La fabricación de chapa metálica se refiere a una variedad de procesos utilizados para ensamblar o fabricar piezas a partir de chapa metálica en bruto. Según el material y las especificaciones del proyecto, se pueden utilizar uno o más procesos de chapa Se pueden utilizar para lograr el resultado deseado. Los clientes tienen opciones como corte de metal, soldadura, doblado, mecanizado, punzonado y estampado para crear sus productos. En esta guía, exploraremos cada proceso de chapa metálica en detalle, ayudándole a identificar los métodos más adecuados para su aplicación específica.
Descripción general de la fabricación de chapa metálica
La fabricación de chapa metálica es esencial para diversos procesos de fabricación, desde la fabricación de juguetes hasta piezas de aviones a gran escala. A pesar de su popularidad, es importante saber cómo funciona este proceso de fabricación. A continuación, se ofrece una descripción detallada de la fabricación de chapa metálica.
¿Qué es el proceso de chapa metálica?
La fabricación de chapa metálica es el proceso de convertir láminas planas de acero o aluminio en estructuras o productos metálicos mediante corte, punzonado, plegado y ensamblaje. La chapa metálica se puede cortar, doblar o estirar en casi cualquier forma, lo que generalmente se hace cortando y quemando el metal.
En el proceso de fabricación de chapa metálica también se pueden utilizar herramientas especiales, como sierras de cinta y sierras de corte. Estas garantizan un corte uniforme durante todo el proceso. Los sopletes de corte son capaces de cortar grandes secciones de chapa metálica con un mínimo esfuerzo.
Las fabricaciones de chapa metálica utilizan prensas plegadoras, que facilitan el proceso de fabricación de chapa metálica, ayudando a crear curvas y ángulos pronunciados dentro del metal. Existe una variedad de prensas plegadoras diferentes, que tienen diferentes funciones y se utilizan para diferentes propósitos.
Otro de los factores principales en la fabricación de chapa metálica es la soldadura. Una vez que todos los componentes están formados, se ensamblan y se sueldan en su posición. Se pueden utilizar muchas técnicas de soldadura en la fabricación de chapa metálica para evitar deformaciones u otras anomalías. Estas técnicas incluyen cubrir el metal con arena durante el proceso de enfriamiento, un proceso especial de enderezamiento, soldar de manera escalonada y utilizar un dispositivo resistente.
El enderezamiento del metal defectuoso se puede lograr con un soplete de oxiacetileno. Se aplica calor al metal de manera lenta para eliminar cualquier anomalía.
El acabado del metal suele realizarse mediante chorro de arena, imprimación y pintura. Esto garantiza que el metal tenga un aspecto fantástico y esté listo para enviarlo al cliente.
Si tienes un proyecto próximo o quieres más detalles sobre lo que podemos hacer por ti, no dudes en ponerte en contacto con nosotros.
