Ajuste del ángulo de un máquina dobladora Implica realizar cambios en la configuración de la máquina para lograr el ángulo de plegado deseado para un material y un espesor específicos. A continuación, se incluye una guía general sobre cómo ajustar el ángulo de una máquina dobladora:
Tabla de contenido
¿Cómo operar correctamente la prensa plegadora?
1. Respete estrictamente los procedimientos de seguridad de operación de las máquinas dobladoras y utilice el equipo de protección laboral según sea necesario. Antes de comenzar, debe verificar cuidadosamente si el motor, el interruptor, el circuito y la conexión a tierra funcionan correctamente y si los controles y los botones del equipo están en la posición correcta.
2. Verifique la superposición y la solidez de las matrices superior e inferior. Verifique si cada dispositivo de posicionamiento cumple con los requisitos para el procesamiento. Cuando la placa deslizante superior y cada eje de posicionamiento no estén en el origen, ejecute el programa de retorno al origen.
3. Después de poner en marcha el equipo, déjelo funcionar en ralentí durante 1 o 2 minutos y mueva la patineta hasta el rango completo 2 o 3 veces. Si detecta algún sonido anormal o mal funcionamiento, debe detener la máquina de inmediato y solucionar el problema. Solo puede trabajar después de que todo esté normal. El trabajo debe estar bajo el mando unificado de una persona, de modo que el operador y el personal de alimentación y prensado puedan cooperar estrechamente para garantizar que el personal que coopera esté en una posición segura antes de enviar la señal de flexión con precisión.
4. La chapa debe compactarse al doblarla para evitar que se levante y lesione a las personas durante el doblado. Al ajustar la matriz de chapa, debe cortar el suministro de energía y detener la operación. Al cambiar la abertura del molde inferior variable, no se permite que ningún material entre en contacto con el molde inferior. Durante el trabajo, no se permite que nadie se pare detrás de la máquina dobladora. Está estrictamente prohibido doblar la chapa solo por un extremo.
¿Cómo ajustar el ángulo de la máquina dobladora?
Prepare la máquina:
Asegúrese de que la prensa plegadora esté correctamente configurada y de que se hayan tomado todas las medidas de seguridad. Asegúrese de que la máquina esté apagada antes de realizar cualquier ajuste.
Inspeccionar las herramientas:
Compruebe el estado de las herramientas, incluidos los punzones y las matrices. Asegúrese de que estén en buenas condiciones y montados de forma segura.
Seleccione las herramientas correctas:
Elija las herramientas adecuadas para la tarea de doblado. El tipo y el tamaño de las herramientas afectarán el ángulo de doblado.
Consulte las especificaciones del material:
Consulte las especificaciones del material que se va a doblar. Comprenda la resistencia a la tracción y el espesor del material, ya que estos factores influyen en el proceso de doblado.
Calcular o establecer el tonelaje:
Calcule el tonelaje necesario en función de las propiedades y el espesor del material. Ajuste el tonelaje de la prensa plegadora en consecuencia para garantizar un plegado adecuado sin sobrecargar la máquina.
Ajuste la posición del ariete:
Ajuste la posición del ariete para controlar el ángulo de plegado. Esto se hace generalmente configurando el tope trasero y los topes de profundidad en la máquina. Siga el manual o la interfaz de programación de la máquina para realizar estos ajustes con precisión.
Realizar curvas de prueba:
Antes de doblar la pieza de trabajo, realice dobleces de prueba en material de descarte para ajustar con precisión los ajustes del ángulo. Realice cambios incrementales según sea necesario hasta lograr el ángulo deseado.
Comprobar y medir:
Después de ajustar el ángulo, verifique y mida las curvas de prueba utilizando las herramientas de medición adecuadas. Asegúrese de que el producto final cumpla con las especificaciones requeridas.
Ajuste según sea necesario:
Si se necesitan más ajustes, ajuste los parámetros en función de los resultados de las curvas de prueba. Repita el proceso hasta lograr el ángulo deseado de manera uniforme.
Configuración del documento:
Una vez que se logra el ángulo correcto, documente los ajustes de la máquina, incluidos el tonelaje, la posición del ariete y los detalles de las herramientas. Esta documentación sirve como referencia para futuras tareas de plegado similares.
