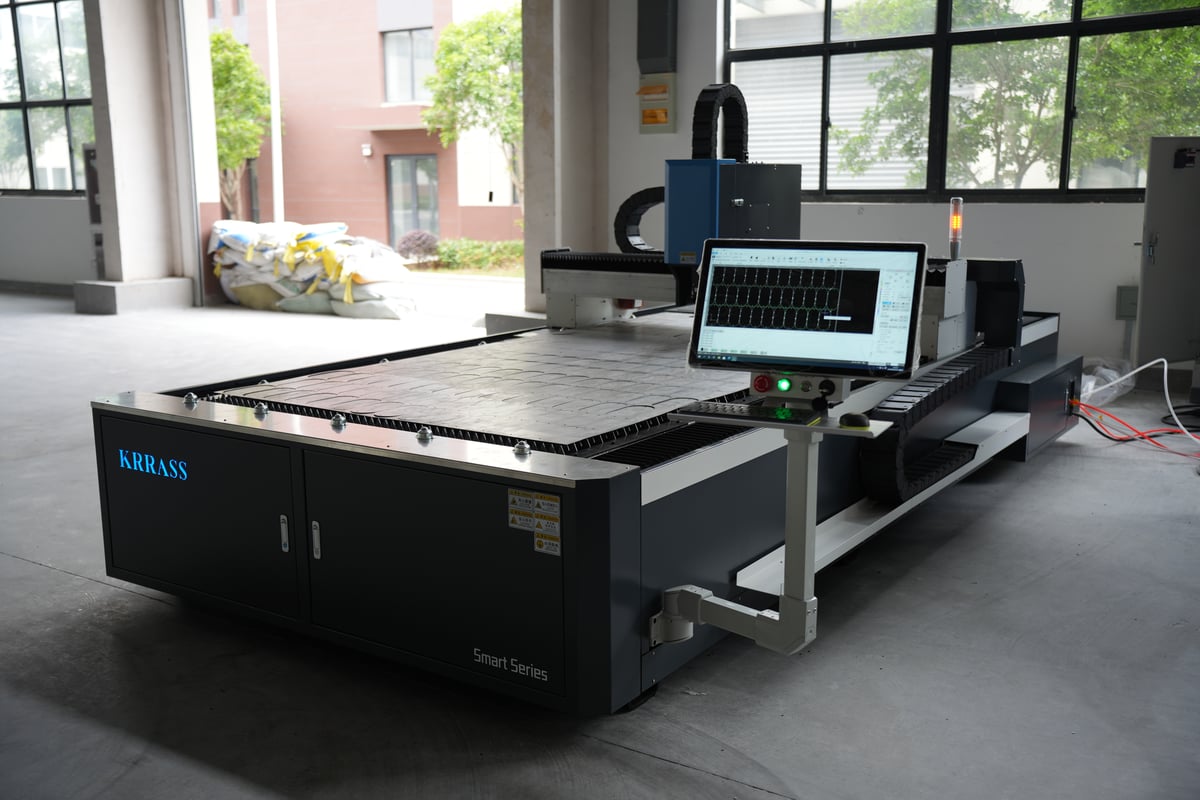
Entwicklung der Laserschneidleistung: Die Grenzen des Möglichen erweitern
Von 6000 W über 8000 W bis hin zu den einst unvorstellbaren 10.000 W-Laserschneidmaschinen hat sich die Leistung dieser Maschinen Schritt für Schritt verbessert und unsere Erwartungen übertroffen. Bisher war das Faserlaserschneiden auf das Schneiden von Kohlenstoffstahlplatten mit einer Dicke von bis zu 20 mm und Edelstahlplatten mit einer Dicke von bis zu 12 mm beschränkt. Mit 10.000 W-Laserschneidmaschinen wie dem Modell Dada können jetzt jedoch Aluminiumlegierungsplatten mit einer Dicke von bis zu 40 mm und Edelstahlplatten mit einer Dicke von bis zu 50 mm effektiv geschnitten werden.
Verbesserte Schneidfunktionen
Bei Edelstahlplatten mit einer Dicke von 3 bis 10 mm arbeitet eine 10.000-W-Laserschneidmaschine mit mehr als der doppelten Geschwindigkeit einer 6.000-W-Maschine. Bei Kohlenstoffstahlanwendungen erreicht diese Maschine schnelles Schneiden von hellen Oberflächen mit Geschwindigkeiten von 18 bis 20 mm pro Sekunde, also das Doppelte der Standardschneidgeschwindigkeit. Darüber hinaus erhöht die Verwendung von Druckluft oder Stickstoff beim Schneiden von Kohlenstoffstahl mit einer Dicke von bis zu 12 mm die Effizienz im Vergleich zum Sauerstoffschneiden um das Sechs- bis Siebenfache.
