En talleres pequeños donde cada metro cuadrado cuenta, seleccionar el equipo adecuado puede marcar la diferencia a la hora de optimizar el espacio y la productividad. La dobladora CNC compacta se está convirtiendo cada vez más en la opción preferida por las empresas que necesitan doblar con precisión pero tienen un espacio limitado. Estas máquinas, que combinan tecnología CNC avanzada con un tamaño reducido, ofrecen numerosas ventajas, especialmente para los talleres que buscan maximizar la eficiencia sin sacrificar la calidad. Exploremos los cinco principales beneficios de utilizar una Dobladora CNC compacta en pequeños talleres.
Introducción
En los talleres pequeños, el espacio suele ser un recurso valioso y su uso eficiente puede tener un impacto significativo en la productividad general. Cada metro cuadrado cuenta, por lo que es fundamental invertir en maquinaria que no solo ofrezca un alto rendimiento, sino que también ocupe un espacio reducido. La maquinaria que ahorra espacio permite a los talleres optimizar las operaciones, reducir el desorden y hacer espacio para otras herramientas esenciales, todo ello manteniendo altos estándares de producción.
Una de esas soluciones es la Dobladora CNC compacta, una máquina que combina la tecnología avanzada de control numérico por computadora (CNC) con un diseño que ahorra espacio. Su capacidad para ofrecer un plegado de precisión en un formato más pequeño la ha hecho cada vez más popular entre los talleres pequeños. Ya sea para la fabricación de metales u otras necesidades de plegado, la dobladora CNC compacta ofrece un equilibrio perfecto entre funcionalidad y eficiencia, lo que ayuda a las empresas a maximizar su espacio y producción.
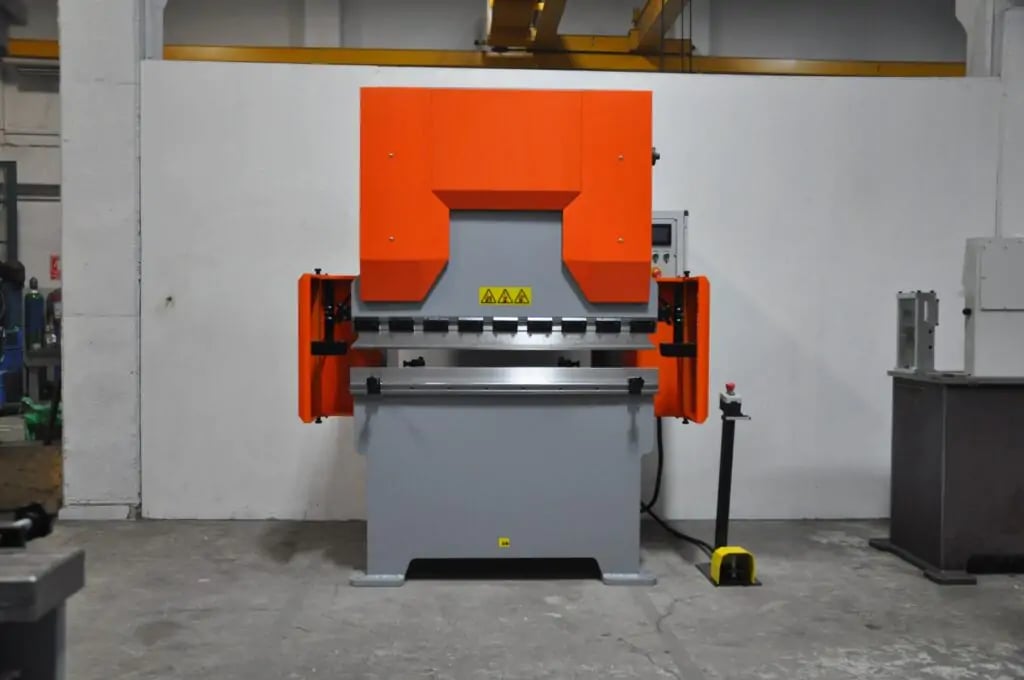
¿Qué es una prensa plegadora compacta?
A Prensa plegadora compacta Es una pieza vital de equipo en la industria metalúrgica, utilizada principalmente para doblar y dar forma a chapa metálica en formas predeterminadas y precisas. Estas máquinas son cruciales en los procesos de fabricación que requieren la formación de piezas metálicas, desde simples soportes hasta componentes complejos utilizados en industrias como la automotriz, la aeroespacial y la construcción.
