En la industria de fabricación de chapa metálica, la operación de plegado suele ser un cuello de botella en el proceso de producción. La tecnología de plegado de paneles puede ayudar a los fabricantes de metales a agilizar este paso, lo que aumenta significativamente la capacidad y la velocidad de fabricación. Cuando la aplicación y el uso anual se alinean bien con la combinación de piezas, el retorno de la inversión de una Dobladora de paneles CNC Se puede realizar rápidamente.
Tabla de contenido
Tipos de dobladoras de paneles
Las plegadoras de paneles, también conocidas como máquinas plegadoras de paneles o prensas plegadoras, vienen en varios tipos, cada uno diseñado para satisfacer necesidades y requisitos de fabricación específicos. A continuación, se muestran algunos tipos comunes de plegadoras de paneles:
Dobladoras de paneles manuales: Se trata de máquinas plegadoras de paneles básicas operadas manualmente por el operario. Son adecuadas para operaciones a pequeña escala o aplicaciones donde la precisión y la velocidad no son factores críticos.
Prensas plegadoras hidráulicas: Las prensas plegadoras hidráulicas utilizan cilindros hidráulicos para ejercer fuerza sobre la herramienta de plegado, lo que permite un plegado preciso y potente de láminas de metal. Son adecuadas para una amplia gama de aplicaciones y ofrecen alta precisión y repetibilidad.
Prensas plegadoras servoeléctricas: Estas prensas plegadoras utilizan servomotores en lugar de sistemas hidráulicos para accionar el mecanismo de plegado. Ofrecen alta precisión, eficiencia energética y bajos requisitos de mantenimiento. Las prensas plegadoras servoeléctricas suelen preferirse para aplicaciones que requieren plegado a alta velocidad y formas intrincadas.
Prensas plegadoras CNC (control numérico por computadora): Las prensas plegadoras CNC están equipadas con controles computarizados que permiten un control preciso del proceso de plegado. Los operadores pueden programar la máquina para doblar láminas de metal en formas complejas con alta precisión y repetibilidad. Las prensas plegadoras CNC son muy versátiles y adecuadas para una amplia gama de aplicaciones.
Prensas plegadoras tándem: Las prensas plegadoras en tándem consisten en varias máquinas plegadoras que funcionan en tándem para aumentar la capacidad y la eficiencia de plegado. Se utilizan para doblar láminas de metal grandes y pesadas o para producciones de gran volumen.
Frenos de caja y de cárter: Las plegadoras de cajas y sartenes, también conocidas como plegadoras de dedos, son máquinas dobladoras especializadas que se utilizan para doblar láminas de metal en cajas, sartenes y otras formas complejas con lados rectos. Cuentan con dedos ajustables que permiten un doblado preciso a lo largo de múltiples ejes.
Máquinas plegadoras de paneles: Las máquinas plegadoras de paneles están diseñadas específicamente para plegar láminas de metal a lo largo de líneas rectas para crear curvas cerradas. Se utilizan a menudo en industrias como la de calefacción, ventilación y aire acondicionado, techado y automoción para la fabricación de paneles y cerramientos.
