La importancia de las posiciones focales en corte por láser No se puede exagerar la importancia de las operaciones de corte, ya que afectan directamente la calidad, la eficiencia y la precisión del proceso de corte. La posición focal se refiere al punto exacto en el que el haz láser converge a su diámetro más pequeño, conocido como punto focal. Este punto es donde el haz láser proporciona la máxima densidad de energía, lo que permite un rendimiento de corte óptimo. A continuación, se presentan varias razones clave que destacan la importancia de las posiciones focales en las operaciones de corte por láser:
Enfoque del corte por láser
Enfoque de rayos láser
Cada fabricante puede tener su opinión sobre cuál es el elemento más importante en corte por láser¿Cree que se trata de mantener el tamaño de punto más pequeño y una orientación de lente perpendicular al eje del haz láser? Si respondió que sí, tiene razón en parte, pero se deben considerar muchos otros factores con respecto a las propiedades del haz láser y las aplicaciones de corte. Mantener las posiciones de enfoque dentro del material es crucial para la repetibilidad de los parámetros de corte láser y para producir una calidad de borde consistente.
Por ejemplo, cuando se trabaja con materiales gruesos, en realidad es necesario crear un patrón de quemado más grande para crear un canal más ancho, que es necesario para soportar un mayor volumen de material fundido que debe ser expulsado durante el proceso de corte. Para crear este patrón de quemado más grande, se enfoca el haz por encima o por debajo de la superficie del material, según el gas auxiliar. En consecuencia, enfocar un punto pequeño en la superficie suele ser un enfoque menos exitoso para materiales más gruesos.
Sin embargo, para materiales más delgados, un punto pequeño enfocado en la superficie del material es mucho más efectivo que uno más grande porque hay menos material involucrado y, en consecuencia, no se requiere un canal más amplio.
Un factor muy importante a tener en cuenta en el corte por láser es el uso de un gas auxiliar, como oxígeno, nitrógeno o aire comprimido. Cada gas tiene propiedades específicas relacionadas con la aceleración del proceso de combustión, la evacuación del material fundido o ambas cosas.
En el corte por láser, los gases auxiliares favorecen dos reacciones específicas: exotérmica o endotérmica. Las reglas de enfoque varían según el tipo de reacción y el gas utilizado.

Enfoque para reacciones exotérmicas
Las reacciones exotérmicas se crean utilizando un gas que ofrece propiedades acelerantes, como el oxígeno. Durante este tipo de reacción, la intensa energía del rayo láser vaporiza (o literalmente hierve) el material cortado a medida que el oxígeno reacciona vigorosamente con el material fundido en su estado líquido. Durante el corte a alta presión asistido por oxígeno, el material base se lleva a una temperatura tan intensamente alta que la conversión del material en vapor térmico es casi completa.
Las reglas de enfoque para apoyar reacciones exotérmicas requieren que las posiciones de enfoque estén por encima de la superficie para materiales gruesos o justo en la superficie superior para materiales más delgados.
Cuando el foco está sobre el material, normalmente se utiliza una presión baja y un volumen bajo para ayudar a licuar y luego expulsar el material fundido (aproximadamente de 6 a 8 libras por pulgada cuadrada a 40 pies cúbicos por hora). En realidad, se vaporiza muy poco del material porque el pequeño volumen de oxígeno no puede soportar la vaporización completa. Cuando el foco está ubicado justo en la superficie del material, normalmente se utiliza una presión alta y un volumen alto (aproximadamente 60 PSI a 80 CFH). Esto es suficiente para soportar una vaporización vigorosa del material.
Por eso, cuando se inspeccionan la mayoría de las mesas de corte en las que se cortan predominantemente materiales más finos, se ve muy poco material acumulado en los soportes de la mesa. Por el contrario, las mesas de corte que se utilizan para procesar materiales más gruesos tendrán un volumen mucho mayor de material acumulado en sus soportes.
Enfoque en reacciones endotérmicas
Las reacciones endotérmicas, por otro lado, se crean cuando se utiliza un gas que tiene propiedades inertes o no reactivas. El nitrógeno y el argón entran en esta categoría.
