Wir präsentieren die Ergebnisse von Experimenten, die die Machbarkeit der Verwendung eines fasergekoppelten Nd untersuchen:YAG-Laser zum Schneiden von dicken Weichstahlplatten (Dicke > 15 mm). Die Tests wurden mit einem Dauerstrich-Nd:YAG-Laser mit 2,5 kW durchgeführt, der über eine Glasfaser mit Quarzkern von 0,6 mm Durchmesser auf das Werkstück gerichtet wurde. Die in der Studie verwendeten Weichstahlproben waren zwischen 10 und 50 mm dick. Die Auswirkungen verschiedener Betriebsparameter – einschließlich Brennfleckgröße, Position der Schneiddüse relativ zur Stahloberfläche, Hilfsgasdruck, Laserleistung und Schnittgeschwindigkeit – auf die Qualität der Schnittflächen wurden untersucht und analysiert.
Vorläufige Ergebnisse zeigen, dass es möglich ist, Weichstahlplatten mit einer Dicke von bis zu 50 mm bei Geschwindigkeiten von bis zu 200 mm/min mit nur 500 W Nd:YAG-Laserleistung zu schneiden. Die resultierenden Schnittflächen waren glatt und bartfrei, was darauf hindeutet, dass die Nd:YAG-Lasertechnologie ein erhebliches Potenzial zum Schneiden dicker Stahlplatten bietet.
Einführung
Laserschneiden in der Materialverarbeitung
Das Laserschneiden macht etwa ein Viertel der Lasermaterialbearbeitungsindustrie aus [1]. In den letzten 30 Jahren, seit der erste gasunterstützte Laserschnitt durchgeführt wurde [2], hat sich die grundlegende Methode des Laserschneidens kaum verändert. Beim Schneiden von Weichstahl wird der Laserstrahl typischerweise auf oder nahe der Werkstückoberfläche fokussiert und von einem koaxialen Strom aus Sauerstoffhilfsgas umgeben. Typischerweise werden Laserleistungen von bis zu 3 kW zum Schneiden von Weichstahl mit Dicken von 12 bis 15 mm eingesetzt, während dickere Platten im Allgemeinen mit Plasma- oder Autogensystemen geschnitten werden. Obwohl CO2-Laser in der Lage sind, Metalle mit einer Dicke von bis zu 40 mm zu schneiden, nehmen Schnittqualität und Reproduzierbarkeit mit zunehmender Dicke erheblich ab [3].
Herausforderungen beim Schneiden dickerer Materialien
Ein Ansatz zum Schneiden dickerer Weichstahlplatten besteht darin, die Laserleistung zu erhöhen. Diese Methode bietet zwar mehrere Vorteile, bringt aber auch erhebliche Herausforderungen mit sich. Bei höheren Leistungen (3,5 kW und mehr) kann die Strahlqualität instabil werden, was die Lebensdauer optischer Komponenten verkürzt, die Geräte- und Betriebskosten erhöht und die Schnittpräzision beeinträchtigt. Wie in [4] gezeigt, bleibt die Schnittbreite bei einer gegebenen Oberflächengüte zwar ungefähr konstant, die Schnittgeschwindigkeit nimmt jedoch nicht direkt proportional zur Materialdicke ab, was auf einen Rückgang der Schneideffizienz bei zunehmender Materialdicke hindeutet.
Diese Verringerung der Schneidleistung bei zunehmender Materialdicke wird auf die abnehmende Fähigkeit des Hilfsgases zurückgeführt, das geschmolzene Material zu scheren. Mit zunehmender Dicke muss auch der Druck des Hilfsgases erhöht werden, um das geschmolzene Material wirksam zu entfernen. Bei Sauerstoff als Hilfsgas erfordert die exotherme Reaktion, die im Schnittspalt auftritt, jedoch eine Reduzierung des Sauerstoffdrucks bei zunehmender Materialdicke, um übermäßiges Brennen und Überreaktionen zu verhindern. Daher ist die Regelung des Sauerstoffdrucks von entscheidender Bedeutung, um unkontrolliertes Brennen außerhalb des erhitzten Bereichs zu vermeiden. Dadurch entsteht ein Widerspruch in den Anforderungen: Während eine Erhöhung der Laserleistung die Schneidleistung verbessern kann, reicht sie nicht aus, um die Einschränkungen zu überwinden, die sich aus der notwendigen Regelung des Sauerstoffdrucks ergeben. Dies stellt ein Hindernis für das Erreichen größerer Schnittdicken dar, trotz des Potenzials einer höheren Laserleistung.