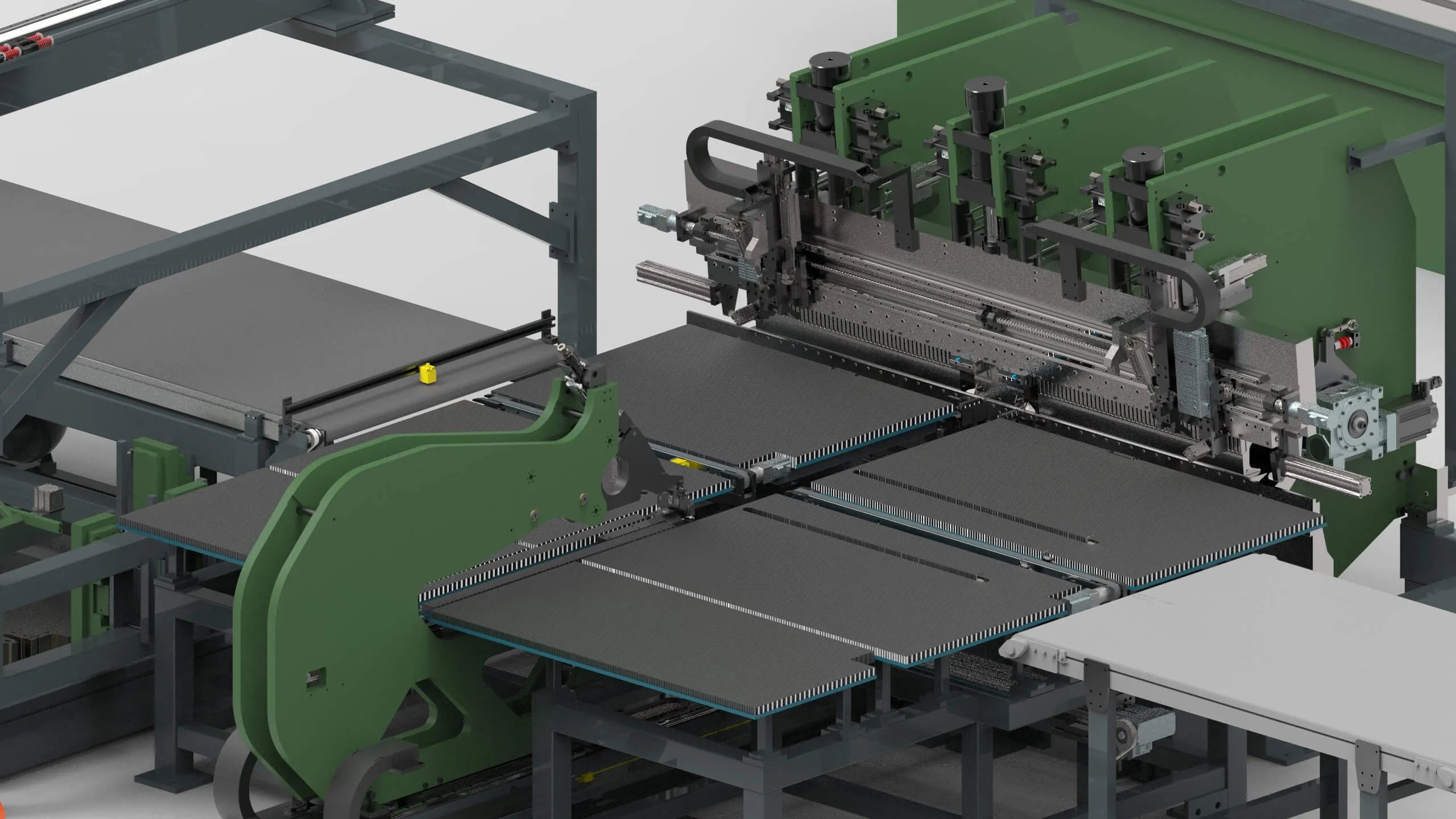
¿Qué es una máquina dobladora de paneles CNC?
A Dobladora de paneles CNC es una máquina avanzada y totalmente automatizada que utiliza programas informáticos para doblar paneles de metal en formas precisas. CNC, que significa Control Numérico por Computadora, representa lo más alto de la tecnología de doblado de paneles. Estas máquinas son especialmente adecuadas para industrias que exigen alta precisión y personalización, como la automotriz, la aeroespacial y la construcción. Las dobladoras de paneles CNC pueden trabajar con diversos materiales metálicos, espesores y formas, produciendo grandes volúmenes de productos de alta calidad y minimizando el desperdicio de material.