Aktuelle Daten zeigen, dass sich die Geschwindigkeit mit höherer Laserleistung deutlich steigern lässt: Das Schneiden von 8 mm dickem Edelstahl ist mit einer 6-kW-Maschine fast 400 TP3T schneller als mit einem 3-kW-Modell. Darüber hinaus arbeitet ein 12-kW-Laser bei 20 mm dickem Edelstahl 114 TP3T schneller als eine 10-kW-Maschine.
Aus wirtschaftlicher Sicht sind die Kosten einer 10.000-W-Laserschneidmaschine nur geringfügig höher als die eines 6-kW-Modells, sie bietet jedoch eine mehr als doppelt so hohe Produktionseffizienz. Diese Effizienz spart nicht nur Arbeit und Platz, sondern wird auch von den Besitzern von Laserverarbeitungsunternehmen geschätzt, was ihre Kosteneffizienz und Produktivitätsvorteile unterstreicht.
Wichtige Tipps zur Leistungsmaximierung von Faserlasern
Materialvorbereitung und -auswahl
Bei der Auswahl geeigneter Materialien für das Faserlaserschneiden müssen deren Zusammensetzung und Dickenkompatibilität berücksichtigt werden. Verschiedene Materialien wie Edelstahl, Kohlenstoffstahl, Aluminium und verschiedene Legierungen reagieren aufgrund ihrer Wärmeleitfähigkeit, ihres Reflexionsvermögens und ihrer chemischen Zusammensetzung unterschiedlich auf das Laserschneiden. Es ist wichtig, Materialien auszuwählen, die zu den Fähigkeiten des Laserschneiders passen und innerhalb des angegebenen Schnittdickenbereichs liegen.
Darüber hinaus ist es wichtig, sicherzustellen, dass die Materialien sauber und frei von Verunreinigungen sind, um Probleme beim Schneiden zu vermeiden. Verunreinigungen wie Öl, Fett oder Rost können die Wirksamkeit des Laserstrahls beeinträchtigen und zu ungleichmäßigen Schnitten, erhöhter Wärmeaufnahme oder sogar Schäden an der Schneidausrüstung führen. Eine ordnungsgemäße Vorbereitung der Materialien, einschließlich gründlicher Reinigung und Oberflächenbehandlung nach Bedarf, trägt dazu bei, die Schnittpräzision und -qualität während des gesamten Produktionsprozesses aufrechtzuerhalten. Diese Praktiken optimieren nicht nur die Schneidleistung, sondern tragen auch zur Langlebigkeit der Faserlaserschneidmaschine und zur Qualität der fertigen Produkte bei.
Optimierung der Schnittparameter
Leistung: Passen Sie die Laserleistungseinstellungen an die Eigenschaften und Dicke des Materials an und optimieren Sie so sowohl Schnittgeschwindigkeit als auch -qualität. Diese Anpassung stellt sicher, dass der Laser ausreichend Energie für saubere und präzise Schnitte ohne übermäßige Hitze oder Materialverzerrung liefert.
Geschwindigkeit: Kontrollieren Sie die Schnittgeschwindigkeit sorgfältig, um ein Gleichgewicht zwischen Effizienz und Präzision zu erreichen. Durch die Anpassung der Geschwindigkeit sind glatte Schnitte bei gleichbleibender Genauigkeit möglich, was für das Erreichen hochwertiger Ergebnisse in Fertigungsprozessen entscheidend ist.
Fokus: Überwachen und optimieren Sie den Laserfokus regelmäßig, um eine gleichbleibende Schnitttiefe und Kantenqualität zu gewährleisten. Die richtige Fokuseinstellung stellt sicher, dass der Laserstrahl während des gesamten Schneidvorgangs die optimale Intensität beibehält, was für präzise Schnitte bei unterschiedlichen Materialstärken unerlässlich ist.