En esencia, una prensa plegadora funciona sujetando una lámina de metal entre un punzón y una matriz, herramientas diseñadas específicamente para crear un pliegue particular. Luego, la máquina aplica una fuerza controlada al metal, deformándolo a lo largo de la línea de plegado deseada. La precisión y la exactitud son clave, especialmente en industrias con tolerancias de componentes ajustadas.
A Prensa plegadora compacta Es una máquina más pequeña y de precisión que se utiliza para doblar láminas o placas de metal en procesos de metalistería. Ofrece las mismas funciones básicas que una prensa plegadora estándar, pero está optimizada para operaciones a menor escala. Esto la hace ideal para talleres, instituciones educativas e industrias que requieren un plegado preciso para cargas más livianas y proyectos más pequeños. A pesar de su tamaño más pequeño, la prensa plegadora compacta ofrece todas las características esenciales de una máquina tradicional, lo que proporciona una solución eficiente y que ahorra espacio sin sacrificar el rendimiento.
Componentes de una prensa plegadora compacta
Aunque una mini prensa plegadora es más pequeña, sus componentes esenciales son similares a los de una prensa plegadora tradicional. Algunos de los componentes clave son:
- Marco:El armazón de la mini prensa plegadora suele estar fabricado con acero de alta resistencia para soportar las fuerzas aplicadas durante el plegado. Aunque es más pequeña, la máquina debe ser lo suficientemente robusta para soportar la presión generada durante el proceso de plegado.
- RAM:El ariete es el componente móvil de la máquina, que presiona el punzón contra la matriz para dar forma al metal. En las miniprensas plegadoras, el movimiento del ariete suele estar controlado por un mecanismo manual o hidráulico.
- Perforar y troquelar:Estas son las herramientas que se utilizan para dar forma al metal. El punzón está unido al ariete y presiona el material en la matriz, que está montada en la bancada. La forma de la matriz determina el ángulo de plegado final y la forma del metal.
- Calibre trasero:El tope trasero es un dispositivo que ayuda a posicionar la lámina de metal con precisión debajo del punzón y la matriz. Esto garantiza un doblado uniforme y repetibilidad en varias piezas.
- Sistema de control:Algunas mini prensas plegadoras están equipadas con controles manuales, mientras que otras pueden contar con sistemas de control numérico computarizado (CNC), que permiten operaciones de plegado de alta precisión con precisión digital.
Tipos de mini prensas plegadoras
Las mini prensas plegadoras se pueden clasificar según su mecanismo de funcionamiento:
- Mini prensa plegadora manual:En esta versión, la máquina se opera manualmente, utilizando una palanca o volante para mover el ariete. Se utilizan comúnmente para materiales más livianos y proyectos más simples que no requieren altos niveles de precisión o automatización.
- Mini prensa plegadora hidráulica:Las miniprensas plegadoras hidráulicas utilizan cilindros hidráulicos para mover el ariete. Esto permite una mayor fuerza y precisión en comparación con las máquinas manuales. Son ideales para talleres pequeños y medianos que requieren plegados uniformes y precisos.
- Mini prensa plegadora neumática:Este tipo de prensa plegadora utiliza presión de aire para mover el ariete. Los sistemas neumáticos suelen ser los preferidos por su velocidad y eficiencia energética, aunque es posible que no proporcionen tanta fuerza como los sistemas hidráulicos.
- Mini prensa plegadora CNC:Las miniprensas plegadoras CNC (control numérico por computadora) ofrecen el más alto nivel de precisión y automatización. El operador ingresa los parámetros de plegado en una computadora y la máquina ajusta automáticamente el cabezal y el tope trasero para lograr los plegados deseados. Las miniprensas plegadoras CNC se utilizan en industrias donde la precisión es primordial, como en la electrónica, la industria aeroespacial y la fabricación de dispositivos médicos.
Características principales de la dobladora CNC compacta y moderna
La evolución de la tecnología de las prensas plegadoras ha traído consigo varias innovaciones a las miniprensas plegadoras, mejorando sus capacidades y facilidad de uso. Estas son algunas de las características clave que se encuentran en las miniprensas plegadoras modernas:
- Sistemas de control CNC:Como se mencionó anteriormente, muchas miniprensas plegadoras ahora vienen equipadas con sistemas CNC. Estos controles computarizados permiten a los operadores programar secuencias de plegado complejas, lo que garantiza resultados consistentes y reduce la necesidad de ajustes manuales. Los sistemas CNC también facilitan la gestión de pedidos repetidos, ya que la máquina puede almacenar programas de plegado para uso futuro.
