A prensa plegadora is a machine tool used in sheet metal fabrication to bend and shape metal sheets into various forms. It's commonly used in industries such as automotive, aerospace, construction, and manufacturing. The press brake operates by clamping the metal sheet between a matching punch and die, then applying force to bend the sheet to the desired angle. The force is typically applied hydraulically or mechanically. Press brakes come in various sizes and configurations to accommodate different sheet metal sizes, thicknesses, and bending requirements. They are essential tools for producing components with precise bends and angles in sheet metal fabrication processes.
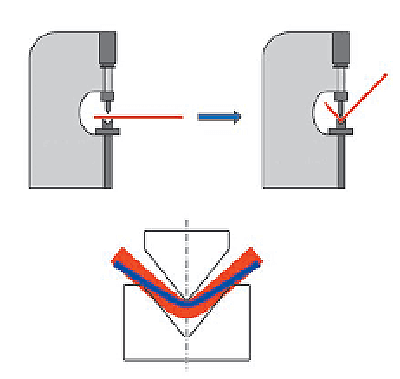
What Is NC Press Brake?
Un Prensa plegadora NC, also known as a numerical control press brake, is a type of press brake equipped with a numerical control system that allows for automated operation and precise control over the bending process.
In an NC press brake, the operator can input the desired bending parameters, such as the angle, bend length, and back gauge position, into the control panel. The machine then automatically adjusts its settings to carry out the bending operation according to the programmed instructions.
NC press brakes offer several advantages over manual or conventional press brakes, including:
1.Precision: The numerical control system allows for highly accurate and repeatable bending operations, resulting in consistent part quality.
2.Efficiency: Automated operation reduces the need for manual adjustments and setup time, leading to higher productivity and faster production cycles.
3.Versatility: NC press brakes can handle a wide range of bending tasks and can be programmed to produce complex shapes and multiple bends in a single operation.
4.Safety: Automated operation reduces the risk of operator error and minimizes the likelihood of accidents during the bending process.
What Is CNC Press Brake?
A CNC press brake, or Computer Numerical Control press brake, is an advanced type of press brake equipped with a computerized control system that precisely regulates the bending process.
In a CNC press brake, the bending parameters such as angle, bend length, and back gauge position are programmed into the machine's computer system using specialized software. The operator typically uses a graphical interface or programming language to input these parameters. The CNC system then controls the movement of the machine's hydraulic or mechanical components to execute the bending operation according to the programmed instructions.
CNC press brakes offer several advantages over manual or NC press brakes, including:
1.Precision: The computerized control system allows for highly accurate and repeatable bending operations, resulting in consistent part quality.
2.Flexibility: CNC press brakes can handle a wide range of bending tasks and can be programmed to produce complex shapes and multiple bends in a single operation.
3.Efficiency: Automated operation reduces the need for manual adjustments and setup time, leading to higher productivity and faster production cycles.
4.Integration: CNC press brakes can be integrated into larger manufacturing systems, allowing for seamless communication and coordination with other CNC machines and manufacturing processes.
Overall, CNC press brakes represent the pinnacle of technology in sheet metal fabrication, offering unparalleled precision, flexibility, and efficiency in bending operations.
¿Cómo funciona una prensa plegadora?
A press brake works by using force to bend sheet metal along a predetermined line, typically referred to as the bend line. Here's a general overview of how a press brake operates:
1.Setup: The operator first secures the sheet metal workpiece between the punch (the upper tool) and the die (the lower tool) within the press brake's workspace. The die features a V-shaped groove that matches the desired bend angle.
2.Adjustment: The operator adjusts the position of the back gauge, which helps to ensure consistent bending dimensions. This back gauge acts as a stop against which the metal is positioned for each bend.
3.Programming: In the case of CNC press brakes, the operator inputs the bending parameters, such as the bend angle, bend length, and back gauge position, into the machine's computer control system. For manual or NC press brakes, adjustments are made manually.
4.Bending: The press brake applies force to the punch, which pushes the sheet metal into the die, causing it to bend along the bend line. The amount of force applied depends on factors such as the material type, thickness, and desired bend angle.
5.Release: Once the bending operation is completed, the press brake releases the force, allowing the operator to remove the bent workpiece.
6.Inspection: The operator inspects the bent workpiece to ensure it meets the required specifications in terms of dimensions, angle, and quality.
Press brakes can perform various types of bends, including V-bends, U-bends, offset bends, and more, depending on the tooling and setup used. The process may be automated with CNC control or carried out manually, depending on the complexity of the bending task and the capabilities of the press brake.
What Is Press Brake Punch and Die?
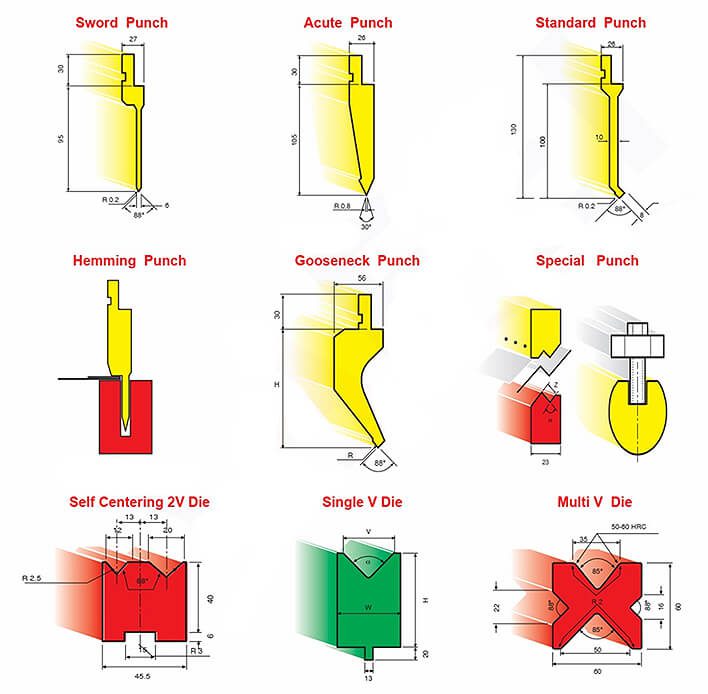
In the context of a press brake, the punch and die are the primary tooling components used to bend sheet metal. Here's a breakdown of each:
1.Press Brake Punch: The punch is the upper tool in a press brake setup. It's typically a hardened steel tool with a profiled edge that applies pressure to the sheet metal workpiece, forcing it into the die to create the desired bend. Punches come in various shapes and sizes to accommodate different bending requirements. The profile of the punch determines the shape of the bend produced in the sheet metal.
2.Press Brake Die: The die is the lower tool in a press brake setup. It's mounted onto the press brake's bed and features a V-shaped groove or channel that matches the desired bend angle. The sheet metal workpiece is positioned over the die during the bending process, allowing the punch to press the metal into the die's groove to achieve the desired bend angle. Dies also come in various sizes and configurations to accommodate different bending tasks and material thicknesses.
Together, the punch and die work in tandem to bend sheet metal along a predetermined line, known as the bend line. By selecting the appropriate punch and die combination, operators can produce a wide range of bend angles and shapes in sheet metal fabrication processes. These tooling components are critical to achieving accurate and consistent bends in sheet metal parts.