Umweltkontrolle
Richtige Belüftung: Eine ausreichende Belüftung ist wichtig, um Rauch, Dämpfe und Partikel zu entfernen, die während des Schneidvorgangs entstehen. Eine effiziente Belüftung verbessert nicht nur die Luftqualität am Arbeitsplatz, sondern verhindert auch die Ansammlung von Schmutz, der den Laserstrahl behindern oder die Materialoberfläche verunreinigen könnte.
Feuchtigkeitsmanagement: Die Aufrechterhaltung optimaler Luftfeuchtigkeitswerte hilft, die Materialeigenschaften zu stabilisieren und Schwankungen in der Schneidleistung vorzubeugen. Übermäßige Luftfeuchtigkeit kann zu Kondensation auf der Optik führen und die Strahlqualität verringern, was sich auf die Schneidpräzision auswirkt. Umgekehrt können zu trockene Bedingungen die statische Elektrizität erhöhen und möglicherweise Entladungsprobleme verursachen.
Temperaturkontrolle: Durch die Kontrolle der Umgebungstemperatur können die thermische Ausdehnung und Kontraktion von Materialien minimiert werden, die die Maßgenauigkeit beim Schneiden beeinträchtigen können. Stabile Temperaturen tragen außerdem zu einer gleichbleibenden Laserstrahlleistung bei und verhindern thermische Belastungen der Maschinenkomponenten.
Sauberkeit: Es ist wichtig, den Arbeitsbereich sauber und ordentlich zu halten. Staub, Schmutz und Ablagerungen können die Laseroptik beeinträchtigen und zu uneinheitlichen Schneidergebnissen führen. Regelmäßiges Reinigen der Maschinenkomponenten, einschließlich Linsen, Spiegel und Schneidköpfe, gewährleistet optimale Leistung und verlängert die Lebensdauer der Geräte.
Sicherheitsmaßnahmen: Durch die Implementierung von Sicherheitsprotokollen, wie z. B. eine ordnungsgemäße Erdung der Maschine, Brandschutzmaßnahmen und persönliche Schutzausrüstung (PSA) für die Bediener, wird bei Laserschneidvorgängen eine sichere Arbeitsumgebung gewährleistet.
Regelmäßige Wartung und Kalibrierung
Um die Spitzenleistung von Faserlaserschneidmaschinen aufrechtzuerhalten, ist die Einhaltung regelmäßiger Wartungspraktiken, die Reinigung, Kalibrierung und Schmierung umfassen, unerlässlich.
Reinigung von Optiken, Linsen und Schneidköpfen: Die regelmäßige Reinigung von Optiken, Linsen und Schneidköpfen ist entscheidend, um angesammelten Schmutz und Verunreinigungen zu entfernen. Staub und Rückstände können die Qualität des Laserstrahls beeinträchtigen und zu ungleichmäßigen Schnitten oder verminderter Präzision führen. Die Verwendung empfohlener Reinigungslösungen und -methoden stellt sicher, dass diese Komponenten sauber und funktionsfähig bleiben und die Schneideffizienz und -qualität optimiert wird.
Regelmäßige Kalibrierung: Regelmäßige Kalibrierungssitzungen sind erforderlich, um die Ausrichtung der Lasersystemkomponenten zu überprüfen und anzupassen. Dieser Vorgang stellt sicher, dass der Laserstrahl genau fokussiert und auf den Schneidpfad ausgerichtet bleibt. Durch die Beibehaltung einer präzisen Ausrichtung können Bediener bei verschiedenen Materialien und Stärken konstant die gewünschten Schneidergebnisse erzielen, wodurch die Wahrscheinlichkeit von Fehlern verringert und die Betriebseffizienz maximiert wird.
Schmierung beweglicher Teile: Das Auftragen geeigneter Schmiermittel auf die beweglichen Teile der Laserschneidmaschine trägt dazu bei, Reibung und Verschleiß zu minimieren. Diese vorbeugende Maßnahme verlängert nicht nur die Lebensdauer kritischer Komponenten, sondern sorgt auch für einen reibungsloseren Betrieb und verringert das Risiko mechanischer Ausfälle. Regelmäßiges Schmieren gemäß den Herstellerrichtlinien sorgt dafür, dass die Zuverlässigkeit und Leistungskonsistenz der Maschine über einen längeren Zeitraum erhalten bleibt.