- Interfaces de pantalla táctil:Algunas miniprensas plegadoras modernas cuentan con interfaces de pantalla táctil, lo que las hace fáciles de usar y de operar. Estas interfaces permiten a los operadores ingresar parámetros de plegado, monitorear el progreso de la operación de plegado y realizar ajustes según sea necesario, todo desde un panel de control central.
- Sensores de precisión y sistemas de retroalimentación:Los sensores de precisión y los sistemas de retroalimentación se integran cada vez más en las miniprensas plegadoras para garantizar un plegado preciso. Estos sistemas controlan la posición del cabezal y del material que se está doblando, y realizan ajustes en tiempo real para mantener la precisión durante todo el proceso de plegado.
- Cambios automáticos de herramientas:En las industrias de alta precisión donde se requieren múltiples herramientas para diferentes plegados, las miniprensas plegadoras con capacidades de cambio automático de herramientas son cada vez más comunes. Esta característica aumenta la eficiencia al reducir el tiempo de inactividad entre cambios de herramientas, lo que facilita el cambio entre diferentes piezas u operaciones de plegado.
- Características de seguridad:Las miniprensas plegadoras modernas están equipadas con varias funciones de seguridad para proteger a los operadores. Estas incluyen cortinas de luz, enclavamientos de seguridad y botones de parada de emergencia que detienen inmediatamente la máquina en caso de un problema. Con el aumento de la automatización, estas funciones de seguridad son esenciales para garantizar un entorno de trabajo seguro, especialmente en talleres pequeños o entornos educativos.
Beneficios de utilizar una dobladora CNC compacta
Beneficio 1: Eficiencia del espacio
Las dobladoras CNC compactas están diseñadas específicamente para ahorrar valioso espacio en el piso, lo que las hace ideales para talleres pequeños. Estas máquinas combinan capacidades de doblado avanzadas en un espacio más pequeño y eficiente en comparación con los equipos de doblado tradicionales. Al ocupar menos espacio, permiten que los talleres destinen más espacio para otras herramientas, materiales o estaciones de trabajo, lo que garantiza un entorno bien organizado y productivo.
La optimización del espacio es crucial para los talleres pequeños porque cada metro cuadrado afecta directamente la eficiencia del flujo de trabajo. Un espacio desordenado o abarrotado puede provocar operaciones más lentas, riesgos de seguridad y dificultad para gestionar varias tareas simultáneamente. Al invertir en una dobladora CNC compacta, las empresas pueden mantener un diseño más limpio y optimizado, lo que no solo mejora la productividad, sino que también aumenta la flexibilidad operativa, lo que permite espacio para el crecimiento y la maquinaria adicional según sea necesario.
Beneficio 2: Precisión y exactitud
Una de las características más destacadas de las dobladoras CNC compactas es su capacidad para ofrecer un plegado de alta precisión, gracias a la avanzada tecnología CNC (Control Numérico Computarizado). Estas máquinas están programadas para ejecutar plegados exactos con un error mínimo, lo que garantiza que cada pieza cumpla con las especificaciones deseadas. La tecnología CNC permite a los operadores establecer parámetros precisos, lo que reduce las posibilidades de error humano y ofrece resultados precisos de manera constante, incluso en tareas de plegado complejas.
En el caso de las necesidades de producción a pequeña escala, la consistencia en la producción es esencial para mantener los estándares de calidad. Las dobladoras CNC compactas se destacan en esta área al producir pliegues uniformes en múltiples tiradas, independientemente de la complejidad o el volumen del trabajo. Esta confiabilidad no solo mejora la eficiencia de los talleres pequeños, sino que también reduce el desperdicio de material, lo que garantiza que cada proyecto se complete con precisión y exactitud, cumpliendo con las demandas de los clientes sin comprometer la calidad.
Beneficio 3: Rentabilidad
Las dobladoras CNC compactas ofrecen una ventaja significativa en términos de rentabilidad, lo que las convierte en una opción ideal para talleres pequeños. En primer lugar, estas máquinas generalmente tienen costos operativos más bajos en comparación con las dobladoras más grandes y de tamaño más industrial. Su menor tamaño a menudo significa un menor consumo de energía, lo que se traduce en facturas de servicios públicos más bajas. Además, las dobladoras CNC compactas requieren menos recursos para su funcionamiento, desde materiales hasta mano de obra, lo que ayuda a los talleres pequeños a mantenerse dentro de sus presupuestos y, al mismo tiempo, mantener una producción de alta calidad.
