Tabla de contenido
Desarrollo del corte por láser
El desarrollo de la tecnología de corte por láser ha supuesto un avance significativo en los procesos de fabricación y fabricación. A continuación, se ofrece una breve descripción general de las etapas clave en el desarrollo de corte por láser:
Invención del láser (años 1960): El concepto de láser (amplificación de luz por emisión estimulada de radiación) fue propuesto por primera vez por científicos en la década de 1950, y el primer láser funcional se desarrolló en 1960. Esta invención revolucionaria allanó el camino para numerosas aplicaciones, incluido el corte por láser.
Primeros experimentos (década de 1960 y 1970): En los primeros años de la tecnología láser, los investigadores llevaron a cabo experimentos para explorar sus posibles aplicaciones. Los primeros experimentos de corte por láser implicaban el uso de láseres de CO2 para cortar materiales como metales, plásticos y telas.
Adopción industrial (década de 1980): En la década de 1980, los avances en la tecnología láser llevaron a la comercialización de sistemas de corte por láser para aplicaciones industriales. Los láseres de CO2 surgieron como la opción preferida para el corte láser industrial debido a su capacidad para cortar una amplia gama de materiales con alta precisión y eficiencia.
Avances en la tecnología láser (década de 1990-2000): Durante las décadas de 1990 y 2000, se produjeron avances significativos en la tecnología láser, lo que dio lugar a mejoras en la velocidad de corte, la precisión y la versatilidad. Los láseres de fibra, que utilizan fibras ópticas para generar rayos láser, surgieron como una alternativa a los láseres de CO2, ofreciendo ventajas como velocidades de corte más altas y menores costos operativos.
Integración de tecnología CNC: La integración de la tecnología de control numérico computarizado (CNC) con los sistemas de corte por láser revolucionó la industria. Los controladores CNC permitieron un control preciso del proceso de corte, lo que permitió cortar formas y diseños complejos con facilidad.
Diversificación de aplicaciones: A medida que la tecnología de corte por láser fue madurando, sus aplicaciones se diversificaron en diversas industrias, incluidas la automotriz, la aeroespacial, la electrónica, los dispositivos médicos y el diseño arquitectónico. El corte por láser se convirtió en el método preferido para cortar patrones, contornos y prototipos intrincados en estas industrias.
Avances en automatización y robótica: En los últimos años, ha habido una tendencia hacia la automatización e integración de la robótica en los sistemas de corte por láser. La manipulación automatizada de materiales, la clasificación de piezas y la carga y descarga robótica han mejorado aún más la productividad y la eficiencia en las operaciones de corte por láser.
Tendencias emergentes: De cara al futuro, los esfuerzos de investigación y desarrollo en curso siguen impulsando la innovación en la tecnología de corte por láser. Las tendencias emergentes incluyen el desarrollo de sistemas de corte por láser híbridos, la fabricación aditiva mediante deposición láser y los avances en fuentes láser y ópticas para un mejor rendimiento de corte.
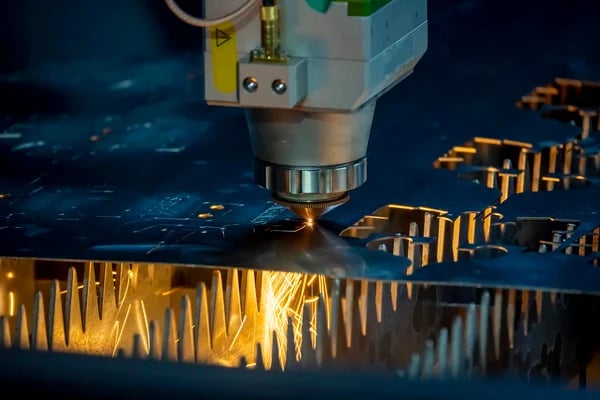
¿Qué es el corte por láser y cómo funciona?
Corte por láser Utiliza un láser de alta potencia que se dirige a través de un sistema óptico y un control numérico por computadora (CNC) para dirigir el haz o el material. Normalmente, el proceso utiliza un sistema de control de movimiento para seguir un código CNC o G del patrón que se va a cortar en el material. El haz láser enfocado quema, funde, vaporiza o es expulsado por un chorro de gas para dejar un borde con un acabado superficial de alta calidad.
El haz láser se crea estimulando materiales láser mediante descargas eléctricas o lámparas dentro de un recipiente cerrado. El material láser se amplifica al ser reflejado internamente a través de un espejo parcial hasta que su energía es suficiente para que escape como un haz de luz monocromática coherente. Esta luz se enfoca en el área de trabajo mediante espejos o fibras ópticas que dirigen el haz a través de una lente que lo intensifica.
En su punto más estrecho, un rayo láser suele tener menos de 0,0125 pulgadas (0,32 mm) de diámetro, pero son posibles anchos de corte tan pequeños como 0,004 pulgadas (0,10 mm) dependiendo del espesor del material.
Cuando el proceso de corte por láser debe comenzar en cualquier lugar que no sea el borde del material, se utiliza un proceso de perforación, mediante el cual un láser pulsado de alta potencia hace un orificio en el material, por ejemplo, tardando entre 5 y 15 segundos en quemar una lámina de acero inoxidable de 0,5 pulgadas de espesor (13 mm).
