Concept
The electrohydraulic ePrAX®control press system newly developed by company close the gap between the valve controlled ePrAX® basic and the servo driven ePrAx solutions for press brakes. This systems is the consistent further deve-opment of servo driven press brake systems from China.
It is an electrohydraulic system which combines the advantages of both drive technologies: Unlike an electric drive, it is powerful and durable thanks to hydraulics, but owing to the compact design dispenses with no external oil lines, making it clean and leakage free to operate, because all the components, are compactly integrated on the cylinder.
The ePrAX®control translates the electrical input from the machine controller (CNC) in to mechanical linear motion*.To accomplish this, the machine controller communicates with the axis controller and subsequently with the motor controller.The synchronized cylinders follow preselected profiles,consisting of a working motion or a rapid motion, using controlled tracing. The drive controls the position of the bending tool - and its force during stamping - with a speed-variable motor-pump unit.
System Principle Overview
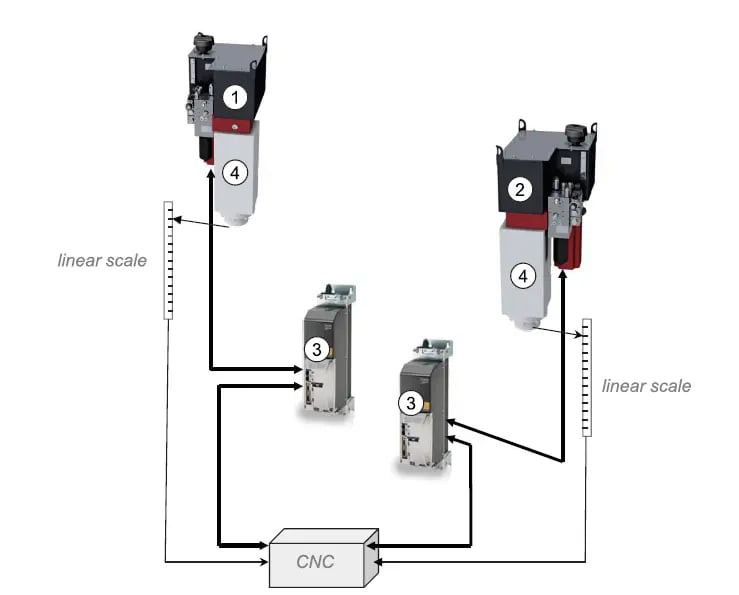
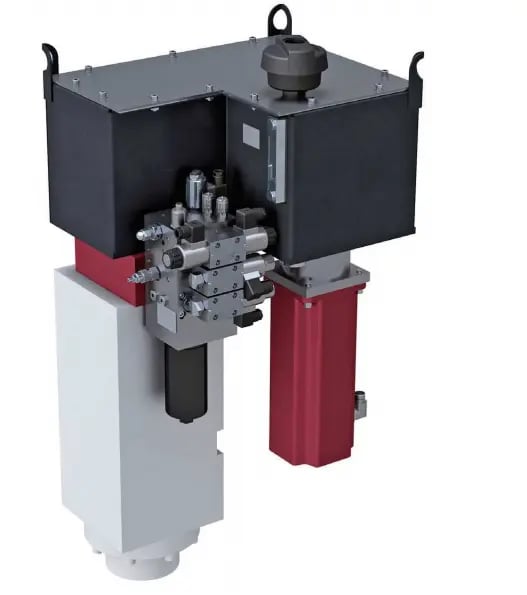
Customer Benefits