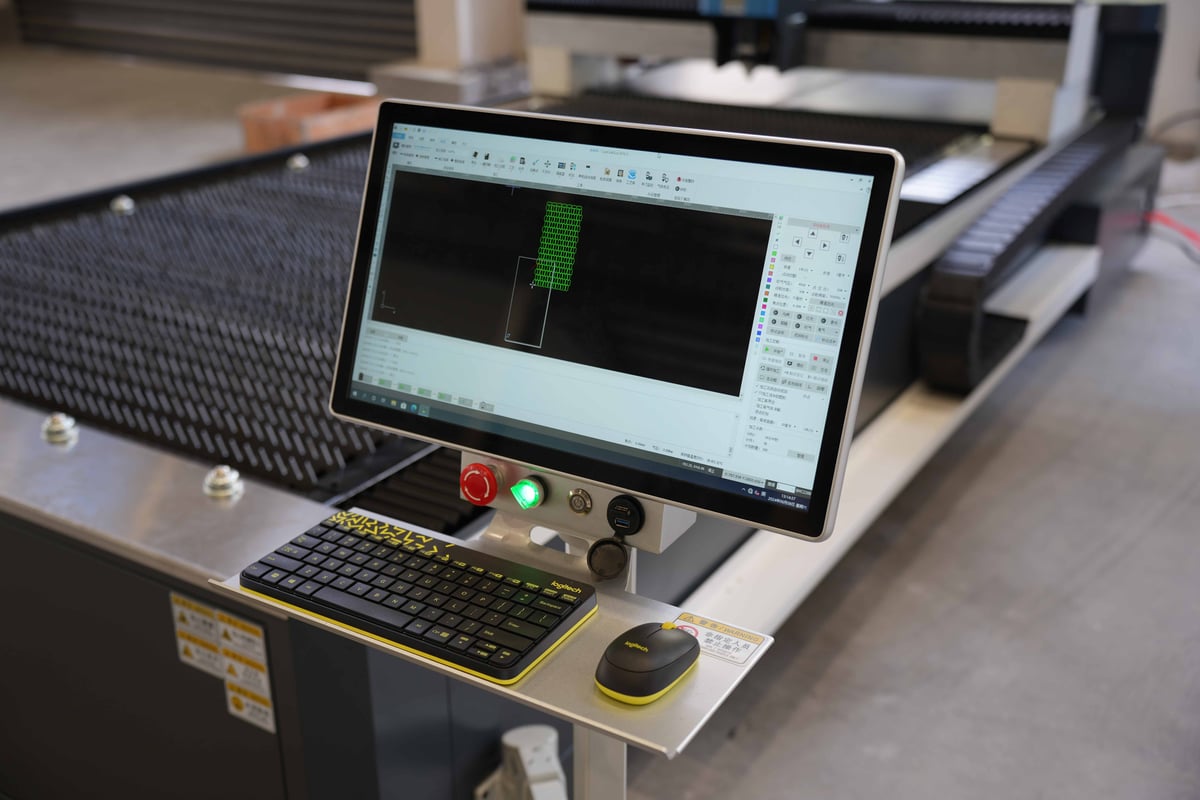
Einsatz von Hilfsgasen
Druckluft: Wenn Druckluft als Hilfsgas verwendet wird, hilft sie dabei, geschmolzenes Metall und Späne aus der Schneidzone zu blasen. Dadurch wird die Ansammlung von Material auf der Schneidfläche verhindert, wodurch das Risiko einer erneuten Verfestigung verringert und die allgemeine Sauberkeit des Schnitts verbessert wird. Druckluft hilft auch dabei, das Material während des Schneidens abzukühlen, was die Schneidgeschwindigkeit und -effizienz verbessern kann, insbesondere bei dünneren Materialien.
Stickstoff: Stickstoff wird aufgrund seiner nicht reaktiven Eigenschaften und seiner Fähigkeit, eine saubere Schnittkante zu erzeugen, allgemein bevorzugt. Bei Verwendung als Schneidgas verdrängt Stickstoff Sauerstoff aus der Schneidzone und reduziert so die Oxidation an der Schnittkante. Dies führt zu einer glatteren, oxidfreien Oberflächenbeschaffenheit, was insbesondere für oxidationsempfindliche Materialien wie Edelstahl und Aluminium von Vorteil ist. Stickstoff trägt auch dazu bei, stabile Schneidbedingungen aufrechtzuerhalten und kann die Gesamtqualität des Schnitts verbessern, einschließlich Kantenglätte und Maßgenauigkeit.
