Seleccionar lo correcto Herramientas para prensa plegadora es esencial para lograr resultados precisos en operaciones de plegado de chapa metálica. Las prensas plegadoras son una piedra angular en la fabricación de metales moderna y su uso generalizado ha dado lugar a una variedad de opciones de herramientas diseñadas para adaptarse a diferentes longitudes y formas de pliegues.
En este artículo, se profundizará en los detalles de la selección de herramientas para prensas plegadoras. La información brindada beneficiará tanto a los operadores novatos como a los profesionales experimentados en el campo. Obtendrá una comprensión de los materiales utilizados para las herramientas para prensas plegadoras, los diversos estilos disponibles, los diferentes tipos y los factores clave a tener en cuenta al elegir las herramientas adecuadas para su prensa plegadora.
¿Qué son las herramientas para prensa plegadora?
Las herramientas de la prensa plegadora son los equipos, como las matrices y los punzones, que se utilizan en la prensa plegadora para crear el pliegue en una chapa metálica. Las herramientas de la prensa plegadora no están integradas en la máquina, sino que son una parte intercambiable de la máquina que se utiliza en función del tipo de trabajo en particular. Las herramientas de la prensa plegadora son los accesorios que entran en contacto con la pieza de trabajo.
¿Cuál es el propósito principal de las herramientas de prensa plegadora?
El propósito principal de Herramientas para prensa plegadora El objetivo es que la máquina sea adecuada para distintos trabajos de plegado de metales. Sin herramientas para prensas plegadoras, una máquina de prensa plegadora estará muy limitada en cuanto al tipo, la forma y el tamaño del plegado que puede realizar.
Sin embargo, las herramientas de las prensas plegadoras amplían las aplicaciones de la máquina. Se pueden formar diferentes ángulos y radios de plegado simplemente cambiando las herramientas. Por lo tanto, las prensas plegadoras pueden adaptarse rápidamente a los cambios de trabajo.
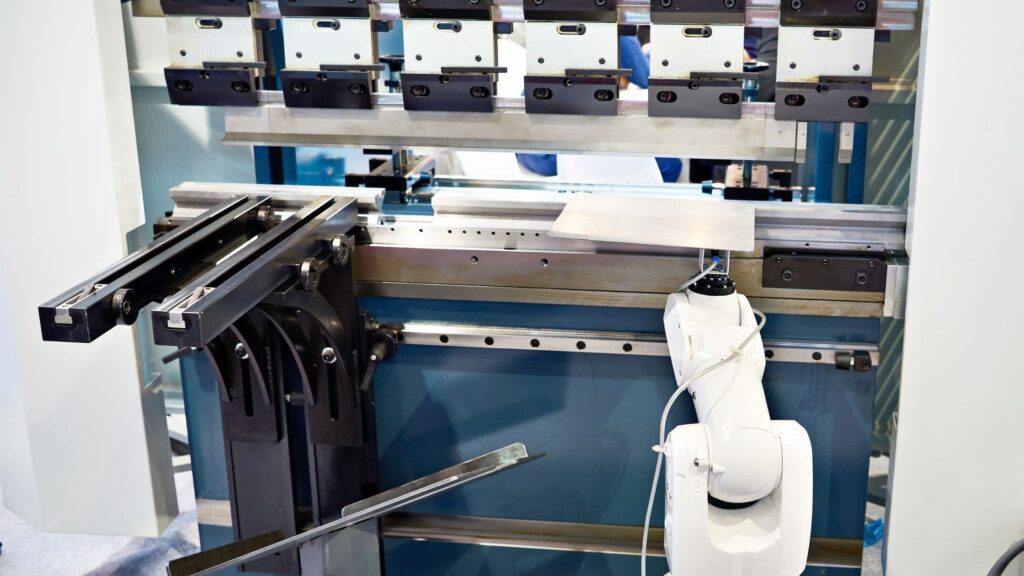
¿Cuáles son los elementos clave de las herramientas de prensa plegadora?
Hay muchos elementos diferentes que funcionan juntos para que una prensa plegadora funcione. Estos elementos son:
Principales tipos de herramientas (punzones)
El punzón es la herramienta que se encuentra en la parte superior de la pieza y que ejerce sobre ella la fuerza necesaria para realizar el plegado. Es muy importante utilizar punzones de buena calidad, ya que son la parte central encargada de ejercer la fuerza necesaria en el proceso de plegado del metal.
