La selección de los parámetros del proceso de corte para Máquinas de corte por plasma CNC es crucial para la calidad, velocidad y eficiencia de los resultados del corte.
Para utilizar correctamente una máquina de plasma CNC para un corte rápido y de alta calidad, es esencial tener un conocimiento profundo y dominio de los parámetros del proceso de corte.
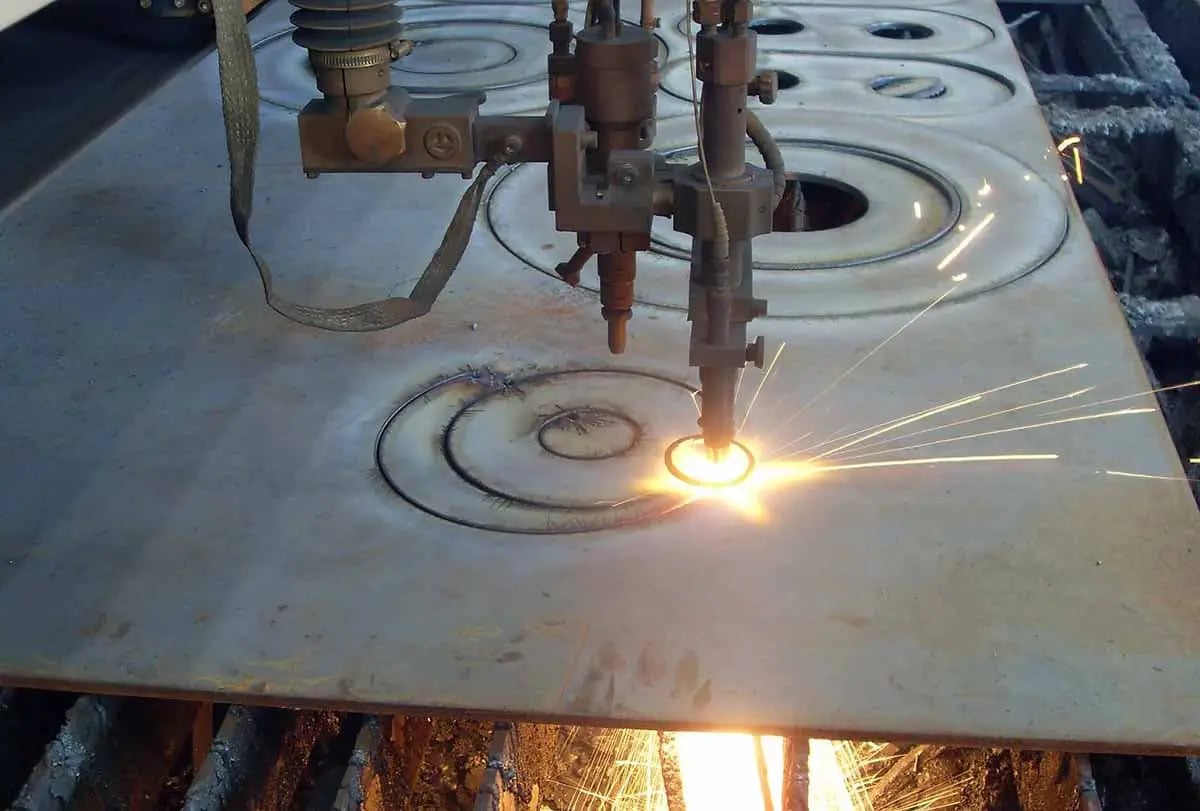
Tabla de contenido
I. Corriente de corte
Es el parámetro más importante del proceso de corte, que determina directamente el espesor y la velocidad de corte, es decir, la capacidad de corte. Sus efectos son los siguientes:
1. A medida que aumenta la corriente de corte, también aumenta la energía del arco, lo que da como resultado una mayor capacidad de corte y una mayor velocidad de corte.
2. A medida que aumenta la corriente de corte, también aumenta el diámetro del arco, haciendo que el corte sea más amplio.
3. Si la corriente de corte es demasiado alta, la boquilla se sobrecalentará, lo que provocará daños prematuros y una disminución de la calidad del corte, o incluso impedirá que se realice un corte normal. Por lo tanto, es necesario elegir la corriente de corte adecuada y la boquilla correspondiente en función del espesor del material antes de cortar.
II. Velocidad de corte
El rango de velocidad de corte óptimo se puede determinar de acuerdo con las instrucciones del equipo o mediante experimentación.
Debido a factores como el espesor del material, el tipo de material, el punto de fusión, la conductividad térmica y la tensión superficial después de la fusión, la velocidad de corte también cambia en consecuencia. Sus principales efectos son los siguientes:
Aumentar moderadamente la velocidad de corte puede mejorar la calidad del corte, es decir, estrechar ligeramente el corte, hacer que la superficie de corte sea más suave y reducir la deformación.
