Comprender el papel crucial que desempeña la selección correcta del tonelaje en las prensas plegadoras es fundamental para garantizar una calidad óptima del producto. La no selección del tonelaje adecuado puede generar diversos problemas de calidad, como deformación del material o grietas, lo que en última instancia afecta la satisfacción del cliente. Para ayudarlo a comprender el tonelaje de la prensa plegadora, incluido cómo calcularlo de manera efectiva, profundizaremos en aspectos esenciales. Hoy, exploraremos la importancia de utilizar un Tabla de tonelaje de prensa plegadora, proporcionando información para ayudarle a tomar decisiones informadas y mejorar la calidad del producto.
Tabla de contenido
Introducción
¿Qué es una prensa plegadora?
Prensas plegadoras Son máquinas fundamentales en la industria de fabricación de chapa metálica, utilizadas para doblar y dar forma a láminas de metal con precisión. Desempeñan un papel fundamental en la transformación de láminas planas de metal en diversos componentes utilizados en industrias que van desde la automotriz hasta la construcción.
Tipos de prensa plegadora
Prensas plegadoras mecánicas: Estos son accionados por un volante y utilizan un mecanismo excéntrico para mover el cabezal, adecuado para operaciones de doblado a alta velocidad.
Prensas plegadoras hidráulicas: Utilizan cilindros hidráulicos para mover el ariete y aplicar fuerza a la pieza de trabajo. Ofrecen un control preciso del proceso de doblado y son capaces de manejar requisitos de alto tonelaje.
Prensas plegadoras neumáticas: Estos utilizan presión de aire para mover el ariete y generalmente se utilizan para materiales de calibre más liviano o requisitos de producción más pequeños.
Prensas plegadoras servoeléctricas: Estos emplean un servomotor para controlar el movimiento del ariete, ofreciendo alta precisión y eficiencia energética. Son ideales para aplicaciones que requieren una fuerza de flexión baja a media.
Prensas plegadoras CNC: Aunque no es un tipo en sí mismo, la tecnología CNC se puede integrar en prensas plegadoras hidráulicas, neumáticas o servoeléctricas para automatizar y controlar el proceso de plegado, mejorando la precisión y la repetibilidad.
Importancia de las tablas de tonelaje de las prensas plegadoras
Precisión: Tablas de tonelaje de prensas plegadoras Ayudar a los profesionales a determinar la cantidad precisa de fuerza necesaria para las operaciones de doblado, garantizando resultados precisos.
Eficiencia: Al consultar las tablas de tonelaje, los fabricantes pueden optimizar su flujo de trabajo y minimizar el desperdicio de material seleccionando las configuraciones adecuadas de la prensa plegadora.
Rentabilidad: El uso preciso de tablas de tonelaje ayuda a optimizar los recursos, lo que genera ahorros de costos en términos de uso de materiales y operación de la máquina.
Seguridad: La utilización adecuada de las tablas de tonelaje garantiza que la prensa plegadora funcione dentro de parámetros seguros, reduciendo el riesgo de accidentes y daños al equipo.
Conceptos básicos
Explicación de las tablas de tonelaje de la prensa plegadora
Tablas de tonelaje de prensas plegadoras Son representaciones gráficas que proporcionan datos esenciales sobre la cantidad de fuerza necesaria para doblar un material específico de un espesor y una longitud determinados. Estos gráficos suelen incluir diversos parámetros, como el tipo de material, el espesor, la longitud de curvatura y el ángulo de curvatura.
Al consultar estos gráficos, los profesionales de fabricación de chapa metálica pueden determinar con precisión el tonelaje necesario para lograr curvas precisas, lo que garantiza la calidad y la integridad de los componentes terminados.
Funciones y aplicaciones de las tablas de tonelaje de prensas plegadoras
Determinación de la fuerza de flexión: Los gráficos de tonelaje ayudan a determinar la cantidad de fuerza necesaria para doblar un material determinado con precisión. Esta información es fundamental para seleccionar la máquina plegadora y la configuración de herramientas adecuadas.
Optimización del proceso de plegado: Al consultar las tablas de tonelaje, los fabricantes pueden optimizar el proceso de plegado, lo que minimiza el ensayo y error y reduce el desperdicio de material. Esto genera una mayor eficiencia y rentabilidad en las operaciones de fabricación de chapa metálica.