Existen muchos tipos de punzones disponibles para distintos trabajos. La selección del punzón debe realizarse solo después de conocer los conceptos básicos de cada tipo de punzón para prensa plegadora. Estos diferentes punzones son:
Punzón estándar
El punzón estándar es la herramienta de plegadora más utilizada. Su cuerpo más grueso y su punta estrecha ejercen un mayor tonelaje que resulta útil para doblar el material más grueso. El lado interior tiene una ligera curva cóncava con los lados exteriores planos. Esto permite doblar una pestaña más corta.
Punzón de ángulo agudo
El punzón de ángulo agudo se utiliza para doblar ángulos muy cortos. Los punzones de ángulo agudo se suelen acortar como punzones agudos. Por lo general, estos punzones se utilizan cuando el ángulo de doblado necesario es de 30° o menos. Estos punzones también pueden doblar fácilmente ángulos más grandes, como 60°. Estos punzones tienen una punta afilada con un cuerpo generalmente voluminoso.
Punzón estrecho
Un punzón estrecho es uniforme en toda su longitud y de poco espesor. Estos punzones se utilizan cuando hay poco espacio libre disponible y otros punzones podrían no encajar fácilmente. También se lo conoce como punzón de espada. Una aplicación común de un punzón estrecho es para cerrar un perfil cuadrado o de tipo caja.
Perforadora de faja
Un punzón de hoja es un tipo de herramienta con un cuerpo muy estrecho y una punta en ángulo que se dobla hacia el interior de una prensa plegadora. La punta en ángulo permite trabajar alrededor de las esquinas y crear curvas. Una aplicación común de un punzón de hoja es fabricar marcos y hojas de puertas.
Golpe de cuello de cisne
Los punzones de cuello de cisne se utilizan para aplicaciones de marcado. Se utilizan para crear perfiles en U con nichos en la pieza de trabajo. La forma de los punzones de cuello de cisne se crea especialmente para que las patas de la pieza de trabajo doblada no colisionen con la herramienta. Una variación de este estilo es el punzón de cuello de cisne, que también se utiliza para el perfilado en U. La forma de nicho de los punzones de cuello de cisne y cuello de cisne crea una línea de fuerza sin soporte. Por lo tanto, estos punzones son más débiles en comparación con otras alternativas. Pueden manejar un tonelaje menor.
Golpe de sacudida
El punzón de doblez es una herramienta especial para prensas plegadoras que se utiliza para hacer pliegues en las esquinas. El punzón de doblez tiene un perfil más delgado, lo que lo hace extremadamente útil para crear pliegues en forma de S. Estos no son punzones muy comunes, a menudo se utilizan para trabajos de selección de punzones especializados.
Punzón superior de radio
El punzón de punta redondeada tiene una punta redondeada en lugar de las puntas afiladas que tienen otros punzones. Esto crea una curva en forma de U en lugar de una curva aguda en forma de V. Este punzón generalmente se combina con una matriz en forma de U para lograr una esquina correctamente redondeada.
Tipos de herramientas inferiores (matrices)
Una matriz es una herramienta hueca que se coloca debajo de una pieza de trabajo para brindar soporte y precisión para el proceso de doblado. Las matrices absorben toda la fuerza ejercida por el punzón, por lo que también están hechas de materiales de alta resistencia. Hay muchas formas y tamaños diferentes de matrices disponibles para adaptarse a diversas operaciones. Las formas de matrices más comunes son:
Matriz en V simple
Una matriz en V simple tiene una cavidad en forma de "V" ahuecada en la herramienta. También se las conoce como matriz en "V" simple. Son las matrices de prensa plegadora más utilizadas debido a su amplia versatilidad. La selección de matrices en V simple se realiza según la regla del 8. Establece que la longitud de la abertura de la matriz en V debe ser 8 veces el espesor del material.
Troqueles en V autocentrantes de dos vías
Las matrices en V autocentrantes de dos vías tienen dos cavidades en forma de V colocadas en paralelo. Esto proporciona un flujo de trabajo más rápido en comparación con una matriz en V única. No es necesario volver a utilizar las herramientas en caso de que se necesite otro ángulo de plegado.