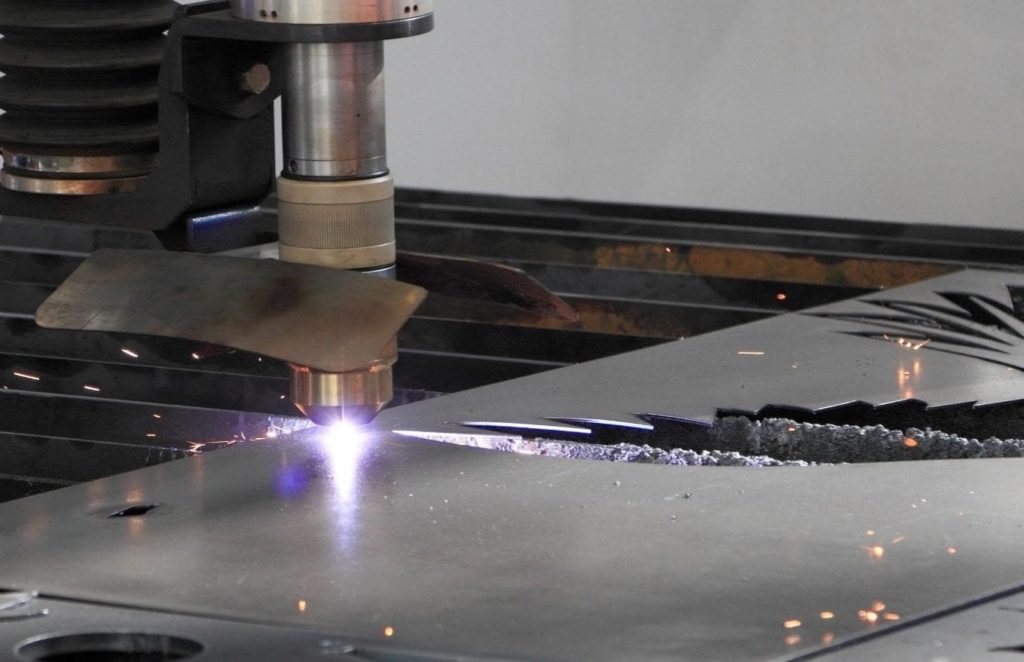
Técnicas de corte de chapa metálica
Las técnicas de corte consisten en separar el material de chapa metálica aplicando una gran fuerza para provocar que los bordes cortantes fallen. Se dividen en dos grupos: corte sin cizallamiento: corte por láser, corte por plasma, corte por chorro de agua y corte con cizallamiento: corte, troquelado, punzonado y aserrado. En esta sección se analizará cada técnica en detalle.
Corte por láser
El corte por láser es un proceso de corte térmico que implica la fusión de metales en áreas localizadas utilizando rayos láser enfocados.
Implica dos subprocesos que se ejecutan simultáneamente. El primer proceso implica enfocar un rayo láser de alta potencia sobre el material de chapa metálica. El rayo láser es absorbido por el material, lo que hace que se vaporice. El segundo proceso se produce al mismo tiempo, donde una boquilla de corte proporciona el gas de proceso o soplado para el corte láser. Este gas suele ser nitrógeno u oxígeno y ayuda a proteger el cabezal de procesamiento de vapores y salpicaduras. También es importante para la eliminación del exceso de materiales de la ranura.
Los cortadores láser pueden cortar una amplia gama de metales, desde acero inoxidable hasta acero dulce y metales no ferrosos. Sin embargo, los metales más reflectantes, como el aluminio, pueden resultar más difíciles de cortar. En esos casos, los láseres de fibra suelen ser la mejor opción. El espesor del metal puede variar entre 20 mm y 40 mm, y el espesor máximo depende de la potencia del láser.
El proceso de corte por láser es el más adecuado para aplicaciones industriales. Es muy flexible, ahorra tiempo y puede ofrecer un alto grado de precisión. Sin embargo, el proceso tiene un alto consumo de energía y gas, lo que se traduce en altos costos de inversión y estrictos requisitos de seguridad.
Corte por plasma
Es un proceso de corte térmico que implica cortar metal con gas ionizado (plasma). A medida que se lleva a cabo el proceso, se aplica una cantidad considerable de calor al metal y este se va derritiendo gradualmente. El resultado final es un corte áspero con rebabas grandes y una zona oxidada alrededor del área de corte.
Es importante tener en cuenta que la herramienta de corte por plasma solo funcionará de manera eficaz en metales conductores de electricidad. Es uno de los mejores métodos para cortar aluminio y acero inoxidable de espesor medio, cobre, latón y otros materiales conductores. Puede utilizar este proceso de corte para piezas de chapa metálica más gruesas (hasta 50 mm) en las que no haya requisitos estrictos para el acabado de la superficie.