Garantizar la calidad y la precisión: Las tablas de tonelaje desempeñan un papel fundamental para garantizar la calidad y la precisión del proceso de plegado. Al seleccionar el tonelaje correcto en función de las propiedades y dimensiones del material, los profesionales pueden lograr plegados precisos que cumplan con las especificaciones y tolerancias deseadas.
Consideraciones de seguridad: El uso correcto de las tablas de tonelaje ayuda a garantizar que la prensa plegadora funcione dentro de parámetros seguros. La sobrecarga de la máquina puede provocar daños en el equipo o accidentes, lo que resalta la importancia de consultar las tablas de tonelaje para una operación segura.
Componentes de los gráficos de tonelaje de la prensa plegadora
Tablas de tonelaje de prensas plegadoras Por lo general, constan de los siguientes componentes:
Tipo de material: Los distintos materiales presentan distintos niveles de resistencia a la flexión, lo que requiere distintas cantidades de fuerza. Los materiales más comunes son el acero, el aluminio y el acero inoxidable.
Espesor del material: El espesor de la chapa metálica que se dobla influye directamente en la cantidad de fuerza necesaria. Los materiales más gruesos suelen requerir un mayor tonelaje.
Longitud de curva: La longitud de la curva o la distancia entre los puntos de curvatura afectan el tonelaje requerido. Las curvas más largas pueden requerir un tonelaje mayor en comparación con las curvas más cortas.
Ángulo de curvatura: El ángulo en el que se dobla el material también afecta el tonelaje requerido. Los ángulos más pronunciados pueden requerir un mayor tonelaje para lograr el doblez deseado.
Tablas de tonelaje de prensas plegadoras para el diseño del proceso de plegado
Cómo seleccionar el tonelaje de la prensa plegadora según las tablas de tonelaje de la prensa plegadora
Características del material del fósforo:
Asegúrese de que el tipo y el espesor del material coincidan con las especificaciones proporcionadas en la tabla de tonelaje. Los distintos materiales requieren distintas cantidades de fuerza para doblarse, por lo que es fundamental seleccionar la categoría adecuada en la tabla.
Tenga en cuenta las especificaciones de curvatura:
Tenga en cuenta los requisitos específicos de la curva, incluidos el ángulo y la longitud de la curva. Estas especificaciones influirán en la cantidad de fuerza necesaria para el proceso de curvado y ayudarán a determinar el tonelaje adecuado.
Consulte la tabla de tonelaje:
Consulte la tabla de tonelaje de la prensa plegadora para determinar el tonelaje requerido según las propiedades del material y las especificaciones de plegado. Localice los valores correspondientes para la longitud de plegado, el ángulo y el espesor del material en la tabla para identificar el rango de tonelaje adecuado.
Seleccione herramientas compatibles:
Elija herramientas para prensa plegadora que sean compatibles con el tonelaje y las especificaciones de plegado seleccionados. Las herramientas deben ser capaces de lograr el ángulo y la longitud de plegado deseados sin exceder los límites de tonelaje especificados.
Verificar y ajustar según sea necesario:
Antes de iniciar el proceso de doblado, verifique que el tonelaje seleccionado y la configuración de las herramientas coincidan con las especificaciones proporcionadas en la tabla de tonelaje. Realice los ajustes necesarios para garantizar la precisión y exactitud en la operación de doblado, teniendo en cuenta factores como las variaciones del material y la complejidad del doblado.
Tabla de fuerza de flexión del aire
Un diagrama de fuerza de plegado con aire, o diagrama de fuerza, desglosa una serie de componentes clave del plegado de chapa metálica en un formato de fácil consulta. Poder leer un diagrama de fuerza de plegado es crucial para cualquier operador de prensa de plegado e ingeniero de chapa metálica.
El calibre, el radio interior, la apertura de la matriz y la longitud mínima de la brida están todos interconectados a través de diferentes ecuaciones y relaciones; la tabla de fuerza de curvatura de aire organiza estas variables y señala el camino hacia la configuración ideal.
