Controles de prensa plegadora Son esenciales en la fabricación de metales, ya que facilitan operaciones de plegado precisas, eficientes y seguras, lo que garantiza resultados de alta calidad y una producción rentable. Su impacto en la industria metalúrgica moderna es profundo, lo que los convierte en un componente invaluable del proceso.
Esta guía está diseñada para ser un recurso útil para cualquier persona en el campo de la fabricación de metales, ya sea un recién llegado que busca comprender los fundamentos o un profesional experimentado que busca mantenerse informado sobre los últimos desarrollos en tecnología de controladores de prensa plegadora.
¿Qué son los controles de prensa plegadora?
Un controlador de prensa plegadora es un dispositivo especializado que gestiona el funcionamiento de una máquina plegadora. La prensa plegadora, una máquina robusta, está diseñada para doblar y dar forma a chapas, placas y otros materiales metálicos. Al actuar como sistema de control central de la máquina, el controlador de prensa plegadora permite a los operadores dar forma al metal con una precisión y una consistencia excepcionales, lo que garantiza altos niveles de precisión en cada operación.
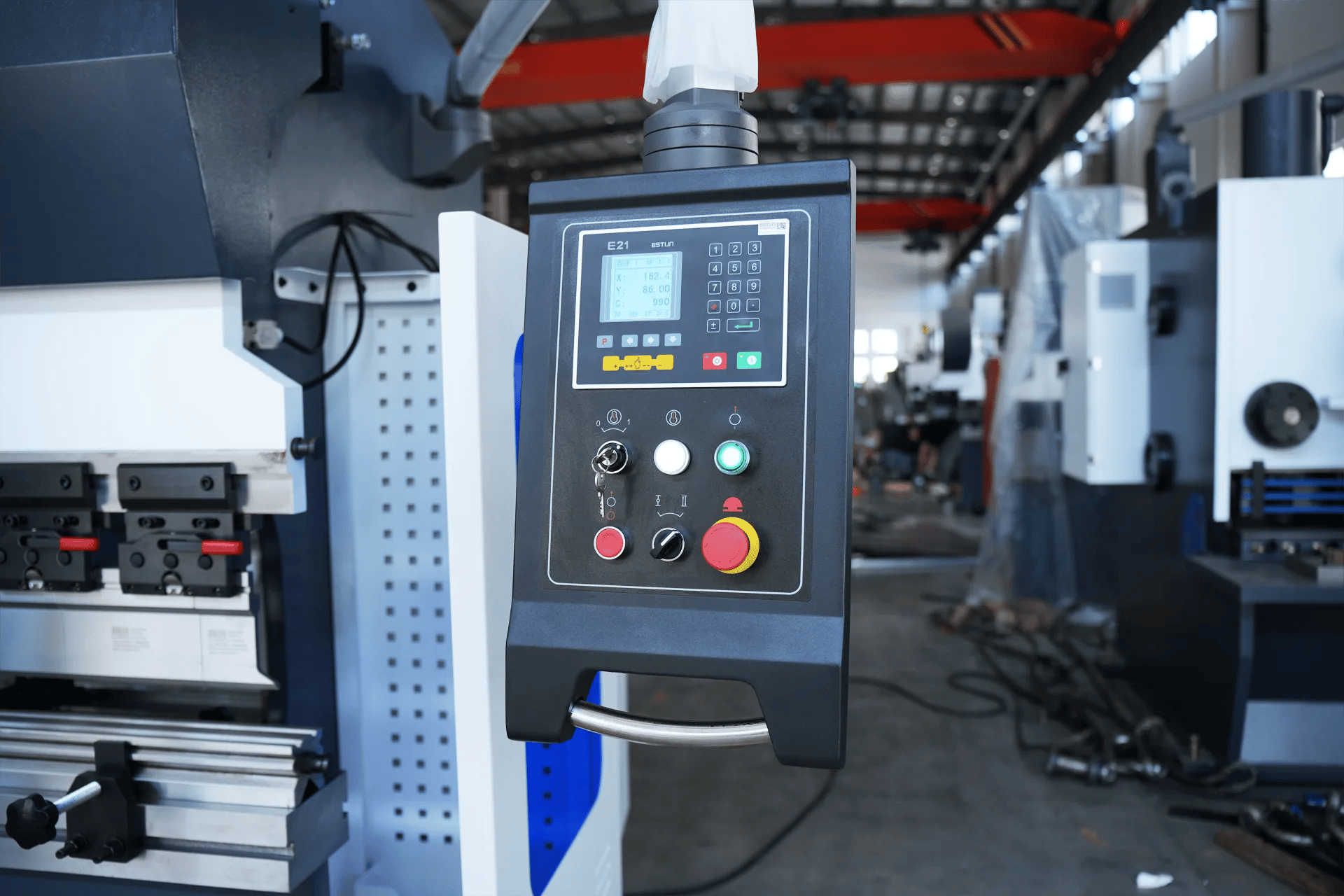
Función de los controles de la prensa plegadora
Interfaz de control:
La interfaz de control de un controlador de prensa plegadora es donde el operador interactúa con la máquina. Generalmente incluye una pantalla táctil o un panel fácil de usar con botones y una pantalla digital. A través de esta interfaz, los operadores pueden ingresar parámetros de plegado, como el ángulo de plegado deseado, la longitud de plegado y la información de las herramientas.
