La calidad de corte por láser El proceso de corte por láser está sujeto a una multitud de factores, lo que lo convierte en una interacción compleja. En el corazón del proceso de corte por láser se encuentra la interacción entre el haz láser y los materiales que se cortan, que se clasifica en dos fenómenos principales: microscópicos y macroscópicos.
Los fenómenos microscópicos profundizan en los intrincados procesos de reacción cuántica que ocurren durante la interacción entre el láser y el material. Mientras tanto, los fenómenos macroscópicos abarcan la absorción, la reflexión y la refracción de los materiales, así como la conversión de energía y la transmisión de los rayos láser.
Más allá de las características intrínsecas del material que se procesa, los factores relacionados con el hardware también influyen en la calidad del corte. Exploremos estos factores juntos.
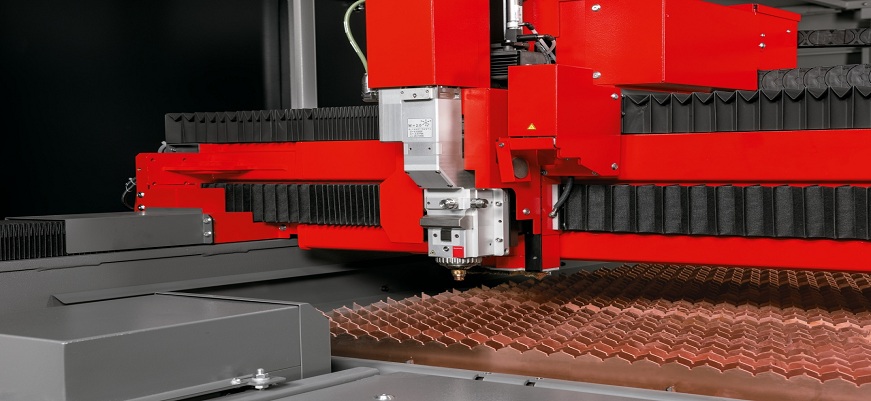
Importancia del control de calidad
El control de calidad tiene un papel insustituible en las empresas. Mediante el muestreo y el control de procesos, las organizaciones pueden mejorar su rendimiento. Lo mismo es válido para el proceso de corte por láser. Sin embargo, surge la pregunta de cómo medir la calidad del corte de metales por láser.
En los textos anteriores hemos hecho hincapié en la importancia de optimizar los parámetros de corte por láser, es decir, la implementación de un mantenimiento preventivo de la cortadora láser. Cuando se trata de cortadoras láser buenas y de alta calidad, la posibilidad de anomalías en el proceso de corte se reduce al mínimo. Sin embargo, se debe prestar atención a otros indicadores clave de rendimiento (KPI) importantes que brindan retroalimentación sobre el nivel de calidad del corte por láser.
Normas de corte por láser
Como una gran parte de los negocios y procesos de las organizaciones actuales están estandarizados y normalizados, se han desarrollado normas que prescriben parámetros de calidad para el corte por láser. La norma ISO DIN EN ISO 9013:2002 define los requisitos para el corte por láser y otros tipos de corte térmico. La norma prescribe el control de los siguientes parámetros de corte:
- metal fundido
- la incisión del corte
- la punción del corte
- líneas de corte
- aspereza
Parámetros de control de calidad
- Formación del metal fundido: el control de este parámetro se realiza normalmente mediante inspección visual del metal que se está cortando. La información obtenida mediante la comprobación se refiere al enfoque del haz láser o a la óptica del cortador láser.
- La incisión del corte: parámetro que depende del material a cortar y que viene determinado por la tolerancia de cada metal de forma diferente. La información que se obtiene al inspeccionar la incisión nos indica el tamaño de la penetración del haz láser en el metal.
- La perforación: la perforación del metal se produce debido a la acción corrosiva y puede cambiar en gran medida la calidad del corte. Este parámetro suele inspeccionarse visualmente y describirse cualitativamente.
- Líneas de corte: las líneas de corte durante el corte por láser están determinadas por la velocidad a la que se corta cada posición. Este parámetro también se inspecciona visualmente y la información proporcionada por la inspección indica la necesidad de ajustar los parámetros de corte en términos de potencia y velocidad.
- Rugosidad: parámetro que influye en la necesidad de manipulación adicional del material después del corte por láser. La rugosidad se define en función del espesor del material que se está cortando.