El corte por plasma garantiza un corte más rápido, una mayor precisión y repetibilidad que muchos otros procesos de corte. También garantiza la automatización, lo que garantiza el corte eficaz de metales de alta resistencia con un menor aporte de calor. Una desventaja de este proceso es que el consumo de energía es relativamente alto y es posible que se produzca ruido con el corte en seco.
Corte por chorro de agua
El proceso de corte por chorro de agua implica el uso de un chorro de agua a alta presión para cortar láminas de metal. La presión suele rondar los 60.000 psi, lo que proporciona una velocidad de unos 610 m/s para cortar prácticamente cualquier tipo de lámina de metal.
El corte por chorro de agua es versátil y puede cortar materiales duros y blandos con abrasivos y agua a presión. En concreto, el corte por chorro de agua puro es mejor para cortar metales blandos como tejidos, caucho o láminas de metal. El corte por chorro de agua abrasivo es más adecuado para materiales duros como acero al carbono, acero inoxidable, aluminio y cobre.
El corte por chorro de agua es una gran alternativa al proceso de corte por láser. Permite obtener acabados superficiales excelentes sin rebabas ni distorsiones por calor. Sin embargo, las presiones altas pueden provocar cierta deformación cerca del área de corte, por lo que es necesario un soporte adecuado para el componente.
Cizallamiento
El corte es un proceso de fabricación de metales que corta líneas rectas sobre materiales metálicos planos mediante la aplicación de una fuerza de corte, lo que hace que los materiales se separen en ese punto de corte. Es ideal para aplicaciones de gran volumen y para cortar materiales blandos como aluminio, acero dulce y latón que no requieren acabados limpios.
Si es necesario obtener bordes rectos en láminas de metal con bordes ásperos o irregulares, el corte por cizallamiento es una de las mejores opciones. Es rentable para operaciones de alto rendimiento cuando se necesita producir miles de piezas en poco tiempo. Sin embargo, la acción de corte crea rebabas y deformación en el material. Por lo tanto, puede no ser una buena opción para aplicaciones que requieren un acabado final limpio.
Supresión
El troquelado consiste en extraer una pieza de chapa de una pieza más grande del material en bruto mediante el uso de un punzón y una matriz de troquelado. La matriz sujeta la chapa durante el proceso mientras el punzón aplica una "fuerza de troquelado" a través del metal. El material extraído es el componente deseado, mientras que el material que permanece en la matriz es el material en bruto que queda.
El troquelado de chapa metálica permite obtener componentes personalizados económicos y garantiza una precisión, un control dimensional y una repetibilidad excelentes. Sin embargo, es un poco más lento y conlleva mayores costes de herramientas que la operación de punzonado tradicional.
Puñetazos
El punzonado también crea agujeros en la chapa metálica mediante la fuerza de corte. Sin embargo, en este caso, el material extraído del agujero es el material de desecho, mientras que el material que queda en la matriz es el componente final. El punzonado ayuda a crear cortes y agujeros de varios tamaños y formas.
Este proceso es más rápido que el troquelado, ya que permite obtener piezas limpias y precisas en poco tiempo. Además, no hay riesgo de cambios térmicos en la pieza de trabajo porque no hay calor involucrado. Sin embargo, la preparación para el punzonado puede llevar mucho tiempo, ya que las cuchillas y las matrices de punzonado deben coincidir con precisión.
Aserradura
El aserrado consiste en cortar progresivamente materiales metálicos con una herramienta de dientes de sierra para realizar una serie de pequeños cortes en el metal. Cada diente de sierra utiliza fricción y fuerza de corte para separar una pequeña viruta de material del cuerpo del mismo.
Las sierras de cinta para metal tienen dientes finos y ligeramente curvados, ideales para cortar aluminio, latón, cobre y otros metales no ferrosos. Las sierras de cinta horizontales están configuradas para cortar barras más largas para cumplir con los requisitos de tamaño. Por otro lado, las sierras de cinta verticales ayudan a realizar cortes más complejos que requieren contornos precisos en la pieza de metal.