Capacidades de programación:
Los controladores de las prensas plegadoras están equipados con funciones de programación que permiten a los operadores crear y almacenar programas de plegado. Estos programas definen las instrucciones específicas para la operación de plegado, incluida la secuencia de plegados, los ángulos y las posiciones. Los controladores avanzados pueden ofrecer interfaces de programación gráfica, lo que facilita la visualización de la secuencia de plegado.
Mecanismos de seguridad:
La seguridad es de suma importancia en cualquier operación de fabricación de metales. Los controladores de las prensas plegadoras están equipados con funciones de seguridad para proteger tanto al operador como a la máquina. Estos mecanismos de seguridad incluyen:
Cortinas de luz:
Éstos emiten un haz de luz invisible que al interrumpirse detiene inmediatamente el funcionamiento de la máquina para evitar accidentes.
Botón de parada de emergencia:
Un botón grande y de fácil acceso que, al presionarlo, detiene todos los movimientos de la máquina en caso de emergencia.
Enclavamientos:
Estos garantizan que todas las puertas y portones de seguridad estén bien cerrados antes de que la máquina pueda funcionar, lo que reduce el riesgo de accidentes.
Monitoreo en tiempo real:
Muchos controladores de prensas plegadoras modernas brindan monitoreo y retroalimentación en tiempo real. Los operadores pueden observar el proceso de plegado, monitorear el desgaste de las herramientas y realizar ajustes según sea necesario para mantener la precisión y la calidad.
Precisión y repetibilidad:
La función principal de un controlador de prensa plegadora es ejecutar operaciones de plegado con un alto grado de precisión y repetibilidad. Esto es crucial para cumplir con tolerancias estrictas y producir componentes que cumplan con los estándares de calidad.
Los controladores de prensa plegadora son el sistema nervioso central de las máquinas de plegado en la fabricación de metales. Proporcionan a los operadores las herramientas para programar, monitorear y controlar el proceso de plegado con precisión, eficiencia y seguridad. Su capacidad para producir pliegues precisos de manera constante es un testimonio de su importancia en la industria metalúrgica. A medida que la tecnología continúa avanzando, los controladores de prensa plegadora evolucionan para satisfacer las demandas de una industria que cambia rápidamente, mejorando aún más su papel en la conformación del mundo moderno de la fabricación de metales.
Tipos de controles de prensa plegadora
Los controladores de prensa plegadora se presentan en varios tipos, cada uno con características y capacidades específicas para satisfacer las diversas necesidades de fabricación de metales. Comprender estos tipos es fundamental para seleccionar el controlador adecuado para una aplicación en particular. Aquí, exploraremos dos de los tipos comunes de controladores de prensa plegadora:
Controladores manuales:
Los controladores manuales son la forma más sencilla de controlar una prensa plegadora. Proporcionan un control básico sobre la operación de plegado y suelen utilizarse en máquinas plegadoras más antiguas o más pequeñas. En los controladores manuales, el operador ajusta directamente parámetros como el ángulo de plegado, la posición del tope trasero y la velocidad del cabezal mediante controles físicos. Si bien los controladores manuales están menos automatizados que sus contrapartes digitales, son rentables y pueden ser una buena opción para tareas de plegado menos complejas.