Las plegadoras de paneles CNC funcionan sujetando una lámina de metal en su lugar y luego utilizando un sistema mecánico o hidráulico para doblar el metal a lo largo de un eje predeterminado. El sistema de control funciona como el cerebro de la máquina, gestionando el proceso de plegado con una precisión y eficiencia excepcionales. Un software avanzado permite a los operadores establecer parámetros detallados, incluidas las secuencias y los ángulos de plegado, y almacenar programas para su uso futuro. Esta infraestructura digital garantiza la coherencia y la precisión en las tiradas de producción.
Al igual que las máquinas plegadoras CNC, las plegadoras de paneles CNC se especializan en doblar láminas de metal grandes y delgadas. Ofrecen una excelente precisión y repetibilidad, lo que las hace adecuadas para la producción de gran volumen. Los factores a tener en cuenta para las plegadoras de paneles CNC incluyen la cantidad de estaciones de plegado, las opciones de herramientas y el nivel de automatización.
¿Cómo funciona una máquina dobladora de paneles CNC?
Una paneladora CNC funciona fijando una lámina de metal entre una viga superior y otra inferior. A continuación, la máquina realiza una serie de movimientos precisos hacia arriba y hacia abajo con estas vigas para doblar el metal a lo largo de líneas predefinidas. Este proceso de doblado se gestiona mediante un software avanzado, que garantiza precisión y consistencia.
Los componentes esenciales de una plegadora de paneles CNC incluyen las vigas de sujeción, las cuchillas de plegado y una unidad de control. Las vigas de sujeción sujetan la chapa metálica, mientras que las cuchillas de plegado se mueven para crear los pliegues deseados. La unidad de control permite al operador programar patrones y ángulos de plegado específicos, lo que garantiza que cada pieza se fabrique según especificaciones exactas.
¿Cómo puede el doblado de paneles mejorar la eficiencia del doblado y la velocidad de producción?
Es un hecho ampliamente reconocido que el tiempo promedio de preparación de una prensa plegadora oscila entre 15 y 30 minutos, lo que ha llevado a muchos fabricantes de prensas plegadoras a desarrollar sistemas de cambio automático de herramientas. Este largo tiempo de preparación a menudo obliga a los fabricantes a producir en exceso para justificar los costos de preparación, lo que da como resultado un exceso de inventario, trabajo en proceso (WIP) o incluso piezas extraviadas o descartadas.
Por otro lado, las plegadoras de paneles ofrecen tiempos de preparación mucho más rápidos porque pueden utilizar herramientas comunes para manejar distintas geometrías de piezas y espesores de material. Los operarios no necesitan cambiar físicamente las herramientas entre trabajos. En cambio, simplemente deslizan las herramientas de sujeción a nuevas posiciones según sea necesario. Esto se puede hacer manualmente en unos cinco minutos o con un cambiador automático de herramientas, que reduce el tiempo de preparación a aproximadamente 90 segundos.
Esta reducción en el tiempo de preparación hace que las dobladoras de paneles sean ideales para los fabricantes que implementan principios de fabricación eficiente: producen solo lo que se necesita, cuando se necesita y minimizan el trabajo en proceso (WIP).
La tecnología de plegado de paneles funciona según el principio de la línea de transferencia, lo que garantiza que las piezas avancen continuamente a medida que las distintas estaciones trabajan simultáneamente. Al utilizar un enfoque modular, los fabricantes pueden combinar varias unidades de plegado para reducir aún más los tiempos del ciclo de plegado.
Este método es particularmente eficaz para lograr una relación 1:1 entre las operaciones de troquelado y plegado. Una vez que se alcanza esta relación equilibrada, los procesos de troquelado y plegado se pueden integrar en una única línea continua, lo que garantiza que ninguna máquina o proceso quede en espera. Además, el proceso se puede optimizar alimentando directamente las piezas terminadas al área de ensamblaje, eliminando así la manipulación adicional y el trabajo en proceso.
¿Cómo puede el doblado de paneles simplificar todo el proceso de producción?