Durante este tipo de reacción, el gas solo contribuye a la evacuación del material fundido a través del canal de corte. El proceso endotérmico depende en gran medida de la energía bruta del haz láser enfocado para llevar el metal base rápidamente a un estado fundido y crear el canal de corte adecuado. Esto permite que el gas inerte expulse el material licuado a través del canal de corte, dejando una superficie cortada limpiamente sin adherencia de escoria.
Las reglas de enfoque para favorecer las reacciones endotérmicas requieren que las posiciones de enfoque estén en la parte inferior del material o justo debajo de ella. Mantener el enfoque debajo del material crea una ligera forma de V dentro del canal de corte, lo que permite que el gas a alta presión comprima el material fundido a través del canal de corte a alta velocidad y lo expulse por la base del canal.
Las reacciones endotérmicas requieren un gran volumen y una alta presión para permitir la evacuación rápida del material fundido. Los volúmenes típicos pueden comenzar en 350 CFH para materiales delgados y alcanzar más de 3000 CFH para materiales más espesos. Las presiones pueden comenzar en 140 PSI para materiales delgados y aumentar a más de 300 PSI para materiales más espesos.
El uso de aire comprimido como gas auxiliar produce reacciones endotérmicas y exotérmicas al mismo tiempo. Sin embargo, como el volumen de aire está compuesto principalmente de nitrógeno (aproximadamente el 78 por ciento), se trata principalmente de una reacción endotérmica, mientras que el pequeño volumen de oxígeno (aproximadamente el 20 por ciento) crea una reacción exotérmica simultánea pero más pequeña. Esto da como resultado una fusión más rápida del material base debido a las propiedades reactivas del oxígeno. El resto del aire es principalmente inerte en su composición y solo contribuye a la reacción endotérmica producida por el nitrógeno.
El corte con aire comprimido tiene mejores resultados cuando la posición de enfoque se mantiene en el centro del espesor del material.
Efectos de rayos sin procesar
Así como la intensidad del sol afecta la capacidad de la lupa para enfocar y crear un tamaño de punto efectivo, el rayo láser en bruto influye en la capacidad para enfocar su energía y el tamaño del punto de enfoque resultante. Esta es la regla general: cuanto mayor sea el diámetro del rayo en bruto, mayor será el diámetro de cintura focal resultante y más lejos se proyectará el punto focal de la lente.
Otra forma de cambiar el tamaño del punto de manera efectiva es usar una lente con una distancia focal efectiva (EFL) diferente. Esto crea no solo un tamaño de punto diferente, sino también una profundidad de foco (DOF) diferente, como se ilustra en la Figura 3. Tenga en cuenta que la DOF no solo se refiere al punto donde el haz es más pequeño (cintura focal), sino que también incluye un rango justo antes y después del tamaño de punto más pequeño.
Como ejemplo de cambio del tamaño del punto y la profundidad de campo, considere un haz láser de CO2 con una longitud de onda de 10.600 nm, un diámetro de haz bruto de 20 mm y un M2 de 2. Si pasamos este haz a través de una lente de 3,75 pulgadas (95,25 mm), el diámetro en la cintura focal sería de aproximadamente 128 micrones (0,128 mm). Ahora, si sustituimos una lente de 5 pulgadas (127 mm), utilizando el mismo haz bruto de 20 mm, el diámetro en la cintura focal sería de 170 micrones (0,170 mm). Al mismo tiempo, se produciría un cambio en la profundidad de foco entre las dos lentes. La lente de 3,75 pulgadas tendría una profundidad de campo de aproximadamente 1,2 mm, en comparación con una profundidad de campo de 2,16 mm para la lente de 5 pulgadas.
