Presentamos los resultados de experimentos que exploran la viabilidad de utilizar un Nd acoplado a fibra:Láser YAG para cortar placas gruesas de acero dulce (espesor > 15 mm). Las pruebas se llevaron a cabo con un láser Nd:YAG de onda continua de 2,5 kW, que se aplicó a la pieza de trabajo a través de una fibra óptica con núcleo de sílice de 0,6 mm de diámetro. Las muestras de acero dulce utilizadas en el estudio tenían un espesor de entre 10 y 50 mm. Se investigaron y analizaron los efectos de varios parámetros operativos (incluido el tamaño del punto focal, la posición de la boquilla de corte en relación con la superficie del acero, la presión del gas auxiliar, la potencia del láser y la velocidad de corte) sobre la calidad de las superficies cortadas.
Los resultados preliminares indican que es posible cortar placas de acero dulce de hasta 50 mm de espesor a velocidades de hasta 200 mm/min con tan solo 500 W de potencia de láser Nd:YAG. Las superficies de corte resultantes fueron lisas y sin escoria, lo que sugiere que la tecnología láser Nd:YAG tiene un potencial significativo para cortar placas de acero gruesas.
Introducción
Corte por láser en la industria de procesamiento de materiales
El corte por láser representa aproximadamente una cuarta parte de la industria de procesamiento de materiales por láser [1]. En los últimos 30 años desde que se logró el primer corte por láser asistido por gas [2], el método fundamental de corte por láser ha experimentado pocos cambios. Para cortar aceros dulces, el haz láser se enfoca normalmente en la superficie de la pieza de trabajo o cerca de ella y está rodeado por una corriente coaxial de gas de asistencia de oxígeno. Por lo general, se utilizan potencias láser de hasta 3 kW para cortar aceros dulces con espesores que van desde 12 a 15 mm, mientras que las placas más gruesas generalmente se cortan utilizando sistemas de plasma u oxicombustible. Aunque los láseres de CO2 son capaces de cortar metales de hasta 40 mm de espesor, existe una reducción significativa en la calidad del corte y la reproducibilidad a medida que aumenta el espesor [3].
Desafíos al cortar materiales más gruesos
Un método para cortar placas de acero dulce más gruesas consiste en aumentar la potencia del láser. Si bien este método ofrece varias ventajas, también presenta desafíos importantes. A potencias más altas (3,5 kW y más), la calidad del haz puede volverse inestable, lo que reduce la vida útil de los componentes ópticos, aumenta los costos de equipo y de operación y afecta la precisión del corte. Como se demuestra en [4], aunque el espesor de la ranura permanece aproximadamente constante para una calidad de acabado de superficie dada, la velocidad de corte no disminuye en proporción directa al espesor del material, lo que sugiere una disminución en la eficiencia de corte a medida que aumenta el espesor del material.
Esta reducción en la eficiencia de corte con el aumento del espesor del material se atribuye a la disminución de la capacidad del gas auxiliar para cortar el material fundido. A medida que aumenta el espesor, la presión del gas auxiliar también debe aumentar para eliminar eficazmente el material fundido. Sin embargo, con oxígeno como gas auxiliar, la reacción exotérmica que ocurre en la ranura requiere una reducción en la presión de oxígeno a medida que aumenta el espesor del material para evitar quemaduras excesivas y sobrerreacción. Por lo tanto, controlar la presión de oxígeno se vuelve crucial para evitar quemaduras incontroladas fuera del área calentada. Esto crea una contradicción en los requisitos: si bien aumentar la potencia del láser puede extender el rendimiento de corte, no es suficiente para superar las limitaciones impuestas por la necesidad de controlar la presión del oxígeno. Esto presenta una barrera para lograr mayores espesores de corte, a pesar del potencial de una mayor potencia del láser.