Es importante señalar que el plegado de paneles no solo aborda el cuello de botella del plegado, sino también las operaciones posteriores. Un análisis de los diferentes procesos en un taller de fabricación de chapa metálica promedio muestra que la soldadura y el ensamblaje son, con diferencia, los procesos más costosos del taller, y uno de los principales culpables es el mal ajuste. ¿Cuánto tiempo tiene que dedicar el operador de soldadura a intentar que la pieza encaje en el dispositivo de soldadura en lugar de soldar? ¿Con qué frecuencia el operador de ensamblaje tiene dificultades para conseguir que las piezas encajen entre sí? Esto sucede con mucha frecuencia.
Las plegadoras de paneles pueden ayudar a optimizar estas operaciones posteriores al producir piezas con gran planitud y precisión. Se logra una planitud superior porque, a diferencia de una prensa plegadora con bombeo dinámico, se coloca un tonelaje mínimo a lo largo de la línea de plegado.
Las mejoras en la precisión se pueden atribuir a la forma en que se referencia la pieza. Se hace referencia a partir de un único punto de referencia, lo que elimina lo que se conoce como acumulación de error de tolerancia. Al realizar múltiples pliegues en una prensa plegadora, a menudo se requiere que el operador mida a partir de bridas previamente dobladas. Esto abre la posibilidad de que el error de tolerancia se acumule, dejando al operador de soldadura o ensamblaje como la última línea de defensa para corregir el problema. Una descripción general rápida de los departamentos de soldadura y ensamblaje es un buen punto de partida para evaluar el proceso de plegado.
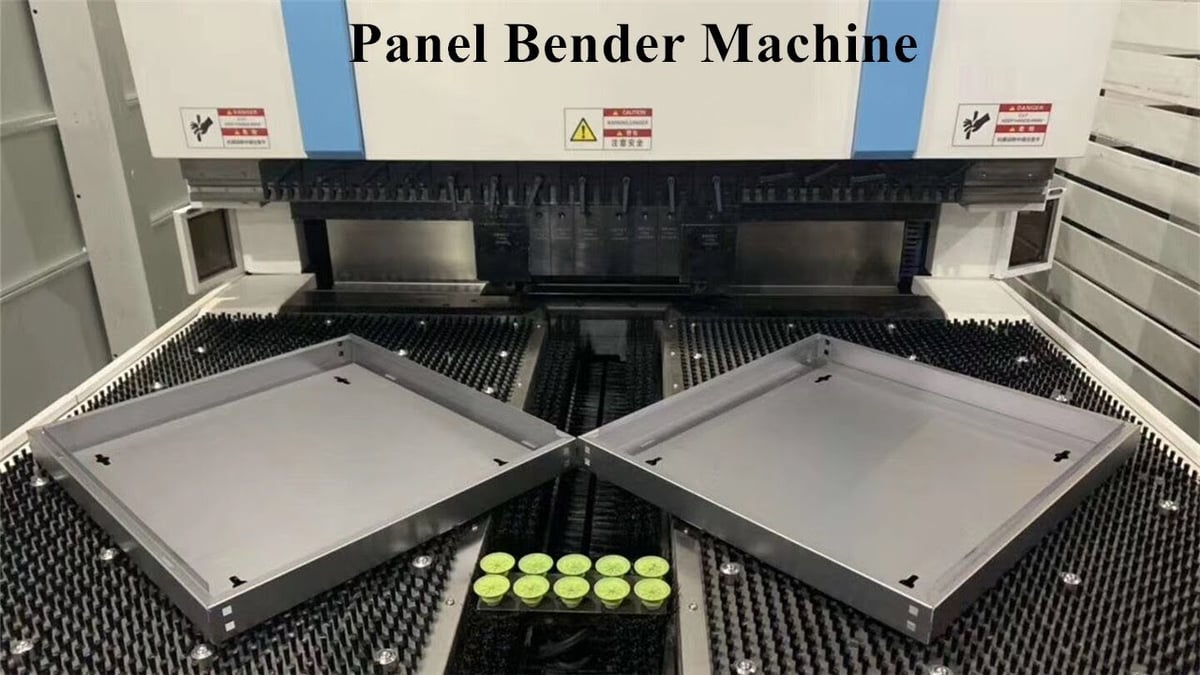
¿Cómo se puede procesar una gama más amplia de geometrías de piezas?
