Tabla de contenido
Introducción de la cizalla guillotina
El cizalla guillotina Ofrece mayor eficiencia, precisión y confiabilidad en comparación con la cizalla de viga oscilante, ya que elimina el espacio libre en la estructura y permite ajustar el ángulo de cizallamiento.
Sin embargo, al cortar placas anchas y pesadas o placas delgadas de alta resistencia, la cizalla de guillotina puede enfrentar desafíos como la deformación de la máquina que afecta la precisión del corte.
La mayor parte de la investigación en este campo se centra en el impacto de los parámetros de corte en la precisión, el diseño y la automatización del sistema de control o la simulación del proceso de corte utilizando puntos discretos.
Sin embargo, existe una investigación limitada sobre el análisis de las propiedades mecánicas y la optimización de la estructura de tijeras de guillotina.
Este artículo pretende abordar esta brecha mediante el análisis de las características estáticas y dinámicas de la máquina herramienta y la simulación del proceso de corte de placas. A través de este análisis, se obtienen datos de corte continuo y se propone un esquema de optimización.
Análisis estático
En la figura 1 se muestra un modelo estructural de una cizalla guillotina 6 x 3200 NC. Durante el funcionamiento, el dispositivo de tope, accionado por el tornillo de rodillo, ajusta la longitud de corte. A continuación, el cilindro de presión es comprimido por la placa de corte.
Una vez que se establecen los parámetros de corte, como la distancia entre la cuchilla y el ángulo de corte, los cilindros hidráulicos en ambos extremos impulsan las cuchillas superior e inferior para moverlas y completar el proceso de corte de la placa.