Métodos alternativos para cortar acero grueso
Para superar las limitaciones que supone aumentar la potencia del láser, se han desarrollado numerosas técnicas para mantener o mejorar el rendimiento del corte a medida que aumenta el espesor del acero dulce. Algunos de estos métodos incluyen: corte por llama láser [5], lentes de doble foco [6], corte por haz con óptica adaptativa [7], corte por láser con una boquilla coaxial (anular) [8], corte por láser de CO2 de doble haz [9], rayos láser giratorios [13, 14] y corte con oxígeno asistido por láser (Lasox©) [10 – 12].
Corte por láser Nd:YAG con predominio de oxígeno y oscilación
En trabajos anteriores, informamos sobre el corte de placas de acero dulce más gruesas utilizando un rayo láser Nd:YAG giratorio [14]. En este estudio, investigamos el uso de un láser Nd:YAG suministrado por fibra con un rayo oscilante (una técnica similar a girar el rayo) y el método de corte láser dominado por oxígeno, similar al corte Lasox [10, 11, 12]. Los ensayos de corte láser Nd:YAG dominado por oxígeno se llevaron a cabo primero con bajas presiones de gas de asistencia de oxígeno y luego con altas presiones de oxígeno.
Este nuevo enfoque tiene como objetivo abordar los desafíos de cortar acero dulce grueso mejorando la eficiencia de remoción de material y al mismo tiempo gestionando los problemas relacionados con la presión del gas de asistencia y la estabilidad de la viga.
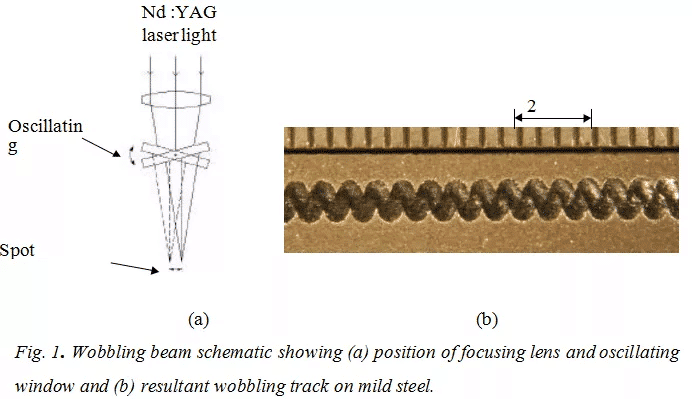
2.2 Corte de aceros mediante un enfoque dominado por oxígeno asistido por láser
El método de corte con oxígeno asistido por láser se implementó en placas de acero dulce AS3678 de espesor de 16 a 50 mm. Las presiones del gas asistido por oxígeno se mantuvieron por debajo de 120 kPa (corte con oxígeno a baja presión, LoPOx) o a presiones altas (corte con oxígeno a alta presión, HiPOx). Los resultados del corte se registraron en función de la calidad del corte (estrías de corte, forma de la ranura, exceso de escoria) y la velocidad de corte.
Resultados
3.1 Oscilación del rayo láser.
Al hacer oscilar el haz sobre la pieza de trabajo, el espesor máximo de corte se incrementó de 12 mm, como se lograba con el corte convencional, a 16 mm. Un gráfico de la velocidad máxima de corte para varios espesores y potencias de láser, que se ve en la Figura 2, indica que, aunque el espesor de corte mejoró con el haz oscilante, la velocidad de corte es similar a la del corte convencional (CW). Esto indica que el proceso de corte que ocurre dentro de la ranura permanece inalterado durante el corte con haz oscilante. También se lograron velocidades de corte similares con el haz giratorio [14].
