Desde el máquina laminadora de placas Sufre un estrés importante durante su funcionamiento y es propenso a sufrir varios fallos durante su uso. En la siguiente sección, analizaremos dos fallos comunes y sus respectivas soluciones.
Fractura y reparación del eje principal de la máquina laminadora de placas
Un 50×3000 máquina laminadora de placas En una fábrica de maquinaria se observaron grietas en el eje principal después de un año de uso. Al realizar una detección de fallas por ultrasonidos, se descubrió que la estructura del eje principal estaba dividida en dos partes: una sección forjada y una sección fundida, que no cumplían con el estándar nacional para la detección de fallas de Clase II.
Para determinar la causa del daño con mayor precisión, el personal de mantenimiento diseccionó el eje principal y descubrió que los resultados de la detección eran precisos. Después de su análisis, se concluyó que la causa principal de la fractura del eje principal fue una soldadura deficiente. El área de soldadura era pequeña, el proceso era áspero y había inclusiones de escoria de soldadura, lo que provocó defectos de baja resistencia.
1.1 Esquema de reparación.
En función de las condiciones de tensión del eje principal, se utilizó una técnica de soldadura a tope. Para lograrlo, se realizaron dos ranuras en forma de U en el lugar de la soldadura y se mecanizaron un hoyo y un saliente respectivamente en el centro del eje roto, con una tolerancia de ajuste de H7/H7.
Para garantizar la coaxialidad de la soldadura, se diseñaron un bloque de dimensionamiento en forma de V y un anillo de diámetro igual como parte de la configuración.
1.2 Materiales y métodos de soldadura.
Durante la inspección del material del eje principal con un equipo de inspección, se descubrió que está hecho de acero n.° 45. Sin embargo, este acero tiene un rendimiento de soldadura deficiente, lo que genera numerosos desafíos durante la soldadura.
Además, debido al gran diámetro del eje principal, es necesario precalentarlo antes de soldar. La máquina de soldar utilizada es la máquina de soldar con protección de gas de dióxido de carbono XC500. El alambre de soldadura utilizado es ER50-6 con un diámetro de 1,2 mm.
Durante el proceso de soldadura, el voltaje se mantiene alrededor de 35 V, la corriente varía de 220 a 250 A y la velocidad está entre 15 y 25 cm/min.
Para garantizar la penetración completa en el eje principal, se debe reducir la velocidad durante la fase inicial de soldadura y se debe emplear el método de transporte de la tira en línea recta. A medida que aumenta el ancho de la ranura, el movimiento de soldadura se debe cambiar a una forma de dientes de sierra para minimizar la deformación.
Además, la soldadura debe ser realizada por dos personas simultáneamente, alternando entre una rotación hacia arriba y hacia abajo.
1.3 Soldadura.
Antes de soldar, se deben realizar algunos pasos de pretratamiento.
En primer lugar, se debe desmontar el eje principal y realizar determinados procesos de mecanizado, como perforaciones y ranuras, en el eje principal, tal como se especifica en los planos. También se deben probar los dos ejes rotos para comprobar que el montaje es correcto.
Para evitar el impacto de la escoria de soldadura en el conjunto, se debe limpiar el área cercana a la soldadura con un removedor de escoria para eliminar cualquier escoria residual generada durante el mecanizado.
A continuación, los ejes rotos se colocan en la máquina perforadora T20 y se alinean utilizando un bloque de dimensionamiento en forma de V para ajustar la diferencia de altura horizontal. A continuación, los dos ejes se conectan utilizando un rodillo y se verifica la coaxialidad utilizando una regla de corte. Se realizan ajustes finos utilizando una lámina fina de cobre para garantizar que el error de coaxialidad no supere los 0,05 mm.
Por último, se utilizan ángulos para reforzar los cuatro extremos.
Para reducir la deformación del eje principal durante la soldadura, se utiliza el método de dos personas soldando simultáneamente. El rodillo instalado en el eje principal se suelda simétricamente en cuatro posiciones, arriba, abajo, izquierda y derecha, y la longitud de soldadura aumenta gradualmente.
Después de cada sesión de soldadura, la escoria de soldadura debe eliminarse rápidamente y cualquier tensión de soldadura debe aliviarse golpeando la soldadura.