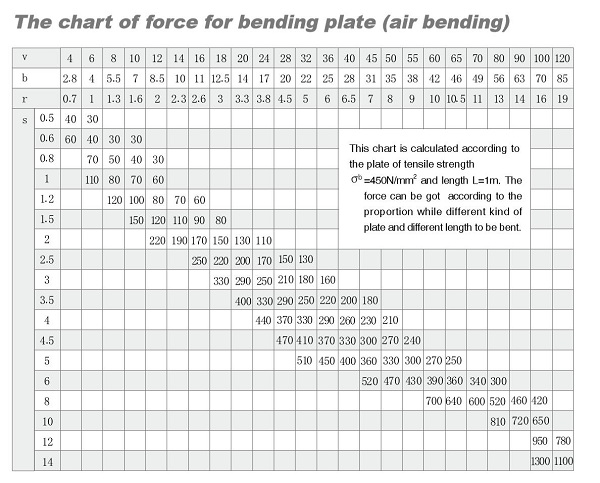
Nota: El valor de la tabla es la presión necesaria para doblar la lámina cuando la longitud es de 1 metro.
Cálculo del tonelaje necesario para el plegado
Una vez que comprenda cómo utilizar una tabla de fuerza de curvatura, será fácil calcular el tonelaje necesario para cualquier operación de curvatura:
- Calcule la abertura en V deseada en función del espesor de la chapa que va a doblar. Redondee hacia arriba hasta la abertura en V más cercana en la tabla para que coincida con su herramienta.
- Calcule la relación entre la resistencia a la tracción de su material y el acero estándar (carbono .3%, 45 kg/mm²). Hacemos esto porque la mayoría de los gráficos de fuerza de flexión por aire se basan en acero estándar.
- Multiplique la longitud de la pieza de trabajo (L) por el tonelaje por pie (F) de la tabla de fuerza estándar por la relación entre la resistencia a la tracción (TS) del material y la resistencia a la tracción del acero dulce.
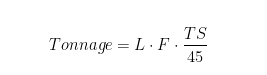
Resistencia a la tracción (TS)
La resistencia a la tracción es una propiedad del metal y se basa en la cantidad de fuerza necesaria para provocar que el material falle o se rompa. El tonelaje necesario está directamente relacionado con la resistencia a la tracción del material. Como mostraremos a continuación, la resistencia a la tracción sirve como una forma conveniente de convertir un gráfico de fuerza de flexión de un material a otro.
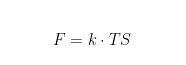
Resistencia a la tracción de diferentes materiales
Material | Suave (kg/mm^2) | Duro (kg/mm^2) |
Dirigir | 2.5 - 4 | - |
Estaño | 45387 | - |
Aluminio | 9.3 | 171 |
Aleación de aluminio tipo 4 | 23 | 48 |
Duralumin | 26 | 48 |
Zinc | 15 | 25 |
Cobre | 22-28 | 30-40 |
Latón (70:30) | 33 | 53 |
Latón (60:40) | 38 | 49 |
Bronce fosforoso / Bronce | 40-50 | 50-75 |
Alpaca | 35-45 | 55-70 |
Hierro laminado en frío | 32-38 | - |
Acero al carbono .1% | 32 | 40 |
Acero al carbono .2% | 40 | 50 |
Acero al carbono .3% | 45 | 60 |
Acero al carbono .4% | 56 | 72 |
Acero al carbono .6% | 72 | 90 |
Acero al carbono .8% | 90 | 110 |
Acero al carbono 1.0% | 100 | 130 |
Acero al silicio | 55 | 65 |
Acero inoxidable | 65-70 | - |
Níquel | 44-50 | 57-63 |
Cómo leer la tabla de tonelaje de la prensa plegadora
El Tabla de tonelaje de prensas plegadoras Puede ser útil cuando se conocen el espesor del material y el iR (radio interno del producto).