Controladores CNC:
Los controladores de control numérico por computadora (CNC) son el estándar moderno en la tecnología de las prensas plegadoras. Estos controladores ofrecen un alto nivel de automatización y precisión. Los controladores de prensa plegadora CNC están equipados con una interfaz de computadora que permite al operador programar secuencias de plegado complejas. Ofrecen funciones como el almacenamiento de múltiples programas de plegado, la gestión de herramientas y el monitoreo en tiempo real del proceso de plegado. Los controladores CNC permiten realizar plegados precisos y repetibles y son ideales para la producción de gran volumen y aplicaciones con estrictos requisitos de calidad.
Cómo elegir los controles adecuados para la prensa plegadora
Los controladores de prensa plegadora son el corazón y el cerebro de la fabricación de metales, responsables de garantizar operaciones de plegado precisas y eficientes. Elegir el controlador de prensa plegadora adecuado es una decisión crucial que puede afectar significativamente la calidad, la productividad y la versatilidad de sus procesos de trabajo de metales. En este artículo, lo guiaremos a través de las consideraciones clave al seleccionar el controlador ideal. prensa plegadora Controlador para sus necesidades específicas.
Determine los requisitos de su aplicación
El primer paso para elegir el controlador de prensa plegadora adecuado es definir claramente los requisitos de su aplicación. Tenga en cuenta los siguientes factores:
Tipo de material: Diferentes materiales (por ejemplo, acero, aluminio o acero inoxidable) pueden requerir características o capacidades de controlador específicas.
Grosor del material: Los materiales más gruesos pueden requerir controladores más potentes.
Complejidad de la pieza: Las piezas complejas con múltiples curvas y tolerancias estrictas pueden requerir capacidades de programación avanzadas.
Volumen de producción: La producción de gran volumen puede beneficiarse de funciones automatizadas y una gestión eficiente de herramientas.
Controladores manuales y CNC
Decide si necesitas un controlador de prensa plegadora manual o CNC:
Controladores manuales: adecuados para tareas de doblado simples y soluciones rentables.
Controladores CNC: ideales para operaciones de plegado complejas, alta precisión y automatización.
Programación e interfaz
Evalúe la facilidad de programación y la interfaz de usuario del controlador. Busque las siguientes características:
Interfaz fácil de usar: Una pantalla táctil o panel intuitivo para una fácil navegación e ingreso de datos.
Programación Gráfica: Ayudas visuales para crear programas de plegado, especialmente útiles para piezas complejas.
Programación fuera de línea: la capacidad de programar secuencias de flexión fuera de línea y transferirlas al controlador.
Compatibilidad de herramientas
Asegúrese de que el controlador de la prensa plegadora sea compatible con las herramientas que planea utilizar. Busque funciones como bibliotecas de herramientas y la capacidad de administrar y optimizar las configuraciones de herramientas.
Características de seguridad
La seguridad es primordial en la fabricación de metales. Tenga en cuenta las siguientes características de seguridad:
Cortinas de luz: Barreras de seguridad infrarrojas que detienen la máquina si un objeto u operador ingresa a la zona de peligro.
Botón de parada de emergencia: un botón grande y de fácil acceso para detener todos los movimientos de la máquina en caso de emergencia.
Enclavamientos: Medidas de seguridad que garantizan que todas las puertas y compuertas de seguridad estén cerradas antes de la operación.
Marcas y modelos
Investigue marcas y modelos de controladores de prensas plegadoras de confianza. Marcas populares como Delem, ESA y otras ofrecen una amplia gama de opciones con diversas características y capacidades. Lea reseñas y busque recomendaciones de colegas de la industria.
Consideraciones presupuestarias
Determine su presupuesto para el controlador de la prensa plegadora. Si bien los controladores avanzados ofrecen numerosas funciones, es esencial lograr un equilibrio entre el costo y la funcionalidad que se ajuste a sus necesidades específicas.
Nivel de habilidad del operador
Tenga en cuenta el nivel de habilidad de sus operadores. Los controladores fáciles de usar con interfaces claras son beneficiosos, especialmente si tiene operadores con distintos niveles de experiencia.
A prueba de futuro
Piense en el largo plazo. Seleccione un controlador de prensa plegadora que pueda adaptarse a sus necesidades cambiantes y a la tecnología cambiante. Los controladores con actualizaciones de software y funciones ampliables pueden ser una inversión inteligente.
