Seleccionar el prensa plegadora Y el utillaje para un trabajo específico implica mucho más que simplemente asegurar la fuerza bruta. Un error de cálculo puede hacer que salgan piezas del utillaje volando, a la vez que se excede la carga central del carnero, lo que provoca la deformación del carnero y la bancada de la prensa plegadora. Si no lo cree, observe casi cualquier prensa plegadora mecánica de alto kilometraje y cuente el número de calzas entre la matriz y la bancada.
Para evitar estos problemas, revise sus límites de tonelaje y carga.
¿Cuánto tonelaje requiere un trabajo?
Comience por consultar una tabla de tonelaje estándar que relaciona el espesor de la pieza con el ancho de la abertura de la matriz. La intersección de ambos valores le indica el tonelaje aproximado por pie requerido para el trabajo, basado en acero laminado en frío de 60,000 PSI.
Sin embargo, las tablas de tonelaje pueden ser imprecisas. Por lo tanto, para determinar el tonelaje requerido por un trabajo de forma rápida y precisa en cada ocasión, considere usar la siguiente fórmula, que calcula el tonelaje por pulgada al conformar con aire acero laminado en frío AISI 1035 con resistencia a la tracción de 60,000 PSI sobre un ancho de matriz determinado:
Tonelaje por pulgada = {[(575 × Espesor del material2) / Ancho de la matriz] / 12}.
Comience por consultar una tabla de tonelaje estándar que relaciona el espesor de la pieza con el ancho de la abertura de la matriz. La intersección de ambos valores le indica el tonelaje aproximado por pie requerido para el trabajo, basado en acero laminado en frío de 60,000 PSI.
Sin embargo, las tablas de tonelaje pueden ser imprecisas. Por lo tanto, para determinar el tonelaje requerido por un trabajo de forma rápida y precisa en cada ocasión, considere usar la siguiente fórmula, que calcula el tonelaje por pulgada al conformar con aire acero laminado en frío AISI 1035 con resistencia a la tracción de 60,000 PSI sobre un ancho de matriz determinado:
Tonelaje por pulgada = {[(575 × Espesor del material2) / Ancho de la matriz] / 12}.
Multiplique este valor por la longitud de la curva y obtendrá el tonelaje total requerido para la aplicación.
Aun así, en cualquier taller, los tipos de materiales varían, y cada uno tiene su propia resistencia a la tracción. La resistencia a la tracción se define como la capacidad de un material para soportar peso sin romperse ni desgarrarse bajo una carga uniforme, no bajo un impacto repentino.
Para incorporar diferentes materiales al cálculo del tonelaje, se incluye un factor de material en la fórmula de tonelaje. A continuación, se presentan algunos factores de material comunes:
Acero laminado en frío AISI 1035 = 1
Acero inoxidable 304 = 1,4 a 6
Aluminio 6061 T6 = 1,28
Aluminio 5052 H32 = 0,50
Utilizamos el acero AISI 1035 de 60 000 PSI (el tipo de acero laminado en frío más común) como referencia, por lo que le asignamos un valor de 1. Para obtener un factor para un material específico, puede realizar una comparación simple de resistencias a la tracción, utilizando una resistencia a la tracción de 60 000 PSI como referencia. Por ejemplo, si trabaja con un material con una resistencia a la tracción máxima especificada de 120 000 PSI, divida ese valor entre 60 000 para obtener 2, que se convierte en el factor de material en la fórmula de tonelaje.