Tonelaje necesario para doblar material de 1 mm de largo (F)
Ancho de la matriz en V (abertura en V) mm ( V )
Longitud mínima de brida a doblar mm (b)
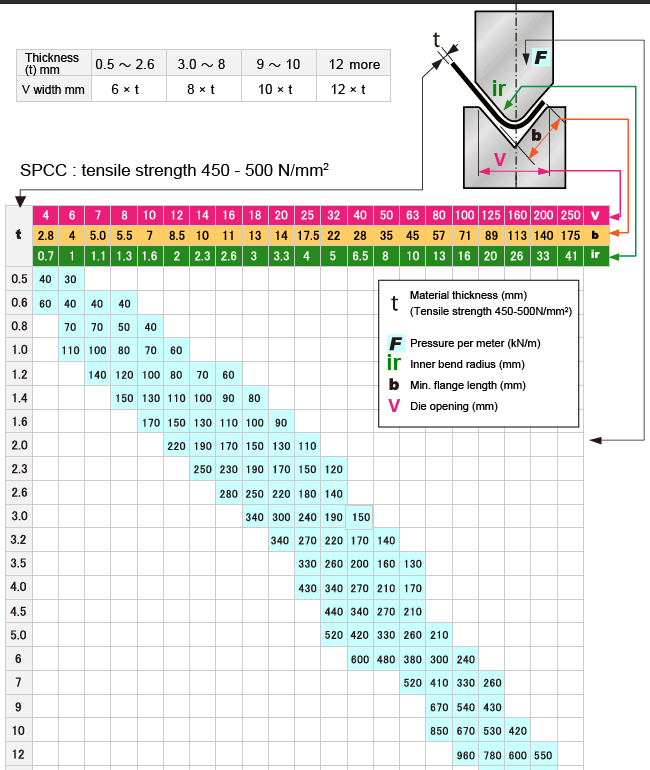
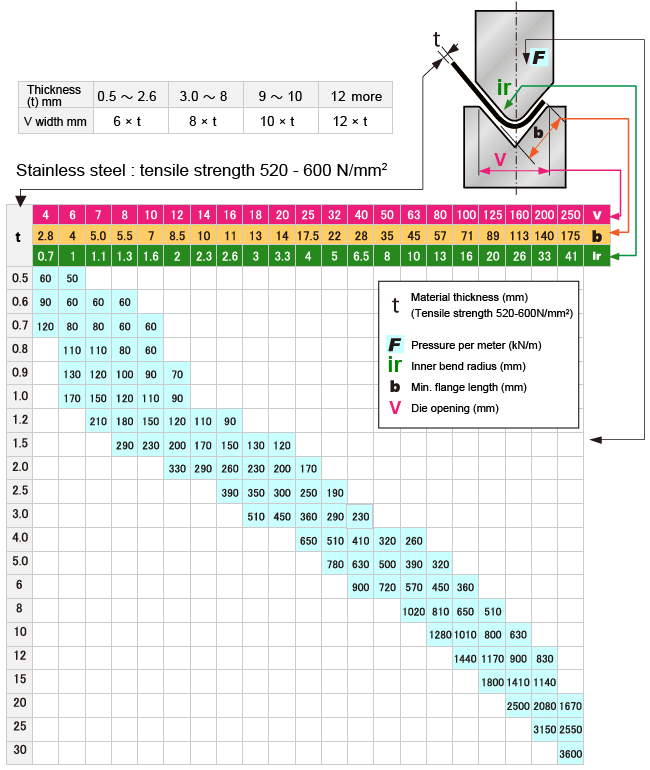
Problemas y soluciones comunes en el uso de la tabla de tonelaje
Variaciones de materiales
Asunto: Las variaciones del material, como las diferencias en dureza o composición dentro del mismo tipo de material, pueden generar discrepancias entre las fuerzas de flexión previstas y las reales.
Solución:
Prueba de materiales: Realice pruebas exhaustivas del material para determinar sus propiedades mecánicas, incluidas la dureza, el límite elástico y la elasticidad. Utilice estos datos para ajustar los cálculos de tonelaje en consecuencia.
Ajustar la configuración de tonelaje: Aumente el margen de seguridad al seleccionar el tonelaje de la tabla para adaptarse a las posibles variaciones de material. Esto garantiza que la prensa plegadora pueda manejar cambios inesperados en las propiedades del material sin comprometer el proceso de plegado.
Calibración regular: Asegúrese de que la prensa plegadora esté calibrada periódicamente para mantener la precisión en los cálculos de tonelaje y las predicciones de fuerza de plegado.
Formas de curvas complejas
Asunto: Las operaciones de doblado que involucran formas complejas o múltiples curvas pueden plantear desafíos a la hora de predecir con precisión los tonelajes requeridos.
Solución:
Descomponer curvas: Divida las operaciones de plegado complejas en segmentos más pequeños y manejables. Analice cada segmento individualmente y calcule el tonelaje requerido en función de parámetros de plegado específicos.