Marcas comunes de controles de prensa plegadora
Si bien muchos fabricantes producen estos controladores, ciertas marcas se han ganado el reconocimiento por su innovación, confiabilidad y rendimiento. En esta introducción, analizaremos en detalle varias marcas destacadas de controladores de prensas plegadoras.
Eliminar:
Delem es una marca consolidada y respetada en el mundo de los controladores de prensas plegadoras. Conocida por sus controladores CNC avanzados, Delem ofrece una gama de funciones que satisfacen las necesidades de la industria metalúrgica. Sus controladores son reconocidos por su precisión y confiabilidad, lo que los convierte en la opción preferida de muchos profesionales de la fabricación de metales. Los controladores Delem suelen presentar interfaces fáciles de usar y compatibilidad con varios modelos de prensas plegadoras, lo que permite una integración perfecta en los flujos de trabajo existentes.
miSA:
ESA, o European Systems Automation, es otra marca de prestigio que fabrica controladores de alta calidad para prensas plegadoras. Los controladores ESA son conocidos por su innovación y flexibilidad. Ofrecen una amplia gama de funciones avanzadas, que incluyen corrección de ángulos, prevención de colisiones y conectividad en red. Estos controladores suelen ser elegidos por fabricantes que requieren capacidades sofisticadas y procesos de producción eficientes.
Cibelec:
Cybelec es una marca suiza con una fuerte presencia en el mercado de controladores de prensas plegadoras. Sus controladores son ampliamente reconocidos por su precisión y adaptabilidad. Cybelec ofrece soluciones tanto para aplicaciones de plegado estándar como complejas. Sus controladores suelen contar con interfaces fáciles de usar y potentes capacidades de programación, lo que los convierte en una excelente opción para una variedad de necesidades de trabajo con metales.
Amada:
Amada, una marca reconocida en la industria manufacturera, también produce controladores para prensas plegadoras. Sus controladores son conocidos por su compatibilidad con las máquinas plegadoras Amada, lo que garantiza una integración perfecta y un rendimiento optimizado. Los controladores Amada están diseñados para proporcionar operaciones de plegado precisas y eficientes, lo que refleja el compromiso de la marca con la calidad y la innovación.
DVL:
LVD es un fabricante global de controladores para prensas plegadoras, entre otros equipos para trabajar metales. Los controladores LVD están diseñados para mejorar la precisión y la productividad de las máquinas plegadoras. Suelen venir equipados con funciones avanzadas de programación, supervisión y seguridad. Los controladores LVD gozan de gran reconocimiento por su contribución a la eficiencia de los procesos de fabricación de metales.
Soluciones personalizadas:
Además de estas marcas establecidas, algunas operaciones de fabricación de metales pueden requerir controladores de prensa plegadora especializados o personalizados. Estas soluciones se adaptan a las necesidades únicas de la aplicación y pueden implicar la colaboración con proveedores de sistemas de control o fabricantes de máquinas para desarrollar soluciones a medida.
Conclusión
Estas son solo algunas de las marcas más destacadas en el mercado de controladores de prensas plegadoras. Cada una de estas marcas ofrece un conjunto distinto de características, capacidades e innovaciones para satisfacer los diversos requisitos de la industria de fabricación de metales. La elección de la marca de controlador de prensa plegadora adecuada depende de factores como las necesidades específicas de su aplicación, la compatibilidad con su máquina plegadora y el nivel de precisión y automatización que busca. Ya sea que opte por una marca reconocida como Delem, ESA o Cybelec, o explore soluciones personalizadas, el objetivo final es mejorar la precisión, la eficiencia y la productividad de sus procesos de trabajo de metales.
Comparación entre sistemas de control NC y CNC
En el mundo de la fabricación de metales, la elección de los controles adecuados para la prensa plegadora es fundamental para lograr precisión y eficiencia. El sistema de control numérico de la prensa plegadora es un sistema que controla los procedimientos de la máquina a través de una serie de programas.
El sistema de control de la prensa plegadora se divide en controladores NC y CNC. Tanto el controlador CNC como el NC se utilizan para garantizar la precisión de posicionamiento de las herramientas de la prensa plegadora y el tope trasero. Su principal diferencia radica en si el programa permite modificaciones.
El sistema de control numérico no puede modificar el programa, mientras que el sistema CNC puede modificarlo o editarlo. El sistema CNC es una versión avanzada del sistema NC que mejora enormemente la precisión y la eficiencia de la operación de plegado.