The ePrAX®control15 system is an innovative servo drive for press brakes, featuring an extremely simple cylinder interface without external tubing. The simple drive/cylinder interface ensures easy installation of the customer's cylinder. As a result, ePrAXB control offers customers the following benefits:
Fast - increased performance up to 10% by reducing thecycle time
Efficient - improving energy efficiency of up to 50 %compared to conventional systems
Precise - up to 0.005mm positioning accuracy(with high end cylinder/servo seals)
Flexible - strokes up to 400 mm realizable
Reliable - minimal risk of leakage
Whisper - reduced noise developmentin all operating modes
Compact - creates new space at themiddle traverse
Compatible - simple integration into the CNC
Cost optimized - less installation and service expenses
Environmentally friendly - considerably reduced oil volume
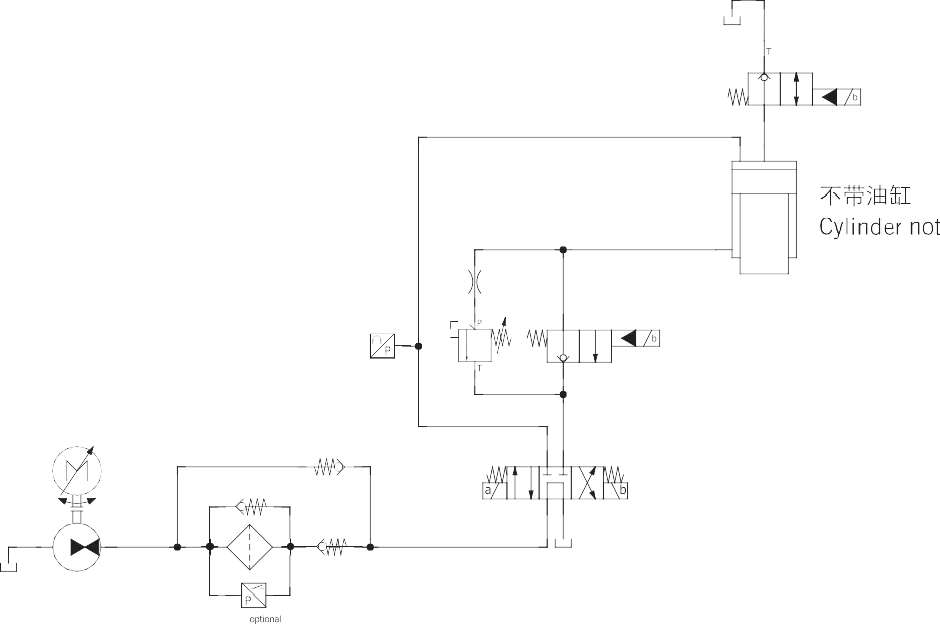
Technical Parameter of ePrAX®control
Data Per Axis | Unit | ePrAX®control15 | ePrAX®control19 |
Volumn flow | I/min | max 22.5 | max 36.5 |
Operating pressure | bar | max 320 | max 320 |
Pressing force | kN | max 550* | max 850** |
Working stroke | mm | max 400* | max 400** |
Rapid speed | mm/s | max 200* | max 200 ** |
Working speed | mm/s | 10-15*** | 10-15*** |
Drive power | kW | 6 | 10.2 |
Weight per actuator | kg | 108 | 152 |
Installation | Vertical | ||
Ambient temperature range | ℃ | 0~to +40 | |
Rust protection | / | Surface protected by protective oil tank outside surface primed | |