Las sierras de cinta tienen la capacidad de crear cortes rectos precisos. También vienen con características avanzadas como rodamientos dobles, ajustes de seguimiento de la hoja y rodillos guiados por la hoja. Estas características garantizan aún más un corte preciso y constante. Las sierras de cinta generan cortes más pequeños que muchos otros procesos de corte, lo que reduce sustancialmente el desperdicio. Por lo tanto, es una excelente opción para reducir los costos de fabricación. Sin embargo, es difícil mantener el contacto requerido entre la superficie de las piezas de trabajo planas y la herramienta de corte. Esto puede causar inestabilidad del material e inconsistencias en el corte.
Técnicas de conformado de chapa metálica
El conformado de chapa metálica implica remodelar los materiales metálicos mientras aún se encuentran en estado sólido. En esta sección se tratarán los procesos de conformado más importantes para chapa metálica. Estos procesos tienen diversas aplicaciones para fabricar piezas fabricadas a medida.
Doblado
El plegado es el proceso que deforma el metal con fuerza y lo dobla en el ángulo deseado para darle la forma requerida. Se lleva a cabo con prensas plegadoras y máquinas laminadoras. Una prensa plegadora utiliza un punzón y una matriz para doblar la chapa metálica. Existen diferentes tipos de máquinas laminadoras y pueden laminar chapa metálica en diversas formas dentro de rangos específicos.
Existen varios métodos de doblado de chapa metálica, y los más comunes incluyen:
- Doblado en V. En este caso, el punzón de doblado proporciona la fuerza necesaria para doblar los materiales metálicos (colocados sobre la matriz en V) en los ángulos deseados. Este método dobla las placas de acero sin cambiar su posición.
- Doblado de rollos. Este método dobla láminas de metal en formas curvas o rollos. Utiliza una prensa plegadora, una prensa hidráulica y tres rodillos para crear la curva deseada. Se prefiere para componentes como tubos, conos y otros materiales con formas huecas.
- Curva en U. Este proceso de doblado es similar al doblado en V. Las únicas diferencias son que se utiliza una matriz en forma de U y los componentes finales tienen forma de U.
- Doblado rotatorio. Este método permite doblar metales en ángulos agudos. Es una excelente opción para doblar ángulos mayores a 90 grados.
- Limpiar la flexión. Se utiliza una matriz de limpieza para determinar el radio interior de la curvatura de la chapa metálica.
En general, la flexión es ideal para metales que son maleables pero no frágiles. Entre ellos se incluyen el acero dulce y el acero para muelles, el aluminio 5052 y el cobre. Los materiales como el aluminio 6061, el latón, el bronce y el titanio son más difíciles de doblar.
El plegado es rentable cuando se utiliza para producciones de bajo a mediano volumen, lo que da como resultado piezas con excelentes propiedades mecánicas. Sin embargo, existe una alta posibilidad de que la recuperación elástica afecte el ángulo de plegado resultante.
Dobladillo
El dobladillo consiste en doblar el borde de una chapa metálica sobre sí misma para crear una zona con dos capas. A menudo se realiza en dos etapas. La primera etapa consiste en doblar la chapa metálica y hacerla llegar hasta el fondo en una matriz en V. La segunda etapa consiste en retirar el material y colocarlo en una matriz de aplanamiento. Este proceso aplana el dobladillo para darle la forma deseada.
El engrapado es eficaz para reforzar los bordes de las piezas y mejorar su aspecto. La precisión del proceso ayuda a obtener componentes con calidades superficiales superiores. Sin embargo, durante este proceso se produce una deformación del material que da lugar a variaciones dimensionales.
Laminación
El laminado de chapa es el proceso en el que una pieza de metal pasa a través de un par de rodillos para reducir el espesor del material o conseguir un espesor uniforme. Los rodillos giran constantemente para crear fuerzas de compresión que deforman plásticamente la pieza de trabajo. Si los rodillos están directamente perpendiculares a la pieza de chapa, se produce el aplanamiento.