Como ocurre con cualquier tecnología, el plegado de paneles conlleva sus propios desafíos. Muchos fabricantes están ansiosos por adoptar esta tecnología, pero descubren que no tienen la combinación adecuada de piezas para aprovechar al máximo la eficiencia de la máquina. Las geometrías complejas de las piezas o las piezas estrechas suelen plantear dificultades para el plegado de paneles, especialmente si la máquina no puede manipular este tipo de piezas con su diseño estándar de herramientas y manipuladores.
El concepto de la paneladora multiherramienta surgió de una extensa investigación destinada a ampliar las capacidades para que se pudieran procesar geometrías de piezas más variadas sin la necesidad de cambios manuales adicionales en las herramientas.
Una característica clave de la paneladora multiherramienta es su consola integrada, que puede alojar múltiples herramientas de plegado. Esto le permite doblar perfiles de piezas complejas que antes no eran adecuadas para el plegado de paneles. Además, un dispositivo manipulador en la parte posterior de la paneladora multiherramienta permite el procesamiento de piezas de tipo canal estrecho, que eran un desafío para las paneladoras tradicionales.
La plegadora de paneles multiherramienta puede manejar espesores de chapa de acero dulce que van desde 0,020 a 0,118 pulgadas y longitudes de hasta 13 pies para una sola máquina, o hasta 26 pies cuando se utilizan dos máquinas en tándem. Otras características, como herramientas móviles, dispositivos de inspección visual, pinzas y herramientas personalizadas, se pueden integrar en el sistema final.
Diseñada para ser fácil de usar, la paneladora multiherramienta es fácil de programar, controlar y mantener. Funciona con accionamientos eléctricos, lo que garantiza un bajo consumo de energía y un alto rendimiento.
¿Cuándo necesitas una dobladora de paneles CNC?
Las dobladoras de paneles son ideales para manipular piezas grandes, cuadradas, planas, rectas y rectangulares que son difíciles de doblar y manejar para una sola persona utilizando una prensa plegadora, especialmente cuando se trata de piezas que requieren un acabado de alta calidad.
El doblado de paneles se utiliza comúnmente para formar:
- Electrodomésticos como refrigeradores
- Aparatos eléctricos como armarios eléctricos y artefactos de iluminación.
- Equipos de climatización
- Componentes de construcción, incluidos paneles, puertas, ascensores, bandejas de cables, plataformas y perfiles.
- Muebles de metal para cocinas comerciales, oficinas, unidades de almacenamiento y lockers.
- Remolques de camiones
Esta tecnología es especialmente beneficiosa para doblar piezas cosméticas o de aspecto crítico. Una mesa de cepillos sostiene la pieza desde abajo y el movimiento interpolado de la herramienta de doblado en los ejes X e Y mantiene un único punto de contacto con la brida durante el proceso de doblado, lo que minimiza significativamente los rayones y las marcas.
La tecnología de plegado de paneles aporta numerosas ventajas a la fabricación moderna de chapa metálica. Aunque existen algunas limitaciones en cuanto a los tipos de piezas que pueden procesar las plegadoras de paneles, pueden ser el método de plegado más eficiente cuando la aplicación es adecuada.