En el análisis de simulación, se descartan el filete de transición y el orificio roscado, y se importa un modelo tridimensional simplificado en un software de análisis de elementos finitos. Los dos lados del soporte de la herramienta superior se fijan con restricciones y se establece un contacto de unión para simular la soldadura y la fijación de la rosca de las piezas del soporte de la herramienta superior.
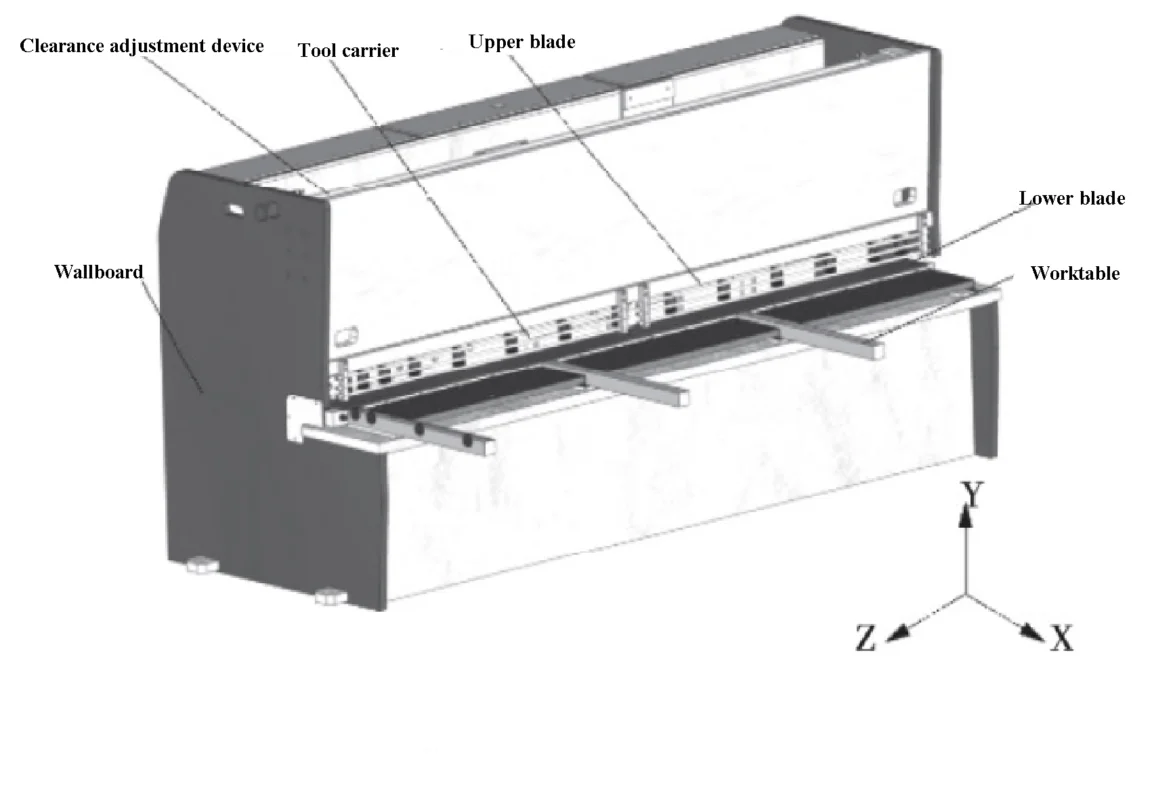
Según la fórmula de Norsali:
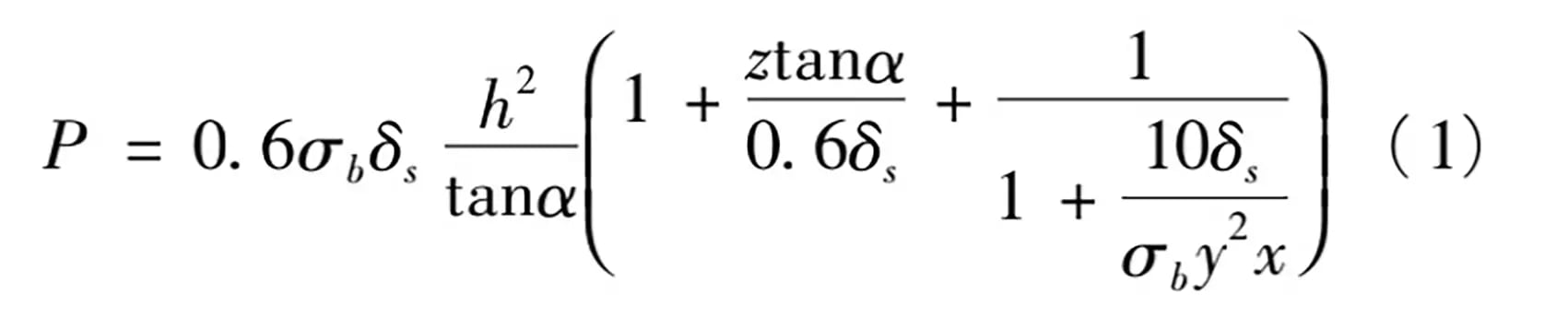
En la fórmula:
σb – Límite de resistencia de la placa a cortar;
δs – Ductilidad de la chapa a cortar;
h – Espesor de la chapa a cortar;
α – Ángulo de corte;
x、y、z – El coeficiente de fuerza de flexión, el valor relativo de la holgura lateral del filo de corte y el coeficiente de presión.
La fuerza de corte vertical (P1) se calcula en 212,8 kN utilizando la fórmula (1), mientras que la fuerza de corte horizontal (P2) se estima en 30% de la fuerza de corte vertical, o 63,8 kN. Tanto la fuerza de corte vertical como la horizontal se aplican a la torreta superior y se resuelven utilizando ANSYS Workbench.
Se compara y analiza la deformación en cada dirección al inicio, a la mitad y al final del corte. Como se ve en la Tabla 1, la deformación del carro superior en la dirección Y es la mayor, y la deformación en las direcciones X y Z puede considerarse insignificante en comparación.
Las posiciones inicial y final de la deformación en la dirección Y son aproximadamente iguales y mucho menores que la posición media. Durante el proceso de corte, la deformación del portaherramientas superior muestra una tendencia cóncava.
Tabla 1 Esfuerzo equivalente máximo y deformación máxima en direcciones X, Y y Z del portaherramientas superior
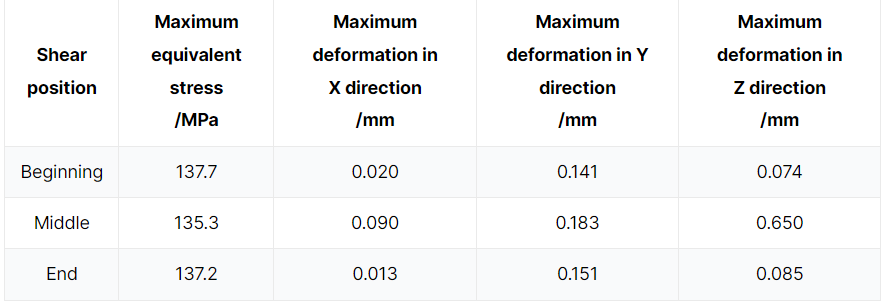
Las figuras 2 y 3 muestran la tensión equivalente máxima en el medio y la deformación máxima en la dirección Y, respectivamente.