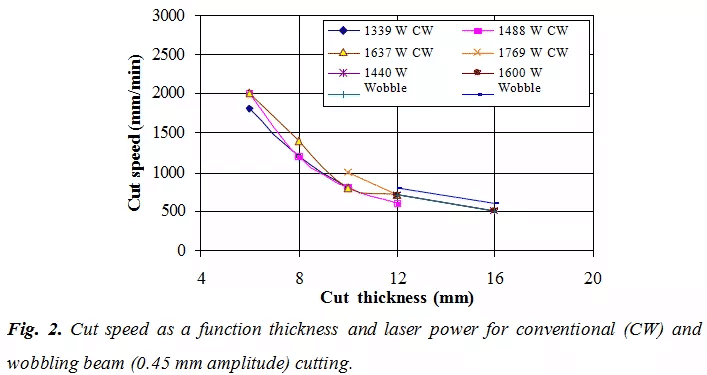
El aumento del espesor de corte se puede atribuir al aumento del ancho de la ranura. Esto se demuestra al variar la amplitud de la oscilación, como se muestra en la Figura 3. Aquí, a medida que la amplitud de la oscilación se reduce secuencialmente desde una amplitud máxima de 0,45 mm a cero, el ancho de la ranura se reduce, lo que corresponde a una reducción en la capacidad de limpiar la masa fundida. Esto demuestra claramente la necesidad de tener un ancho de ranura adecuado para permitir que se limpie la escoria. Esta opinión también la expresan otros [12], donde se sugiere que tanto la dinámica de fluidos como la termodinámica están limitadas por ranuras estrechas.
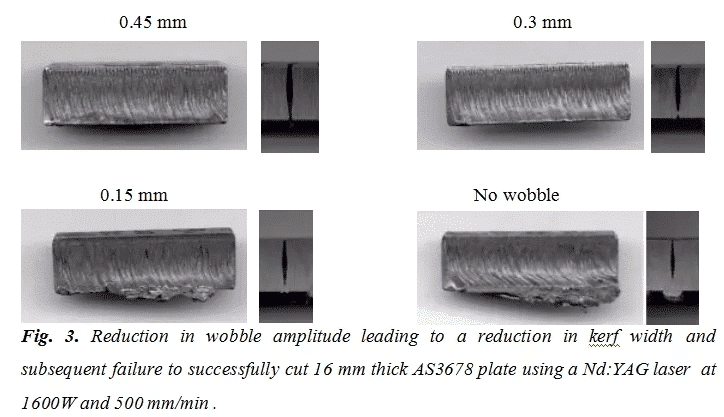
3.2 Corte de aceros mediante un enfoque dominado por oxígeno asistido por láser
3.2.1 Corte dominado por oxígeno a baja presión – LoPOx
El proceso de corte LoPOx utiliza el mismo haz láser de mayor diámetro y el mismo chorro de oxígeno estrecho e imponente en la parte superior de la pieza de trabajo que se observa en el proceso Lasox, pero con presiones de gas de asistencia inferiores a 120 kPa. Las superficies de corte que se muestran en la Figura 4 utilizando el proceso LoPOx demuestran que las bajas potencias del láser incidente no obstaculizan el corte láser siempre que se pueda producir la iniciación primaria y continua del corte. De hecho, a medida que aumenta la velocidad de corte, la potencia del láser incidente puede aportar demasiada energía y, por lo tanto, provocar que se produzca una estría excesiva. Esto se demuestra en la figura al observar la velocidad de corte de 450 mm/min, donde se generó una superficie mejor con una potencia del láser incidente de 533 W que la que se logró a 1420
W. Aquí, la velocidad de la reacción exotérmica está determinada por la velocidad de corte. La potencia del láser incidente solo es necesaria para calentar la superficie superior a más de 1000 °C [11] e iniciar el proceso de fusión reactiva. Una potencia láser incidente excesiva reduce la calidad del corte. Esto demuestra que los problemas de interacción oxígeno-hierro, no la potencia láser incidente, ahora determinan principalmente la calidad del corte. Por lo tanto, este es un proceso de corte láser dominado por el oxígeno.
En la Figura 4, a medida que se reduce la potencia para cada velocidad de corte, los primeros indicios de potencia incidente mínima son el mal comienzo del corte, como se ve en el extremo derecho. Esto demuestra que los requisitos de potencia al inicio del corte son mayores que los del proceso de corte en curso y que la potencia requerida para el establecimiento rápido de un proceso de corte constante y no la potencia para el proceso en curso es el criterio esencial.