Si la velocidad de corte es demasiado rápida, la energía de la línea de corte será menor que el valor requerido y el chorro no puede expulsar la masa fundida de corte inmediatamente, lo que genera una mayor cantidad de arrastre hacia atrás y escoria colgando en el corte, lo que provoca una disminución en la calidad de la superficie del corte.
Cuando la velocidad de corte es demasiado baja, como la posición de corte es el ánodo del arco de plasma, para mantener la estabilidad del arco mismo, el punto o área del ánodo debe encontrar un lugar para conducir la corriente cerca del corte más cercano, lo que transferirá más calor radialmente al chorro.
Por lo tanto, el corte se hace más ancho y el material fundido de ambos lados del corte se acumula y solidifica en el borde inferior, formando escoria difícil de limpiar. Además, el borde superior del corte forma una esquina redondeada debido al calentamiento y la fusión excesivos.
Cuando la velocidad es extremadamente baja, el arco puede incluso extinguirse. Por lo tanto, la buena calidad de corte y la velocidad de corte son inseparables.
III. Tensión de arco
El voltaje de salida normal de la fuente de alimentación generalmente se considera el voltaje de corte.
Las máquinas de corte por arco de plasma CNC suelen tener un voltaje sin carga y un voltaje de trabajo elevados.
Cuando se utilizan gases con alta energía de ionización, como nitrógeno, hidrógeno o aire, el voltaje necesario para un arco de plasma estable es mayor. Cuando la corriente es constante, un aumento del voltaje significa un aumento de la entalpía del arco y de la capacidad de corte.
Si se reduce el diámetro del chorro mientras se aumenta el caudal de gas al mismo tiempo que aumenta la entalpía, a menudo se obtiene una velocidad de corte más rápida y una mejor calidad de corte.
IV. Gas de trabajo y caudal
Los gases de trabajo incluyen gas de corte, gas auxiliar y algunos equipos también requieren gas de arranque. Por lo general, el gas de trabajo adecuado debe seleccionarse en función del tipo, el espesor y el método de corte del material.
El gas de corte debe garantizar la formación de un chorro de plasma mientras elimina el metal fundido y los óxidos del corte.
Un flujo excesivo de gas puede quitar más calor del arco, acortar la longitud del chorro, provocar una disminución en la capacidad de corte y un arco inestable; un flujo de gas insuficiente puede hacer que el arco de plasma pierda su rectitud necesaria, lo que da como resultado cortes superficiales y también causa fácilmente escoria colgando.
Por lo tanto, el caudal de gas debe estar bien coordinado con la corriente y la velocidad de corte.
El más moderno máquinas de corte por arco de plasma controlar el caudal mediante la presión del gas porque cuando la apertura de la pistola es fija, controlar la presión del gas también controla el caudal.
La presión de gas utilizada para cortar un determinado espesor de material generalmente debe seleccionarse de acuerdo con los datos proporcionados por el fabricante del equipo.
Si hay otras aplicaciones especiales, la presión del gas debe determinarse mediante ensayos de corte reales.
Los gases de trabajo más utilizados son argón, nitrógeno, oxígeno, aire y H35, gas mixto argón-nitrógeno, etc.
1. El gas argón casi no reacciona con ningún metal a altas temperaturas y el arco de plasma del gas argón es muy estable.
Además, la boquilla y el electrodo utilizados tienen una vida útil relativamente larga. Sin embargo, el voltaje del arco de plasma de argón es menor y el valor de entalpía no es alto, lo que da como resultado una capacidad de corte limitada.
En comparación con el corte por aire, su espesor de corte disminuirá aproximadamente en 25%.
Además, en un entorno protector de argón, la tensión superficial del metal fundido es mayor, aproximadamente 30% más alta que en un entorno de nitrógeno.
Por lo tanto, puede haber más problemas de escoria colgada.
Incluso cuando se corta con una mezcla de gas argón y otros gases, se tiende a formar escoria pegajosa. Por ello, actualmente rara vez se utiliza gas argón puro solo para el corte por plasma.
2. El gas hidrógeno se utiliza normalmente como gas auxiliar mezclado con otros gases.
Por ejemplo, el conocido gas H35 (fracción de volumen de hidrógeno de 35%, el resto es argón) es uno de los gases más fuertes en capacidad de corte por arco de plasma, lo que se debe principalmente al gas hidrógeno.
Debido a que el gas hidrógeno puede aumentar significativamente el voltaje del arco, el chorro de plasma de hidrógeno tiene un alto valor de entalpía. Cuando se mezcla con gas argón, la capacidad de corte del chorro de plasma mejora enormemente.
En general, para materiales metálicos con un espesor de más de 70 mm, se suele utilizar argón + hidrógeno como gas de corte. Si se utiliza un chorro de agua para comprimir aún más el arco de plasma de argón + hidrógeno, se puede lograr una eficiencia de corte aún mayor.