Alternative Methoden zum Schneiden von dickem Stahl
Um die Einschränkungen durch die zunehmende Laserleistung zu überwinden, wurden zahlreiche Techniken entwickelt, um die Schneidleistung bei zunehmender Dicke von Weichstahl aufrechtzuerhalten oder zu verbessern. Einige dieser Methoden sind: Laserbrennschneiden [5], Doppelfokuslinsen [6], Strahlsägen mit adaptiver Optik [7], Laserschneiden mit einer koaxialen (ringförmigen) Düse [8], Doppelstrahl-CO2-Laserschneiden [9], rotierende Laserstrahlen [13, 14] und laserunterstütztes Sauerstoffschneiden (Lasox©) [10 – 12].
Wobbeln und sauerstoffdominiertes Nd:YAG-Laserschneiden
In früheren Arbeiten haben wir über das Schneiden dickerer Weichstahlplatten mit einem rotierenden Nd:YAG-Laserstrahl berichtet [14]. In dieser Studie untersuchen wir den Einsatz eines fasergeführten Nd:YAG-Lasers mit einem taumelnden Strahl (eine Technik, die dem Rotieren des Strahls ähnelt) und der sauerstoffdominierten Laserschneidmethode, die dem Lasox-Schneiden ähnelt [10, 11, 12]. Versuche zum sauerstoffdominierten Nd:YAG-Laserschneiden wurden zunächst mit niedrigem Sauerstoff-Hilfsgasdruck und dann mit hohem Sauerstoffdruck durchgeführt.
Mit diesem neuartigen Ansatz sollen die Herausforderungen beim Schneiden von dickem Weichstahl bewältigt werden, indem die Effizienz des Materialabtrags verbessert und gleichzeitig die Probleme im Zusammenhang mit dem Hilfsgasdruck und der Strahlstabilität gelöst werden.
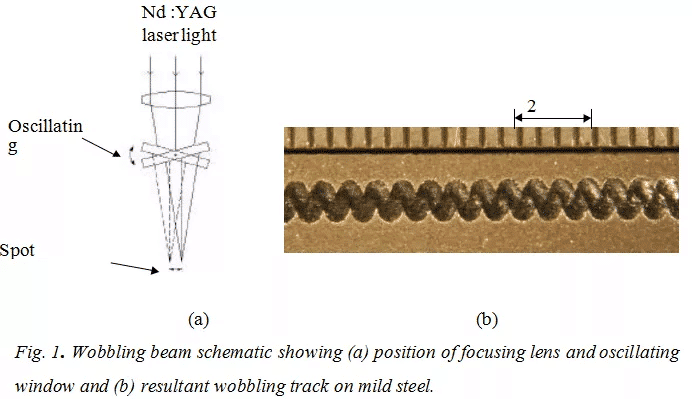
2.2 Schneiden von Stählen mit dem laserunterstützten sauerstoffdominierten Verfahren
Die Methode des laserunterstützten Sauerstoffschneidens wurde an AS3678-Weichstahlplatten mit einer Dicke von 16 bis 50 mm angewendet. Der Sauerstoff-Hilfsgasdruck wurde entweder auf weniger als 120 kPa (Niederdruck-Sauerstoffschneiden – LoPOx) oder auf hohen Druck (Hochdruck-Sauerstoffschneiden – HiPOx) gehalten. Die Schneidergebnisse wurden als Funktion der Schnittqualität (Schnittstreifen, Schnittform, übermäßige Bartbildung) und der Schnittgeschwindigkeit aufgezeichnet.