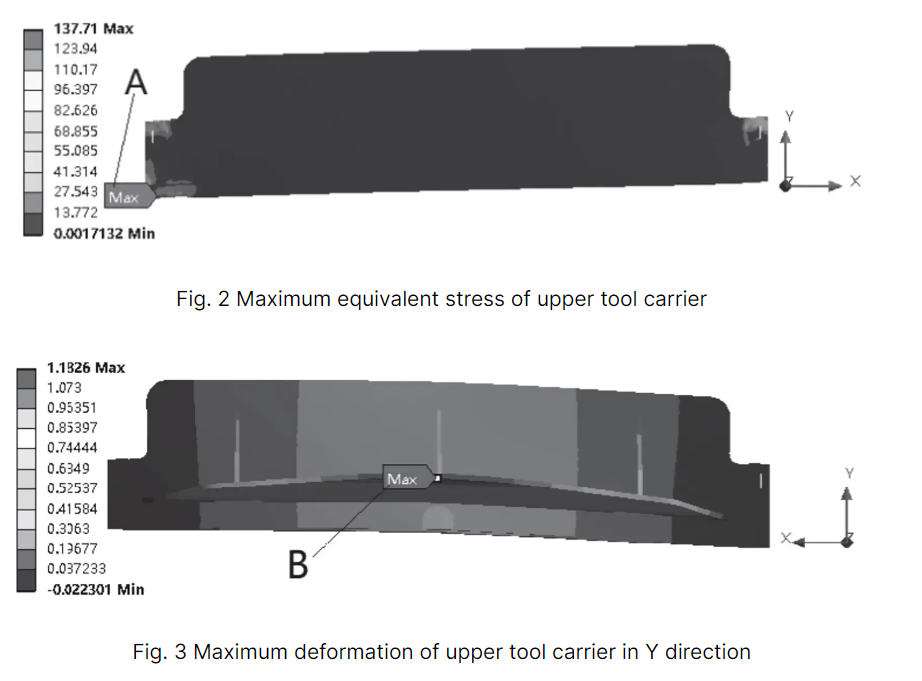
Analizando la Tabla 1 y las Figuras 2 y 3, se puede determinar que la tensión equivalente del portaherramientas superior es la más alta al inicio del proceso de corte. Esta tensión se encuentra en la posición del cilindro hidráulico y tiene un valor de 137,7 MPa, que es inferior a la resistencia a la fluencia de 235 MPa para el portaherramientas superior.
A mitad del proceso de corte, la deformación máxima del portaherramientas superior en la dirección Y se observa en la placa de soporte posterior B, con un tamaño de 1,183 mm. Mientras tanto, la deformación de la cuchilla en la dirección Y es de 0,346 mm, que es inferior a 1 mm y cumple con los requisitos necesarios.
Análisis dinámico transitorio
En la simulación dinámica, se coloca un deslizador en la posición inicial de la cuchilla superior y se lo somete constantemente a la fuerza de corte con una velocidad especificada. El movimiento del deslizador se utiliza para simular el proceso de corte de la placa.
Dado que el deslizador solo transmite fuerza de corte, se ha ajustado para que tenga contacto sin fricción con la cuchilla superior. Durante el corte de la chapa metálica, el contacto entre la cuchilla superior y la chapa metálica que se va a cortar se ilustra en la Figura 4. La longitud de contacto (s) es de 8:1.