Sauerstoff und andere Gase: Sauerstoff ist ein weiteres häufig verwendetes Hilfsgas, insbesondere zum Schneiden von Weichstahl. Es verstärkt die exotherme Reaktion mit dem Metall und erhöht dadurch die Schnittgeschwindigkeit und -effizienz. Sauerstoff ist jedoch möglicherweise nicht für oxidationsanfällige Materialien geeignet, da er zu raueren Schnittkanten und potenziellen Wärmeeinflusszonen führen kann.
Optimierung des Gasverbrauchs: Die Wahl des Hilfsgases hängt vom zu schneidenden Material und den gewünschten Schneidergebnissen ab. Die richtige Auswahl und Optimierung des Gases kann sich erheblich auf die Schneidgeschwindigkeit, die Kantenqualität und die Gesamteffizienz des Prozesses auswirken. Bediener sollten mit verschiedenen Gasarten und -drücken experimentieren, um die optimalen Einstellungen für bestimmte Materialien und Dicken zu ermitteln und so die bestmögliche Schneidleistung sicherzustellen.
So wählen Sie die beste Leistung für einen Ideen-Schneideffekt
Die Leistung einer Laserschneidmaschine ist ein entscheidender Faktor, den Sie beim Kauf von Geräten für Metallschneidvorgänge berücksichtigen sollten. Sie hat direkten Einfluss auf die Energieabgabe des Laserkopfes und wirkt sich sowohl auf die Qualität der Bearbeitung als auch auf die Betriebsgeschwindigkeit aus. Höhere Leistungsstufen ermöglichen eine bessere Schnittqualität und Effizienz und verkürzen die Produktionszeiten erheblich.
In der Blechbearbeitungsindustrie haben Lasermaschinen für dünne Materialien normalerweise eine Mindestleistung von 500 W. Üblicherweise werden jedoch Schneidleistungen zwischen 3 und 20 kW verwendet, die je nach Produktionsanforderungen und gewünschten Betriebsvorteilen ausgewählt werden. In jüngster Zeit haben Faserlaserschneidtechnologien sogar Leistungsstufen von bis zu 40 kW erreicht, um den industriellen Anforderungen nach schnelleren Verarbeitungsgeschwindigkeiten und verbesserten Schneidfunktionen gerecht zu werden.
Durch die Wahl der geeigneten Laserleistung können Hersteller optimale Ergebnisse in Bezug auf Präzision, Produktivität und Kosteneffizienz erzielen. Systeme mit höherer Leistung verbessern nicht nur die Schnittgeschwindigkeit und -qualität, sondern bieten auch mehr Vielseitigkeit bei der Handhabung einer Vielzahl von Materialstärken und -arten. Mit dem fortschreitenden technologischen Fortschritt entwickeln sich Skalierbarkeit und Effizienz von Laserschneidmaschinen weiter und erfüllen so die sich wandelnden Anforderungen moderner Fertigungsindustrien.
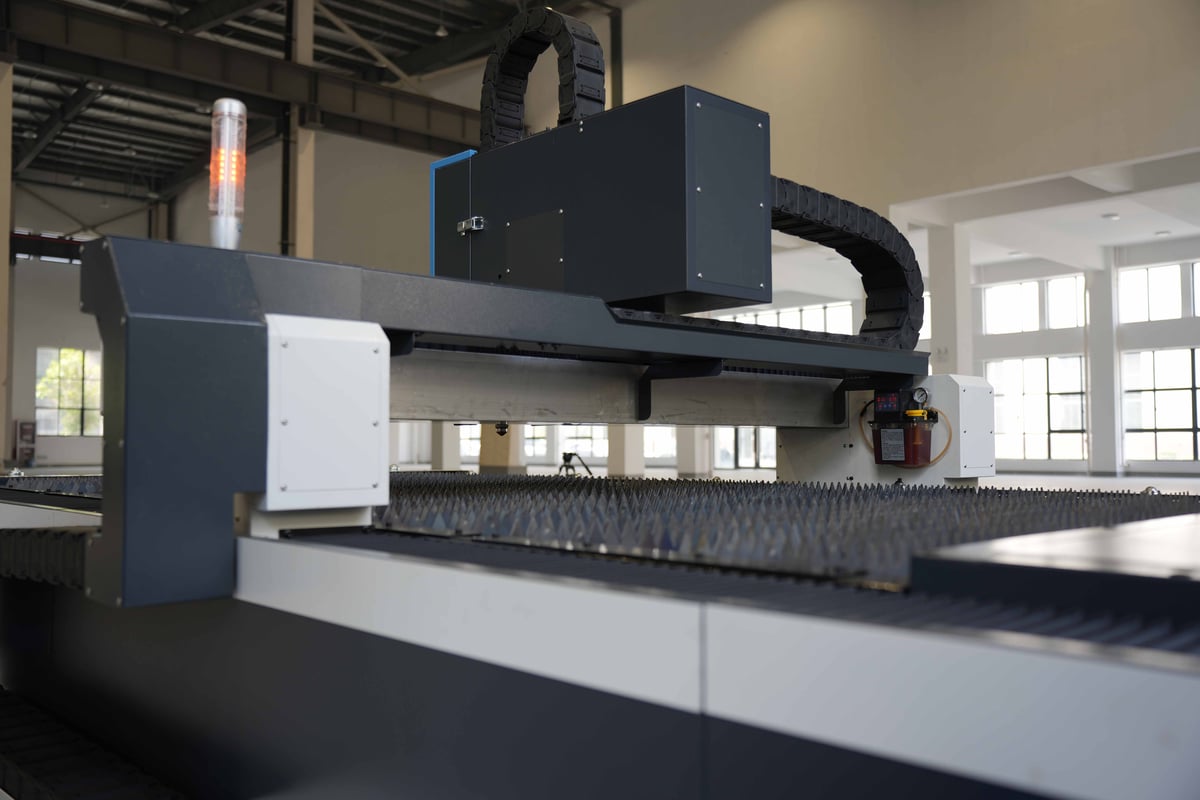