Ergebnisse
3.1 Wackeln des Laserstrahls.
Durch Taumeln des Strahls auf dem Werkstück konnte die maximale Schnittdicke von 12 mm, die beim konventionellen Schneiden erreicht wurde, auf 16 mm erhöht werden. Ein Diagramm der maximalen Schnittgeschwindigkeit für verschiedene Dicken und Laserleistungen (siehe Abbildung 2) zeigt, dass die Schnittdicke zwar mit dem Taumelstrahl verbessert wurde, die Schnittgeschwindigkeit jedoch der des konventionellen (CW-)Schneidens ähnelt. Dies deutet darauf hin, dass der Schneidprozess innerhalb des Schnittspalts beim Taumelstrahlschneiden unverändert bleibt. Ähnliche Schnittgeschwindigkeiten wurden auch mit dem rotierenden Strahl erreicht [14].
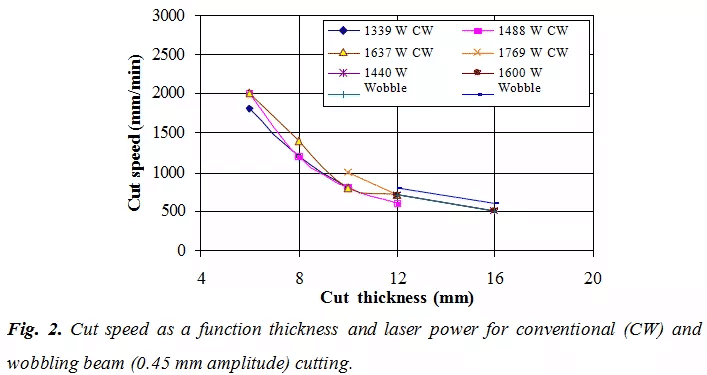
Die erhöhte Schnittdicke kann auf die größere Schnittbreite zurückgeführt werden. Dies wird durch Variation der Taumelamplitude demonstriert, wie in Abbildung 3 gezeigt. Hier wird die Schnittbreite reduziert, wenn die Taumelamplitude stufenweise von einer maximalen Amplitude von 0,45 mm auf Null reduziert wird, was einer Verringerung der Fähigkeit entspricht, die Schmelze zu entfernen. Dies zeigt deutlich, wie wichtig eine ausreichende Schnittbreite ist, damit die Schlacke entfernt werden kann. Diese Ansicht wird auch von anderen vertreten [12], wo darauf hingewiesen wird, dass sowohl die Strömungsdynamik als auch die Thermodynamik durch schmale Schnitte eingeschränkt werden.
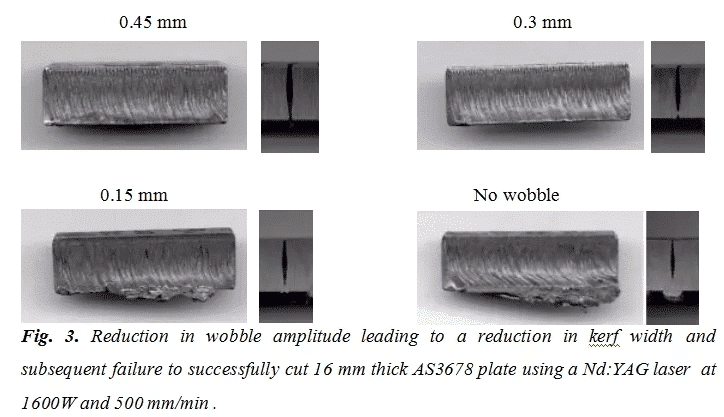
3.2 Schneiden von Stählen mit dem laserunterstützten sauerstoffdominierten Verfahren
3.2.1 Sauerstoffdominiertes Schneiden bei niedrigem Druck – LoPOx
Beim LoPOx-Schneidverfahren wird der gleiche Laserstrahl mit größerem Durchmesser und der gleiche schmale Sauerstoffstrahl auf der Oberseite des Werkstücks verwendet wie beim Lasox-Verfahren, allerdings mit einem Hilfsgasdruck unter 120 kPa. Die in Abbildung 4 mit dem LoPOx-Verfahren gezeigten Schnittflächen zeigen, dass niedrige Laserleistungen das Laserschneiden nicht behindern, solange der Schnitt primär und fortlaufend eingeleitet werden kann. Tatsächlich kann die Laserleistung bei zunehmender Schnittgeschwindigkeit zu viel Energie beitragen und daher zu übermäßiger Streifenbildung führen. Dies wird in der Abbildung durch Beobachtung der Schnittgeschwindigkeit von 450 mm/min demonstriert, bei der mit 533 W Laserleistung eine bessere Oberfläche erzeugt wurde als mit 1420 W.