Existen dos procesos principales de laminado: el laminado en caliente y el laminado en frío. El laminado en caliente se produce por encima de la temperatura de recristalización del material, mientras que el laminado en frío suele producirse a temperatura ambiente. Las aplicaciones más habituales de las chapas metálicas laminadas son las de tubos y caños, piezas estampadas, discos, ruedas y llantas, etc.
El laminado es un proceso rápido y de alta eficiencia, lo que lo hace adecuado para la producción en masa. El proceso puede diseñarse para crear piezas con tolerancias estrictas y perfiles transversales complejos. Sin embargo, el laminado de metales requiere una inversión inicial elevada, por lo que es más adecuado para la producción en masa.
Estampado
La estampación de chapa metálica es una técnica de conformado en frío que utiliza prensas y matrices de estampación para transformar materias primas en diversas formas. Este proceso es compatible con una amplia gama de materiales de chapa metálica, incluidos acero inoxidable, acero con alto y bajo contenido de carbono, aluminio, latón, cobre, etc.
El estampado puede ser, en general, una combinación de técnicas complejas de corte y conformado para obtener componentes complejos con operaciones más breves. Abarca el plegado, el punzonado, el estampado y el rebordeado para crear una amplia gama de productos.
La estampación de metales es rentable. El proceso es rápido, requiere menos herramientas y menos tiempo de trabajo, y es relativamente barato mantener las matrices de estampación, lo que contribuye a una reducción general de los gastos. La automatización de la estampación de metales también es fácil. Por lo tanto, la programación adecuada de las máquinas de estampación de metales garantizará la entrega constante de piezas de precisión de alta calidad y repetibilidad. Pero la desventaja de la estampación es el aumento del costo de las prensas. Si es necesario alterar el diseño durante la producción, puede resultar difícil cambiar las matrices.
Curling
El rizado de chapa metálica es el proceso de agregar rollos huecos y circulares a los bordes de la chapa metálica. La mayoría de los procesos de rizado se realizan en tres etapas: las dos primeras etapas crean las curvas para el rizo, mientras que la tercera etapa cierra el rizo.
Los rizos ayudan a eliminar los bordes afilados sin tratar de una pieza de trabajo para que sea más segura de manipular. Un borde rizado también le proporciona resistencia. El rizado también puede provocar rebabas y deformaciones del material, por lo que se debe tener cuidado durante el proceso.
Hilado de metales
El hilado consiste en dar forma a los discos de metal para que tengan huecos simétricos de rotación. Durante el proceso, el material se coloca entre el contrapunto de la máquina y un mandril de hilado con forma. Al girar, el rodillo de hilado ayuda a darle a la lámina la forma del mandril.
El hilado de metales es ideal para placas de metal blando, como acero inoxidable, cobre, latón, aluminio, etc. El hilado de metales puede producir varias piezas huecas de diversas formas sin comprometer su calidad. Se pueden incorporar otros procesos de conformado de chapa metálica, como el plegado y el punzonado, en un ciclo de hilado, lo que lo hace muy flexible tanto para la producción en lotes pequeños como para la producción en grandes volúmenes. Las limitaciones de tamaño y forma son la principal desventaja de este proceso. Produce solo piezas con formas concéntricas y simétricas.
Técnicas de soldadura de chapa metálica
La soldadura es un proceso que une dos piezas de chapa metálica mediante calor, presión o ambos. Es un proceso de alta temperatura que funde el metal base, generalmente añadiendo material de relleno.