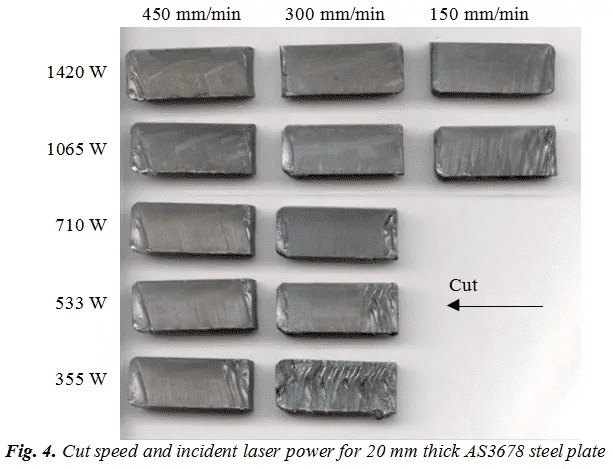
Al realizar un corte LoPOx con un diámetro de boquilla coaxial más pequeño para un material del mismo espesor, se obtienen las mismas velocidades de corte pero con un ancho de corte más estrecho y, en consecuencia, un flujo de oxígeno reducido. Sin embargo, no se pudieron lograr cortes de alta calidad con las potencias láser más bajas y el diámetro de boquilla más grande utilizado en la Figura 4. Esto se produce a pesar de que el punto láser es más intenso como resultado de pasar a través de una boquilla de diámetro más pequeño. Esto demuestra que el requisito de un corte lo suficientemente ancho para permitir que se elimine la escoria se aplica igualmente para el proceso de corte dominado por el oxígeno.
Los lados del corte son más cónicos que los que se encuentran en el corte convencional (dominado por láser). La naturaleza del proceso de corte, dominado por el oxígeno, significa que la ranura está influenciada por la forma del imponente chorro de oxígeno, y la parte superior de la ranura tiene el mismo ancho que la boquilla coaxial utilizada.
La holgura entre la boquilla y la pieza de trabajo se modificó y los resultados típicos de esta variación se muestran en la Figura 5. Para varios diámetros de boquilla, la calidad del corte se redujo significativamente con holguras mayores que 25% del diámetro de la boquilla. Los aumentos en la holgura entre la boquilla y la pieza de trabajo expusieron más flujo de la boquilla a los gases atmosféricos ambientales antes de ingresar a la ranura [8]. El cambio en la holgura se realizó sin cambios correspondientes en el diámetro del punto láser con resultados similares. Esto demuestra además que los cambios en la intensidad de la potencia del láser incidente y no en el gas de asistencia fueron el factor que afectó la calidad del corte láser en el rango probado. La Figura 5 también muestra el efecto de una holgura demasiado pequeña (0,1 mm) donde el haz convergente aún no excede el diámetro del chorro de gas, por lo que no permite que funcione el proceso de corte láser dominado por oxígeno.
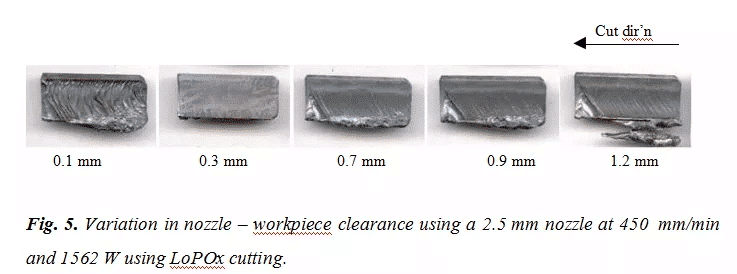
Se logró un espesor de corte máximo de 32 mm utilizando el corte con Nd:YAG LoPOx. El corte por encima de este espesor con los diámetros de boquilla utilizados provocó la formación de escoria excesiva dentro de la ranura y una pérdida de perpendicularidad del corte. Esto demuestra aún más la relación entre el ancho de la ranura y el espesor de corte cuando se utilizan presiones de corte bajas (convencionales).
