What Is an Electro-hydraulic Servo Press Brake
An electro-hydraulic servo press brake is a specific type of press brake used in metalworking and fabrication processes, particularly for bending sheet metal. It combines electrical, hydraulic, and servo control systems to precisely control the bending operation.
CNC press brake electro-hydraulic servo system is a kind of automatic control system established according to the principle of hydraulic transmission by using electro-hydraulic servo mechanism. In this system, the movement of the actuator changes with the change of the control signal.
With the increasing development of technology, modern sheet metal processing, especially the bending process requirements are increasingly high, there are different technical needs for equipment and processing efficiency, and for environmental protection and energy saving, both enterprises and the state have strict control, so compared to hydraulic bending machine, electro-hydraulic servo system control bending machine is increasingly accepted by major customers.
Components and Function
Electro-Hydraulic System: This press brake utilizes both electrical and hydraulic power systems. The electrical system typically includes components such as a motor and control unit, while the hydraulic system comprises pumps, valves, cylinders, and reservoirs for hydraulic fluid.
Servo Control: The servo control system plays a crucial role in achieving precise bending angles and positioning. Servo motors are used to control the movement of the ram (the bending component) and the back gauge (which positions the workpiece). Servo control ensures accurate and repeatable bending operations.
Press Brake Structure: Like other press brakes, the electro-hydraulic servo press brake consists of a sturdy frame, a movable upper beam (ram), and a lower bed with a V-shaped groove or die. The sheet metal to be bent is placed between the upper and lower tools.
Operation: When a bending operation is initiated, the servo-controlled hydraulic system applies force to the ram, causing it to descend and exert pressure on the sheet metal. The amount of force applied is determined by factors such as material thickness, type, and desired bend angle. The servo control system precisely regulates the movement of the ram to achieve the desired bending result.
Control Systems: Electro-hydraulic servo press brakes are equipped with advanced control systems that allow operators to input bending parameters with high precision. These control systems often feature user-friendly interfaces, such as touchscreen panels or computer numerical control (CNC) systems, enabling easy programming and operation.
Safety Features: Safety is paramount in industrial machinery, and electro-hydraulic servo press brakes are equipped with various safety features to protect operators and prevent accidents. These may include safety light curtains, interlocks, emergency stop buttons, and guards around moving parts.
Advantages: Electro-hydraulic servo press brakes offer several advantages over conventional hydraulic or mechanical press brakes. These include higher accuracy, faster setup times, reduced energy consumption, quieter operation, and the ability to perform complex bending sequences with multiple bends.
Working Principle
Electro-hydraulic servo valve is a kind of automatic control valve, which is both electro-hydraulic conversion component and power amplifier component. Its function is to convert small power analog signal input into high power hydraulic energy flow and pressure output with the change of electric signal size and polarity, and fast response, so as to realize the control of hydraulic actuator displacement, speed, acceleration and force. The electro-hydraulic servo valve is usually composed of an electrical and mechanical converter, a hydraulic amplifier and a detection feedback mechanism.
The compact design eliminates the need for external piping, and the system is mounted directly on the cylinder, making it cleaner and leak-free compared to electric drives alone.
The system converts the electrical signal from the CNC controller into a mechanical linear motion. To accomplish this motion, signals are transmitted between the machine's CNC controller and the motor drive controller. The synchronous cylinders control the tracking and fast running according to a predefined working curve. A speed-controlled servo pump unit is used to drive and control the position of the bending tool and the bending force during the bending process.
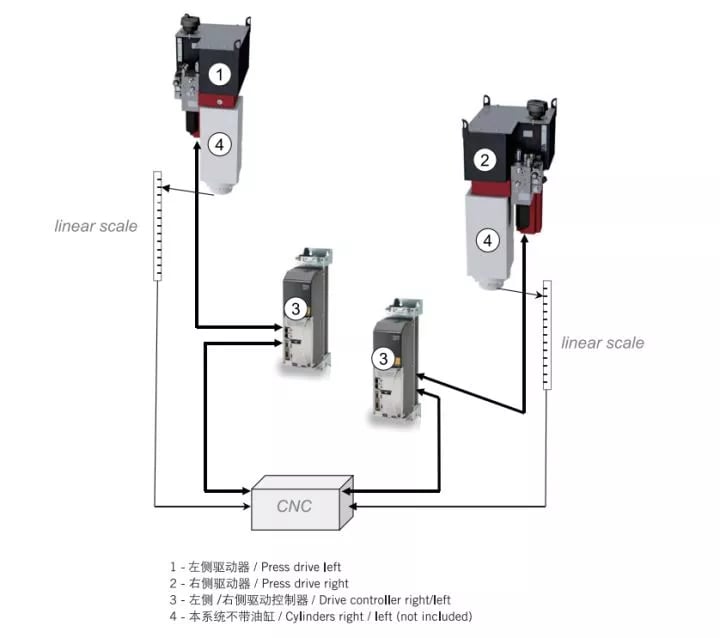
Advantages
The electro-hydraulic servo bending machine is controlled by the controller through two sets of servo bi-directional pump system to control the flow and pressure of Y1 and Y2 cylinders respectively, and the oil from the upper cavity of the cylinder is directly pumped into the lower cavity of the cylinder to realize the lifting of the upper die, and the oil pump is reversed to pump the oil from the lower cavity of the cylinder directly into the upper cavity of the cylinder to realize the sheet metal bending.
The synchronization of the left and right of the upper die of the machine is controlled by two sets of servo bi-directional pumps respectively. The machine not only has high precision, energy saving, low noise, but also is more stable and reliable, using less oil, which is conducive to the manufacture of large stroke ultra-high speed bending machine.
Summary
An electro-hydraulic servo press brake is a sophisticated machine used for bending sheet metal with high precision and efficiency. It utilizes a combination of electrical and hydraulic components, along with servo control systems, to achieve accurate and consistent bending results.