Troquel Multi V
Las configuraciones de matriz en V múltiple tienen una cantidad de cavidades en V dispuestas alrededor de la matriz. La cantidad de cavidades en V puede variar desde 3 en adelante. Una matriz en V múltiple agrega la variedad de opciones de doblado disponibles en una sola herramienta. Los cambios en el ángulo de doblado o el espesor del material se pueden lograr con una simple rotación de la matriz.
Matrices para corrugado
Las matrices corrugadoras tienen un patrón corrugado en la parte inferior. Estas matrices se utilizan en requisitos específicos en los que la chapa doblada requiere el mismo patrón en la superficie exterior.
Matrices para aplanar y dobladillar
Se utiliza una matriz de aplanamiento y dobladillo para doblar toda la longitud de la brida en un ángulo agudo y aplanarla por completo. La herramienta inferior viene en dos variantes: con resorte y con sección en U.
Matrices para formación de canales
Una matriz de formación de canales crea un canal en forma de "U" sobre una chapa plana. Para crear un canal en forma de U se necesitan dos pasadas de matrices en V tradicionales. Sin embargo, una matriz de formación de canales puede realizar el trabajo en una sola pasada.
Portaherramientas
Un portaherramientas para prensa plegadora es un accesorio muy útil para montar las herramientas en la prensa plegadora. Los portaherramientas modernos vienen con características productivas, como cambios rápidos de herramientas. Un portaherramientas de buena calidad también aumenta la precisión del proceso de plegado al minimizar la vibración de la herramienta.
Tope trasero
El tope trasero de una prensa plegadora se utiliza para alinear con precisión la pieza de trabajo para lograr un plegado preciso. El tope trasero se puede mover en el eje X y tiene varios topes y bloques. Estos topes detendrán el proceso de plegado una vez que se alcance la longitud de plegado requerida. Una configuración correcta del tope trasero mejora la repetibilidad y la consistencia del proceso de plegado de la prensa plegadora.
Sistema de coronación
Un sistema de abombamiento es un tipo de herramienta de plegadora que compensa la deflexión que se produce durante la deformación del cabezal y de la mesa de trabajo durante el proceso de plegado. Un sistema de abombamiento es especialmente indispensable cuando se trata de plegado de chapas de gran tamaño debido a la gran deflexión que se produce.
Para utilizar de forma eficaz el sistema de bombeo es necesario conocer la deformación y la deflexión de la prensa plegadora. Hay dos tipos diferentes de sistemas de bombeo disponibles: el sistema de bombeo hidráulico y el sistema de bombeo mecánico.
Dispositivos de seguridad para prensas plegadoras
Los dispositivos de seguridad de las prensas plegadoras son herramientas secundarias que se instalan en la prensa plegadora para garantizar la seguridad del operador, la pieza de trabajo y la máquina en sí. Los distintos modelos de prensas plegadoras vienen con diferentes dispositivos de seguridad. Los sistemas de seguridad de prensas plegadoras más comunes son:
- Centinela láser: El sistema Laser Sentry coloca varios rayos láser alrededor del troquel. Cuando cualquier presencia interrumpe los rayos láser, el sistema Laser Sentry detiene inmediatamente el funcionamiento de la máquina y retrae el troquel. Esto proporciona un alto nivel de seguridad al operador y garantiza que sus extremidades no sufran daños durante el flujo de trabajo de la prensa plegadora.
- Cortinas de luz: Las cortinas de luz son un dispositivo de detección de presencia común que proporciona seguridad automática al operador sin necesidad de ninguna configuración. Funcionan de manera similar al sistema de centinela láser. Cuando se interrumpe el flujo de las cortinas de luz, el sistema de seguridad detiene el funcionamiento de la máquina de inmediato y sin demora.
- Guardias: Las protecciones de la prensa plegadora están presentes en los laterales y en la parte trasera de la máquina. Las protecciones laterales impiden la entrada de los brazos del operador o de cualquier objeto extraño entre la matriz y el punzón. Las protecciones traseras impiden la interferencia con el tope trasero y otros componentes detrás de la prensa plegadora.
