¿Qué es una máquina laminadora de placas?
Una máquina laminadora de placas, también conocida como roladora de placas o máquina laminadora, es un dispositivo mecánico que se utiliza en la metalurgia para doblar placas planas o láminas de metal en formas curvas o cilíndricas. Estas máquinas se utilizan comúnmente en industrias como la fabricación, la construcción, la construcción naval y la fabricación de metales.
La función principal de una máquina laminadora de placas es aplicar fuerza a una placa o lámina metálica plana, haciendo que se doble alrededor de un eje central. Este proceso implica pasar el metal entre una serie de rodillos que ejercen presión sobre el material, dándole gradualmente la forma deseada. Las máquinas laminadoras de placas pueden producir una variedad de formas, incluidos cilindros, conos y arcos, según la configuración de los rodillos y las especificaciones de la máquina.
Las máquinas laminadoras de placas vienen en diferentes tipos y tamaños para adaptarse a diversas aplicaciones y espesores de material. Algunas máquinas se operan manualmente, lo que requiere que el operador ajuste los rodillos y alimente el material a mano, mientras que otras son totalmente automáticas o semiautomatizadas, con controles hidráulicos o eléctricos para doblar y dar forma con precisión.
Estas máquinas son esenciales en las industrias donde se requieren componentes metálicos curvos o cilíndricos, como en la fabricación de tanques, tuberías, recipientes a presión y componentes estructurales. Las máquinas laminadoras de placas permiten a los fabricantes producir formas complejas con gran precisión y eficiencia, lo que las convierte en herramientas indispensables en las operaciones modernas de metalistería.
Sin embargo, las fracturas de rodillos pueden interrumpir las operaciones y generar tiempos de inactividad costosos. Comprender las causas, las medidas preventivas y las soluciones es esencial para mantener la eficiencia y la productividad de la máquina.
Introducción:
Máquinas laminadoras de placas Son equipos cruciales en diversas industrias, que facilitan la conformación de metales en las formas deseadas. Sin embargo, las fracturas de rodillos pueden interrumpir las operaciones y generar costosos tiempos de inactividad. Comprender las causas, las medidas preventivas y las soluciones es esencial para mantener la eficiencia y la productividad de las máquinas.
Causas de fractura de rodillos:
Calidad del material:Los materiales de mala calidad utilizados en la construcción de rodillos pueden provocar fracturas prematuras. Los rodillos de calidad fabricados con materiales duraderos, como el acero endurecido, son menos susceptibles a las fracturas.
Sobrecarga:Una presión o carga excesiva sobre los rodillos que supere su capacidad puede provocar tensión y, en última instancia, fractura. Respetar los límites de carga recomendados es fundamental para evitar fracturas relacionadas con la sobrecarga.
Fatiga:El uso continuo a lo largo del tiempo puede debilitar los rodillos y provocar fracturas por fatiga. El mantenimiento y la inspección regulares ayudan a identificar problemas relacionados con la fatiga antes de que se agraven.
Desalineación:La alineación incorrecta de los rodillos puede provocar una distribución desigual de la tensión, lo que puede provocar fracturas. Para evitar este problema, es necesario realizar controles y ajustes periódicos de la alineación.
Corrosión:La exposición a elementos corrosivos puede degradar los materiales de los rodillos, lo que aumenta el riesgo de fracturas. Las medidas adecuadas de almacenamiento y protección, como recubrimientos o lubricantes, pueden mitigar los daños relacionados con la corrosión.