Característica | Control numérico (NC) | CNC (Control numérico por computadora) |
Forma completa | Control numérico | Control numérico por computadora |
Método de entrada | Cintas perforadas y tarjetas perforadas | Teclados y entrada digital |
Modificación del programa | Difícil, requiere volver a perforar las tarjetas. | Fácil, se puede modificar directamente en la computadora. |
Almacenamiento de memoria | No hay almacenamiento de memoria para programas | Memoria disponible para almacenar y reutilizar programas |
Costo | Menos costoso | Más caro |
Costo de mantenimiento | Más bajo | Más alto |
Requisito de habilidad del operador | Requiere operadores altamente calificados | Requiere operadores menos calificados |
Flexibilidad | Menos flexible | Más flexible |
Exactitud | Menor precisión | Mayor precisión |
Tiempo de ejecución | Más lento | Menos consumo de tiempo |
Operación continua | No se puede ejecutar de forma continua | Puede funcionar de forma continua durante 24 horas. |
Nivel de automatización | Automatización inferior | Mayor automatización |
Escenarios aplicables | Operaciones sencillas como taladrado, perforado y fresado. | Operaciones complejas como fresado, torneado, rectificado y taladrado. |
Capacidad computacional | Limitado | Avanzado, con sistemas de retroalimentación para una mayor precisión. |
Eficiencia de producción | Más bajo | Superior, adecuado para producción en masa. |
Intervención humana | Requiere más intervención manual | Se necesita una mínima intervención manual |
Almacenamiento de programas | Los programas no se pueden almacenar | Los programas se pueden almacenar y reutilizar |
Retroalimentación operativa | Sistema de circuito abierto, sin retroalimentación | Sistema de circuito cerrado, proporciona retroalimentación para la precisión. |
El sistema CNC también es fácil de usar y puede mejorar la eficiencia del trabajo. Contiene varias funciones de programación que pueden almacenar una gran cantidad de pasos de plegado complejos, lo que permite producir grandes cantidades de piezas complejas con mayor rapidez. Un buen sistema de control puede optimizar los procedimientos y mejorar la eficiencia de la producción.
Sin embargo, ¿sabes qué controlador de prensa plegadora es la mejor opción? Este artículo te mostrará cómo seleccionar el controlador de prensa plegadora adecuado. Antes de comenzar, veamos primero el video.
Marcas de sistemas de control CNC: Comparación
1. Sistemas de control CNC Delem
Delem, fundada en los Países Bajos en 1978, es una empresa líder centrada en el campo del control CNC para la fabricación de plegado de chapa metálica. Los sistemas de control de prensas plegadoras de Delem incluyen soluciones DA-Retrofit, series DA-40, DA-50 y DA-60.
Los sistemas de control CNC DA-66T, 69T, 53T, 58T, 41T y 42T de Delem son versiones con pantalla táctil, mientras que los sistemas de control CNC DA-66W y 65R son versiones con botones.
(1) Versión de pantalla táctil
Delem tiene una variedad de versiones de pantalla táctil del controlador CNC.
Serie DA-40
El controlador de esta serie se utiliza especialmente para las prensas plegadoras tradicionales con eje de torsión. El sistema puede controlar el tope trasero (X&R) y la viga (Y).
La pantalla LCD brillante se puede utilizar para programar parámetros como el ángulo, la herramienta y el material. El DA-42 también tiene las funciones de control de bombeo y control de presión.
Serie DA-50
La A-58T es adecuada para la prensa plegadora síncrona electrohidráulica. La DA-58T proporciona programación gráfica táctil 2D para calcular automáticamente el proceso de plegado y la detección de colisiones. Las posiciones de todos los ejes se calculan automáticamente.
El proceso de plegado se simula con la máquina y las herramientas a escala real. El DA-58T también se puede utilizar para operaciones en tándem. El DA-53T puede controlar los ejes Y1, Y2 y dos ejes auxiliares.
Serie DA-60
La serie DA-60 ofrece programación gráfica en pantalla táctil 2D y 3D. Los modelos DA-69T y DA-66T son adecuados para procedimientos de plegado que requieren una gran precisión. El modelo DA-66T ofrece programación 2D que incluye cálculo automático de la secuencia de plegado y detección de colisiones. El sistema es modular, el programa es expandible y la operación es más flexible.