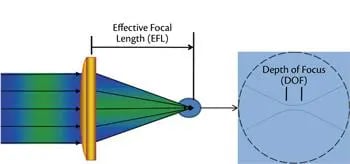
Otra consideración que puede alterar la proyección del punto focal del haz es un cambio en el frente de onda del haz antes de que llegue a la lente. El frente de onda del haz en bruto se puede describir como convergente, paralelo o divergente. En el caso de un frente de onda convergente, el haz se hace esencialmente más pequeño a medida que viaja. A medida que este frente de onda convergente llega a la lente, la proyección de enfoque resultante es más corta que la de un frente de onda paralelo debido a la proyección de diámetro de haz más pequeño en la parte superior de la lente. Por el contrario, enfocar un frente de onda divergente da como resultado una proyección de punto focal más larga que la de un frente de onda paralelo debido al diámetro de haz más grande proyectado en la superficie superior de la lente.
Aplicaciones en el mundo real
Es importante controlar todos los aspectos relacionados con el mantenimiento de las proyecciones de puntos de enfoque adecuadas. Debe asegurarse de que el haz sin procesar en el resonador óptico esté en buenas condiciones y de que el haz se entregue correctamente a la lente. El uso de la lente de distancia focal adecuada puede cambiar la velocidad a la que se funde el material y el espesor que se puede procesar. Una lente de distancia focal corta, como una EFL de 3,75 pulgadas, es más efectiva hasta un espesor máximo de calibre 12 o 0,104 pulgadas. Una lente de 5 pulgadas es más efectiva hasta un espesor máximo de 0,250 pulgadas. Para materiales más gruesos, use una lente de 7,5 pulgadas hasta un máximo de 1,25 pulgadas y una lente de 10 pulgadas hasta un máximo de 1,312 pulgadas para lograr el corte más efectivo.
Una práctica que realmente ahorra tiempo es utilizar un EFL que le permita cubrir la mayor parte de su producción diaria sin tener que cambiar de lente. El uso de una lente de 7,5 pulgadas le permitirá, en la mayoría de los casos, lograr todos los objetivos relacionados con el mantenimiento del enfoque adecuado, desde un calibre 16 hasta un grosor de 1 pulgada, durante el transcurso de la producción de un día.
Como se mencionó anteriormente, la elección del gas auxiliar tiene mucho que ver con la forma en que se determinará la posición focal dentro del material. El corte láser asistido por oxígeno (exotérmico) requerirá que las posiciones de enfoque estén justo en la superficie o por encima de la superficie del material. Se requieren muy pocos cambios focales a menos que esté cambiando de corte de alta presión a corte de baja presión porque el enfoque siempre está en o cerca de la superficie del material y, en consecuencia, no se ve afectado por los cambios en el espesor del material. Por otro lado, el corte láser asistido por nitrógeno (endotérmico) depende mucho del enfoque en función del espesor del material que se va a procesar porque el enfoque está en o cerca de la parte inferior del material.
En cualquier caso, todos los puntos focales básicos pueden satisfacerse utilizando un dispositivo de enfoque automático CNC, como un espejo adaptativo.
Un espejo adaptable funciona modificando la forma de su superficie mediante la aplicación de presión en su parte posterior. En su estado normal, sin presión aplicada, la superficie del espejo adaptable es cóncava. A medida que se aplica presión al espejo, la superficie cambia de cóncava a plana y luego a convexa. Al modificar la forma del espejo, se modifica el frente de onda del haz y, en consecuencia, se altera el tamaño del haz en la lente y la posición focal proyectada dentro del material.
Otro beneficio importante del enfoque automático es la capacidad de cambiar la posición focal dinámicamente durante el proceso de perforación, lo que permite una entrada máxima de energía dentro del espesor del material y reduce los tiempos generales de perforación.
Los avances en las tecnologías de corte por láser que sirven para mejorar el rendimiento y la productividad continúan hasta el día de hoy. Sin embargo, lo que sigue siendo muy importante es la entrega del haz sin procesar a la lente y el mantenimiento de las posiciones focales adecuadas, según la aplicación.
Si se mantienen la posición focal y las formas de proyección adecuadas dentro del material que se va a procesar, se minimizan los demás requisitos necesarios para producir un corte uniforme y de alta calidad. Esto ahorra tiempo de configuración y, al mismo tiempo, mantiene una productividad y un rendimiento constantes.