- Control con dos manos: El control a dos manos requiere que el operador use ambas manos para iniciar el ciclo de la prensa plegadora. Esto garantiza que el operador no inicie la máquina accidentalmente cuando una de sus manos esté entre la abertura de la matriz y el punzón. El control a dos manos es más económico que el láser centinela y las cortinas de luz. Sin embargo, reduce ligeramente la velocidad de toda la operación.
Estructura de las herramientas de la prensa plegadora
Las herramientas de prensa plegadora se dividen en punzón y matriz, que se utilizan para la formación y separación de moldes de estampación de chapa metálica. El molde utilizado para la formación tiene una cavidad y el molde utilizado para la separación tiene un borde cortante.
Selección de materiales:
Generalmente se utilizan T8 o T10, T10A y el mejor material 42CrMo, que requiere principalmente alta resistencia, alta tenacidad y buena resistencia al desgaste. El acero para matrices de trabajo en frío Cr12MoV es un buen material. El rendimiento de uso puede ser satisfactorio y el rendimiento del proceso es bueno, el precio será más alto. 42CrMo es un acero templado y revenido de aleación de alta resistencia con alta resistencia y tenacidad y puede trabajar por debajo de los 500 grados.
Condiciones de uso:
1. Encienda la máquina dobladora, gire el interruptor de llave, presione la bomba de aceite para iniciar y la bomba de aceite de la máquina dobladora comenzará a girar. En este momento, la máquina aún no ha comenzado a funcionar.
2. El ajuste de la carrera requiere una prueba de funcionamiento cuando se inicia oficialmente el trabajo de doblado con el molde de la máquina dobladora. Cuando la matriz superior de la máquina dobladora desciende hasta el fondo, debe haber un espacio de espesor de placa. De lo contrario, provocará daños en el molde y la máquina. El ajuste de la carrera también tiene un ajuste rápido eléctrico y un ajuste fino manual.
3. Para la selección de la ranura de la matriz de la máquina dobladora, generalmente se selecciona una ranura de 8 veces el ancho del espesor de la placa. Si dobla una placa de 4 mm, debe elegir una ranura de aproximadamente 32.
4. Compruebe la superposición y la firmeza de los moldes superior e inferior de la máquina dobladora; compruebe si cada dispositivo de posicionamiento cumple con los requisitos de procesamiento. Compruebe con frecuencia la superposición de los moldes superior e inferior; si las instrucciones del manómetro cumplen con las normas.
5. Cuando se dobla la lámina, se debe compactar para evitar que se levante y lastime al operador durante el doblado.
6. Se debe cortar el suministro de energía al ajustar la matriz de chapa metálica y se debe detener la operación.
7. Al cambiar la apertura de la matriz inferior de la máquina dobladora variable, no se permite que ningún material entre en contacto con la matriz inferior.
8. Está prohibido utilizar matrices de máquinas dobladoras para doblar placas de hierro de gran espesor o placas de acero endurecido, aceros de aleación de alto grado, aceros cuadrados y láminas que excedan el rendimiento de la máquina dobladora de chapa metálica para evitar daños a la máquina herramienta.
9. Apague la máquina dobladora y coloque bloques de madera en los moldes inferiores debajo de los cilindros a ambos lados para bajar la placa deslizante superior sobre los bloques de madera. Primero salga del programa del sistema de control y luego corte el suministro de energía.
Ajuste de la instalación:
Al instalar las herramientas de la prensa plegadora, asegúrese de verificar el estado del equipo, luego instálelo y depúrelo de acuerdo con los pasos y preste atención a la seguridad personal durante la depuración.
Ajuste de la máquina: Al instalar las herramientas de la prensa plegadora, primero debe comprender el rendimiento de la máquina, encender la máquina dobladora, ajustarla y verificarla con paciencia, y ver si la máquina ha usado polvo y virutas de hierro anteriormente. Evite problemas innecesarios para un uso posterior.
Ajuste del recorrido del control deslizante: En primer lugar, compruebe si la relación entre el espesor del molde de la máquina dobladora y los módulos superior e inferior es normal. El control deslizante general debe controlarse en el punto de conmutación de la línea de carrera. Se debe prestar atención a esto, de lo contrario, el molde no se utilizará con normalidad, pero algunas personas aún cometen este tipo de errores a menudo.
