Compra máquina plegadora Es una inversión necesaria en una fábrica de procesamiento de chapa metálica, por lo que es muy importante que todos los clientes sepan cómo elegir una prensa plegadora que pueda doblar perfectamente las piezas de trabajo. Este artículo presenta cinco puntos de atención que los clientes deben conocer antes de comprar máquinas plegadoras.
Piezas de trabajo
El primer punto importante a tener en cuenta es la pieza de trabajo que los clientes quieren producir, y el objetivo de todos los clientes es comprar una prensa plegadora que pueda completar la tarea de plegado con la mesa más corta y el menor tonelaje. Para elegir el modelo de máquina que mejor se adapte a sus necesidades, los clientes deben considerar cuidadosamente los grados de material de la placa, el espesor máximo de la placa y la longitud. Si la mayor parte del trabajo es acero dulce con un espesor de 2 mm y una longitud máxima de 3000 mm, la fuerza de plegado no necesita ser mayor a 50 toneladas. Sin embargo, si está realizando una gran cantidad de conformado con troqueles de fondo, tal vez deba considerar una prensa plegadora de 160 toneladas.
Bueno, suponiendo que el espesor máximo del material es de 6 mm, la longitud máxima es de 3000 mm, la fuerza de plegado requiere 200 toneladas y el plegado con matriz de fondo (plegado corregido) requiere al menos 450 toneladas. Si la mayoría de las piezas de trabajo son de 1500 mm o menos, el tonelaje se reduce casi a la mitad, lo que reduce en gran medida el costo de compra. En este caso, la elección del modelo de máquina en función de la pieza de trabajo es muy importante.
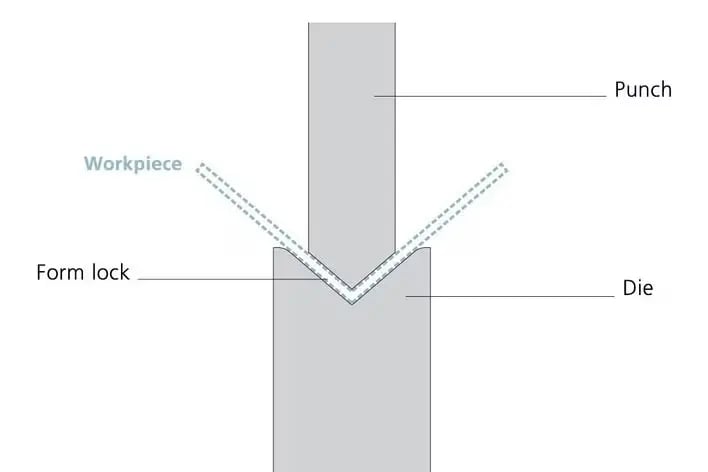
Desviación
Con la misma carga, la deflexión de la mesa y el deslizador de la máquina plegadora de 3000 mm es cuatro veces mayor que la de la máquina de 1500 mm. Dicho esto, una prensa plegadora más corta requiere menos ajuste de las cuñas para producir piezas aceptables. El ajuste reducido de las cuñas, a su vez, reduce el tiempo de configuración.
El grado del material también es un factor clave. En comparación con el acero dulce, el acero inoxidable normalmente requiere alrededor de 50% más de carga, mientras que la mayoría de los grados de aluminio blando requieren alrededor de 50% menos. Siempre puede obtener una tabla de tonelaje de la prensa plegadora del fabricante de la prensa plegadora que muestre una estimación del tonelaje necesario por pie de longitud para diferentes espesores y materiales.
La antigua prensa plegadora hidráulica NC requiere que los clientes presten mucha atención a la desviación de la mesa porque este es el punto clave que afecta la precisión del plegado, pero ahora la prensa plegadora CNC puede ajustar automáticamente la desviación mediante su controlador CNC.
Radio de curvatura de las piezas de trabajo
Al doblar las piezas de trabajo, el radio de curvatura es 0,156 veces la distancia de apertura de la matriz. Durante el proceso de doblado, la distancia de apertura de la matriz debe ser 8 veces el espesor del material metálico. Por ejemplo, al formar acero dulce de 2 mm utilizando un espacio de 12,7 mm, la pieza tiene un radio de curvatura de aproximadamente 1,98 mm. Si el radio de curvatura es casi tan pequeño como el espesor del material, se requiere un troquel de formación con fondo. Sin embargo, la presión necesaria para formar un troquel de fondo es aproximadamente 4 veces mayor que la del doblado libre.
Si el radio de curvatura es menor que el espesor del material, se debe utilizar un punzón con un radio de filete en el extremo frontal menor que el espesor del material y se debe recurrir al método de curvatura por impresión. De esta manera, se requiere 10 veces la presión de curvatura libre. Para la curvatura libre, los punzones y matrices se mecanizan a 85° o menos (cuanto más pequeño, mejor). Al utilizar este conjunto de matrices, preste atención al espacio entre el punzón y la matriz en la parte inferior de la carrera y al sobrecurvado suficiente para compensar la recuperación elástica para mantener el material alrededor de 90°.