Tipps zur Auswahl der richtigen Leistung zum Metallschneiden
Materialart und Dicke: Verschiedene Metalle erfordern unterschiedliche Laserleistungen für effizientes Schneiden. Dickere Materialien wie Edelstahl oder Aluminium können beispielsweise höhere Leistungsstufen erfordern, um saubere Schnitte zu erzielen.
Anforderungen an Schnittgeschwindigkeit und Präzision: Höhere Laserleistungen ermöglichen im Allgemeinen schnellere Schnittgeschwindigkeiten bei gleichbleibender Präzision. Berücksichtigen Sie das gewünschte Gleichgewicht zwischen Geschwindigkeit und Genauigkeit basierend auf Ihren Produktionsanforderungen.
Maschinenleistung und Technologie: Bewerten Sie die Fähigkeiten der verfügbaren Laserschneidmaschinen. Moderne Fortschritte in der Faserlasertechnologie bieten eine breite Palette an Leistungsoptionen, von niedrigeren Leistungen für dünne Materialien bis hin zu höheren Leistungen für dicke und schnelle Schnitte.
Kosten- und Betriebseffizienz: Leistungsstärkere Laser bieten zwar schnellere Schnittgeschwindigkeiten und eine bessere Qualität, sind aber auch mit höheren Betriebskosten verbunden. Bewerten Sie die Wirtschaftlichkeit einer Investition in höhere Leistung anhand Ihres Produktionsvolumens und Ihrer Anforderungen.
Anwendungsspezifisches: Berücksichtigen Sie die spezifischen Anwendungen und Branchen, in denen Sie tätig sind. Einige Anwendungen erfordern möglicherweise spezielle Schneidfunktionen, die nur Laser mit höherer Leistung bieten können.
Bedeutet höhere Laserleistung immer eine bessere Schneidleistung?
Nicht unbedingt. Während eine höhere Laserleistung im Allgemeinen höhere Schneidgeschwindigkeiten ermöglicht, was insbesondere bei dickeren Metallmaterialien von Vorteil ist, hängt die tatsächliche Schneidleistung von mehreren Faktoren ab, die über die Leistung hinausgehen:
- Material- und Dickenvariabilität: Für optimale Ergebnisse sind bei verschiedenen Metallen und Materialstärken unterschiedliche Laserleistungsstufen erforderlich. Das Schneiden dünner Materialien mit zu hoher Leistung kann beispielsweise zu Überschmelzen oder einer größeren Wärmeeinflusszone führen, was Präzision und Kantenqualität beeinträchtigt.
- Präzisions- und Detaillierungsanforderungen: Das Schneiden komplizierter Designs oder detaillierter Muster erfordert ein Gleichgewicht zwischen Kraft und Präzision. Übermäßige Kraft kann die Schnittgeschwindigkeit erhöhen, kann aber zu Lasten feiner Details und Genauigkeit gehen, was in Branchen wie der Elektronik oder der Schmuckherstellung von entscheidender Bedeutung ist.