Para asegurar la coaxialidad, se debe detener la soldadura cuando se alcanzan 3/5 de la profundidad de la ranura y se debe verificar la desviación de la coaxialidad para determinar la dirección de la siguiente curva. El husillo se puede enderezar aumentando adecuadamente la longitud del arco de soldadura y la corriente.
1.4 Efecto.
Las estadísticas indican que después de esta reparación del husillo, no ha habido grietas en el husillo durante los últimos tres años.
Todo el proceso de reparación con soldadura llevó cuatro días y requirió 15 kg de varilla de soldadura. El costo total de la reparación, incluidos los gastos de mecanizado y material, fue de 5788 yuanes.
Si se tuviera que comprar un husillo nuevo, costaría 220.000 yuanes y tardaría 35 días en transportarlo e instalarlo.
En comparación, la reparación del husillo no solo ahorra costes, sino que también reduce el tiempo necesario y aumenta la eficiencia.
Reparación de avería de motor de máquina laminadora de placas
Una máquina dobladora de placas de presión de tres rodillos Em040-160, fabricada en Italia, dejó de funcionar repentinamente durante el funcionamiento.
Tras la inspección, se encontró que la señal eléctrica era normal y se determinó inicialmente que se trataba de un problema mecánico.
El trabajador de mantenimiento primero quitó el motor de la cola del rodillo superior y giró manualmente el eje de entrada de la caja de reducción del rodillo superior para confirmar que la caja de reducción funcionaba correctamente.
Al desmontar el motor, se descubrió que la placa de cubierta móvil en la cara final de la placa de distribución de aceite en el lado de entrada de aceite del motor estaba rota, y el anillo de sellado debajo de la placa de cubierta también estaba dañado. Los residuos del daño habían ingresado al émbolo, lo que provocó que el aceite se canalizara tanto dentro como fuera de la placa de distribución de aceite, lo que impidió la generación de presión de trabajo.
El motor hidráulico utilizado en esta máquina dobladora es un motor de pistón radial de cinco estrellas S7b3000 o de marca Sai importado. Comprar piezas de motor nuevas al fabricante sería una tarea costosa y llevaría mucho tiempo.
Por lo tanto, el departamento de mantenimiento de equipos decidió reparar el motor internamente, en función de la tarea de producción y el progreso de la fábrica.
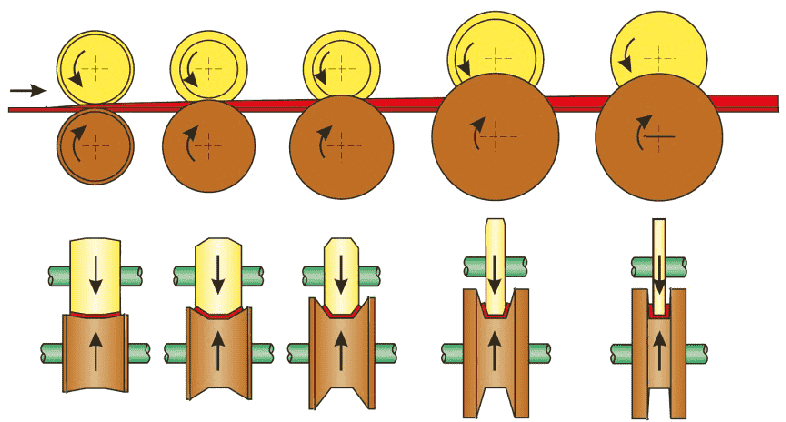
Se mecanizó una nueva placa de cubierta móvil del tamaño de la placa de distribución de aceite y se obtuvo un anillo de sellado a partir de un agente sellador de aceite. Los sellos originales eran una junta tórica y un anillo de ranura circular.
Sin embargo, el agente solo tenía juntas tóricas y anillos planos, mientras que los tamaños originales eran 2,5 y 1,9 mm, y los tamaños disponibles eran 2,5 y 1,4 mm, que no eran adecuados para su uso.
Como solución, se utilizó un anillo de retención de 3 mm en lugar del anillo de retención de 1,9 mm. Dado que la ranura del sello de aceite de la placa de distribución de aceite tenía 3,6 mm de profundidad y 3,2 mm de ancho, la junta tórica de 3,0 tenía un pequeño espacio en la ranura para la compresión y el anillo de retención del plano 1,4 se podía colocar de forma segura en la ranura.
Se montó el motor y se reinició la máquina, permitiendo que el rodillo superior girara libremente. Después de estar en funcionamiento durante un mes, el motor seguía funcionando normalmente.