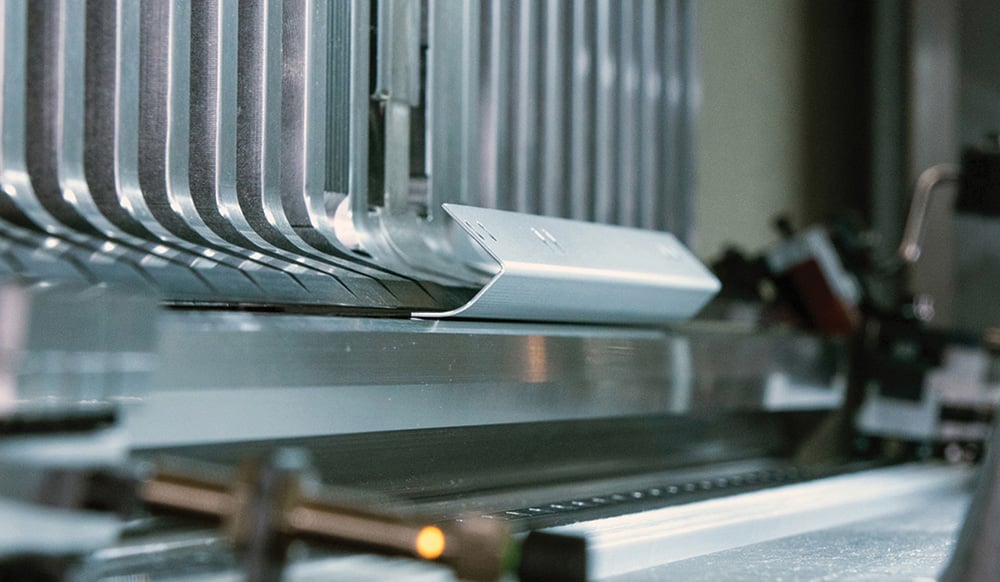
Cómo entender el sistema CNC de una máquina dobladora de paneles
Componentes de un sistema CNC de plegadora de paneles
Un sistema CNC de doblado de paneles integra componentes clave cruciales para un doblado eficiente de metales:
El Mecanismo de sujeción Sujeta de forma segura las láminas de metal en su lugar durante el doblado, garantizando estabilidad y precisión durante todas las operaciones. Cuchillas de flexión ajustarse dinámicamente para lograr curvas precisas según lo programado, mejorando la versatilidad de la máquina para manejar diversas tareas de curvado. Unidad de control actúa como eje central, gestionando todas las operaciones CNC desde la programación de complejas secuencias de plegado hasta la garantía de resultados consistentes y precisos con una mínima intervención manual. Interfaz de software Permite a los operadores ingresar parámetros de doblado específicos, monitorear operaciones en tiempo real y administrar sin problemas las funciones de la máquina, optimizando la productividad y la personalización en los procesos de fabricación de metales.
Principios de funcionamiento
La programación implica configurar ángulos de plegado, secuencias y dimensiones precisas dentro del sistema CNC, lo que permite a los operadores adaptar los procesos de plegado a especificaciones exactas. Esta capacidad agiliza la producción y mejora la flexibilidad.
La automatización desempeña un papel fundamental en las plegadoras de paneles CNC, ya que automatiza el proceso de plegado, minimiza el trabajo manual y garantiza resultados consistentes lote tras lote. Esta automatización no solo aumenta la eficiencia, sino que también reduce el riesgo de error humano.
La precisión es un sello distintivo de las plegadoras de paneles CNC, que les permite alcanzar altos niveles de exactitud y repetibilidad en las operaciones de plegado. Esta precisión es esencial para mantener los estándares de calidad y cumplir con tolerancias estrictas en la fabricación de metales.
Capacidades
Comprender las capacidades de manejo de materiales implica conocer la gama de metales y espesores que el sistema CNC puede manejar de manera efectiva, lo que garantiza la compatibilidad con diversas necesidades de fabricación.
La capacidad del sistema para realizar curvas complejas le permite realizar formas y curvas intrincadas con un tiempo de configuración mínimo, mejorando la eficiencia operativa y la versatilidad en las tareas de fabricación de metales.
La evaluación de la eficiencia de la producción resalta cómo el sistema CNC mejora el rendimiento al automatizar los procesos y reducir el desperdicio de material, optimizando en última instancia las operaciones de fabricación para aumentar la productividad y la rentabilidad.