W. Hier wird die Geschwindigkeit der exothermen Reaktion durch die Schnittgeschwindigkeit bestimmt. Die einfallende Laserleistung ist nur erforderlich, um die obere Oberfläche auf über 1000 °C zu erhitzen [11] und den reaktiven Schmelzprozess einzuleiten. Übermäßige einfallende Laserleistung verringert die Schnittqualität. Dies zeigt, dass Fragen der Sauerstoff-Eisen-Wechselwirkung und nicht die einfallende Laserleistung jetzt in erster Linie die Schnittqualität bestimmen. Daher handelt es sich hierbei um einen sauerstoffdominierten Laserschneidprozess.
In Abbildung 4 ist bei jeder Schnittgeschwindigkeit die Leistung reduziert, und ein erster Hinweis auf eine minimale Leistung ist der schlechte Schnittbeginn, wie am rechten Ende zu sehen. Dies zeigt, dass der Leistungsbedarf beim Schnittbeginn höher ist als der des laufenden Schneidprozesses, und dass die Leistung, die für die schnelle Etablierung eines gleichmäßigen Schneidprozesses erforderlich ist, und nicht die Leistung für den laufenden Prozess das entscheidende Kriterium ist.
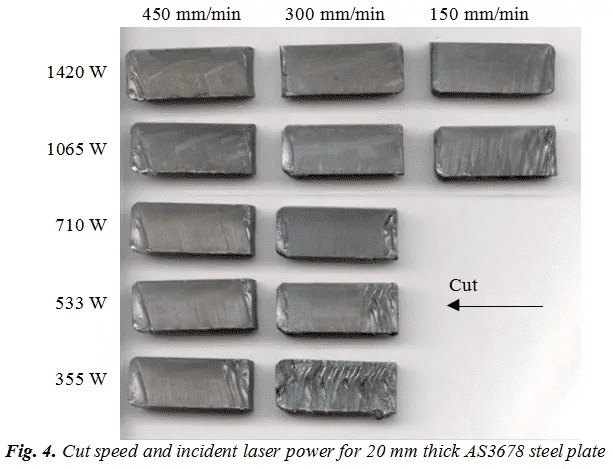
Beim LoPOx-Schneiden mit einem kleineren Durchmesser der koaxialen Düse für Material gleicher Dicke werden die gleichen Schnittgeschwindigkeiten erreicht, jedoch mit einer schmaleren Schnittbreite und folglich einem reduzierten Sauerstofffluss. Die hochwertigen Schnitte konnten jedoch bei den niedrigeren Laserleistungen mit dem größeren Düsendurchmesser in Abbildung 4 nicht erreicht werden. Dies trotz eines intensiveren Laserflecks als Folge des Durchgangs durch eine Düse mit kleinerem Durchmesser. Dies zeigt, dass die Anforderung eines ausreichend breiten Schnitts, damit die Schlacke entfernt werden kann, auch für den sauerstoffdominierten Schneidprozess gilt.
Die Seiten des Schnitts sind stärker verjüngt als beim konventionellen (laserdominierten) Schneiden. Da der Schneidprozess von Sauerstoff dominiert wird, wird der Schnitt durch die Form des auftreffenden Sauerstoffstrahls beeinflusst, wobei die Oberseite des Schnitts die gleiche Breite wie die verwendete Koaxialdüse hat.