Enfoque iterativo: Comience con ajustes de tonelaje más bajos y aumente gradualmente según sea necesario. Esto permite realizar ajustes y ajustes finos a medida que avanza el proceso de doblado, lo que garantiza resultados óptimos.
Software de simulación: Utilice software de simulación que predice con precisión las fuerzas de doblado para formas complejas. Estas herramientas simulan el proceso de doblado virtualmente, lo que permite a los fabricantes optimizar los ajustes de tonelaje antes de la producción real.
Consulte a los expertos: Busque el asesoramiento de profesionales experimentados o ingenieros especializados en la fabricación de chapa metálica para obtener orientación sobre el manejo de formas de curvatura complejas y la selección de tonelajes adecuados.
Variaciones del espesor del material
Asunto: Las variaciones en el espesor del material a lo largo de la chapa pueden provocar una flexión desigual o una sobrecarga de la prensa plegadora.
Solución:
Medición de espesor: Mida el espesor del material en varios puntos de la lámina para identificar variaciones. Utilice el valor de espesor máximo al consultar la tabla de tonelaje para garantizar una capacidad suficiente para todas las áreas del pliegue.
Doblado selectivo: Si es posible, ajuste la secuencia de plegado para tener en cuenta las variaciones de espesor. Priorice los plegados en áreas con espesor constante para minimizar el impacto de las variaciones en el proceso de plegado general.
Implementar el control de calidad: Implemente medidas de control de calidad estrictas para garantizar que el espesor del material se mantenga dentro de las tolerancias aceptables. Las inspecciones y controles regulares durante el proceso de fabricación pueden ayudar a identificar y abordar las variaciones de espesor desde el principio.
Error del operador
Asunto: La entrada de datos inexactos o la interpretación errónea de las tablas de tonelaje por parte de los operadores pueden llevar a una selección incorrecta de configuraciones de tonelaje.
Solución:
Formación y educación: Proporcionar capacitación integral a los operadores sobre cómo interpretar y utilizar correctamente las tablas de tonelaje. Destacar la importancia de introducir datos con precisión y las posibles consecuencias de los errores del operador.
Vuelva a comprobar: Implemente procedimientos para verificar dos veces los cálculos y ajustes de tonelaje antes de iniciar las operaciones de doblado. Incentive a los operadores a verificar el tonelaje seleccionado con las especificaciones proporcionadas en la tabla de tonelaje para garantizar la precisión.
Documentación: Mantenga una documentación detallada de los cálculos y ajustes de tonelaje para cada operación de doblado. Esto permite una fácil referencia y revisión, lo que ayuda a identificar y abordar cualquier discrepancia o error. Las actualizaciones periódicas de capacitación y las evaluaciones de habilidades también pueden ayudar a mitigar los errores del operador con el tiempo.
Cómo calcular el tonelaje de una prensa plegadora
Relación entre la presión de plegado y el tonelaje de la prensa plegadora
En el manómetro, la unidad de presión es MPa. 1 Pa = 1 N/m2, 1 MPa = 1000000 Pa, 1 m2 = 1000000 mm2. El kilogramo fuerza es la unidad de fuerza: 1 kg fuerza = 9,8 Newton. Son dos magnitudes físicas diferentes, pero tienen cierta relación: para producir una presión de “1 MPa”, se requieren unos 10 kg de fuerza sobre un área de un centímetro cuadrado. [1 N = 1 kg·m/s²]
Al seleccionar una máquina dobladora, el cliente generalmente elige la máquina por tonelaje. Para ser precisos, una presión de 980 KN equivale a una fuerza de 100 toneladas. En la selección de la máquina, estimamos aproximadamente que una presión de 1000 KN equivale a una fuerza de aproximadamente 100 toneladas.
Fórmula para el cálculo del tonelaje de la prensa plegadora
La fórmula de cálculo de la presión: P=650S2·L/V
Parámetros importantes en el proceso de plegado
P = Presión nominal (KN)
S = espesor de la placa (mm)
L = longitud de la placa (m)
V = ancho de la muesca (mm)
Como regla general, el ancho de la muesca es de 8 a 10 veces el espesor de la placa.