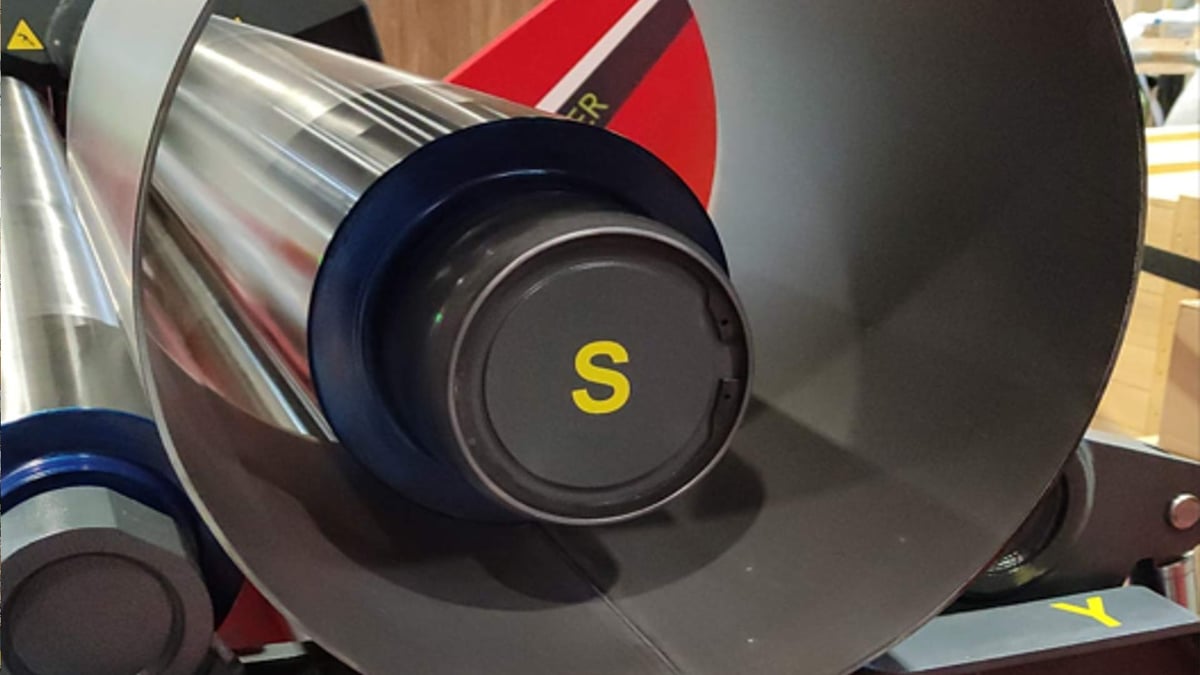
Medidas preventivas:
Inspección de calidad:Priorice los rodillos fabricados con materiales de alta calidad y realice inspecciones exhaustivas antes de la instalación para garantizar su integridad.
Gestión de carga:Respete las capacidades de carga recomendadas y evite sobrecargar la máquina para evitar fracturas relacionadas con el estrés.
Mantenimiento regular:Implemente una rutina de mantenimiento programada, que incluya lubricación, controles de alineación e inspecciones visuales, para identificar posibles problemas de manera temprana.
Comprobaciones de alineación:Inspeccione y ajuste periódicamente la alineación de los rodillos para garantizar una distribución uniforme de la tensión y minimizar el riesgo de fracturas.
Protección contra la corrosión:Implemente medidas para proteger los rodillos de la corrosión, como aplicar recubrimientos o utilizar materiales resistentes a la corrosión.
Soluciones a la fractura de rodillos:
Reemplazo:En caso de fracturas o daños graves, es necesario reemplazar los rodillos afectados con repuestos de alta calidad para restaurar la funcionalidad de la máquina.
Reparar:Las fracturas menores pueden repararse mediante técnicas de soldadura o mecanizado. Sin embargo, asegúrese de que las reparaciones cumplan con los estándares de seguridad y calidad para evitar problemas posteriores.
Actualizaciones:Considere actualizar a materiales de rodillos más resistentes o más duraderos para mitigar el riesgo de fracturas futuras y mejorar la longevidad de la máquina.
Capacitación:Brindar a los operadores la capacitación adecuada sobre la operación, el mantenimiento y los protocolos de seguridad de la máquina para evitar el mal uso o manejo inadecuado que pueda provocar fracturas.
Conclusión:
Máquina laminadora de placas Las fracturas de rodillos pueden interrumpir las operaciones y generar costos significativos si no se abordan de inmediato. Al comprender las causas, implementar medidas preventivas y emplear soluciones adecuadas, las empresas pueden minimizar el tiempo de inactividad, mejorar la productividad y prolongar la vida útil de sus equipos. Priorizar los protocolos de calidad, mantenimiento y seguridad es clave para mitigar el riesgo de fracturas de rodillos y garantizar operaciones sin problemas en entornos industriales.