Der Abstand zwischen Düse und Werkstück wurde variiert. Typische Ergebnisse dieser Variation sind in Abbildung 5 dargestellt. Bei verschiedenen Düsendurchmessern verringerte sich die Schnittqualität signifikant, wenn der Abstand größer als 25% des Düsendurchmessers war. Bei einer Vergrößerung des Abstands zwischen Düse und Werkstück wurde ein größerer Teil des Düsenstroms den umgebenden atmosphärischen Gasen ausgesetzt, bevor er in den Schnitt eintrat [8]. Die Änderung des Abstands wurde ohne entsprechende Änderungen des Laserspotdurchmessers vorgenommen, mit ähnlichen Ergebnissen. Dies zeigt weiter, dass Änderungen des Hilfsgases und nicht der einfallenden Laserleistung der Faktor waren, der die Laserschnittqualität im getesteten Bereich beeinflusste. Abbildung 5 zeigt auch die Auswirkung eines zu kleinen Abstands (0,1 mm), bei dem der konvergierende Strahl den Durchmesser des Gasstrahls noch nicht überschreitet und deshalb der sauerstoffdominierte Laserschneidprozess nicht zugelassen wird.
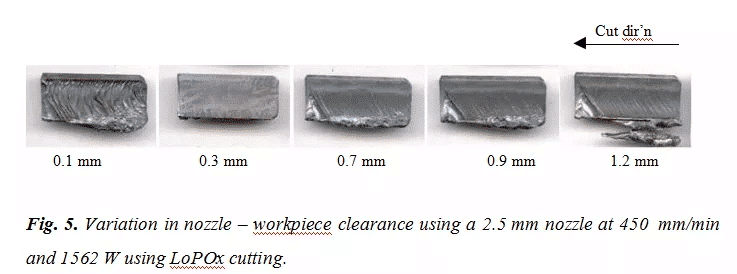
Mit Nd:YAG LoPOx-Schneiden wurde eine maximale Schnittdicke von 32 mm erreicht. Beim Schneiden über diese Dicke hinaus mit den verwendeten Düsendurchmessern kam es zur Bildung von übermäßiger Bartbildung im Schnitt und zu einem Verlust der Rechtwinkligkeit des Schnitts. Dies verdeutlicht weiter die Beziehung zwischen Schnittbreite und Schnittdicke bei Verwendung niedriger (konventioneller) Schneiddrücke.
3.2.2 Sauerstoffdominiertes Nd:YAG-Laserschneiden bei hohem Druck – HiPOx
Durch Verwendung eines viel höheren Versorgungsdrucks und kleinerer Düsendurchmesser konnte Stahl mit einer größeren Dicke geschnitten werden als zuvor mit dem LoPOx-Verfahren. Die Schnittkapazität lag bei einer Stahlplatte aus AS 3679 zwischen 32 und 50 mm Dicke. Typische Schnittgeschwindigkeiten in Bezug auf Materialdicke und Laserleistung sind in Abbildung 1 dargestellt.
6. Die Abbildung zeigt eine Fortsetzung der Schneidprozesse aus dem Niederdruckbereich, die für dünnere Materialien verwendet werden.
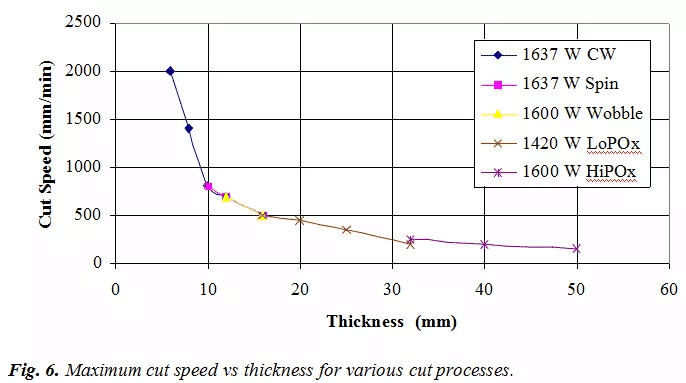
Die Verwendung hoher Förderdrücke führt zu einem komplexen Gasfluss, der zu inneren Stoßerscheinungen führen kann. Hinweise auf die Interaktion der Stoßstrukturen beim Schneiden sind als „Grate“ oder feinere Markierungen auf der Schnittfläche sowie als senkrecht zu den Riefen verlaufende Linien zu erkennen. Die Verschiebung dieser Grate mit dem Abstand zwischen Düse und Werkstück ist außerdem eine Folge der Verstärkung oder Aufhebung der inneren Stöße des Hilfsgases und des charakteristischen Stoßes, der in Form eines „X“ zu Beginn des Schnitts auftritt [15]. Arbeiten [16, 17] weisen auch auf eine komplexe und manchmal oszillierende Interaktion der Stöße mit den Schnittwänden hin. Ein Hinweis auf die oszillierende Natur des Schnitts ist das gleichmäßige „Summen“, das unter manchen Schneidbedingungen zu hören ist.