Ajuste del módulo de carrera: Después de ajustar el estándar de carrera del deslizador, el siguiente paso es ajustar el punto límite superior del módulo. En términos generales, cuando el módulo está en el punto más alto, se deben ajustar el módulo y el interruptor. De esta manera, se puede hacer fluir la posición de reposo del módulo y, a través de algunas de las operaciones anteriores, se puede aumentar considerablemente la eficiencia de producción. En este proceso, también es necesario reducir la velocidad del módulo. Debido a que el módulo debe desacelerarse cuando está en el punto muerto inferior, lo que protege la máquina y el molde.
Ajuste del espacio: Finalmente, se ajusta el espacio entre los moldes de la máquina dobladora. Primero se mide el espacio entre el módulo superior y el módulo inferior y se debe determinar el espacio razonable en función de la placa doblada.
Ajuste del ángulo: El ajuste del ángulo de curvatura también es el eslabón más importante. La selección del ángulo debe estar relacionada con los requisitos del producto. En términos generales, al doblar un molde de 90°, el ángulo debe ajustarse para que sea mayor que el ángulo entre los dos lados. A veces puede resultar ajustado. Se puede solucionar ajustando los tornillos de la máquina. Después del ajuste, si el producto no cambia según la demanda, no lo modifique nuevamente. Luego, al doblar, use el manómetro para calcular el número de presión preciso y ajuste la presión. Para no causar astillas en el molde.
Procedimientos operativos de herramientas para prensas plegadoras
Las herramientas de prensa plegadora se dividen en moldes de máquina dobladora manual, máquinas dobladoras hidráulicas y herramientas de prensa plegadora CNC. Las herramientas de prensa plegadora hidráulica se pueden dividir en sincronización de eje de torsión, sincronización máquina-hidráulica y sincronización electrohidráulica según el método de sincronización. Las herramientas de prensa plegadora hidráulica se pueden dividir en tipo de movimiento ascendente y tipo de movimiento descendente según el modo de movimiento. Incluye soporte, banco de trabajo y placa de sujeción. El banco de trabajo se coloca sobre el soporte.
El banco de trabajo se compone de una base y una placa de presión. La base está conectada a la placa de sujeción mediante una bisagra. La base se compone de una carcasa, una bobina y una tapa, y la bobina se coloca sobre la carcasa. Dentro del hueco, la parte superior del hueco está cubierta con una placa de cubierta. Preste atención a los siguientes puntos durante el funcionamiento:
1. Cumplir estrictamente con los procedimientos operativos seguros de los trabajadores de máquinas herramienta y usar el equipo de protección laboral según sea necesario.
2. Antes de comenzar, debe verificar cuidadosamente si el motor, el interruptor, el circuito y la conexión a tierra son normales y firmes, y verificar que las partes de control y los botones del equipo estén atascados en la posición correcta.
3. Verificar la coincidencia y firmeza de los moldes superior e inferior; verificar si cada dispositivo de posicionamiento cumple con los requisitos de procesamiento.
4. Cuando la placa deslizante superior y cada eje de posicionamiento no estén en el origen, ejecute el programa de retorno al origen.
5. Una vez que el equipo se haya puesto en marcha, déjelo funcionar en seco durante 1 o 2 minutos y deslícelo por completo 2 o 3 veces. Si se produce algún ruido anormal o un mal funcionamiento, deténgalo de inmediato, elimine el problema y deje de trabajar hasta que todo vuelva a la normalidad.
6. Durante el trabajo, debe haber una persona al mando, de modo que los operadores y el personal de alimentación y supresión cooperen estrechamente para garantizar que el personal que coopera esté en una posición segura antes de emitir la señal de flexión.
7. Cuando se dobla la lámina, se debe compactar para evitar que se levante y lastime a las personas durante el doblado.
8. Se debe cortar el suministro de energía al ajustar el molde de prensa de chapa metálica y continuar después de detener la operación.
9. Al cambiar la apertura del molde inferior variable, no permita que ningún material entre en contacto con el molde inferior.