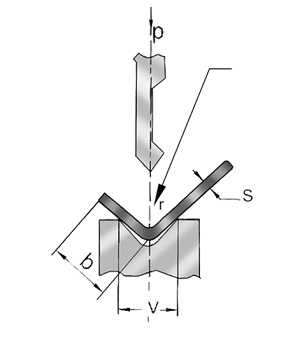
Calculadora de tonelaje
Apertura en V recomendada del troquel inferior
Espesor del material S | 0,5-2,5 mm | 3-8 mm | 9-10 mm | >12 mm |
Abertura en V de la matriz inferior | 6×S | 8×S (General) | 10×S | 12×S |
Radio interior de curvatura desde la abertura de la matriz en V
Material | V |
Acero dulce | 1/6 × V |
Inoxidable | 1/5 × V |
Aluminio | 1/8 × V |
Tonelaje requerido para otros metales
Latón blando | Tonelaje × 0,5 |
Aluminio blando | Tonelaje × 0,5 |
Acero inoxidable | Tonelaje × 1,5 |
Acero de alta resistencia | Tonelaje ×2,75 |
Tonelaje de dobladillo de acero dulce
Mm | Desgarro,t/m | Dobladillo completo |
0.6 | 9 | 23 |
1 | 15 | 40 |
1.5 | 22 | 63 |
2 | 30 | 80 |
2.5 | 55 | 90 |
3 | 77 | 100 |
Casos de estudio
Caso 1
Cuando la longitud de la placa es de 4000 mm y s es de 5 mm, calculamos v = 45 mm (5 x 9 = 45). Consultamos la tabla y encontramos que la presión de flexión unitaria es de 360 kN/m. Como la longitud de la placa es de 4 m, sabemos que el tonelaje total es de 360 kN x 4 = 1440 kN = 144 toneladas.
Los datos de esta tabla se basan en materiales con resistencia a la tracción = 450 N/mm².
La tabla anterior es para placas de acero al carbono, por lo que para calcular el tonelaje de la prensa plegadora para placas de diferentes materiales es necesario multiplicar por diferentes coeficientes de material.
El coeficiente de cálculo aproximado de la presión de flexión es el siguiente:
Bronce (blando): 0,5
Acero inoxidable: 1,5
Aluminio (blando): 0,5
Acero al cromo molibdeno: 2
Caso 2
Una fábrica necesita comprar una prensa plegadora hidráulica CNC para doblar placas de acero inoxidable. La longitud de la placa es de 3 metros y el espesor es de 6 mm.
Al consultar la tabla de fuerza de plegado, sabemos que la presión unitaria necesita 390 kN y el tonelaje total es 1170 kN (117 toneladas). Debido a que el coeficiente del acero inoxidable es 1,5, la fábrica necesita comprar una prensa plegadora con al menos 175,5 toneladas.
Calcular con la fórmula: P=650×62×3/ (10×6)=117kN. Si es acero inoxidable, el tonelaje es 117,5×1,5=175,5ton.
Según los requisitos de plegado y las condiciones de producción, los clientes pueden elegir el equipo de plegado adecuado. Sin embargo, el tonelaje de la prensa plegadora también depende del troquel inferior de la prensa plegadora en casos específicos. Al utilizar una abertura más amplia del troquel inferior, la prensa plegadora requiere un tonelaje menor. Las personas aún necesitan consultar el tonelaje con la fábrica de prensas plegadoras cuando compran una prensa plegadora con punzón superior y troquel inferior personalizados.
Sobreestimación del tonelaje: consecuencias y métodos
El uso de un tonelaje excesivo durante la operación de plegado puede generar diversos riesgos y complicaciones. Es importante comprender estos riesgos para mantener la calidad de la pieza de trabajo y la integridad de la máquina plegadora.
Los riesgos de utilizar demasiado tonelaje
Daños en la prensa plegadora:
Sobreestimar el tonelaje puede ejercer una tensión indebida sobre los componentes de la prensa plegadora, lo que puede provocar un desgaste prematuro o incluso una falla catastrófica de la máquina.
Daños en las herramientas:
La fuerza excesiva puede dañar el punzón y la matriz, lo que genera reparaciones o reemplazos costosos y tiempo de inactividad de la máquina.
Daños en la pieza de trabajo:
Aplicar demasiada fuerza puede provocar defectos en el metal, como grietas, deformaciones o exceder el ángulo de curvatura deseado, lo que puede hacer que la pieza de trabajo quede inutilizable.