- Oberflächenqualität und Finish: Auch bei hoher Leistung hängt die Qualität des Schnitts weitgehend von Faktoren wie Strahlqualität, Brennpunktgenauigkeit und Schneidkopfdesign ab. Falsche Einstellungen können zu rauen Kanten oder Materialverzerrungen führen und die Qualität des Endprodukts beeinträchtigen.
Fallstudien und Datenanalyse:
- Fall 1: Eine Studie zum Vergleich von 6-kW- und 12-kW-Faserlasern im Automobilbau ergab, dass der 12-kW-Laser zwar höhere Schneidgeschwindigkeiten bei 10 mm starken Edelstahlplatten erreichte, der 6-kW-Laser jedoch aufgrund der besseren Kontrolle der Wärmeeinflusszone glattere Kanten und weniger Materialverzerrungen erzeugte.
- Fall 2: Daten aus einer Fertigungswerkstatt zeigten, dass sich bei 8 mm starken Aluminiumblechen die Schnittgeschwindigkeit um 401 TP3T verbesserte, wenn man die Leistung des Lasers von 3 auf 6 kW erhöhte; die Ausschussrate stieg jedoch aufgrund häufigerer Gratbildung und gröberer Schnitte bei der höheren Leistung.
- Forschungseinblicke: Untersuchungen von Lasertechnologieinstituten zeigen, dass eine optimale Schneidleistung häufig durch ein Gleichgewicht zwischen Leistung, Strahlqualität und Schneidparametern erreicht werden kann. Eine höhere Leistung kann die Produktivität steigern, kann jedoch sorgfältige Anpassungen erfordern, um die Schnittpräzision aufrechtzuerhalten und Materialabfall zu minimieren.
Zusammenfassend lässt sich sagen, dass eine höhere Laserleistung zwar die Schneideffizienz und -geschwindigkeit verbessern kann, das Erreichen der besten Schneidleistung jedoch einen differenzierten Ansatz erfordert. Dabei müssen Parameter wie Leistung, Geschwindigkeit und Strahlqualität basierend auf spezifischen Materialeigenschaften, Anwendungsanforderungen und der gewünschten Ausgabequalität optimiert werden. Durch die Abstimmung dieser Faktoren erreichen Hersteller nicht nur eine schnellere Produktion, sondern auch eine überlegene Schnittgenauigkeit und Oberflächengüte.
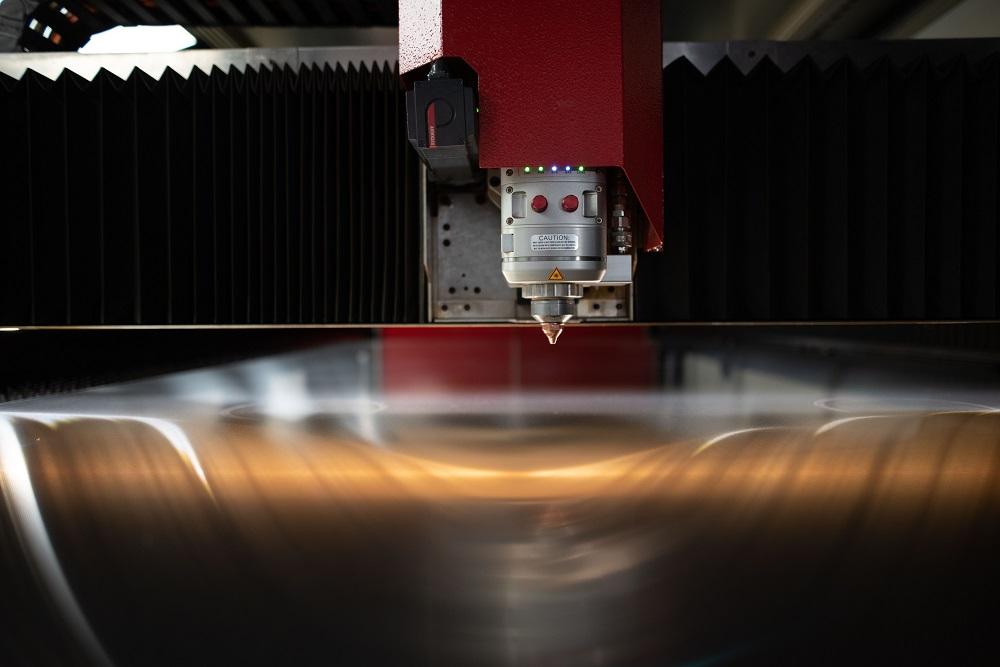
Zusammenfassung: Entfesseln Sie Ihr Laserschneidpotenzial mit Krrass Laser
Suchen Sie nach einem Laserschneider, der auf Ihre spezifischen Materialschneidanforderungen zugeschnitten ist? Möchten Sie wissen Wie dick kann ein 3000-W-Faserlaser schneiden?? Bei Krrass Laser sind wir auf Spitzentechnologie spezialisiert, die darauf ausgelegt ist, eine breite Palette von Materialien präzise und effizient zu bearbeiten. Egal, ob Sie mit Metallen, Kunststoffen, Keramik oder anderen Materialien arbeiten, unsere Laserschneidlösungen sorgen für erstklassige Qualitätsergebnisse für Ihre Projekte.