3.2.2 Corte por láser Nd:YAG dominado por oxígeno a alta presión – HiPOx
Utilizando presiones de suministro mucho más altas y boquillas de diámetro más pequeño, se descubrió que era posible cortar aceros más gruesos que los obtenidos anteriormente mediante el proceso LoPOx. Se demostró que la capacidad de corte estaba entre 32 y 50 mm de espesor utilizando una placa de acero AS 3679. Las velocidades de corte típicas con respecto al espesor del material y la potencia del láser se muestran en la Figura
6. La figura muestra una continuación de los procesos de corte desde la región de baja presión utilizada para materiales más delgados.
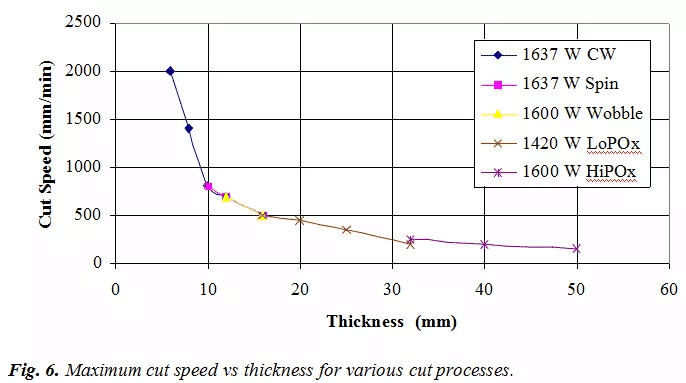
El efecto de utilizar altas presiones de suministro significa que el flujo del gas es complejo y puede dar lugar a características de choque interno. La evidencia de la interacción de las estructuras de choque durante el corte se puede ver como "crestas" o marcas menores en la superficie de corte y vistas como líneas que corren perpendiculares a la estría. Además, el desplazamiento de estas crestas con la holgura entre la boquilla y la pieza de trabajo resulta del refuerzo o la anulación de los choques internos del gas de asistencia y el choque característico que aparece al comienzo de la ranura en forma de "X" [15]. El trabajo [16, 17] también indica una interacción compleja y a veces oscilatoria de los choques con las paredes de la ranura. La evidencia de la naturaleza oscilatoria del corte está en el "zumbido" constante que se puede escuchar en algunas condiciones de corte.
Utilizando una boquilla coaxial de 1,5 mm de diámetro, se demostró que la capacidad de corte era satisfactoria para placas de 32 y 40 mm, y los resultados de corte de placas de 40 mm se muestran en la Figura 7. La distancia entre la boquilla y la pieza de trabajo aumentó significativamente con las altas presiones de gas auxiliar y la forma de la ranura fue mucho menos cónica que la observada en LoPOx como resultado de la corriente de gas de alta velocidad menos divergente. Dichas ranuras se pueden ver en la Figura 8.
