Tabla de contenido
¿Qué es una prensa plegadora?
A prensa plegadora Es una máquina herramienta que se utiliza en la metalurgia para doblar y dar forma a láminas de metal y placas. Utiliza un mecanismo hidráulico o mecánico para aplicar fuerza a una pieza de trabajo, lo que hace que se doble a lo largo de un eje recto. Las prensas plegadoras se utilizan ampliamente en diversas industrias, incluidas la fabricación, la automoción, la aeroespacial, la construcción y más.
¿Qué es una paneladora?
A máquina dobladora de paneles, también conocida como máquina plegadora o máquina plegadora de paneles, es un tipo de máquina herramienta que se utiliza en la metalurgia para doblar y plegar paneles de chapa metálica en formas específicas. A diferencia de las prensas plegadoras, que doblan principalmente chapa metálica a lo largo de un eje recto, las máquinas dobladoras de paneles están diseñadas para crear pliegues, curvas y bridas complejas en paneles de chapa metálica.
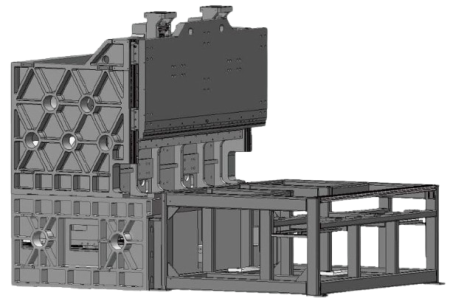
¿Cuáles son las diferencias entre ellos?
Sistema de sujeción:Las máquinas dobladoras de paneles suelen utilizar un sistema de sujeción para sujetar firmemente el panel de chapa metálica en su lugar durante el proceso de doblado. Esto garantiza pliegues precisos y uniformes sin deslizamientos.
Viga plegable:La viga de plegado, también conocida como viga de doblado o cuchilla de plegado, es la herramienta principal que se utiliza para doblar la chapa metálica. Se mueve vertical y horizontalmente para crear pliegues de diversos ángulos y formas.
Sistema de tope trasero:Al igual que las prensas plegadoras, las máquinas plegadoras de paneles pueden contar con un sistema de tope trasero para posicionar con precisión el panel de chapa metálica para el plegado. Esto garantiza la repetibilidad y la consistencia en el proceso de plegado.
Control CNC:Muchas máquinas dobladoras de paneles modernas están equipadas con sistemas de control numérico por computadora (CNC), lo que permite el funcionamiento y la programación automatizados de secuencias de doblado complejas. Las máquinas dobladoras de paneles CNC ofrecen un control preciso de los ángulos, longitudes y profundidades de doblado, así como la capacidad de almacenar y recuperar programas de doblado.
Estampación:Las máquinas dobladoras de paneles pueden utilizar varias opciones de herramientas para adaptarse a diferentes requisitos de doblado, como curvas rectas, curvas de radio, dobladillos y rebordes. Las herramientas se pueden cambiar o ajustar fácilmente para lograr diferentes configuraciones de doblado.
Cómo elegir entre las dos máquinas
La elección entre una prensa plegadora o una máquina plegadora de paneles depende de varios factores, incluidos los requisitos específicos de sus proyectos de fabricación de metales, el presupuesto, el espacio disponible y el volumen de producción. A continuación, se indican algunas consideraciones que le ayudarán a tomar la decisión:
Complejidad de flexión:Las plegadoras de paneles son ideales para proyectos que requieren pliegues, curvas y formas complejas en paneles de chapa metálica. Si sus proyectos implican geometrías intrincadas o múltiples pliegues con diferentes ángulos, una plegadora de paneles puede ser la mejor opción. Las prensas plegadoras, por otro lado, son más adecuadas para pliegues rectos y angulares más simples.
Volumen de producción:Tenga en cuenta el volumen de piezas de chapa metálica que necesita producir. Las plegadoras de paneles suelen ser más rápidas y eficientes para doblar grandes cantidades de paneles con formas complejas debido a su funcionamiento automatizado y a los rápidos tiempos de preparación. Las prensas plegadoras pueden ser más adecuadas para producciones de menor volumen o para proyectos con requisitos de plegado más sencillos.
Precisión y repetibilidad:Las máquinas dobladoras de paneles suelen ofrecer una alta precisión y repetibilidad en el plegado debido a su funcionamiento controlado por CNC y a sus herramientas precisas. Si sus proyectos requieren tolerancias estrictas y resultados de plegado consistentes, una dobladora de paneles puede ser la opción preferida. Las prensas plegadoras también pueden lograr una alta precisión con operadores expertos y una configuración adecuada, pero pueden requerir más ajustes manuales para plegados complejos.
Espacio en el piso:Tenga en cuenta el espacio disponible en su taller o planta de fabricación. Las plegadoras de paneles suelen ocupar menos espacio que las prensas plegadoras, lo que las hace adecuadas para talleres más pequeños o entornos de producción reducidos. Las prensas plegadoras pueden requerir más espacio para la configuración, el almacenamiento de herramientas y la manipulación de materiales.
Versatilidad:Las prensas plegadoras ofrecen una mayor versatilidad en términos de capacidades de plegado, ya que pueden adaptarse a una amplia gama de materiales, espesores y configuraciones de plegado. Con las herramientas y la configuración adecuadas, las prensas plegadoras pueden realizar tareas de plegado tanto simples como complejas. Las máquinas plegadoras de paneles, si bien están especializadas para el plegado de paneles, pueden tener limitaciones en términos de espesor del material y ángulos de plegado.
Costo:Tenga en cuenta su presupuesto y el costo total de propiedad, incluido el precio de compra inicial, el mantenimiento y los costos operativos. Las plegadoras de paneles tienden a ser más caras al principio debido a su tecnología CNC avanzada y sus funciones de automatización. Las prensas plegadoras pueden ofrecer una solución más rentable para operaciones de menor escala o proyectos con requisitos de plegado más simples.
En definitiva, la elección entre una prensa plegadora y una paneladora depende de sus necesidades de producción específicas, su presupuesto y sus objetivos a largo plazo. Es importante evaluar cuidadosamente sus requisitos y capacidades antes de tomar una decisión. Además, consultar con fabricantes de equipos o expertos de la industria puede brindar información y orientación valiosas para seleccionar la máquina adecuada para sus aplicaciones de fabricación de metales.
Conclusión
En resumen, si bien tanto las prensas plegadoras como las máquinas plegadoras de paneles se utilizan para aplicaciones de plegado de metales, las prensas plegadoras son más versátiles para operaciones de plegado complejas y ofrecen mayor precisión y flexibilidad. Las plegadoras de paneles son máquinas especializadas diseñadas específicamente para plegar paneles o láminas grandes con pliegues en línea recta.