Otro factor importante en su relación costo-beneficio es el ahorro a largo plazo mediante la eficiencia energética y el mantenimiento mínimo. Las dobladoras CNC compactas están diseñadas para ser más eficientes en el uso de energía, lo que no solo ayuda a reducir los costos operativos sino que también contribuye a la longevidad de la máquina. Además, con menos componentes mecánicos y un diseño aerodinámico, estas máquinas tienden a requerir menos mantenimiento que las máquinas más grandes y complejas. Esto minimiza el tiempo de inactividad y los costos de reparación, lo que permite a las empresas lograr una producción constante sin interrupciones frecuentes, maximizando el retorno de la inversión a lo largo del tiempo.
Beneficio 4: Versatilidad
A pesar de su menor tamaño, las dobladoras CNC compactas son máquinas muy versátiles capaces de manejar una amplia gama de materiales y requisitos de doblado. Ya sea que trabajen con acero, aluminio, cobre u otros metales, estas máquinas se pueden adaptar fácilmente a diferentes tareas, lo que las convierte en una herramienta esencial en pequeños talleres que necesitan flexibilidad en sus procesos de producción. Esta versatilidad garantiza que las empresas puedan asumir diversos proyectos sin la necesidad de múltiples máquinas especializadas, lo que reduce tanto los costos como los requisitos de espacio.
Lo que realmente distingue a las dobladoras CNC compactas es su capacidad de ofrecer esta versatilidad sin comprometer la funcionalidad. Incluso con su tamaño reducido, estas máquinas incorporan tecnología CNC avanzada que permite un control preciso de operaciones de doblado complejas. Ya sea un lote pequeño o un diseño personalizado, la dobladora CNC compacta puede satisfacer las demandas de varios trabajos, lo que permite que los talleres pequeños mantengan una producción de alta calidad en diferentes aplicaciones.
Beneficio 5: Facilidad de uso y automatización
Las dobladoras CNC compactas están diseñadas con interfaces fáciles de usar, lo que las hace fáciles de operar incluso para aquellos con experiencia técnica limitada. Los sistemas de control CNC permiten a los operadores ingresar instrucciones precisas a través de un software intuitivo, lo que les permite establecer parámetros, ajustar ángulos de doblado y administrar múltiples tareas con un mínimo esfuerzo. Esta simplicidad reduce la curva de aprendizaje, lo que permite que los talleres integren rápidamente la máquina en las operaciones diarias sin una capacitación extensa.
La automatización es otra característica clave que mejora la facilidad de uso y aumenta la productividad. Con procesos automatizados, la dobladora CNC compacta puede realizar pliegues complejos con una mínima intervención manual, lo que reduce la intensidad de la mano de obra y el riesgo de error humano. La automatización no solo acelera la producción, sino que también permite a los operadores centrarse en otras tareas, lo que en última instancia aumenta la eficiencia general. Esta combinación de diseño fácil de usar y automatización convierte a las dobladoras CNC compactas en una poderosa herramienta para optimizar el flujo de trabajo en talleres pequeños, mejorando tanto la productividad como la calidad de los resultados.
Curvadora compacta en sectores industriales
Las miniprensas plegadoras, aunque están diseñadas para proyectos de pequeña y mediana escala, se han abierto camino en varios sectores industriales debido a su versatilidad y precisión. Su naturaleza compacta, combinada con tecnología moderna, permite que estas máquinas realicen tareas altamente especializadas que las máquinas más grandes podrían tener dificultades para realizar debido a problemas de espacio o exceso de capacidad. A continuación, se muestra un análisis más detallado de cómo se utilizan las miniprensas plegadoras en diferentes industrias:
1. Industria aeroespacial
La industria aeroespacial exige precisión y fiabilidad, ya que las piezas que se utilizan en aeronaves y vehículos espaciales deben cumplir con estrictos estándares de seguridad y rendimiento. Las miniprensas plegadoras se utilizan ampliamente para fabricar componentes pequeños que deben ajustarse a tolerancias estrictas. Entre ellos se incluyen soportes, componentes de montaje y diversas piezas de chapa metálica que se utilizan en los interiores de aeronaves y en los sistemas de control.