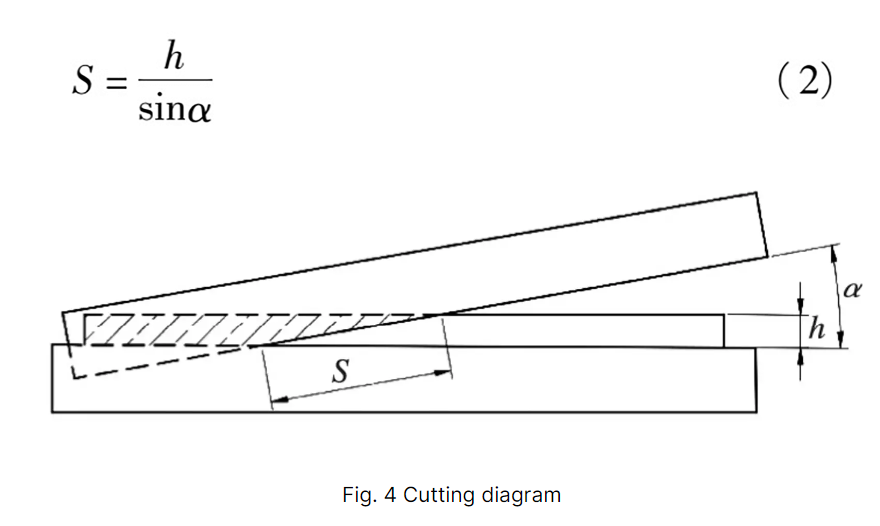
Para simplificar el cálculo, se supone que la fuerza de corte se distribuye uniformemente sobre un área rectangular con la longitud (s) y el ancho (t) de la pala. Como resultado, el deslizador se modela como un cuboide con la misma longitud (s) y ancho (t), como se muestra en la Figura 5.
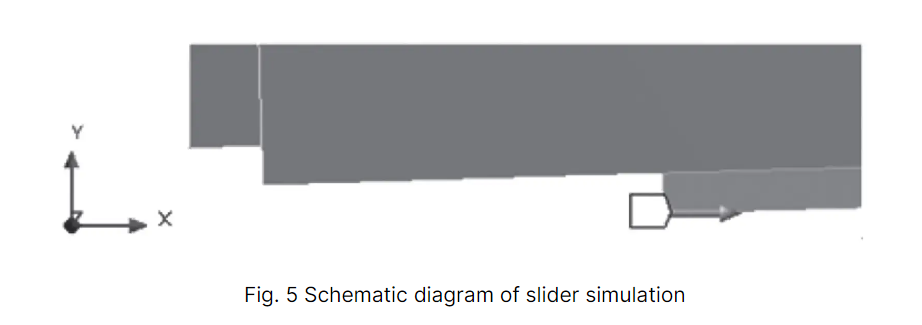
Al resolver la tensión equivalente máxima y la deformación máxima en las direcciones Y y Z en cada posición, los resultados se presentan en la Tabla 2. La tendencia de la deformación y la tensión del portaherramientas superior durante el proceso de corte se muestra en la Figura 6.
Tabla 2. Esfuerzo equivalente máximo y deformación máxima en las direcciones Y y Z del portaherramientas superior bajo cada paso de carga
Paso de carga | Esfuerzo equivalente máximo | Deformación máxima en dirección Y | Deformación máxima en dirección Z |
/MPa | /mm | /mm | |
1 | 138.1 | 0.265 | 0.181 |
2 | 153.2 | 0.38 | 0.33 |
3 | 158.4 | 0.403 | 0.386 |
4 | 159.2 | 0.469 | 0.426 |
5 | 157.5 | 0.592 | 0.463 |
6 | 153.8 | 0.571 | 0.454 |
7 | 148.1 | 0.58 | 0.461 |
8 | 150.3 | 0.635 | 0.478 |
9 | 153.7 | 0.543 | 0.458 |
10 | 154.9 | 0.477 | 0.446 |
11 | 153.2 | 0.482 | 0.425 |
12 | 141.8 | 0.358 | 0.336 |
13 | 136.4 | 0.25 | 0.175 |
Como se observa en la Tabla 2 y la Figura 6, la deformación del portaherramientas superior cambia con el cambio de la posición de corte. La deformación es significativa en el medio y relativamente pequeña y simétrica en ambos lados, en concordancia con los resultados de la simulación estática.
La deformación máxima del portaherramientas superior en las direcciones Y y Z se produce en el paso de carga 8, con valores de 0,635 mm y 0,478 mm, respectivamente, que son inferiores a 1 mm.
La tensión equivalente máxima se encuentra en el paso de carga 4 y tiene un valor de 159,2 MPa, que es inferior al límite elástico de 235 MPa para el portaherramientas superior.