Geben Sie sich bei Ihren Projekten nicht mit weniger als Präzision zufrieden. Kontaktieren Sie Krrass Laser noch heute für fachkundige Beratung, wettbewerbsfähige Angebote und um zu erfahren, wie unsere fortschrittliche Laserschneidtechnologie Ihre Fertigungsprozesse verbessern kann.
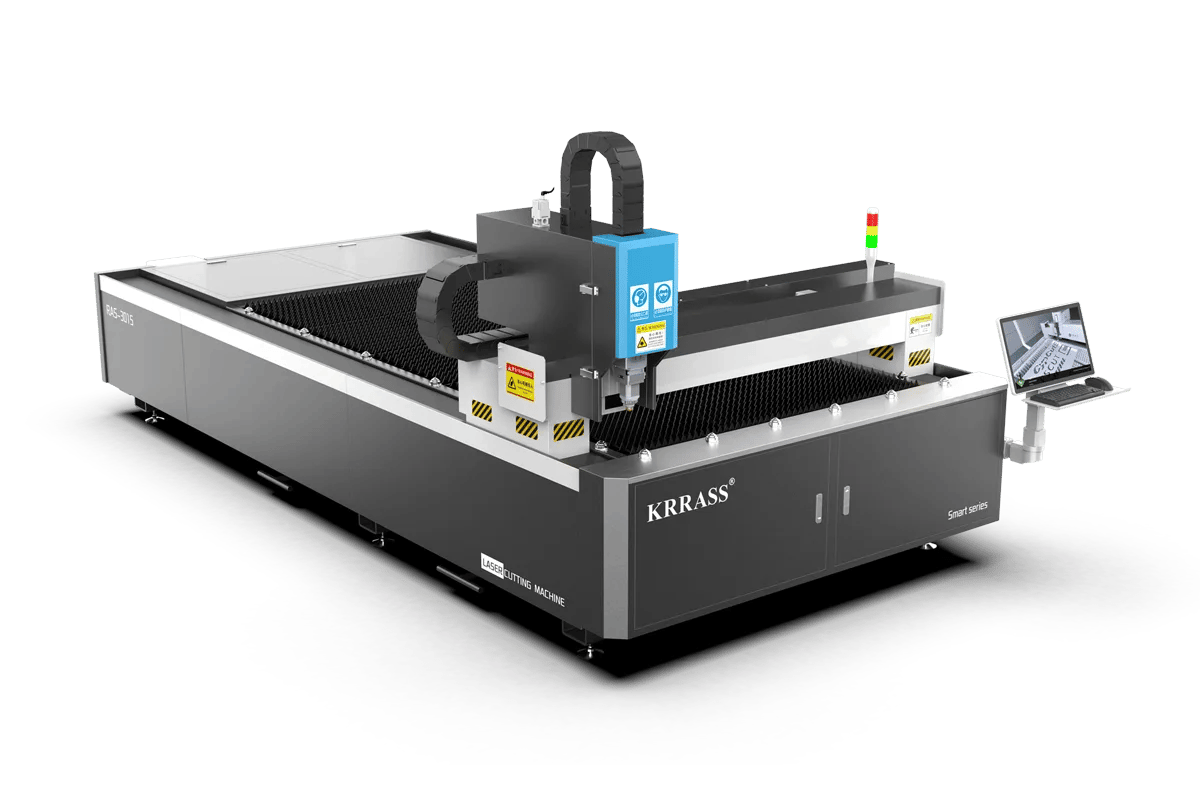