Precisión reducida:
El exceso de tonelaje puede provocar variaciones en la recuperación elástica e inconsistencias en el ángulo de curvatura, lo que compromete la precisión del proceso de curvatura.
Peligros de seguridad:
Operar una máquina más allá de su capacidad prevista puede representar riesgos de seguridad para el operador y otro personal en las cercanías.
Consejos para evitar la sobreestimación
Utilice datos de material precisos:
Asegúrese de que la resistencia a la tracción y el espesor del material se midan con precisión y se tengan en cuenta en los cálculos de tonelaje.
Seleccione el ancho de matriz adecuado:
Elija una abertura de matriz que sea adecuada para el espesor y el tipo de material, ya que esto puede afectar significativamente el requisito de tonelaje.
Consulte las tablas de materiales y equipos:
Los fabricantes suelen proporcionar cuadros que relacionan las propiedades del material con el tonelaje necesario para longitudes y ángulos de curvatura específicos. Utilice estos cuadros para obtener estimaciones más precisas.
Utilice una calculadora de tonelaje:
Utilice una calculadora de tonelaje de prensa plegadora confiable que tenga en cuenta todas las variables, incluido el tipo de material, el espesor, la longitud de curvatura y el ancho de la matriz.
Tenga en cuenta el radio de curvatura: tenga en cuenta el radio de curvatura deseado en sus cálculos, ya que esto puede afectar la cantidad de tonelaje requerido.
Realizar curvas de prueba:
Realice curvas de prueba en material de desecho para determinar el tonelaje real necesario para un trabajo en particular, lo que puede ayudar a refinar sus estimaciones.
Utilice controles CNC cuando estén disponibles:
Para las prensas plegadoras CNC, aproveche la capacidad del sistema de control para calcular y ajustar el tonelaje automáticamente en función de los parámetros programados.
Manténgase dentro de los límites de la máquina:
Consulte siempre las especificaciones de la prensa plegadora para asegurarse de que el tonelaje no supere la capacidad máxima de la máquina. Operar dentro de los límites de la prensa plegadora es crucial para la longevidad del equipo y la seguridad de las operaciones.
Operadores de trenes:
Capacite adecuadamente a los operadores de prensas plegadoras para que comprendan la importancia de un cálculo preciso del tonelaje y los riesgos asociados con la sobreestimación. Un operador informado tiene más probabilidades de realizar ajustes precisos y reconocer cuándo los valores de tonelaje pueden ser demasiado altos.
Mantenimiento regular:
Mantenga la prensa plegadora y las herramientas en buenas condiciones de funcionamiento. El mantenimiento regular puede ayudar a identificar posibles problemas que puedan afectar la precisión de los requisitos de tonelaje, como herramientas desgastadas o desviaciones de calibración.
Ajustes y resultados del documento:
Mantenga un registro de todos los ajustes realizados en función de las curvas de prueba o trabajos anteriores. Esta documentación puede servir como una valiosa referencia para trabajos futuros en materiales similares o con especificaciones de curvatura similares.
Considere la recuperación elástica del material:
Tenga en cuenta la recuperación elástica del material, que es la tendencia del material a volver a su forma original después de doblarse. Esto puede afectar el ángulo final y puede provocar una sobrecompensación en el tonelaje si no se tiene en cuenta adecuadamente.
Si siguen estos consejos y son conscientes de los riesgos asociados con la sobreestimación de los requisitos de tonelaje, los operadores pueden ayudar a garantizar que las operaciones de la prensa plegadora sean seguras y efectivas, produciendo curvas de alta calidad sin desgaste innecesario del equipo ni riesgo de daños en la pieza de trabajo.
De la misma manera, subestimar el tonelaje de la máquina dobladora también tendrá un impacto negativo en el plegado. Todos deben prestar atención al calcular el tonelaje.
Conclusión
Tablas de tonelaje de prensas plegadoras son de suma importancia para los profesionales que se dedican a la fabricación de chapa metálica. Estos gráficos proporcionan información esencial sobre la fuerza necesaria para doblar con precisión distintos materiales de distintos espesores y longitudes.
Comprender y utilizar eficazmente las tablas de tonelaje y aprender a calcular el tonelaje son fundamentales para garantizar la calidad y la precisión del proceso de doblado.