(2) Versión de botón
Los dos controladores de versión de botón más comunes de Delem son el DA-66W y el DA-65R. Estos dos sistemas proporcionan funciones de programación gráfica 2D y visualización gráfica 3D. También ofrecen una función de enlace entre varias máquinas y la pantalla táctil es una configuración opcional.
2. Sistema de control CNC de la ESA
Fundada en Italia en 1962, Automation es una empresa líder a nivel mundial en el campo de los sistemas CNC integrados. En 2022, los productos de ESA incluirán principalmente las series 600 y 800. Los modelos más utilizados son los S660, S640, S630, S830, S840, S850, etc.
(1) Serie S600
La serie S600 son todas pantallas táctiles. Pueden controlar un mínimo de 3 ejes y un máximo de 128 ejes. El PLC y la HMI se pueden reprogramar para cumplir con los requisitos personalizados. Se pueden adaptar a una variedad de máquinas de plegado, incluidas las prensas plegadoras hidráulicas, las prensas plegadoras hidráulicas sincrónicas, las prensas plegadoras eléctricas y las prensas plegadoras tándem, etc.
(2) Serie S800
La serie S800 es una nueva línea de productos lanzada por la empresa en 2020. La innovación de la serie S800 se refleja principalmente en la modularización inteligente, la digitalización completa y la conexión de red inalámbrica. La pantalla es totalmente táctil 100% y las herramientas gráficas pueden desarrollar interfaces 3D complejas.
3. Sistema de control CNC Cybelec
Cybelec, fundada en Suiza en 1970, es un fabricante de renombre mundial de software de control numérico por ordenador para el conformado de metales. El sistema CNC de Cybelec incluye versiones con botones: CT8P, CT8PS, CT8PS, CT15P y la versión de pantalla táctil: serie VisiTouch. A continuación, se muestra un vídeo de la experiencia de nuestra empresa con el controlador Cybelec VT19:
La serie Cybtouch está equipada con la herramienta Cybtouch, que se puede utilizar para la transmisión inalámbrica entre la PC y el sistema. Las pantallas táctiles modernas con superficie de vidrio aerodinámica se pueden utilizar con guantes.
La pantalla táctil permite la programación de gráficos 2D o 3D, que se pueden programar directamente. Cálculo automático de la secuencia de plegado, medición de ángulos y detección de colisiones. Puede controlar el movimiento de varios ejes y se puede utilizar para prensas plegadoras en tándem.
Comparación de controladores de prensas plegadoras
Característica/Marca | Delem DA-66T | ESA 630 | Cybelec VisiTouch 19 |
Mostrar | Pantalla táctil TFT a color de alta resolución de 17" | Pantalla táctil a color de 10" | Pantalla táctil de superficie de vidrio aerodinámico moderno de 19" |
Modo de programación | Programación gráfica 2D, cálculo automático de secuencia de curvatura, detección de colisiones | Editor gráfico y visualización 2D | Dibujo gráfico de perfil en 2D, cálculo automático de secuencia de curvatura |
Capacidad de memoria | 1 GB | Disco de silicio de 128 MB | Tarjeta de memoria CFAST SATA de 32 GB |
Ejes soportados | Hasta 8+1 ejes | Hasta 5 ejes | Múltiples ejes, incluidas ayudas de plegado complejas y ejes esclavos |
Sistema operativo | Ventanas en tiempo real integradas | No especificado | Ventanas 10 |
Interfaz de usuario | Navegación táctil intuitiva, ergonomía optimizada | Interfaz de pantalla táctil fácil de usar | HMI fácil de usar, programación intuitiva, asistentes de configuración dedicados |
Programación fuera de línea | Software offline Profile-TL | Se incluye una licencia de software sin conexión | Funciones de copia de seguridad y restauración internas |
Características de seguridad | Interruptor de parada de emergencia, interfaz de corrección y flexión del sensor | No especificado | Sistema de seguridad láser DSP-TX, compensación automática Y1/Y2 |
Precio | Alto | Bajo | Medio |
Facilidad de uso | Interfaz de usuario intuitiva y de alta calidad | Mediano, adecuado para operaciones de complejidad simple a media. | Interfaz alta, fácil de usar, configuración rápida. |
Compatibilidad | Compatibilidad con Delem Modusys, USB, interfaz periférica | Adecuado para varias prensas plegadoras, incluidas las convencionales, sincronizadas, híbridas, eléctricas y tándem. | Compatible con archivos de formato DXF y 3D |
Características adicionales | Configuración completa de la máquina en 3D, múltiples estaciones de herramientas, algoritmos de control altamente efectivos | Programación gráfica avanzada, algoritmos sofisticados, HMI clara y ergonómica | Visualización y simulación 3D completa, soluciones automáticas para piezas complejas |
1. Sistemas de control de la ESA
Ventajas:
- Versatilidad: Las series S600 y S800 de ESA cuentan con controles de pantalla táctil y pueden gestionar configuraciones de 3 a 128 ejes.