10. Cuando la máquina herramienta esté en funcionamiento, no se permitirá que nadie permanezca detrás de ella.
11. Está estrictamente prohibido doblar la sábana solo por un extremo.
12. Si durante el funcionamiento se detectan errores en la pieza de trabajo o el molde, se debe detener y corregir. Está estrictamente prohibido corregirlos con las manos para evitar lesiones en las manos.
13. Está prohibido doblar placas de hierro de gran espesor o placas de acero templado, aceros aleados de alto grado, aceros cuadrados y láminas que excedan el rendimiento de la máquina dobladora de chapa para evitar dañar la máquina herramienta.
14. Verifique con frecuencia la superposición de los moldes superior e inferior; si las instrucciones del manómetro cumplen con las regulaciones.
15. Detenga inmediatamente la máquina si ocurre alguna anomalía, verifique la causa y elimínela a tiempo.
16. Antes de apagar, coloque bloques de madera en los moldes inferiores debajo de los cilindros en ambos lados para bajar la placa deslizante superior sobre los bloques de madera.
17. Primero salga del programa del sistema de control y luego corte la fuente de alimentación.
La herramienta adecuada para el trabajo
El viejo dicho que te enseñó tu padre sobre seleccionar “la herramienta adecuada para el trabajo” no solo se aplica a tu caja de herramientas. Cualquier herramienta que entre en contacto con una pieza de trabajo (ya sea un martillo, una broca o una cuchilla de corte) debe elegirse con cuidado. A pesar del enorme tonelaje que una prensa plegadora aporta a tus proyectos de fabricación, tu máquina es tan buena como las herramientas de prensa plegadora que le colocas.
La selección del punzón o matriz incorrectos para una prensa plegadora no solo conlleva el riesgo de provocar un plegado deficiente, sino que también puede generar el peligro muy real de agrietamiento.o explotando—Herramientas. Por el bien del trabajo y del personal, elija siempre las herramientas de prensa plegadora adecuadas tanto para su taller como para el trabajo en cuestión.
Principios básicos de selección de herramientas
Las reglas básicas para la selección de herramientas para prensa plegadora son simples:
- Compre una variedad de punzones y matrices de alta calidad para abastecer su tienda.
- Utilice el tipo correcto de punzón y matriz para el trabajo de doblado en el que está trabajando.
- Reconozca que los dos principios anteriores son sólo eso:principiosTéngalos en cuenta mientras se propone ahora la tarea de Realmente aprendiendo sobre herramientas para prensas plegadoras y aplicar lo aprendido para hacer ambas cosas correctamente.
Es conveniente que el propietario o el operador de una prensa plegadora realice un curso y compre uno o dos libros sobre herramientas para prensas plegadoras para comprender realmente el tema. Comprar la primera pieza de herramienta que vea, especialmente si puede conseguirla a un "buen precio", puede terminar costándole bastante al final. Cuando compre neumáticos para su vehículo, probablemente investigue un poco. Lo mismo se aplica a la compra de herramientas para su freno (u otras máquinas para trabajar metales).
Por lo general, el conocimiento suficiente para comprar los mejores neumáticos termina allí (tal vez con la compra de neumáticos para nieve que se cambian dos veces al año), pero las herramientas de la prensa plegadora se cambian a diferentes configuraciones con mucha frecuencia. Es como comprar un juego de neumáticos para cada condición de la carretera: pavimento caliente, cemento frío, grava, barro, lluvia, aguanieve, nieve en polvo, hielo, granizo, etc.
La mejor marca de herramientas del mundo no le servirá de mucho si selecciona el punzón o la matriz incorrectos para un trabajo, así que conozca cada tipo y aprenda para qué se utilizan y cuándo.
Cómo elegir las herramientas de prensa plegadora para un taller
Algunas pautas que pueden ayudar a iniciar el proceso de compra de buenas herramientas para un taller:
- Compre herramientas de alta precisión rectificadas y endurecidas fabricadas con tolerancias dentro del rango de 0,0004 pulgadas. Las herramientas de estilo europeo están rectificadas con precisión con una tolerancia cercana a ±0,0005″ y están extremadamente endurecidas. Las herramientas de estilo New Standard también están rectificadas con precisión para lograr mayor precisión.
- Todas las herramientas deben tener la misma altura para eliminar la necesidad de realizar ajustes constantes de la máquina y sus dispositivos de soporte entre proyectos. También permitirá que las nuevas herramientas coincidan con las piezas antiguas.