Las miniprensas plegadoras equipadas con tecnología CNC permiten a los fabricantes de la industria aeroespacial producir pliegues repetibles con extrema precisión. El menor tamaño de la máquina también permite una configuración más sencilla y transiciones más rápidas entre diferentes tareas de producción, algo esencial en el altamente competitivo sector aeroespacial, donde incluso las ineficiencias menores pueden provocar retrasos significativos o un aumento de los costos.
2. Sector Automotriz
En la industria automotriz, las miniprensas plegadoras se utilizan para fabricar piezas más pequeñas, como soportes, palancas y sistemas de montaje. Estos componentes son cruciales para el ensamblaje del vehículo, ya que contribuyen a la seguridad, la integridad estructural y la funcionalidad. Mientras que las prensas plegadoras más grandes manejan paneles de carrocería más grandes, las miniprensas plegadoras se destacan en el plegado de piezas más pequeñas y detalladas que requieren delicadeza.
En aplicaciones automotrices personalizadas y de posventa, las miniprensas plegadoras son ideales para fabricar piezas personalizadas como jaulas antivuelco, refuerzos de chasis y componentes interiores a medida. Permiten a los talleres crear estos componentes en volúmenes reducidos manteniendo al mismo tiempo una alta precisión y calidad.
3. Cajas eléctricas y electrónicas
La mini prensa plegadora desempeña un papel esencial en la producción de cajas, carcasas y envolventes eléctricas para diversos dispositivos electrónicos. Estas carcasas no solo deben proteger los delicados componentes que se encuentran en su interior, sino que también deben cumplir con especificaciones precisas de montaje y funcionalidad.
Las láminas metálicas que se utilizan en electrónica suelen ser delgadas, ligeras y requieren curvaturas complejas que solo una miniprensa plegadora puede lograr. Además, las miniprensas plegadoras CNC se emplean con frecuencia en el sector de la electrónica debido a su capacidad para producir piezas detalladas de manera uniforme, lo que resulta fundamental en aplicaciones de alta tecnología donde los errores en las dimensiones pueden provocar fallas en el equipo.
4. Dispositivos médicos
En el campo médico, los dispositivos y equipos suelen contener piezas de metal fabricadas a medida. Estas piezas son fundamentales para la funcionalidad y la seguridad de los instrumentos médicos, las herramientas quirúrgicas y los equipos de diagnóstico. Las miniprensas plegadoras se utilizan para formar estas piezas con la precisión necesaria, lo que garantiza que cumplan con los estrictos estándares de la industria médica.
Teniendo en cuenta los altos estándares de seguridad y reglamentación en el campo médico, la precisión de las miniprensas plegadoras es esencial. El acero inoxidable y otros materiales de alta calidad, que se utilizan a menudo en dispositivos médicos, requieren fuerzas de plegado específicas que las miniprensas plegadoras hidráulicas o CNC pueden proporcionar. Además, la capacidad de crear prototipos de pequeñas cantidades rápidamente utilizando miniprensas plegadoras permite a los ingenieros médicos probar nuevos diseños e innovaciones de forma más eficiente.
5. Sistemas HVAC (calefacción, ventilación y aire acondicionado)
Las miniprensas plegadoras desempeñan un papel importante en la industria de HVAC para la fabricación de conductos de aire, rejillas de ventilación y otras piezas de chapa metálica. La demanda de soluciones de HVAC personalizadas tanto en entornos comerciales como residenciales requiere máquinas dobladoras versátiles que puedan crear una variedad de formas y tamaños de manera rápida y eficiente.
La precisión que ofrecen las miniprensas plegadoras garantiza que los conductos de aire y otros componentes encajen perfectamente en los sistemas de climatización, mejorando el flujo de aire y la eficiencia. Las empresas de climatización se benefician del tamaño compacto de estas máquinas, que les permite trabajar en espacios reducidos y producir los componentes necesarios en el lugar o en pequeños talleres.
6. Joyería y orfebrería artesanal
El plegado complejo y a pequeña escala que se requiere para la joyería y la metalistería artística hace que las miniprensas plegadoras sean una herramienta indispensable en esta industria especializada. Los joyeros y artesanos utilizan estas máquinas para dar forma a las láminas de metal y crear diseños hermosos y complejos, como anillos, pulseras, colgantes y esculturas.
El control y la precisión que ofrecen las miniprensas plegadoras manuales o accionadas por CNC permiten la creatividad sin comprometer la calidad ni la durabilidad del producto final. Los artistas pueden crear curvas suaves, ángulos agudos y diseños intrincados en metal, todos ellos esenciales para la joyería de alta calidad y las piezas de arte en metal personalizadas.