- Programabilidad: el PLC y la HMI se pueden reprogramar para cumplir con requisitos personalizados.
- Amplia aplicabilidad: adecuado para varios tipos de prensas plegadoras, incluidas prensas plegadoras hidráulicas, hidráulicas sincronizadas, eléctricas y tándem.
- Actualizaciones rápidas: Los productos de la ESA se actualizan con frecuencia para mantenerse al día con los avances tecnológicos.
Desventajas:
- Complejidad: Debido a su multifuncionalidad, puede requerir más tiempo de aprendizaje y adaptación.
2. Sistemas de control Cybelec
Ventajas:
- Excelente calidad: Los productos Cybelec son reconocidos por su calidad superior y brindan un control de curvatura de alta precisión.
- Alta confiabilidad: funciona excelentemente durante el uso a largo plazo con bajas tasas de fallas.
Desventajas:
- Operación compleja: En comparación con otras marcas, la interfaz de Cybelec puede ser más compleja, requiriendo más tiempo de capacitación y adaptación.
3. Sistemas de control de deleciones
Ventajas:
- Facilidad de uso: Los productos Delem son fáciles de usar y operar, adecuados para una rápida incorporación.
- Variedad de opciones: ofrece una gama de modelos, incluidas versiones de pantalla táctil (por ejemplo, DA-66T, 69T, 53T, 58T, 41T, 42T) y versiones de botón (por ejemplo, DA-66W, 65R), que satisfacen diferentes necesidades.
- Programación eficiente: sistemas como el DA-58T proporcionan programación gráfica táctil 2D, cálculo automático del proceso de doblado y detección de colisiones.
Desventajas:
- Costo más alto: los productos Delem son relativamente caros, lo que puede no ser adecuado para usuarios conscientes del presupuesto.
4. Recomendaciones
Al elegir un controlador de prensa plegadora, tenga en cuenta sus necesidades específicas y su presupuesto:
- Presupuesto limitado e incorporación rápida: los sistemas de control Delem se recomiendan por su facilidad de uso, aunque se debe considerar su mayor costo.
- Alta calidad y precisión: Cybelec es una excelente opción, a pesar de su operación más compleja, su calidad superior y confiabilidad valen la inversión.
- Multifuncionalidad y personalización: Los sistemas de control ESA son la mejor opción, especialmente para escenarios que requieren control y personalización de múltiples ejes.
Últimos avances en tecnología de control de prensas plegadoras
El campo de la fabricación de metales evoluciona continuamente y la tecnología de los controladores de prensas plegadoras no es una excepción. Los avances recientes en los controladores de prensas plegadoras han traído consigo mejoras significativas en precisión, eficiencia, automatización y facilidad de uso. A continuación, se presenta una descripción general de algunas de las últimas innovaciones y tendencias en la tecnología de los controladores de prensas plegadoras:
Integración con software CAD/CAM:
Uno de los avances más notables en la tecnología de control de las prensas plegadoras es la integración perfecta con el software de diseño asistido por ordenador (CAD) y fabricación asistida por ordenador (CAM). Esta integración permite la importación directa de diseños de piezas al controlador de la prensa plegadora, lo que reduce la necesidad de introducir datos manualmente y minimiza el riesgo de errores. Los operadores ahora pueden programar de forma rápida y precisa secuencias de plegado complejas a partir de archivos CAD, lo que aumenta la eficiencia y la precisión.
Programación y simulación fuera de línea:
Los controladores de las prensas plegadoras modernas suelen ofrecer funciones de simulación y programación sin conexión. Esta tecnología permite a los operadores crear y probar programas de plegado sin interrumpir el proceso de producción real. Las simulaciones virtuales ayudan a identificar y abordar posibles problemas, lo que garantiza que el proceso de plegado se optimice antes de comenzar. Esto reduce los tiempos de configuración y minimiza los desechos, lo que en última instancia genera ahorros de costos.