Mantenimiento y Capacitación
Garantizar el rendimiento óptimo de una paneladora CNC implica dos aspectos críticos: mantenimiento y capacitación del operador.
Las tareas de mantenimiento periódicas son esenciales para mantener el sistema CNC en óptimas condiciones. Esto incluye controles de rutina, lubricación de piezas móviles e inspección de componentes eléctricos para evitar averías y garantizar su longevidad.
Igualmente importante es la capacitación integral de los operadores. Los operadores deben ser competentes en todos los aspectos del uso del sistema CNC, desde la programación de parámetros específicos y la resolución de problemas hasta el cumplimiento de los protocolos de seguridad. Una capacitación adecuada no solo maximiza la eficiencia operativa, sino que también minimiza el tiempo de inactividad y garantiza prácticas de trabajo seguras en el entorno de fabricación.
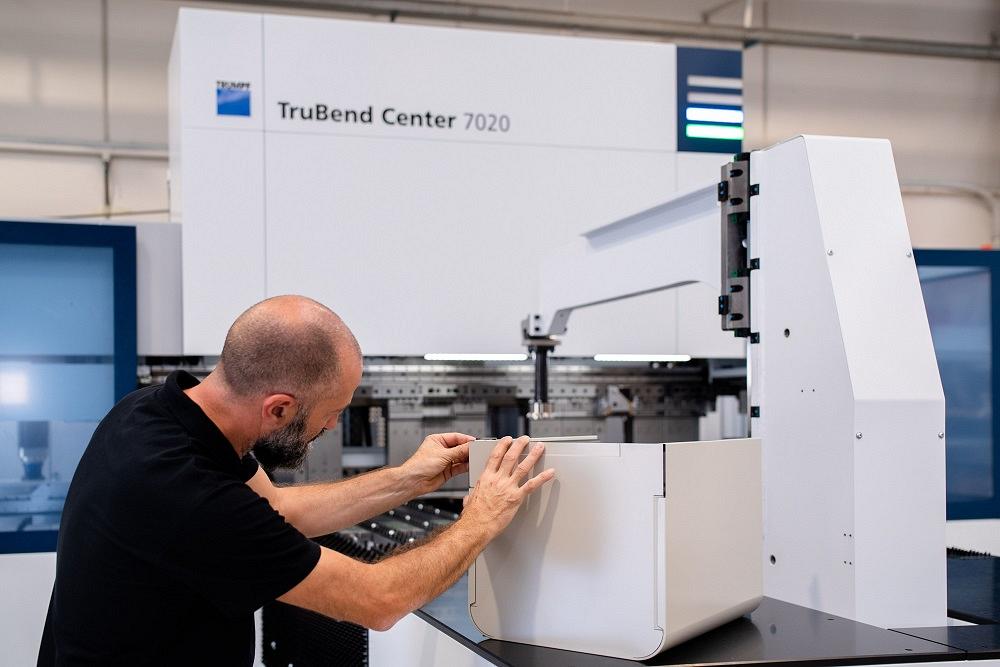
¿Cómo elegir la dobladora de paneles CNC adecuada?
Para elegir la máquina dobladora de paneles CNC adecuada, es necesario tener en cuenta varios factores para garantizar que cumpla con sus requisitos y necesidades de fabricación específicos. A continuación, le presentamos una guía paso a paso para ayudarlo a tomar la decisión correcta:
Evalúe sus requisitos de curvatura:
Determine el tipo y el grosor de los materiales que va a doblar (por ejemplo, acero, aluminio, acero inoxidable).
Tenga en cuenta el tamaño y la complejidad de las piezas que necesita producir, incluidos los ángulos de curvatura y las tolerancias requeridas.
Evaluar la capacidad de la máquina:
Busque una dobladora de paneles CNC a la venta que pueda manejar el tamaño y el grosor de sus piezas de trabajo típicas.
Tenga en cuenta factores como la longitud de curvatura, el tonelaje (fuerza de curvatura) y el ángulo de curvatura máximo.