3. El nitrógeno es un gas de trabajo de uso común. Para máquinas de corte por plasma CNC
En condiciones de alto voltaje de suministro de energía, el arco de plasma de nitrógeno tiene mejor estabilidad y mayor energía de chorro que el gas argón.
Incluso al cortar materiales con alta viscosidad, como acero inoxidable y aleaciones a base de níquel, la cantidad de escoria que queda suspendida debajo de la incisión también es muy pequeña. El nitrógeno se puede utilizar solo o mezclado con otros gases.
En el corte automatizado, el nitrógeno o el aire se utilizan a menudo como gas de trabajo en la máquina de corte por plasma, y estos dos gases se han convertido en gases estándar para el corte a alta velocidad de acero al carbono. A veces, el nitrógeno también se utiliza como gas de arranque del arco en el corte por plasma de oxígeno.
4. El oxígeno puede aumentar la velocidad de corte de materiales de acero con bajo contenido de carbono.
Cuando se utiliza oxígeno para cortar, el modo de corte es similar al del oxicorte. El arco de plasma de alta temperatura y alta energía hace que la velocidad de corte sea más rápida, pero debe utilizarse junto con electrodos que sean resistentes a la oxidación a alta temperatura.
Al mismo tiempo, el electrodo debe protegerse contra impactos durante el inicio del arco para prolongar su vida útil.
5. El aire contiene aproximadamente una fracción de volumen de nitrógeno de 78%, por lo que la situación de escoria suspendida que se forma al usar aire para cortar es similar a la que se produce cuando se usa nitrógeno para cortar.
El aire también contiene aproximadamente una fracción de volumen de oxígeno de 21% y, debido a la presencia de oxígeno, la velocidad de corte del acero con bajo contenido de carbono material de acero El uso de aire también es elevado. Al mismo tiempo, el aire es también el gas de trabajo más económico.
Sin embargo, cuando se utiliza aire únicamente para cortar, se producen problemas de escoria suspendida, oxidación y aumento de nitrógeno en la incisión. La baja vida útil de los electrodos y las boquillas también puede afectar la eficiencia del trabajo y los costos de corte.
V. Altura de la boquilla
Se refiere a la distancia entre la cara final de la boquilla y la superficie de corte, que constituye una parte de la longitud total del arco. Dado que el corte por arco de plasma generalmente utiliza fuentes de alimentación de corriente constante o de caída pronunciada, la corriente cambia muy poco después de que aumenta la altura de la boquilla.
Sin embargo, aumentará la longitud del arco y hará que aumente el voltaje del arco, lo que aumentará la potencia del arco. Pero al mismo tiempo, también aumentará la pérdida de energía de la columna de arco expuesta al medio ambiente.
Bajo el efecto combinado de estos dos factores, el efecto del primero a menudo se ve completamente compensado por el segundo, lo que puede reducir la energía de corte efectiva y disminuir la capacidad de corte.
Esto generalmente se manifiesta como un debilitamiento de la fuerza del chorro de corte, un aumento de la escoria residual en la parte inferior de la incisión y un redondeo del borde superior.
Además, teniendo en cuenta la forma del chorro de la máquina de corte por plasma, el diámetro del chorro se expande hacia afuera después de salir de la pistola, y el aumento de la altura de la boquilla provocará inevitablemente un aumento en el ancho de la incisión.
Por lo tanto, elegir la altura de boquilla más pequeña posible es beneficioso para mejorar la velocidad y la calidad del corte.
Sin embargo, cuando la altura de la boquilla es demasiado baja, pueden producirse arcos dobles. El uso de boquillas exteriores de cerámica puede establecer la altura de la boquilla a cero, es decir, la cara del extremo de la boquilla entra en contacto directo con la superficie de corte, lo que puede lograr buenos resultados.
VI. Densidad de potencia de corte
Para obtener un arco de plasma de alta compresión para el corte por plasma, la boquilla de corte utiliza una abertura de boquilla pequeña, una longitud de orificio más larga y un efecto de enfriamiento reforzado. Esto puede aumentar la corriente que pasa a través del área de sección transversal efectiva de la boquilla, es decir, aumentar la densidad de potencia del arco.
Sin embargo, la compresión también aumenta la pérdida de potencia del arco, por lo que la energía real utilizada para cortar es menor que la potencia de salida de la fuente de energía, y su tasa de pérdida generalmente está entre 25% y 50%.
Algunos métodos, como el corte por arco de plasma con compresión de agua, pueden tener una tasa de pérdida de energía más alta. Esta cuestión debe tenerse en cuenta en el diseño de los parámetros del proceso de corte o en la contabilidad económica de los costos de corte.