Bei Verwendung einer Koaxialdüse mit 1,5 mm Durchmesser erwies sich die Schneidleistung für 32- und 40-mm-Platten als zufriedenstellend. Die Ergebnisse beim Schneiden von 40-mm-Platten sind in Abbildung 7 dargestellt. Der Abstand zwischen Düse und Werkstück wurde durch den hohen Hilfsgasdruck deutlich vergrößert und die Form des Schnitts war aufgrund des weniger divergierenden Hochgeschwindigkeitsgasstroms weit weniger konisch als bei LoPOx. Solche Schnitte sind in Abbildung 8 zu sehen.
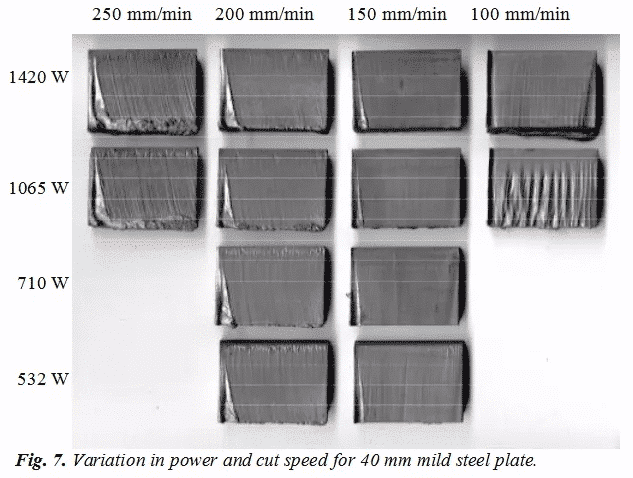
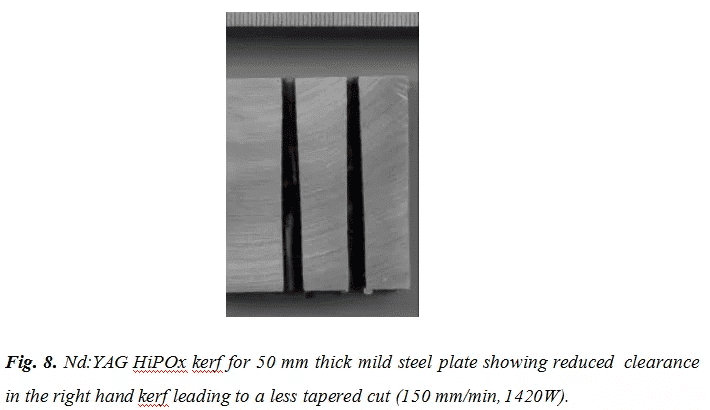
Profilschneiden mit der faserverstärkten Nd:YAG LoPOx-Technik ist anhand der in Abbildung 9 gezeigten Beispiele möglich. Hier führen Temperaturerhöhungen an der Innenseite der Ecken zu einer stärkeren Verjüngung an diesen Stellen. Dies ist am kreisförmigen Schnitt in Abbildung 9 (a) und am Unterschneiden der Ecken in Abbildung 9 (b) zu sehen. Das Unterschneiden scharfer Ecken lässt sich am besten durch die Verwendung reduzierter Schnittgeschwindigkeiten vermeiden, wie in der Abbildung gezeigt.