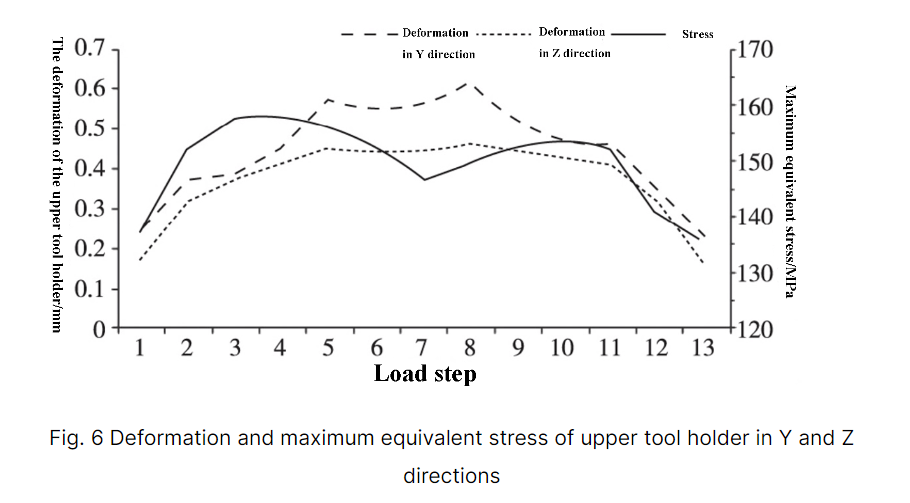
Las figuras 7, 8 y 9 muestran la deformación máxima y la tensión equivalente máxima en las direcciones Y y Z, respectivamente.
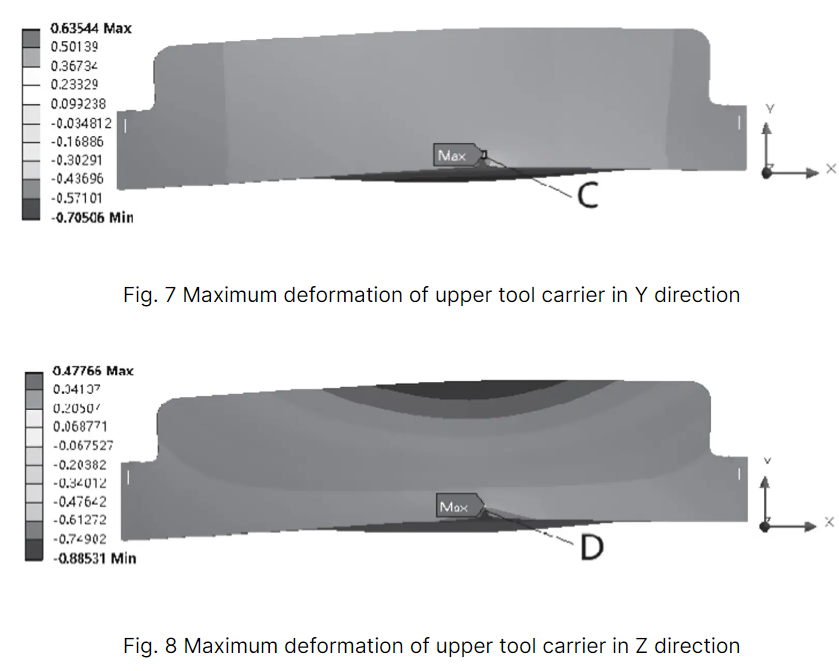
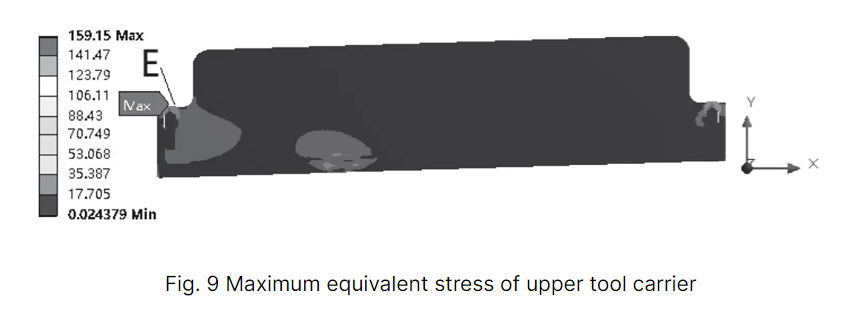
De las Figuras 7, 8 y 9, se puede observar que la máxima deformación del carro superior en la dirección Y ocurre en la pala C, mientras que la máxima deformación en la dirección Z ocurre en la pala D. Ambas deformaciones son menores a 1 mm, cumpliendo con los requerimientos de diseño.