- Compre herramientas en secciones segmentadas de diferentes longitudes. No solo son fáciles de manejar, sino que, como los bloques de construcción de un niño, le permiten organizar las piezas en fila para crear herramientas de la longitud que necesite para el trabajo.
- Aprenda sobre punzones y matrices especializados y sepa cuándo es mejor comprarlos para utilizarlos en trabajos más complicados.
- Esté dispuesto a invertir en un nuevo sistema de sujeción y en herramientas compatibles, si es necesario. Las herramientas de estilo americano tradicionales tienen un área de sujeción más pequeña. Las de estilo europeo tienen una superficie de sujeción más grande, lo que las hace más seguras y precisas. Las herramientas de estilo New Standard de Wila tienen un sistema de sujeción automática para cambios rápidos de herramientas y un asentamiento de herramientas muy preciso. Los punzones de carga frontal y asentamiento automático son ideales por su facilidad, precisión y seguridad.
Selección de herramientas de prensa plegadora para un trabajo específico
Algunos consejos recomendados para ayudar a elegir el mejor punzón y matriz para un trabajo:
- Comprenda las diferencias entre el doblado por aire, el doblado por abajo y el acuñado, y sepa cuándo utilizar cada uno. El doblado por aire, que implica dejar un espacio de aire entre el material y la parte inferior de la matriz en V, es el proceso estándar, pero habrá casos en los que el material deba tocar la parte inferior de la matriz, ya sea ligeramente (doblado por abajo) o en gran medida (acuñado).
- Convierta la tabla de tonelaje de plegado con aire en su mejor amiga. Si su plegadora no viene con una tabla incorporada, busque una en Internet para imprimirla y pegarla en su máquina. Conociendo únicamente el espesor del material y el radio de plegado interior deseado, podrá calcular a partir de la tabla la abertura de troquel en V necesaria, la longitud mínima de brida que se puede doblar y el tonelaje por pie de material para realizar el plegado.
- Aplique la regla de ocho. Si no sabe cuál será el radio de curvatura interior, una guía es seleccionar una abertura en V que sea de seis a diez veces el espesor del material que se va a doblar, es decir, aproximadamente ocho veces en promedio (que es la fórmula que se usa en la mayoría de las tablas de doblado). Cuando no se puede encontrar una coincidencia, redondee al siguiente troquel más cercano y estará cerca de lo que necesita y podrá experimentar a partir de allí.
- No intente elegir un punzón hasta que haya determinado una matriz que tenga la apertura en V adecuada para el trabajo.
- Preste atención a la capacidad máxima de tonelaje de la matriz en cuestión. Para bridas cortas, la apertura en V correcta puede requerir más tonelaje del que puede manejar una matriz específica.
- Seleccione un punzón con una punta cuyo radio sea aproximadamente la mitad del espesor del material si va a doblar acero dulce o acero inoxidable. Para el aluminio blando, el radio de la punta puede tener que ser idéntico al radio interior de la curva.
- Sepa cómo compensar la recuperación elástica del material que se está doblando. Por ejemplo, debido a la mayor resistencia a la tracción del acero inoxidable, suele ser necesario doblarlo en uno o dos grados para permitir que la recuperación elástica devuelva el material al ángulo deseado. Para un doblez de 90°, se suele recomendar utilizar un punzón de 88° para doblar acero inoxidable.
- Aprenda los diferentes estilos de punzones y para qué se utilizan, como los punzones agudos, que se utilizan para doblar ángulos muy pequeños, y los punzones de cuello de cisne con su forma grande y cóncava, que se utilizan para hacer canales y perfiles en U donde de lo contrario una brida impactaría el costado de un punzón estándar.
Análisis de caso específico de selección de matrices para prensas plegadoras
Caso 1 Selección de herramientas para procesar placas de acero inoxidable
La fábrica necesita procesar placas de acero inoxidable 304 con un espesor de 2 mm, un ángulo de doblado de 90° y una longitud de doblado de 1000 mm. Teniendo en cuenta la alta solidez del acero inoxidable, se produce un efecto de recuperación elástica (partes de los materiales vuelven a su forma original después de doblarse debido a la deformación elástica).