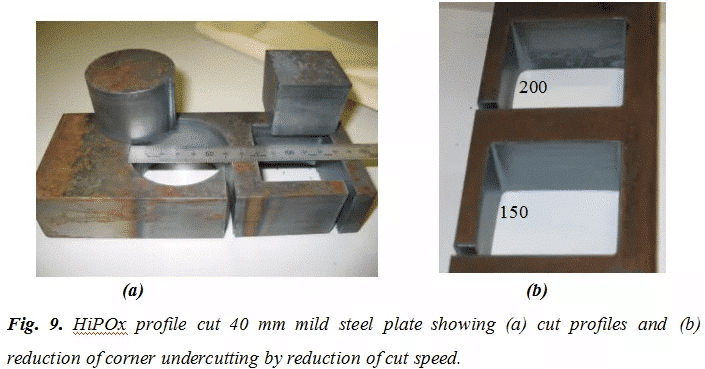
Das Schneiden mit Sauerstoff unter hohem Druck unter Verwendung des Nd:YAG-Lasers, wie er auch mit dem CO2-Laser [12] verwendet wird, erweist sich ebenfalls als hervorragend beim Durchstechen, da weniger als eine Sekunde zum Durchstechen einer 32 mm dicken AS3679-Platte erforderlich ist. Das Entfernen der nach oben ausgeworfenen Schlacke bleibt ein Problem, da ihre Anwesenheit auf der Plattenoberfläche im Schnittpfad die Schnittqualität beeinträchtigt.
Diskussion
Herausforderungen beim Schneiden dicker Stahlplatten
Trotz der neuen Fortschritte bei Laserschneidtechniken und der Möglichkeit, dickere Materialien zu schneiden, bleibt der grundlegende Schneidprozess weitgehend unverändert. Dies zeigt sich an der Verringerung der Schneidgeschwindigkeit bei zunehmender Materialdicke sowie an den gleichbleibenden Schneidgeschwindigkeiten, die bei herkömmlichen Verfahren sowie Verfahren mit rotierendem und taumelndem Strahl beobachtet werden. In allen Fällen stellen die Hauptfaktoren, die das Schneiden dicker Stahlplatten durch reaktives Schmelzen bestimmen – wie Wärmeverluste durch Wärmeleitung und Einschränkungen bei der Entfernung des Schmelzflusses aufgrund von Viskosität und Oberflächenspannung – weiterhin erhebliche Herausforderungen dar. Diese Faktoren lassen sich selbst mit der Entwicklung neuer Schneidverfahren nicht leicht überwinden.
Die Rolle der Schnittbreite und des Sauerstoffverbrauchs
Die unterschiedlichen Schnittbreiten, die durch das Taumeln des Laserstrahls entstehen, sowie die beim sauerstoffdominierten Laserschneiden mit dem Nd:YAG-Laser erzeugten Schnittbreiten unterstreichen die Notwendigkeit entsprechend breiter Schnitte bei zunehmender Materialdicke. Bei mäßigen Materialdicken (~32 mm) ist es jedoch aufgrund des prohibitiven Sauerstoffverbrauchs unpraktisch, den Schnitt über den von der größten LoPOx-Düse erzeugten Wert hinaus zu vergrößern.
In diesem Zusammenhang ist die Verwendung von HiPOx (Hochdrucksauerstoff) bietet eine vielversprechende Lösung. Der unter hohem Druck und hoher Geschwindigkeit stehende Hilfsgasstrom trägt dazu bei, die Vermischung von Sauerstoff mit atmosphärischen Gasen zu reduzieren, sodass mehr Sauerstoff für den reaktiven Schmelzprozess zur Verfügung steht. Darüber hinaus erzeugt der erhöhte Druck deutlich höhere Scherkräfte auf das geschmolzene Material und unterstützt so die Entfernung der Schmelze aus dem Schnitt. Ein weiterer Vorteil der HiPOx-Technik ist der große Abstand zwischen Düse und Werkstück, der den zuverlässigen Betrieb von Hochdruckdüsen gewährleistet, insbesondere beim Schneiden dicker Materialien.