Existen varias técnicas de soldadura disponibles para la fabricación de chapa metálica, que sirven para unir el metal mediante un proceso de fusión y la adición de un material de relleno. Estas técnicas de soldadura incluyen las siguientes:
- Soldadura con electrodo revestido o soldadura por arco metálico protegido (SMAW). Este proceso de soldadura produce una corriente eléctrica con un electrodo que forma un arco cuando entra en contacto con el metal. El arco eléctrico produce temperaturas superiores a 6300 °F para fundir los metales. Es un proceso adecuado para la soldadura a alta velocidad y puede funcionar tanto con fuentes de alimentación de CA como de CC. Sin embargo, se debe tener cuidado al soldar metales delgados porque las temperaturas superiores que produce este proceso pueden dañar el material.
- Soldadura de metal con gas inerte (MIG). También se conoce como soldadura por arco metálico con gas (GMAW) y funciona con gas de protección y un electrodo de alambre continuo. El electrodo de alambre fundido facilita la unión de las piezas metálicas, mientras que el gas de protección protege el baño de soldadura de la interacción con la atmósfera. La soldadura MIG crea soldaduras de alta calidad con una excelente velocidad de soldadura. También se puede automatizar por completo para evitar salpicaduras de soldadura. Sin embargo, esta técnica de soldadura no es adecuada para metales gruesos ni para soldaduras exteriores.
- Soldadura con gas inerte de tungsteno (TIG). Esta soldadura es un proceso de creación de un arco corto para soldar metales más pesados con un electrodo de tungsteno. También hay un gas de protección inerte para proteger el área de soldadura y el electrodo de la contaminación atmosférica. Una gran ventaja de este proceso de soldadura es que funciona adecuadamente para metales no ferrosos como aluminio, cobre, titanio, etc. Hay un alto grado de control de la soldadura con este proceso, lo que ayuda a crear soldaduras muy limpias y fuertes. Por lo tanto, es un método adecuado para construcciones automotrices y aeroespaciales. Sin embargo, la soldadura TIG requiere un profesional altamente capacitado porque es más desafiante.
Tolerancia en la fabricación de chapa metálica
Las tolerancias de fabricación de chapa metálica se refieren a las desviaciones aceptables de las características de las piezas de chapa metálica necesarias para una instalación e integración precisas y consistentes.
En el caso de las piezas de chapa metálica, se suele utilizar la norma ISO 2768-mk para garantizar un control adecuado de los elementos geométricos y dimensionales. A continuación, se muestran 7 estándares de tolerancia que abarcan dimensiones lineales y angulares, planitud y rectitud, cilindricidad y circularidad.
Tabla 1 – Dimensiones lineales
Desviaciones admisibles en mm para rangos en longitudes nominales | f (bien) | Designación de clase de tolerancia (descripción) | v (muy grueso) | |
m (medio) | c (grueso) | |||
0,5 hasta 3 | ±0,05 | ±0,1 | ±0,2 | – |
Más de 3 hasta 6 | ±0,05 | ±0,1 | ±0,3 | ±0,5 |
Más de 6 hasta 30 | ±0,1 | ±0,2 | ±0,5 | ±1,0 |
Más de 30 hasta 120 | ±0,15 | ±0,3 | ±0,8 | ±1,5 |
Más de 120 hasta 400 | ±0,2 | ±0,5 | ±1,2 | ±2,5 |
Más de 400 hasta 1000 | ±0,3 | ±0,8 | ±2,0 | ±4,0 |
Más de 1000 hasta 2000 | ±0,5 | ±1,2 | ±3,0 | ±6,0 |