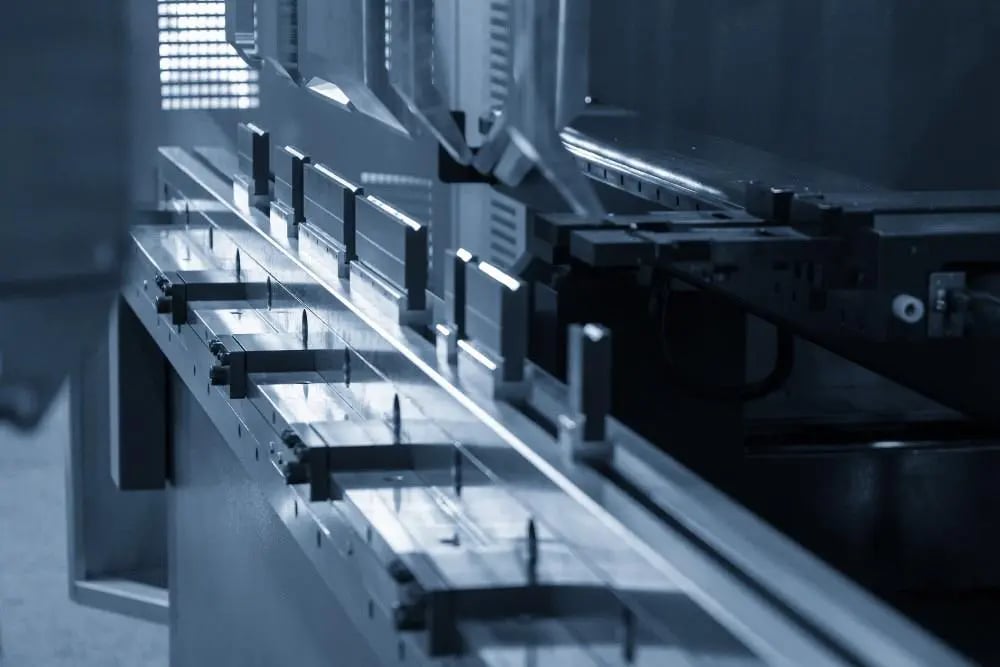
¿Cómo ajustar la longitud de la carrera de la máquina dobladora?
Cómo ajustar manualmente el trazo
1. Encienda el interruptor de límite de la máquina y determine las posiciones de límite superior e inferior para facilitar el ajuste de la carrera.
2. Ajuste manualmente el botón de empuje, alinee el espacio entre el molde inferior y el molde superior y estreche el espacio de presión hasta que cumpla con los requisitos y luego ajuste;
3. Determine las posiciones de carga y descarga y active la función de "posicionamiento automático" en el punto de partida;
4. Según los requisitos, utilice el botón de operación manual para mover la máquina dobladora hacia la derecha o hacia la izquierda hasta que cumpla con los requisitos y determine la carrera, y el trabajo se puede completar automáticamente.
Cómo ajustar automáticamente el trazo
1. En primer lugar, para garantizar la precisión de la carrera de ajuste automático, es necesario instalar algunos sensores pertinentes en la máquina. Estos sensores pueden detectar la posición y el estado de movimiento de la máquina;
2. Al configurar los parámetros de la máquina, la carrera se puede ajustar automáticamente. Solo es necesario sujetar la pieza de trabajo en la máquina y presionar el botón de modo automático para completar el trabajo automáticamente.
3. El modo de ajuste automático requiere configurar las posiciones de límite superior e inferior, calcular automáticamente la longitud de carrera óptima y el ángulo de curvatura en función de la longitud y el ancho de la pieza de trabajo y luego completar automáticamente el trabajo.
Conclusión
En resumen, el ajuste de la carrera del máquina dobladora es un eslabón de operación muy importante y se debe seleccionar el método de ajuste adecuado según los requisitos específicos de la pieza de trabajo. El ajuste manual requiere ciertas habilidades y experiencia, mientras que el ajuste automático requiere la confirmación de los parámetros de la máquina y las posiciones del sensor. Mediante un ajuste razonable de la carrera, se puede mejorar la eficiencia del trabajo y reducir los errores de operación.