La calidad de los cortes láser se puede mejorar mediante un mantenimiento constante del cortador láser y un ajuste preciso de los parámetros de corte. Si bien el control de calidad y la optimización de parámetros desempeñan papeles cruciales, sirven como pasos iniciales para lograr resultados de corte óptimos. La eficacia del control de calidad depende de la ejecución de una serie de cortes.
Cuando se realizan múltiples cortes idénticos, es imprescindible un control meticuloso de los parámetros para evitar la repetición de errores en toda la serie. Por ello, la supervisión y el ajuste continuos de los parámetros garantizan operaciones de corte uniformes y sin errores.
Factores que afectan la calidad del corte por láser de las máquinas de corte por láser
Características del haz:
Existe una relación significativa entre el ancho de la incisión del corte láser y el diámetro del punto focal. Debido a que la densidad de potencia y la densidad de energía de la irradiación láser están relacionadas con el diámetro del punto láser, para obtener una mayor densidad de potencia y escala de energía, en el procesamiento de corte láser, el diámetro del punto debe ser lo más pequeño posible.
Potencia del láser:
La magnitud de la potencia del láser afecta directamente el espesor de la placa de acero que se puede cortar. Cuanto mayor sea la potencia, más grueso será el material que se puede cortar. Además, también afecta la precisión dimensional de la pieza de trabajo, el ancho de la costura de corte, la rugosidad de la superficie de corte y el ancho de la zona afectada por el calor.
La potencia del láser tiene un impacto significativo en la velocidad de corte, el ancho de la costura, el espesor del corte y la calidad del corte. El nivel de potencia está determinado por las características del material y el mecanismo de corte. Los materiales con puntos de fusión altos (como las aleaciones) y alta reflectividad superficial (como el cobre y el aluminio) requieren una mayor potencia del láser.
Por ejemplo, una máquina de corte por láser de fibra de chapa metálica de 1500 W no puede lograr el trabajo de una máquina de corte por láser de 6000 W. Muchas veces, si descubre que el efecto de corte no es ideal, es muy probable que haya elegido el modelo de láser incorrecto.
En el proceso de corte por láser, existe una potencia láser que logra la mejor calidad de corte. Con esta potencia láser, pueden producirse fenómenos de corte incompleto o de escoria suspendida. Con una potencia superior, se sobrecalentará.
Velocidad de corte por láser:
La velocidad de corte tiene un impacto significativo en la calidad del corte. La velocidad de corte ideal dará como resultado una línea relativamente suave en la superficie de corte, una sección transversal del material suave y sin rebabas. Cuando la presión del gas auxiliar y la potencia del láser son constantes, existe una relación inversa no lineal entre la velocidad de corte y el ancho de la costura de corte. Si la velocidad de corte es demasiado lenta, es fácil provocar una sobrefusión del material, la costura de corte se ensancha, la zona afectada por el calor aumenta e incluso la sobrefusión de la pieza de trabajo. Cortar demasiado rápido puede provocar que el material no se corte, lo que hace que salpiquen chispas, produzca escoria en la mitad inferior e incluso queme la lente.
Boquillas:
La apertura de la boquilla y la distancia entre la salida de la boquilla y la superficie del material pueden afectar el efecto de corte.
Posición de enfoque:
La posición del foco afecta directamente el ancho de la incisión, la rugosidad de la sección transversal y la adhesión de los residuos. Las diferentes posiciones focales dan como resultado diferentes diámetros del haz y profundidades focales en la superficie del material procesado, lo que provoca cambios en la forma de la costura de corte y afecta el flujo de gas procesado y metal fundido dentro de la sección transversal.
La posición de enfoque es la distancia desde el foco del láser hasta la superficie de la pieza de trabajo, que afecta directamente la rugosidad de la superficie de corte, la pendiente y el ancho de la costura de corte y el estado de adhesión del residuo fundido. Si la posición de enfoque es demasiado avanzada, aumentará el calor absorbido por el extremo inferior de la pieza de trabajo que se está cortando.
A una determinada velocidad de corte y presión de aire auxiliar, hará que el material que se está cortando y el material fundido cerca de la costura de corte fluyan en estado líquido sobre la superficie inferior. Después de enfriarse, el material fundido se adherirá a la superficie inferior de la pieza de trabajo en forma esférica. Si la posición se retrasa, el calor absorbido por la cara del extremo inferior del material que se está cortando disminuirá, de modo que el material en la costura de corte no puede fundirse por completo y algunos residuos afilados y cortos se adherirán a la superficie inferior de la placa.