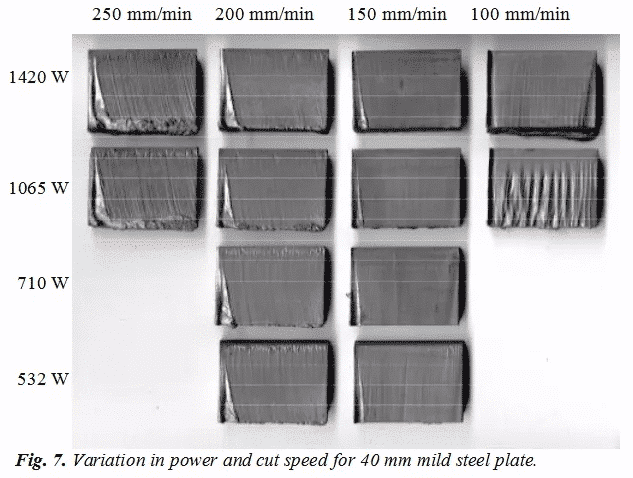
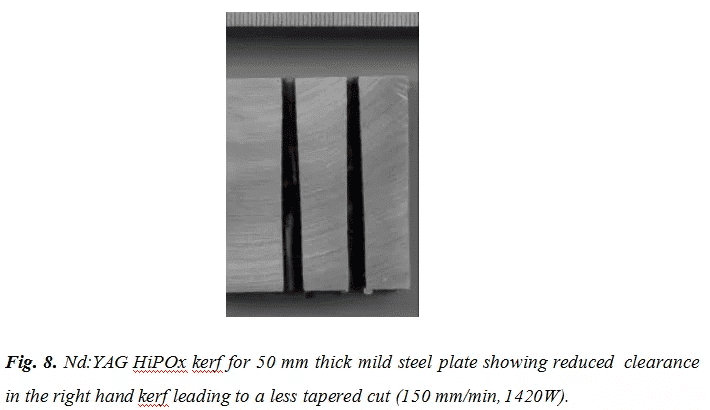
El corte de perfiles mediante la técnica de Nd:YAG LoPOx con aporte de fibra es factible con los ejemplos que se muestran en la Figura 9. En este caso, los aumentos de temperatura en el interior de las esquinas dan como resultado un mayor estrechamiento en estos puntos. Esto se ve en el corte circular de la Figura 9 (a) y el socavado de las esquinas en la Figura 9 (b). El socavado de las esquinas agudas se supera mejor mediante el uso de velocidades de corte reducidas, como se muestra en la figura.
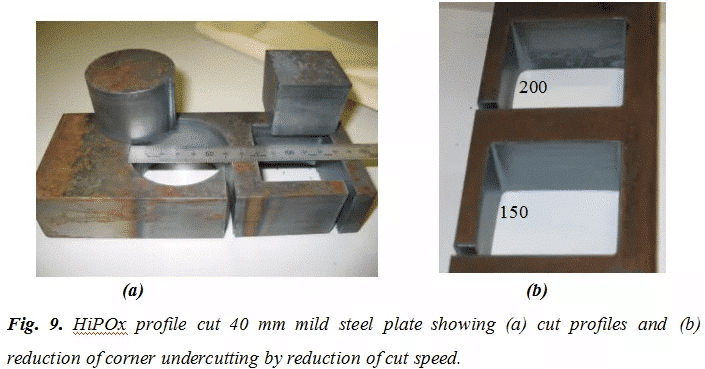
El corte con oxígeno a alta presión con láser Nd:YAG, como el que se utiliza con CO2 [12], también demuestra ser excelente para perforar una placa AS3679 de 32 mm en menos de un segundo. La eliminación de la escoria expulsada hacia arriba sigue siendo un problema, ya que su presencia en la superficie de la placa en la trayectoria de corte es perjudicial para la calidad del corte.
Discusión
Desafíos de cortar placas de acero gruesas
A pesar de los novedosos avances en las técnicas de corte por láser y la capacidad de cortar materiales más gruesos, el proceso de corte fundamental sigue siendo prácticamente inalterado. Esto es evidente por la reducción de la velocidad de corte a medida que aumenta el espesor del material, así como por las velocidades de corte constantes observadas en los métodos convencionales, de haz giratorio y de haz oscilante. En todos los casos, los factores principales que rigen el corte de placas de acero gruesas mediante fusión reactiva (como las pérdidas de calor por conducción y las limitaciones en la eliminación del flujo de fusión debido a la viscosidad y la tensión superficial) siguen planteando desafíos importantes. Estos factores no se superan fácilmente, incluso con el desarrollo de nuevos métodos de corte.