Más de 2000 hasta 4000 | – | ±2,0 | ±4,0 | ±8,0 |
Tabla 2 – Radios externos y alturas de chaflán
Desviaciones admisibles en mm para rangos en longitudes nominales | f (bien) | Designación de clase de tolerancia (descripción) | v (muy grueso) | |
m (medio) | c (grueso) | |||
0,5 hasta 3 | ±0,2 | ±0,2 | ±0,4 | ±0,4 |
Más de 3 hasta 6 | ±0,5 | ±0,5 | ±1,0 | ±1,0 |
Más de 6 | ±1,0 | ±1,0 | ±2,0 | ±2,0 |
Tabla 3 – Dimensiones angulares
Desviaciones admisibles en mm para rangos en longitudes nominales | f (bien) | Designación de clase de tolerancia (descripción) | v (muy grueso) | |
m (medio) | c (grueso) | |||
hasta 10 | ±1º | ±1º | ±1º30′ | ±3º |
Más de 10 hasta 50 | ±0º30′ | ±0º30′ | ±1º | ±2º |
Más de 50 hasta 120 | ±0º20′ | ±0º20′ | ±0º30′ | ±1º |
Más de 120 hasta 400 | ±0º10′ | ±0º10′ | ±0º15′ | ±0º30′ |
Más de 400 | ±0º5′ | ±0º5′ | ±0º10′ | ±0º20′ |
Tabla 4 – Rectitud y planitud
Rangos de longitudes nominales en mm | Clase de tolerancia | |||
yo | K | yo | ||
hasta 10 | 0.02 | 0.05 | 0.1 | |
Más de 10 hasta 30 | 0.05 | 0.1 | 0.2 | |
Más de 30 hasta 100 | 0.1 | 0.2 | 0.4 | |
Más de 100 hasta 300 | 0.2 | 0.4 | 0.8 | |
Más de 300 hasta 1000 | 0.3 | 0.6 | 1.2 | |
Más de 1000 hasta 3000 | 0.4 | 0.8 | 1.6 |
Tabla 5 – Perpendicularidad
Rangos de longitudes nominales en mm | Clase de tolerancia | |||
yo | K | yo | ||
hasta 100 | 0.2 | 0.4 | 0.6 | |
Más de 100 hasta 300 | 0.3 | 0.6 | 1.0 | |
Más de 300 hasta 1000 | 0.4 | 0.8 | 1.5 | |
Más de 1000 hasta 3000 | 0.5 | 1.0 | 2.0 |
Tabla 6 – Simetría (posición para la norma ISO G&T, no para ASME o ANSI GD&T)
Rangos de longitudes nominales en mm | Clase de tolerancia | |||
yo | K | yo | ||
hasta 100 | 0.5 | 0.6 | 0.6 | |
Más de 100 hasta 300 | 0.5 | 0.6 | 1.0 | |
Más de 300 hasta 1000 | 0.5 | 0.8 | 1.5 | |
Más de 1000 hasta 3000 | 0.5 | 1.0 | 2.0 |
Aplicaciones de la fabricación de chapa metálica
Ya sea para fines estructurales, elementos decorativos o componentes funcionales dentro de otros productos, muchas industrias diferentes dependen de la fabricación de chapa metálica.
Echemos un vistazo más de cerca a su variedad de casos de uso comunes.
Quioscos, máquinas expendedoras y recintos
Las máquinas expendedoras y los quioscos generan ingresos importantes para muchas empresas que atienden a clientes, como por ejemplo gimnasios y centros de ocio. Por eso es necesario tener cuidado en su construcción.
Se necesita una gran cantidad de componentes individuales para construir este tipo de máquinas, por lo que requieren la aplicación de fabricación de chapa metálica.
Construcción y seguridad
Los sectores de la construcción y la seguridad utilizan la aplicación de la fabricación de chapa metálica para productos como puertas de seguridad, barandillas, rejas de seguridad y cerramientos de seguridad a medida.
Minorista
Para crear exhibiciones de productos y productos visuales atractivos en el sector minorista se requiere la fabricación de láminas de metal.
La fabricación de chapa metálica puede ayudar a crear una amplia gama de unidades de exhibición minorista para diferentes clientes minoristas, espacios minoristas y exhibidores de tiendas. Por ejemplo, exhibidores de barra, cubos de exhibición minorista, exhibidores portátiles y stands para puntos de venta. Estos productos deben ser llamativos y altamente funcionales.