Por lo general, la posición de enfoque debe estar en la superficie de la pieza de trabajo o un poco más abajo, pero los diferentes materiales requieren diferentes requisitos. Al cortar acero al carbono, la calidad de corte es mejor cuando el enfoque está en la superficie de la placa. Al cortar acero inoxidable, el enfoque debe estar alrededor de la mitad del espesor de la placa para obtener mejores resultados.
Gas auxiliar:
El corte de material requiere el uso de gas auxiliar, principalmente presión de gas y tipo de gas, los cuales pueden afectar la rugosidad de la sección de corte y la generación de escoria.
En el proceso de corte por láser, la presión de aire auxiliar desempeña un papel importante en la eliminación de escoria, el enfriamiento de los materiales y la ayuda a la combustión. Los gases auxiliares incluyen oxígeno, aire comprimido, nitrógeno y gases inertes.
El oxígeno puede participar en la combustión del metal y mejorar la eficiencia de corte, lo que lo hace adecuado para cortar la mayoría de los metales; los gases inertes y el aire son adecuados para cortar ciertos materiales metálicos (como aleaciones de aluminio) y materiales no metálicos, lo que puede prevenir la combustión del material.
Si la presión del gas auxiliar es demasiado alta, aparecerán corrientes de Foucault en la superficie del material, lo que debilitará la capacidad de eliminar materiales fundidos, lo que provocará el ensanchamiento de la costura de corte y una superficie de corte rugosa; si la presión del aire es demasiado baja, el material fundido no se puede eliminar por completo y la escoria se adherirá a la superficie inferior del material. Por lo tanto, la presión del gas auxiliar debe ajustarse durante el corte para obtener la mejor calidad de corte.
Soluciones de calidad de corte por láser para máquinas de corte por láser de fibra
- Configuración óptima de energía: Ajustar la potencia del láser según el tipo y el grosor del material es fundamental para lograr cortes limpios y precisos. Ajustar con precisión los parámetros de potencia garantiza un procesamiento eficiente del material sin provocar zonas excesivamente afectadas por el calor ni bordes ásperos.
- Ajuste de enfoque:El enfoque correcto del haz láser es esencial para mantener la calidad del corte. La calibración y el ajuste periódicos de la posición de enfoque garantizan una calidad del haz y un rendimiento de corte óptimos.
- Selección de gas y control de presión:La elección del gas auxiliar adecuado (como oxígeno, nitrógeno o aire) y el control de su presión eliminan eficazmente el material fundido de la ranura y evitan la oxidación durante el corte. La selección adecuada del gas y el ajuste de la presión contribuyen a mejorar la calidad del filo y a reducir la formación de escoria.
- Mantenimiento de boquillas y lentes:La limpieza e inspección periódicas de las boquillas de corte y las lentes de enfoque son esenciales para evitar la acumulación de residuos y mantener la calidad del haz. Reemplace los componentes desgastados o dañados de inmediato para garantizar un rendimiento de corte constante.
- Tecnología avanzada de cabezal de corte:La actualización a cabezales de corte equipados con funciones avanzadas como ajuste automático de la distancia focal, protección contra colisiones y monitoreo en tiempo real puede mejorar la precisión y la productividad del corte.
- Control dinámico de haz:La implementación de tecnologías de control dinámico del haz, como la conformación y la oscilación del haz, permite un control más preciso de la distribución de la intensidad del rayo láser y mejora la calidad del corte, especialmente en geometrías complejas y esquinas estrechas.
- Manipulación de materiales y fijación:Las técnicas adecuadas de manipulación y fijación de materiales ayudan a minimizar la vibración y la distorsión del material durante el corte, lo que produce cortes más suaves y una precisión dimensional mejorada.
- Parámetros de corte optimizados:El ajuste fino de los parámetros de corte, como la velocidad de corte, la aceleración y la alineación del haz, en función de las propiedades del material y los requisitos de corte, puede mejorar significativamente la calidad y la eficiencia del corte.
- Sistemas de garantía de calidad:La implementación de sistemas de garantía de calidad, como monitoreo en tiempo real, detección automática de defectos y mecanismos de retroalimentación, garantiza una calidad de corte constante y confiable durante todo el proceso de producción.
Al implementar estas soluciones, los operadores pueden optimizar el rendimiento de máquinas de corte por láser de fibra y lograr una calidad de corte superior en una amplia gama de materiales y aplicaciones.