Interference resistance | / | EMC according DIN 55011/61000-6-2 | |
Voltage (controller) | VAC | 340~550 | |
Power dissipation (controller) | W | 280 | |
Oil Volume | I | 34.5 | 55 |
**Based on cylinder size: 188 /180 mm /with cylinder dimensions 88 /180 mm
***Pressure based/concernlng to pressing force
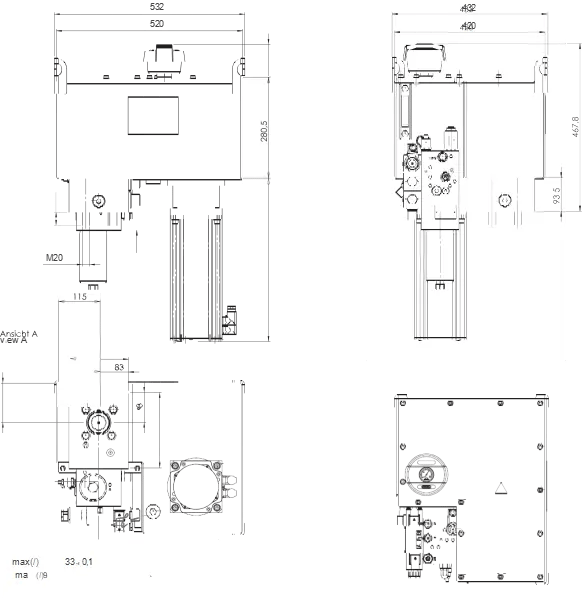
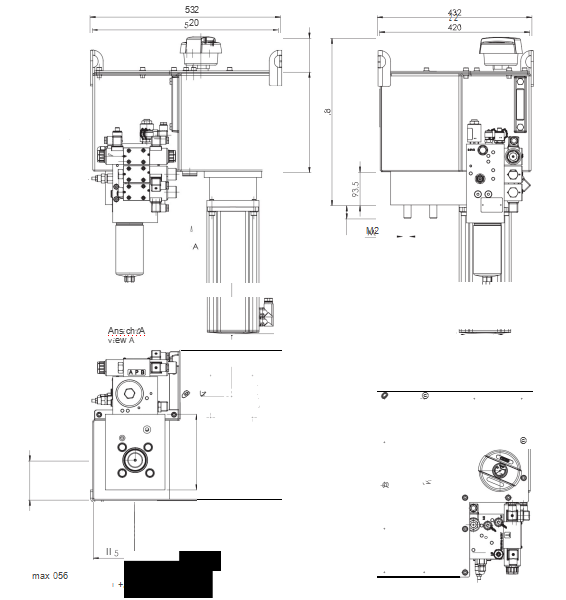
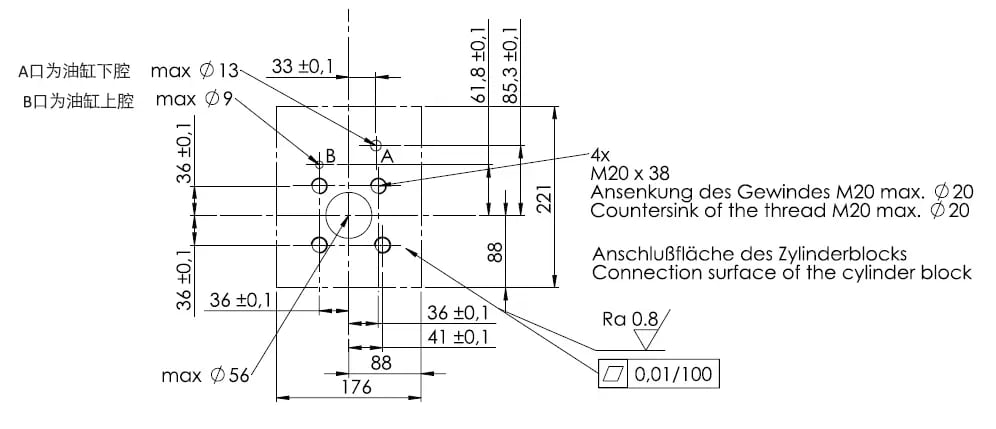
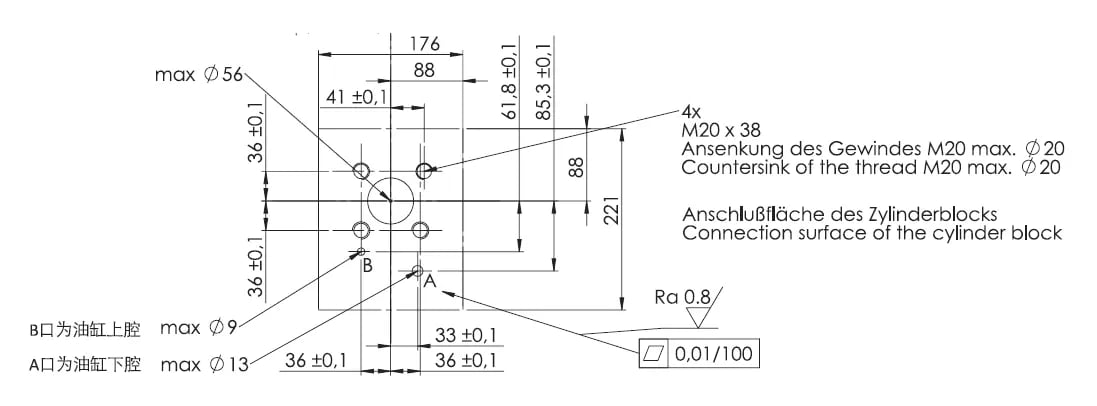
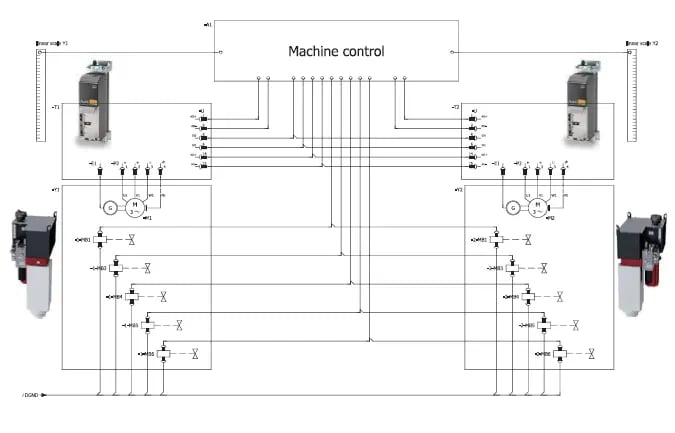
Order Instruction
Type Code
ePrAX® control | 15 | I | X | E | 320 | - | 17 | X | B2 |
1 | 2 | 3 | 4 | 5 | 6 | 7 | 8 | 9 |
Ordering Example
1 Basic version: ePrAX® control
2 Size
-15 Pressing force 550 kN per ePrAX® control@ ¢151 / ¢145 mm cylinder dimensions
-19 Pressing force 850 kN per ePrAX® control@ ¢188 / ¢180 mm cylinder dimensions
3 Bauart
-I Integriert
4 Monitoring of the valves
-X without monitored valves
5 Contamination indicator
-E electrical contamination indicator
-X without contaminiation indicator
6 Operating pressure (bar)
7 Volume flow (I/min)
8 Options
-X without option
9 Modification index
Scope of Delivery
■Servo drives:
-Leftand rightservo drives (without cylinder)
■Electrical assembly:
-Drive control system with shroud
-Line filter
-braking resistance
■CabIing,separate order option
-2 motor cables
-2 resolver cables