El corte por láser utiliza un láser de alta potencia que se dirige a través de un sistema óptico y un control numérico computarizado (CNC) para dirigir el haz o el material. Normalmente, el proceso utiliza un sistema de control de movimiento para seguir un código CNC o G del patrón que se va a cortar en el material. El haz láser enfocado quema, funde, vaporiza o es expulsado por un chorro de gas para dejar un borde con un acabado superficial de alta calidad.
El haz láser se crea estimulando materiales láser mediante descargas eléctricas o lámparas dentro de un recipiente cerrado. El material láser se amplifica al ser reflejado internamente a través de un espejo parcial hasta que su energía es suficiente para que escape como un haz de luz monocromática coherente. Esta luz se enfoca en el área de trabajo mediante espejos o fibras ópticas que dirigen el haz a través de una lente que lo intensifica.
En su punto más estrecho, un rayo láser suele tener menos de 0,0125 pulgadas (0,32 mm) de diámetro, pero son posibles anchos de corte tan pequeños como 0,004 pulgadas (0,10 mm) dependiendo del espesor del material.
Cuando el proceso de corte por láser debe comenzar en cualquier lugar que no sea el borde del material, se utiliza un proceso de perforación, mediante el cual un láser pulsado de alta potencia hace un orificio en el material, por ejemplo, tardando entre 5 y 15 segundos en quemar una lámina de acero inoxidable de 0,5 pulgadas de espesor (13 mm).
Tipo de corte por láser
Este proceso se puede dividir en tres técnicas principales: láser de CO2 (para cortar, taladrar y grabar) y láser de neodimio (Nd) y neodimio itrio-aluminio-granate (Nd:YAG), que son idénticos en estilo, utilizándose el Nd para taladrado de alta energía y baja repetición, y el Nd:YAG para taladrado y grabado de muy alta potencia.
Se pueden utilizar todo tipo de láseres para soldar.
Los láseres de CO2 implican el paso de una corriente a través de una mezcla de gases (excitación por corriente continua) o, más popularmente en la actualidad, el uso de la técnica más nueva de energía de radiofrecuencia (excitación por radiofrecuencia). El método de radiofrecuencia tiene electrodos externos y, por lo tanto, evita los problemas relacionados con la erosión de los electrodos y el recubrimiento del material de los electrodos en el material de vidrio y los componentes ópticos que pueden ocurrir con la corriente continua, que utiliza un electrodo dentro de la cavidad.
Otro factor que puede afectar el rendimiento del láser es el tipo de flujo de gas. Las variantes comunes del láser de CO2 incluyen el flujo axial rápido, el flujo axial lento, el flujo transversal y el de placa. El flujo axial rápido utiliza una mezcla de dióxido de carbono, helio y nitrógeno que circula a alta velocidad mediante una turbina o un soplador. Los láseres de flujo transversal utilizan un simple soplador para hacer circular la mezcla de gases a una velocidad menor, mientras que los resonadores de placa o difusión utilizan un campo de gas estático que no requiere presurización ni cristalería.
También se utilizan diferentes técnicas para enfriar el generador láser y la óptica externa, según el tamaño y la configuración del sistema. El calor residual se puede transferir directamente al aire, pero normalmente se utiliza un refrigerante. El agua es un refrigerante de uso frecuente, que a menudo circula a través de un sistema de transferencia de calor o de refrigeración.
Un ejemplo de procesamiento láser refrigerado por agua es un sistema de microchorro láser, que combina un haz de láser pulsado con un chorro de agua a baja presión para guiar el haz de la misma manera que una fibra óptica. El agua también ofrece la ventaja de eliminar los residuos y enfriar el material, mientras que otras ventajas sobre el corte láser "seco" incluyen altas velocidades de corte, corte paralelo y corte omnidireccional.
Los láseres de fibra también están ganando popularidad en la industria del corte de metales. Esta tecnología utiliza un medio de amplificación sólido en lugar de un líquido o un gas. El láser se amplifica en una fibra de vidrio para producir un tamaño de punto mucho más pequeño que el que se logra con las técnicas de CO2, lo que lo hace ideal para cortar metales reflectantes.
Las ventajas del corte por láser incluyen:
Precisión: El corte por láser ofrece altos niveles de precisión y repetibilidad, lo que lo hace ideal para producir formas intrincadas y complejas con tolerancias estrictas.
Versatilidad: el corte por láser se puede utilizar en una amplia variedad de materiales, incluidos metales, plásticos, madera y más.
Velocidad: El corte por láser es un proceso rápido y eficiente, que permite una producción rápida de piezas y componentes.
Desperdicio mínimo de material: el corte por láser produce cortes estrechos, lo que genera un desperdicio mínimo de material y un mayor uso del mismo.
Bordes limpios: el corte por láser produce bordes limpios y suaves sin necesidad de procesos de acabado secundarios.
Corte sin contacto: dado que el rayo láser no toca físicamente el material, existe un riesgo mínimo de daño o deformación de la pieza de trabajo.
Automatización: Los sistemas de corte por láser se pueden integrar fácilmente con la automatización y la robótica para aumentar la productividad y la eficiencia.