Gráficos y visualización 3D:
Algunos de los controladores de prensas plegadoras más recientes están equipados con gráficos 3D avanzados y funciones de visualización. Estas interfaces proporcionan a los operadores una vista integral del proceso de plegado, lo que les permite inspeccionar la pieza, las herramientas y la configuración de la máquina en un entorno virtual. Esto ayuda a una configuración rápida y precisa, especialmente para piezas complejas con múltiples pliegues.
Flexión asistida por IA:
La inteligencia artificial (IA) y el aprendizaje automático están encontrando su camino en la tecnología de control de las prensas plegadoras. Los algoritmos de IA pueden analizar datos de plegado anteriores para optimizar los procesos de plegado futuros. Esta tecnología puede predecir posibles problemas y sugerir ajustes, lo que conduce a una mejor calidad y eficiencia.
Conectividad IoT:
El Internet de las cosas (IoT) está dejando su huella en la industria de fabricación de metales. Los controladores de prensas plegadoras con conectividad IoT pueden transmitir datos en tiempo real sobre el rendimiento de la máquina, el desgaste de las herramientas y las métricas de producción a un sistema centralizado. Esto permite un mantenimiento proactivo, la toma de decisiones basada en datos y la supervisión remota del proceso de producción.
Interfaces fáciles de usar:
Los controladores de prensa plegadora más modernos priorizan la facilidad de uso. Las interfaces de pantalla táctil intuitivas, la programación gráfica y los asistentes paso a paso facilitan a los operadores con distintos niveles de habilidad la configuración y ejecución eficiente de las operaciones de plegado. Estas interfaces reducen la curva de aprendizaje y minimizan el riesgo de errores.
Innovaciones en seguridad:
La seguridad sigue siendo una prioridad máxima en la tecnología de control de las prensas plegadoras. Los controladores avanzados están equipados con funciones de seguridad mejoradas, como cortinas de luz mejoradas, sistemas de seguridad multizona y una mejor integración con las funciones de parada de emergencia. Estas medidas garantizan la protección de los operadores y el equipo durante el funcionamiento.
Eficiencia Energética:
Algunos controladores de prensas plegadoras se centran ahora en la eficiencia energética. Pueden optimizar los movimientos de la máquina, reduciendo el consumo de energía y el impacto medioambiental. Los controladores energéticamente eficientes no solo ahorran en costes operativos, sino que también contribuyen a prácticas de fabricación sostenibles.
En conclusión, los últimos avances en la tecnología de los controladores de las prensas plegadoras han revolucionado la industria de la fabricación de metales. Estas innovaciones se centran en mejorar la precisión, la eficiencia y la facilidad de uso, al tiempo que incorporan funciones de seguridad, conectividad y sostenibilidad. A medida que la industria siga evolucionando, es probable que los controladores de las prensas plegadoras desempeñen un papel aún más importante a la hora de dar forma al futuro de la metalurgia.
Conclusión
Las prensas plegadoras modernas están equipadas con tecnologías avanzadas controles de prensa plegadora, y las diferentes marcas y modelos de estos controladores pueden ofrecer distintas ventajas. Antes de elegir un sistema de control avanzado para prensas plegadoras, es esencial comprender completamente sus características y la reputación de la marca, para luego seleccionar el controlador más adecuado en función de su presupuesto.
Al seleccionar un controlador para una prensa plegadora, los factores clave a tener en cuenta incluyen funcionalidad, estabilidad, facilidad de uso y seguridad. Los controles de prensa plegadora fáciles de usar pueden mejorar la productividad, reducir el tiempo de configuración y mejorar el rendimiento general de la máquina. Los controladores de alta calidad están diseñados para garantizar un plegado preciso y resultados confiables.
En este artículo, exploro tres marcas de controles de prensa plegadora avanzados que ofrecen la mejor experiencia de usuario. KRRASS, por ejemplo, actualiza continuamente su gama de productos, ofreciendo características y mejoras de vanguardia. Si bien los controles de prensa plegadora KRRASS son conocidos por su facilidad de uso, pueden tener un precio más alto. Sin embargo, su calidad superior justifica la inversión. Actualizar a un controlador CNC de prensa plegadora de última generación puede aumentar el rendimiento de la máquina y reducir los costos generales de producción.