Considerando todo esto, aquí está el cálculo de tonelaje que puedes utilizar para determinar la cantidad de tonelaje que necesitas para un trabajo:
Tonelaje por pulgada = {[(575 × Espesor del material al cuadrado) / Ancho de la matriz] / 12} × Factor del material
Tonelaje total necesario para el trabajo = Toneladas por pulgada × Longitud de la curva en pulgadas
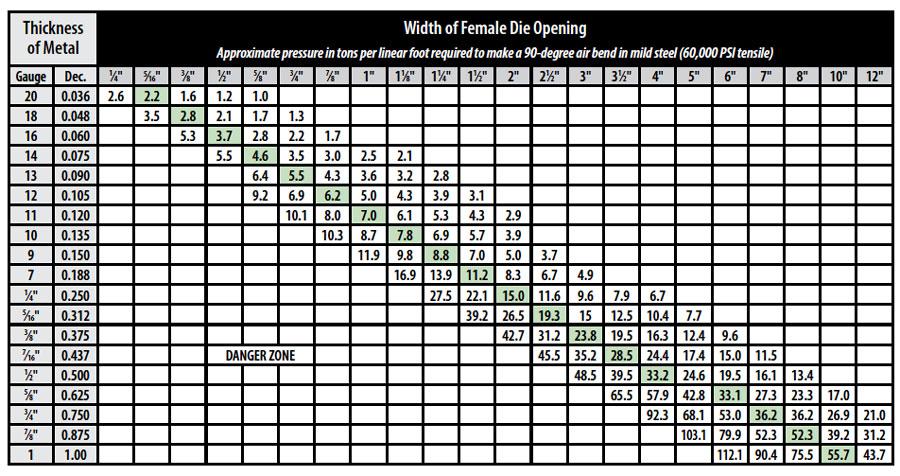
Estas fórmulas se aplican al conformado por aire. Si se realiza el doblado por fondo o acuñado, es necesario tener esto en cuenta. Los cálculos de tonelaje para doblado por fondo y acuñado son, en el mejor de los casos, aproximaciones aproximadas, ya que pueden variar según el operador de la máquina. Sin embargo, estos métodos de doblado aumentan considerablemente el tonelaje requerido. Si se realiza el doblado por fondo, se debe multiplicar el tonelaje por pulgada calculado por al menos un factor de 5; si se realiza el doblado por acuñado, el factor puede ser de 10 o incluso más.
Tenga en cuenta también que el tonelaje máximo no se alcanza de golpe, sino que se acumula a lo largo de una curva pronunciada. Si observa detenidamente, notará que el 80 % del tonelaje total se desarrolla en los primeros 20 grados de curvatura, por lo que incluso un ángulo de curvatura pequeño puede generar enormes presiones sobre las herramientas y el equipo.
También hay que considerar más tonelaje que el necesario para doblar la chapa. El tamaño de la pieza también puede afectar los requisitos de tonelaje. Al trabajar con una pieza pequeña, esta fuerza es extremadamente pequeña. Sin embargo, para piezas más grandes, la fuerza puede ser significativa. El soporte del material, ya sea con mucha mano de obra, elevadores de material en la plegadora o una grúa, puede ayudar a mitigar este efecto.
Tanto si utiliza una tabla de tonelaje como si calcula manualmente los requisitos de tonelaje, necesita saber cómo aplicar la información. Los requisitos de tonelaje del trabajo no deben superar la capacidad de la prensa plegadora ni de las herramientas.
Capacidad de tonelaje de la prensa plegadora
Antes de continuar, es necesario definir algunos términos, el primero de los cuales es la deflexión. La deflexión es la deformación temporal del carnero y la bancada de la prensa plegadora que se produce naturalmente bajo una carga. Al retirarse la presión, también se produce la deflexión bajo carga, y el carnero y la bancada vuelven a sus posiciones originales. En otras palabras, la deflexión es normal y previsible.
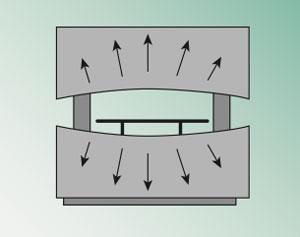
El segundo término es el recalcado, que se produce cuando se excede la deflexión máxima del carnero de la plegadora. Cuando esto ocurre, el carnero y la bancada quedan permanentemente deformados; una vez recalcados, la reparación del carnero y la bancada se vuelve difícil y costosa.
La mayoría de las prensas plegadoras están diseñadas para carga central; es decir, para trabajar en el centro de la bancada. La potencia del pistón proviene de los cilindros a ambos lados de la bancada, mientras que la fuerza de plegado se concentra en el centro.
La deflexión no siempre está presente. En máquinas que permiten carga descentrada, se puede trabajar directamente debajo de un cilindro hidráulico sin deflexión, pero solo se dispone de la mitad del tonelaje de la prensa plegadora. En ese caso, el límite es el límite de carga de la herramienta o la dureza del pistón y su capacidad para soportar el tonelaje.
Punzón recto estándar
Exceder el tonelaje permitido para la prensa plegadora provocará un vuelco del ariete. El límite de carga depende de cada máquina. Solo el proveedor de la máquina puede indicarle el límite de carga en la línea central de su prensa plegadora; puede ser de 30 o 55 toneladas por pie. Debe consultar esta información con el fabricante de la prensa plegadora.
En general, nunca se debe aplicar la carga completa de la máquina en una longitud de curvatura inferior al 60 % de la distancia entre los marcos laterales. Si, por ejemplo, se tiene una cama de 3 metros de largo entre los marcos laterales, se puede aplicar la carga completa de manera uniforme a longitudes de encofrado de tan solo 1,8 metros o más. Esta regla también debe aplicarse a la mayoría de los sistemas de coronación. Si se utiliza la carga completa en menos del 60 % de la longitud de la cama, la plegadora sufrirá cierto grado de desajuste en la cama y el cilindro.