Ciencia, medicina y alimentación
En particular, las industrias científicas, médicas y alimentarias utilizan la fabricación de chapa metálica para crear productos que se encuentran en las cocinas comerciales e industriales, como superficies de trabajo, unidades de almacenamiento y fregaderos.
El acero inoxidable tiende a ser el material elegido para muchas aplicaciones en las industrias de producción y preparación de alimentos.
Transporte
El sector del transporte utiliza miles de productos diferentes fabricados mediante la fabricación de metales. Por ejemplo, los vehículos de emergencia dependen de la fabricación de chapa metálica para la construcción de productos como los compartimentos de las guanteras, los estribos laterales, los soportes de las manillas de las puertas y los marcos de acero para las puertas de las plataformas elevadoras.
La fabricación de chapa metálica es un método excelente para crear piezas grandes y pequeñas que se pueden utilizar en la construcción de vehículos. Además, las barandillas de seguridad en las obras, las trampillas de las escaleras y los productos de seguridad para escaleras se construyen mediante la fabricación de chapa metálica.
Principales tipos de chapa metálica
- Aluminio: Se utiliza para piezas de automóviles, dispositivos eléctricos y utensilios de cocina. Ofrece numerosos beneficios, entre ellos, una buena relación resistencia-peso y una alta conductividad.
- Acero aluminizado: Este metal combina la alta resistencia del acero al carbono con la resistencia superior a la corrosión del aluminio. Las láminas de acero aluminizado se utilizan para productos destinados a entornos de alta temperatura, como los electrodomésticos de cocina.
- Acero carbono: El acero al carbono se utiliza en los mercados industriales y de consumo para una amplia gama de productos. Es una aleación de acero que contiene carbono, lo que hace que el material aumente su dureza y resistencia cuando se somete a un tratamiento térmico.
- Cobre: Algunos ejemplos de productos fabricados con cobre son los lavabos, los techos, las canaletas pluviales y las puertas. El cobre tiene una conductividad eléctrica y térmica mayor que el aluminio, pero puede ser más caro.
- Acero galvanizado: Las láminas de acero galvanizado suelen emplearse para fabricar carrocerías de automóviles, tuberías de agua, vallas, techos y escaleras. Se fabrica recubriendo el acero con zinc mediante un proceso de inmersión en caliente, lo que ayuda a hacerlo más resistente a la corrosión.
- Acero de alta resistencia: Las placas de blindaje militar suelen estar hechas de láminas de acero de alta resistencia. El material se produce mediante la aleación del acero con una variedad de elementos como el carbono, el manganeso y el cobre. Esto ayuda a mejorar su dureza.
- Acero inoxidable: Se utiliza para recipientes de cocina, tanques de almacenamiento de productos químicos y maquinaria de procesamiento de alimentos. El acero inoxidable ofrece una resistencia superior a la corrosión, al fuego y al calor, una relación resistencia-peso y facilidad de fabricación.
- Titanio: Entre los productos típicos fabricados con titanio se encuentran piezas de aviación, equipos médicos y elementos de construcción. Se utiliza principalmente por su alta relación resistencia-peso y su resistencia a la corrosión. Además, es reciclable.
Conclusión
La fabricación de chapa metálica ofrece varias ventajas clave, siendo las tres principales su resistencia, versatilidad y facilidad de mantenimiento. Las piezas de metal creadas a través de varios procesos de chapa Son muy durables y, con el cuidado adecuado, pueden durar muchos años, lo que los hace ideales para proyectos a largo plazo. La versatilidad de la chapa metálica permite que se utilice en una amplia gama de aplicaciones, desde proyectos pequeños hasta grandes, lo que la convierte en un recurso valioso tanto para empresas como para particulares. Además, las fabricaciones de metal son fáciles de mantener, ya que resisten el óxido, la corrosión, el fuego y el calor, lo que hace que los procesos de chapa metálica sean especialmente adecuados para entornos industriales y comerciales.