El papel del ancho de corte y el consumo de oxígeno
Los diferentes anchos de corte producidos al hacer oscilar el haz láser, así como los generados en el corte láser dominado por oxígeno con el láser Nd:YAG, resaltan la necesidad de cortes adecuadamente anchos a medida que aumenta el espesor del material. Sin embargo, con espesores de material moderados (~32 mm), aumentar el corte más allá del producido por la boquilla LoPOx más grande se vuelve poco práctico debido al consumo prohibitivo de oxígeno.
En este contexto, el uso de HiPOx (oxígeno a alta presión) ofrece una solución prometedora. La corriente de gas auxiliar de alta presión y alta velocidad ayuda a reducir la mezcla de oxígeno con los gases atmosféricos, lo que hace que haya más oxígeno disponible para el proceso de fusión reactiva. Además, la mayor presión genera fuerzas de corte significativamente mayores en el material fundido, lo que ayuda a retirar la masa fundida de la ranura. Otra ventaja de la técnica HiPOx es la gran distancia entre la boquilla y la pieza de trabajo que permite, lo que garantiza el funcionamiento confiable de las boquillas de alta presión, especialmente al cortar materiales gruesos.
Requisitos de potencia del láser para el corte con predominio de oxígeno
El corte con oxígeno dominante depende principalmente de la potencia del láser incidente para iniciar y mantener el corte. Los resultados de este estudio indican que la potencia del láser necesaria para el corte con oxígeno dominante es sustancialmente menor que la necesaria para el corte láser convencional. Sin embargo, si bien la potencia necesaria para mantener un corte constante es menor, inicialmente se necesitan potencias más altas para establecer el corte. Una vez que se inicia el corte, la potencia del láser se puede reducir a un nivel que sostenga el proceso de corte. Esto sugiere que un aumento de potencia al comienzo del corte podría maximizar la eficiencia general del corte, al utilizar una potencia más alta solo cuando sea necesaria para la iniciación.
Corte de perfiles y socavado de esquinas
Se ha demostrado que el corte de perfiles mediante el proceso láser Nd:YAG dominado por oxígeno es factible. Sin embargo, un problema común es el socavado en las esquinas internas del perfil cortado. Este problema se puede solucionar programando cuidadosamente la velocidad de corte en estas posiciones específicas para evitar la eliminación excesiva de material y garantizar cortes limpios.
Manejo de perforaciones y escorias
También es posible perforar placas de acero gruesas con un láser Nd:YAG, pero surgen problemas debido a la expulsión hacia arriba de escoria fundida durante el proceso de perforación. Esta escoria puede interferir con el suministro de gas auxiliar durante el corte posterior, lo que genera una mala calidad de corte. Una solución a este problema podría ser la introducción de un chorro de aire anular orientado hacia afuera que rodee la boquilla, lo que ayudaría a alejar la escoria de la ranura. Alternativamente, el problema podría solucionarse programando un Comando de espera CNC Una vez finalizadas todas las operaciones de perforación, se debe dejar tiempo para retirar la escoria expulsada antes de continuar con el corte. Esto ayudará a mantener un flujo constante de gas auxiliar y mejorará el rendimiento general del corte.
Conclusión
El corte por láser dominado por oxígeno, junto con anchos de corte más amplios, demuestra ser un método viable para utilizar un láser Nd:YAG de potencia moderada con suministro de fibra para cortar placas de acero dulce gruesas. Esta técnica es eficaz para cortar acero dulce de hasta 32 mm de espesor con suministro de gas a baja presión. Para espesores mayores, el suministro de gas a alta presión permite cortar acero de hasta 50 mm de espesor, al mismo tiempo que permite una perforación rápida del material. Sin embargo, persisten los desafíos para lograr una calidad de corte constante, especialmente en términos de artefactos de impacto y socavados en las esquinas, que se pueden abordar mediante un corte preciso. Control numérico programación. Además, para perforar con éxito placas más gruesas es necesario gestionar la eliminación de la escoria expulsada para garantizar que el flujo de gas auxiliar no se obstruya, manteniendo así una alta calidad de corte durante el resto del proceso de corte.