Considere las funciones de automatización y productividad:
Evalúe el nivel de automatización que ofrece la paneladora CNC, incluidas características como el cambio automático de herramientas, los sistemas de manipulación de materiales y la integración robótica.
Evalúe las características que mejoran la productividad, como tiempos de configuración rápidos, cambios rápidos de herramientas y capacidades de doblado de alta velocidad.
Revise la precisión y exactitud:
Busque dobladoras de paneles automáticas con sistemas de control avanzados y mecanismos de precisión para garantizar resultados de doblado precisos.
Considere características tales como sistemas de coronación para compensar la desviación y mantener una flexión uniforme a lo largo de la pieza.
Examinar las capacidades del software y la programación:
Evaluar la interfaz de usuario y el software de programación provisto con la máquina dobladora de paneles.
Busque interfaces de programación intuitivas, herramientas de simulación para verificar secuencias de plegado y compatibilidad con software CAD/CAM común.
Evaluar los requisitos de confiabilidad y mantenimiento:
Investigue la reputación del fabricante y la confiabilidad de sus dobladoras de paneles CNC.
Considere factores como el tiempo de funcionamiento de la máquina, los requisitos de mantenimiento y la disponibilidad de repuestos y soporte técnico.
Parámetros técnicos de la máquina dobladora de paneles CNC totalmente automática
Modelo | RAS-1500/RAS-2000/RAS-2500 |
---|---|
Velocidad mínima de plegado continuo | 0,5 s/cuchillo |
Espesor de flexión | Acero inoxidable 201 de 0,8 mm, acero inoxidable 304 de 1,0 mm, acero frío de 1,2 mm, acero de aluminio de 1,6 mm |
Longitud máxima de curvatura (mm) | 1500/2000/2500 |
Altura máxima de curvatura (mm) | 170 |
Tamaño mínimo de moldeo de los cuatro lados (mm) | 280*280 |
Ángulo de curvatura | 0-180 |
Velocidad máxima de alimentación (m/min) | 120 |
Pensamiento final
Elegir la máquina CNC adecuada para doblar chapa metálica es una decisión crucial que afecta significativamente la eficiencia y el éxito de la producción. Los factores clave a tener en cuenta incluyen la compatibilidad de los materiales, los requisitos de doblado, la precisión, el costo y el mantenimiento.
Las máquinas CNC de Krrass ofrecen tecnología avanzada y alta precisión, lo que las hace ideales para operaciones de plegado de chapa metálica eficientes y precisas. Con los avances continuos en la tecnología CNC, el futuro del plegado de chapa metálica parece prometedor. Aproveche el poder de las máquinas CNC de Krrass para liberar el potencial de capacidades de producción mejoradas y éxito operativo.
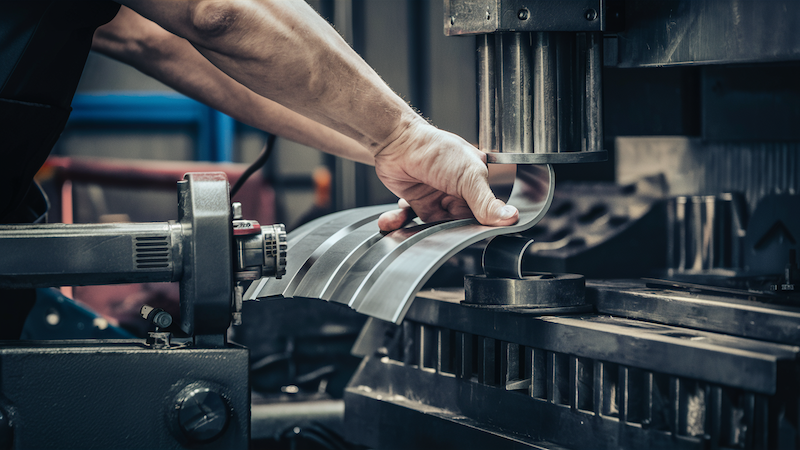