La tensión equivalente máxima se produce en la posición E del portaherramientas superior bajo la influencia del cilindro hidráulico. La tensión sobre la cuchilla es mínima y presenta una buena rigidez.
Análisis modal de cuadros
En el análisis modal, las cuatro bases del marco se fijan y se mantienen en su lugar con restricciones. Se selecciona el método de Lanczos de bloques como método de extracción de modos y el número de modos expandidos se establece en 4 para resolver las primeras cuatro frecuencias naturales de la estructura del marco.
Los cuatro modos de vibración se muestran en la Figura 10, y la Tabla 3 muestra las frecuencias naturales, amplitudes y formas modales de los cuatro modos estructurales de vibración.
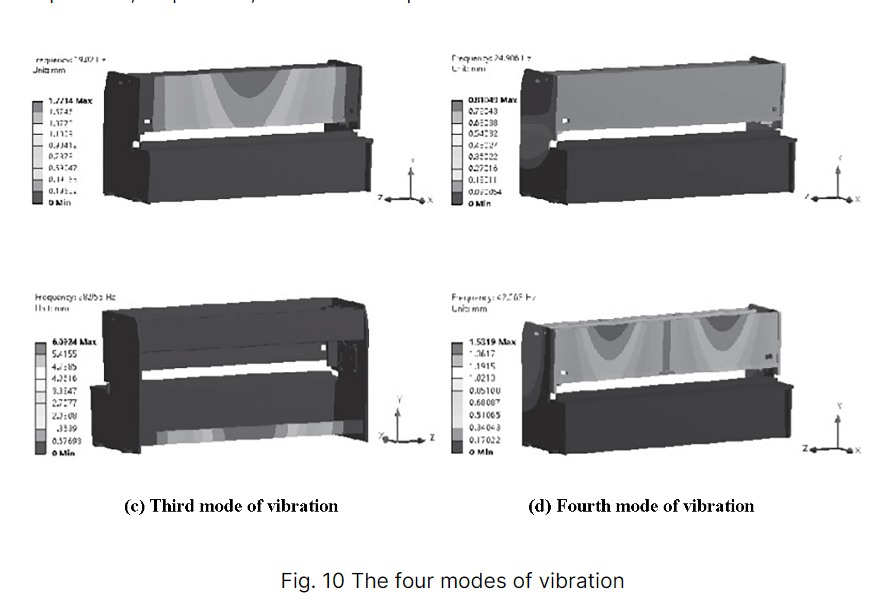
Orden | Frecuencia | Amplitudes | Modo de vibración |
/Hz | /mm | ||
1 | 19.02 | 1.77 | El panel frontal está doblado hacia adelante en la dirección X |
2 | 24.98 | 0.81 | La parte superior del marco se dobla y oscila en dirección Z. |
3 | 28.96 | 6.09 | La viga de soporte inferior se dobla hacia adelante a lo largo de la dirección X. |
4 | 42.66 | 1.53 | El panel frontal está doblado hacia adelante y hacia atrás en dirección X |
De acuerdo con la Figura 10 y la Tabla 3, se puede observar que la deformación por vibración del marco afecta principalmente al panel frontal y a la viga de soporte inferior, lo que provoca vibraciones y ruidos significativos. Cuando la frecuencia es de 19,02 Hz, la amplitud del panel frontal es mayor, lo que podría afectar negativamente al proceso de corte y disminuir su precisión.
Sin embargo, la frecuencia de corte de la cizalla guillotina NC es de 9 veces por minuto, lo que es significativamente menor que la frecuencia natural de primer orden y cumple con los requisitos para el funcionamiento normal.
Es importante minimizar la influencia de fuentes de vibración externas durante el proceso de trabajo para evitar una deformación excesiva por vibración.
Diseño de optimización
El análisis de las características estáticas y dinámicas del proceso de cizallamiento revela que la deformación de la torreta superior presenta una tendencia cóncava durante el cizallamiento, lo que puede afectar la precisión dimensional y de rebabas del troquelado y reducir la calidad general del cizallamiento.