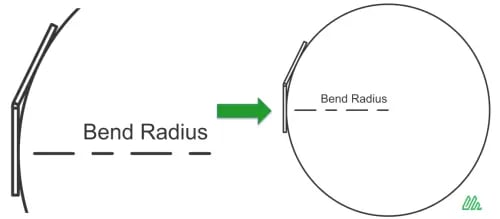
Generalmente, el ángulo de recuperación elástica producido por la matriz de doblado libre en la nueva máquina dobladora es ≤2°, y el radio de doblado es igual a 0,156 veces la distancia de apertura de la matriz. Para el doblado con matriz de fondo, el ángulo de la matriz es generalmente de 86 a 90°. En el extremo inferior de la carrera, debe haber un espacio ligeramente mayor que el espesor del material entre el punzón y el punzón. El ángulo de formación se mejora porque la matriz de fondo se dobla a un tonelaje mayor (aproximadamente 4 veces el de un plegado libre), lo que reduce las tensiones que normalmente causan la recuperación elástica dentro del radio de plegado.
El doblado por impresión es igual que el doblado por troquel inferior, excepto que el extremo delantero del punzón se procesa hasta el radio de doblado requerido y el espacio entre el punzón y la matriz en la parte inferior de la carrera es menor que el espesor del material. La recuperación elástica se evita esencialmente aplicando suficiente presión (aproximadamente 10 veces la curva libre) para forzar el extremo delantero del punzón a entrar en contacto con el material. Para seleccionar la especificación de tonelaje más baja, es mejor planificar un radio de doblado mayor que el espesor del material y utilizar el método de doblado libre siempre que sea posible. Cuando el radio de doblado es grande, la calidad de la pieza terminada y su uso futuro a menudo no se ven afectados.
Precisión de plegado de la prensa plegadora
El requisito de precisión de plegado es un factor que debe considerarse cuidadosamente. Es este factor el que determina si debe considerar una máquina plegadora CNC o una prensa plegadora hidráulica NC. Si la precisión de plegado requiere ±1° y no se puede cambiar, debe comprar una máquina plegadora CNC.
La precisión de repetibilidad del deslizador de la prensa plegadora hidráulica CNC es de ±0,01 mm, y el ángulo preciso debe formarse con dicha precisión y un buen molde. La precisión de repetibilidad del deslizador de la máquina plegadora hidráulica NC es de ±0,05 mm, y la desviación de ±2~3° generalmente ocurrirá bajo la condición de usar un molde adecuado. Además, las prensas plegadoras CNC están listas para una configuración rápida de la matriz, lo cual es una razón innegable para considerar cuando necesita doblar muchas piezas de bajo volumen.
Compra de máquinas herramienta para prensas plegadoras
Incluso si tiene un estante lleno de herramientas para prensas plegadoras, no piense que estas herramientas son adecuadas para las prensas plegadoras recién compradas. Debe asegurarse de que la altura del punzón superior y las matrices inferiores de la prensa plegadora, además de la carrera de la prensa plegadora, sean mayores que la altura de apertura de la prensa plegadora.
Para los moldes convencionales, la desviación por pie debe ser de alrededor de ±0,025 mm y la desviación de longitud total no debe ser mayor que ±0,127 mm. Para las matrices de rectificado fino, la precisión debe ser de ±0,01 mm por 25,4 mm y la precisión total no debe ser mayor que ±0,05 mm. Es mejor utilizar matrices de rectificado fino para Prensas plegadoras CNC y matrices regulares para prensa plegadora NC.
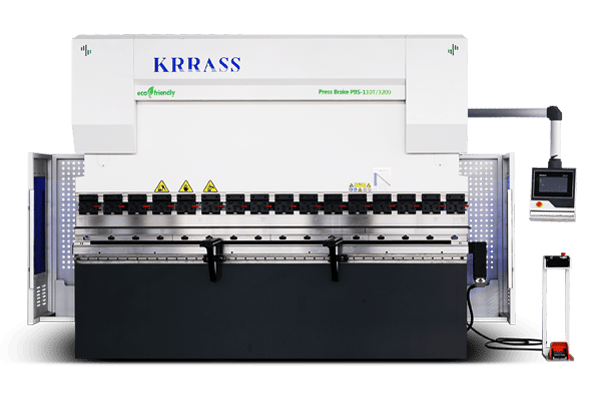
En conclusión, para comprar una máquina plegadora, es necesario que los clientes consideren las piezas de trabajo, la desviación de la prensa plegadora, el radio de curvatura, la precisión de curvatura y las herramientas de la prensa plegadora.