De esta manera, la boca en forma de V R4 troquela (la superficie de contacto entre el punzón superior y la matriz inferior muestra una forma de V y el radio de la boca en forma de V es de 4 mm).
Al mismo tiempo, se eligió el material SKD11 (acero para herramientas de alta calidad, alto contenido de carbono y cromo) para mejorar la abrasividad y la vida útil de la prensa plegadora. Después del procesamiento de prueba, la precisión del tamaño y la calidad de la superficie de la prensa plegadora cumplieron con los requisitos.
Caso 2 Selección de herramientas para procesar placas de aleación de aluminio
La fábrica de equipos automotrices necesita procesar placas de aleación de aluminio 6061-T6 con un ángulo de curvatura de 120° y un espesor de placa de 3 mm. Debido a la suavidad del material de aleación de aluminio, se producirán hendiduras y descascarillados (protuberancias parciales en la superficie del material).
Después de la prueba, se elige la matriz de boca en forma de U R8 (la superficie de contacto entre el punzón superior y la matriz inferior muestra forma de U, el radio de la boca en forma de U es de 8 mm) y la superficie de la matriz se lleva a cabo con un tratamiento de nitruración (un proceso de tratamiento térmico de superficie que puede mejorar la dureza de la superficie de la matriz).
Mientras tanto, la fuerza de flexión se reduce adecuadamente durante el doblado y la superficie de la matriz se pinta con aceite lubricante. La superficie final de la placa de aleación de aluminio es lisa y limpia, sin deflexiones evidentes.
Materiales y calidad de las herramientas
El material de las herramientas es un factor importante para mejorar la calidad de la pieza de trabajo y prolongar la vida útil de las herramientas. El costo del material de las herramientas varía según factores como el material de la pieza de trabajo y la precisión de plegado.
En términos generales, los materiales de herramientas de alta calidad incluyen acero endurecido, acero de alta velocidad (HSS) y carburo de tungsteno. El acero endurecido es duradero, resistente al desgaste y puede soportar grandes pesos.
El acero de alta velocidad es resistente al desgaste, tiene una larga vida útil y un costo más alto que el acero endurecido. Y el carburo de tungsteno es el de mayor calidad y costo.
Mantenimiento y almacenamiento adecuados
Las herramientas de la prensa plegadora necesitan un mantenimiento correcto para prolongar su vida útil y garantizar la calidad del plegado. Es necesario lubricarlas, rectificarlas y controlar su rendimiento de forma regular según las instrucciones de uso.
Almacene las herramientas en áreas especializadas, como armarios de herramientas con cajones o compartimentos. Fije y aísle cada punzón y matriz con espuma o plástico. Además, limpie las herramientas con regularidad, límpielas con un paño suave y use un aerosol antioxidante con regularidad.
Conclusión
Las herramientas de la prensa plegadora influyen en la forma y la calidad de la pieza a doblar. Antes de doblar, es necesario seleccionar las herramientas adecuadas para el material de acuerdo con la chapa metálica.
También es necesario determinar la forma, el ángulo y el tamaño de la abertura de la matriz según la pieza de trabajo que se va a doblar. La selección correcta de las herramientas y el uso de los materiales pueden mejorar la precisión de las piezas de trabajo que se van a doblar.
Afectan el ángulo de plegado, el radio interno, la longitud mínima de la brida y la apariencia de toda la pieza de trabajo. El uso de las herramientas correctas puede mejorar la eficiencia del plegado, reducir los costos, evitar la deformación del perfil y proteger la seguridad de los operadores de la prensa plegadora.
Si todavía tiene dudas sobre la elección de la prensa plegadora y las herramientas de prensa plegadora, le invitamos a ponerse en contacto con mi empresa, Krrass Machine Tool.
Como fabricante de prensas plegadoras con 20 años de experiencia, no solo ofrecemos prensas plegadoras de alta calidad, sino que también nos dedicamos a ofrecer un plan integral de soluciones de procesamiento de plegado.
Lo invito sinceramente a visitar nuestra página de productos y obtener más información sobre nuestra serie de prensas plegadoras y las herramientas correspondientes. Nuestro equipo está listo para brindarle asesoramiento y soporte tecnológico.