Para mejorar la calidad de corte, se puede ajustar la holgura de la cuchilla en los parámetros de corte para aumentar la rigidez de posicionamiento del portaherramientas superior. En este artículo, se ha diseñado un dispositivo de ajuste de la holgura de la cuchilla de tipo guía de bisel dinámico, como se muestra en la Figura 11.
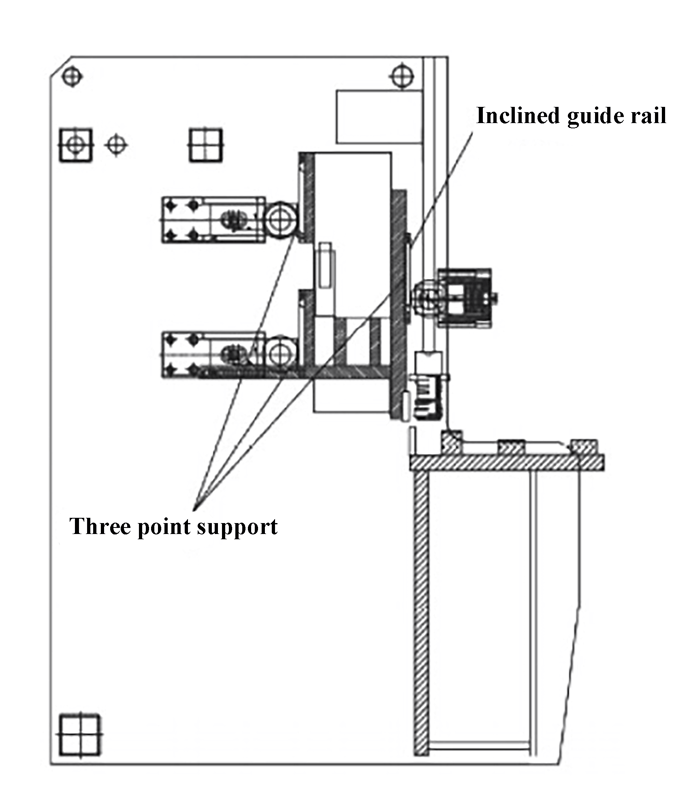
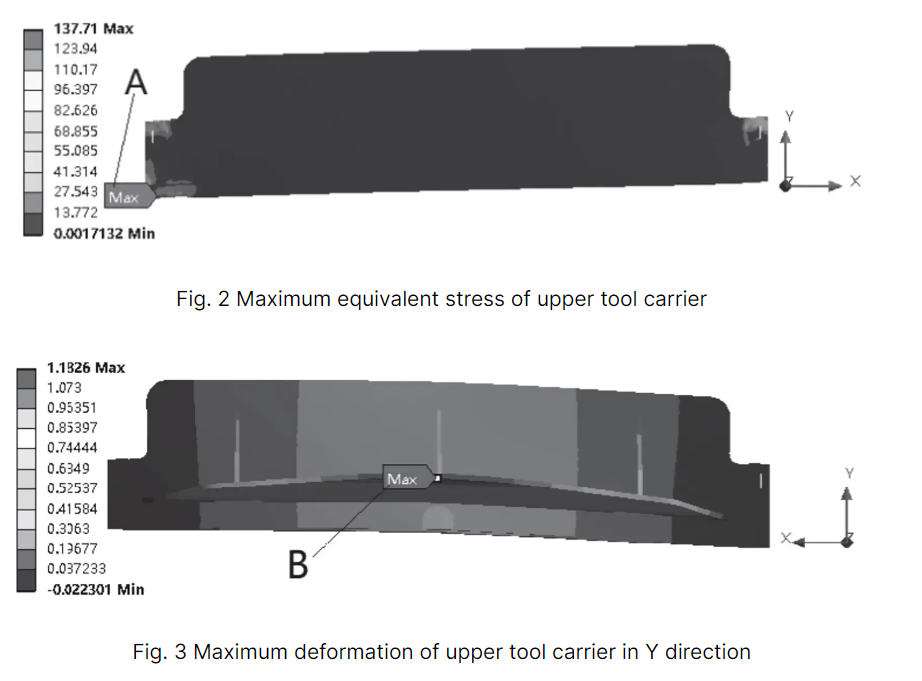