Laserleistungsbedarf beim sauerstoffdominierten Schneiden
Beim sauerstoffdominierten Schneiden kommt es in erster Linie auf die einfallende Laserleistung an, um den Schnitt einzuleiten und aufrechtzuerhalten. Die Ergebnisse dieser Studie zeigen, dass die für das sauerstoffdominierte Schneiden erforderliche Laserleistung wesentlich geringer ist als die für das konventionelle Laserschneiden. Obwohl die zum Aufrechterhalten eines gleichmäßigen Schnitts erforderliche Leistung geringer ist, sind anfänglich höhere Leistungen erforderlich, um den Schnitt zu etablieren. Sobald der Schnitt eingeleitet ist, kann die Laserleistung auf ein Niveau reduziert werden, das den Schneidvorgang aufrechterhält. Dies deutet darauf hin, dass eine Leistungssteigerung zu Beginn des Schnitts die Gesamtschneideeffizienz maximieren könnte, indem eine höhere Leistung nur dann eingesetzt wird, wenn sie zum Einleiten erforderlich ist.
Profilschneiden und Eckenunterschneiden
Das Profilschneiden mit dem sauerstoffdominierten Nd:YAG-Laserverfahren hat sich als machbar erwiesen. Ein häufiges Problem ist jedoch das Unterschneiden an den Innenecken des geschnittenen Profils. Dieses Problem kann durch sorgfältiges Programmieren der Schnittgeschwindigkeit an diesen spezifischen Positionen behoben werden, um übermäßigen Materialabtrag zu vermeiden und saubere Schnitte sicherzustellen.
Piercing- und Krätzemanagement
Das Durchstechen dicker Stahlplatten mit einem Nd:YAG-Laser ist ebenfalls möglich, allerdings ergeben sich beim Durchstechen Probleme durch das Aufwärtsausstoßen von geschmolzener Schlacke während des Durchstechens. Diese Schlacke kann die Zufuhr von Hilfsgas beim nachfolgenden Schneiden beeinträchtigen, was zu einer schlechten Schnittqualität führt. Eine Lösung für dieses Problem könnte die Einführung eines nach außen gerichteten ringförmigen Luftstrahls sein, der die Düse umgibt und dabei hilft, die Schlacke vom Schnitt wegzuleiten. Alternativ könnte das Problem durch die Programmierung eines CNC-Wartebefehl nachdem alle Durchstechvorgänge abgeschlossen sind, sodass genügend Zeit bleibt, um ausgeworfene Schlacke zu entfernen, bevor der Schneidvorgang fortgesetzt wird. Dies trägt dazu bei, einen konstanten Hilfsgasfluss aufrechtzuerhalten und die Gesamtschneidleistung zu verbessern.
Abschluss
Sauerstoffdominiertes Laserschneiden in Verbindung mit breiteren Schnittbreiten erweist sich als praktikable Methode für die Verwendung eines mittelstarken, fasergespeisten Nd:YAG-Lasers zum Schneiden von dicken Weichstahlplatten. Diese Technik eignet sich zum Schneiden von Weichstahl mit einer Dicke von bis zu 32 mm bei Niederdruckgaszufuhr. Bei größeren Dicken ermöglicht die Hochdruckgaszufuhr das Schneiden von bis zu 50 mm dickem Stahl und ermöglicht gleichzeitig ein schnelles Durchstechen des Materials. Es bestehen jedoch weiterhin Herausforderungen bei der Erzielung einer gleichmäßigen Schnittqualität, insbesondere im Hinblick auf Stoßartefakte und Unterschnitte an Ecken, die durch präzises CNC Programmierung. Darüber hinaus muss zum erfolgreichen Durchstechen dickerer Platten die Entfernung ausgeworfener Schlacke kontrolliert werden, um sicherzustellen, dass der Hilfsgasfluss nicht behindert wird und so während des restlichen Schneidprozesses eine hohe Schnittqualität aufrechterhalten wird.