Por ejemplo, el espesor de las placas de metal comúnmente utilizadas en la industria suele ser inferior a 50 mm.
Dentro de este rango de espesor, el corte por arco de plasma convencional a menudo forma un corte con un borde superior más grande y un borde inferior más pequeño, y el borde superior del corte puede provocar una disminución en la precisión del tamaño de la incisión y aumentar el trabajo de procesamiento posterior.
Al utilizar el corte por arco de plasma de oxígeno y nitrógeno de acero al carbono, aluminio y acero inoxidable, cuando el espesor de la placa está dentro del rango de 10-25 mm, el material es más grueso, la verticalidad del borde es mejor y el error de ángulo del borde de corte es de 1 grado a 4 grados.
Cuando el espesor de la placa es inferior a 1 mm, a medida que el espesor de la placa disminuye, el error del ángulo de incisión aumenta de 3-4 grados a 15-25 grados.
En general, se cree que la causa de este fenómeno se debe a la entrada de calor desigual del chorro de plasma en la superficie de corte, es decir, la liberación de energía del arco de plasma en la parte superior de la incisión es mayor que en la parte inferior.
Este desequilibrio de liberación de energía está estrechamente relacionado con muchos parámetros del proceso de la máquina de corte por plasma CNC, como el grado de compresión del arco de plasma, la velocidad de corte y la distancia entre la boquilla y la pieza de trabajo.
Aumentar el grado de compresión del arco puede extender el chorro de plasma de alta temperatura para formar un área de alta temperatura más uniforme y, al mismo tiempo, aumentar la velocidad del chorro, lo que puede reducir la diferencia de ancho de los bordes superior e inferior de la incisión.
Sin embargo, la compresión excesiva de las boquillas convencionales provoca a menudo arcos dobles, que no solo consumen electrodos y boquillas, imposibilitando el proceso de corte, sino que también provocan una disminución de la calidad de la incisión.
Además, la velocidad de corte excesiva y la altura de la boquilla también pueden aumentar la diferencia de ancho entre los bordes superior e inferior de la incisión.
VII. Tabla de parámetros del proceso de corte por plasma
Corriente de corte con protección de aire/plasma de aire de acero con bajo contenido de carbono 130 A
Seleccionar gas | Establecer el flujo de aire de corte | Espesor del material | Voltaje de arco | Distancia entre la antorcha de corte y la pieza de trabajo | Velocidad de corte | Altura inicial de perforación | Retraso en la perforación | |||
Plasma | Gas protector | Plasma | Gas protector. | mm | Voltaje | mm | mm/min | mm | Coeficiente % | Segundo |
Aire | Aire | 72 | 35 | 3 | 136 | 3.1 | 6000 | 6.2 | 200 | 0.1 |
4 | 137 | 3.1 | 4930 | 6.2 | 200 | 0.2 | ||||
6 | 138 | 3.6 | 3850 | 7.2 | 200 | 0.3 | ||||
10 | 142 | 4.1 | 2450 | 8.2 | 200 | 0.5 | ||||
12 | 144 | 4.1 | 2050 | 8.2 | 200 | 0.5 | ||||
15 | 150 | 4.6 | 1450 | 9.2 | 200 | 0.8 | ||||
20 | 153 | 4.6 | 810 | 10.5 | 230 | 1.2 | ||||
25 | 163 | 4.6 | 410 | Empezar desde el borde | ||||||
32 | 170 | 5.1 | 250 |
Corriente de corte de protección de aire/plasma de oxígeno de acero con bajo contenido de carbono 130 A.
Seleccionar gas | Establecer el flujo de aire de corte | Espesor del material | Voltaje de arco | Distancia entre la antorcha de corte y la pieza de trabajo | Velocidad de corte | Altura inicial de perforación | Retraso en la perforación | |||
Plasma | Gas protector | Plasma | Gas protector | mm | Voltaje | mm | mm/min | mm | Coeficiente % | Segundo |
Oxígeno | Aire | 65 | 48 | 3 | 128 | 2.5 | 6500 | 5.0 | 200 | 0.1 |
4 | 129 | 2.8 | 5420 | 5.6 | 200 | 0.2 | ||||
6 | 130 | 2.8 | 4000 | 5.6 | 200 | 0.3 | ||||
10 | 134 | 3.0 | 2650 | 6.0 | 200 | 0.3 | ||||
12 | 136 | 3.0 | 2200 | 6.0 | 200 | 0.5 | ||||
15 | 141 | 3.8 | 1650 | 7.6 | 200 | 0.7 | ||||
43 | 20 | 142 | 3.8 | 1130 | 7.6 | 200 | 1.0 | |||
25 | 152 | 4.0 | 675 | 8.0 | 200 | 1.5 | ||||
32 | 155 | 4.5 | 480 | Empezar desde el borde | ||||||
38 | 160 | 4.5 | 305 |