7. Prototipado e investigación y desarrollo (I+D)
La creación de prototipos es una fase esencial en el desarrollo de productos, ya sea en el sector automotriz, aeroespacial, electrónico o de bienes de consumo. Las miniprensas plegadoras se utilizan con frecuencia en entornos de I+D para producir y probar rápidamente prototipos de piezas metálicas. Los ingenieros y diseñadores de productos utilizan estas máquinas para experimentar con diferentes materiales, espesores y ángulos de plegado para afinar sus diseños antes de pasar a la producción a gran escala.
La capacidad de producir lotes pequeños de piezas según demanda es una ventaja importante en los entornos de I+D. La flexibilidad de las miniprensas plegadoras CNC permite a los diseñadores modificar sus diseños en tiempo real, ajustando parámetros y volviendo a doblar las piezas hasta lograr el resultado deseado. Este proceso iterativo es crucial en industrias donde la innovación impulsa el éxito, y las miniprensas plegadoras permiten a las empresas acelerar sus plazos de desarrollo de productos.
8. Fabricación a medida y talleres de trabajo
En los talleres de fabricación a medida y de encargo, las miniprensas plegadoras son invaluables para producir pedidos únicos o de lotes pequeños. Estos talleres suelen atender a clientes que requieren piezas de metal personalizadas para aplicaciones específicas, que van desde componentes de máquinas hasta elementos arquitectónicos.
Para los talleres, la capacidad de cambiar rápidamente entre diferentes proyectos es esencial, y la versatilidad de las miniprensas plegadoras permite a los operadores manejar una variedad de materiales y diseños de piezas sin necesidad de largos tiempos de configuración. Esta flexibilidad hace que las miniprensas plegadoras sean una solución ideal para la fabricación personalizada, donde la precisión y la velocidad son fundamentales.
Limitaciones de la dobladora compacta
Si bien las mini prensas plegadoras ofrecen varias ventajas, también tienen algunas limitaciones:
- Capacidad limitada:Debido a su menor tamaño, las miniprensas plegadoras no son adecuadas para doblar láminas de metal grandes o gruesas. Su capacidad suele estar limitada a láminas delgadas y pueden tener dificultades con materiales más pesados.
- Menor salida de fuerza:Las miniprensas plegadoras generan menos fuerza que las máquinas de tamaño normal, lo que limita los tipos de materiales que pueden doblar. Por ejemplo, es posible que no puedan manejar metales endurecidos o gruesos.
- Velocidad de producción más lenta:En comparación con las prensas plegadoras automatizadas de mayor tamaño, las miniprensas plegadoras pueden tener velocidades de producción más lentas. Esto es particularmente cierto en el caso de las versiones manuales, en las que el operador debe ajustar manualmente la máquina para cada pliegue.
- Operación manual en algunos modelos:Si bien existen modelos CNC, muchas miniprensas plegadoras se operan manualmente. Esto requiere más habilidad y experiencia por parte del operador, ya que hay menos automatización involucrada en el proceso de plegado.
- Longitud de curvatura limitada:Las mini prensas plegadoras tienen una longitud de plegado más corta en comparación con las máquinas de tamaño completo, lo que puede ser una limitación cuando se trabaja con láminas de metal más largas.
Conclusión: El papel de las dobladoras CNC compactas en la fabricación moderna
El Dobladora CNC compacta Se ha convertido en una herramienta crucial en la fabricación moderna, ya que ofrece precisión, versatilidad y eficiencia en un diseño que ahorra espacio. Ya sea que se utilicen para producción a pequeña escala, fabricación personalizada o fines educativos, estas máquinas brindan la flexibilidad necesaria para satisfacer las demandas de diversas industrias.
A medida que la tecnología avanza, se espera que las dobladoras CNC compactas se vuelvan aún más sofisticadas, con mayor automatización, mayor precisión y mejores características de seguridad. Su papel en la creación de prototipos, trabajos de reparación y fabricación especializada garantiza que seguirán siendo indispensables, especialmente a medida que las industrias priorizan cada vez más la personalización, la sostenibilidad y la eficiencia operativa.
Desde la industria aeroespacial hasta la fabricación de joyas, Dobladoras CNC compactas Ofrecen una poderosa combinación de precisión y adaptabilidad en un espacio compacto, lo que los convierte en un activo valioso en el trabajo de metales y más allá.