Supongamos que tiene una prensa plegadora de 250 toneladas con 4,2 m de separación entre los bastidores laterales. Esto significa que, a plena carga, tiene un área de trabajo mínima del 60 % de la longitud de la plataforma (0,60 × 4,2 m), o 2,6 m. Luego, divide 250 toneladas entre 2,6 m, lo que da como resultado 29,76. Tras redondear, el tonelaje máximo por pie bajo carga es de 30 toneladas estadounidenses por pie. (Al realizar los cálculos, asegúrese de que las unidades sean consistentes; 1 tonelada estadounidense equivale a 1,102 toneladas métricas).
Consideraciones sobre el montaje del punzón
Hay tres estilos de punzones y tres montajes diferentes: el americano cepillado con hombros dobles; el europeo rectificado con precisión con un solo hombro; y el New Standard, que se monta directamente sobre el carnero y la presión fluye directamente a través del cabezal de la herramienta y, en algunos casos, a través de los hombros de la matriz.
Preste especial atención a cómo fluye la presión a través de la herramienta al montar el punzón en la prensa plegadora. Las herramientas estándar estadounidenses son reversibles en cuanto al flujo de presión, pero invertir el punzón puede perder su centro, lo que puede causar problemas de conformado. (También se pierde la relación entre el tope trasero y la línea de plegado, pero ese es otro tema).
Las herramientas de estilo europeo son reversibles en cuanto a los centros, pero pueden instalarse incorrectamente. La presión fluye más allá del ariete y llega a los pernos de montaje. Esto crea una situación peligrosa.
Capacidad de tonelaje de las herramientas
Generalmente, los fabricantes publican una lista de las herramientas que producen, indicando el número de referencia y el tonelaje admisible por pie que cada herramienta puede manejar. Al dividir este valor entre 12, se obtiene el tonelaje máximo admisible por pulgada para esa herramienta. Al multiplicar este valor por la longitud total de la curva en pulgadas, se obtiene el tonelaje máximo admisible para esa longitud. Asegúrese de que este valor supere el tonelaje requerido para el trabajo en cuestión.
A lo largo de los años, he escrito muchos artículos sobre cómo desarrollar los requisitos de tonelaje para una situación particular, y siempre sigo la explicación con la afirmación "Nunca exceda el tonelaje máximo permitido especificado por el fabricante", solo para que luego me pregunten: "Mis herramientas no están clasificadas, entonces, ¿cómo sé si estoy usando demasiado tonelaje?".
Es cierto que algunas herramientas de prensa plegadora no están clasificadas para el tonelaje; esto es común con las herramientas cepilladas americanas. La cantidad exacta de tonelaje por pie que una herramienta determinada soportará depende del material, el tratamiento superficial y la geometría de la herramienta. Incluso para los ingenieros más experimentados, esto puede ser una decisión difícil.
Si un punzón recto de al menos 5 cm de ancho no tiene capacidad nominal, el límite de carga de la herramienta puede ser el límite de carga central de una prensa plegadora típica con un límite de 30 toneladas por pie. Esto se debe a que, al utilizar un punzón recto estándar con un cuerpo de al menos 5 cm de ancho, se puede afirmar con seguridad que puede soportar mucho más tonelaje que 30 toneladas por pie. (Por supuesto, esto puede no ser aplicable al utilizar una prensa plegadora con límites de carga más altos).
Un punzón de cuello de cisne con garganta profunda, diseñado para bridas de retorno grandes, soporta un tonelaje significativamente menor por pie que un punzón recto estándar de 2 pulgadas de espesor. Cuanto mayor sea la profundidad de la garganta del punzón de cuello de cisne, menor será su capacidad de tonelaje (ver
Por ejemplo, una profundidad de garganta del 70 por ciento (20 por ciento más allá del centro) produce una caída del 30 por ciento en la capacidad de tonelaje en comparación con la de una herramienta recta, dependiendo del diseño específico de la herramienta.
Por qué son fundamentales los datos de tonelaje
Lo ideal es consultar la información sobre capacidad de tonelaje tanto del fabricante de herramientas como del proveedor de la prensa plegadora. Disponer de estos datos y aprovecharlos al máximo le ayudará a evitar una situación de sobretonelaje potencialmente peligrosa.
Llevar una máquina más allá de sus límites causa estragos en todos los frentes. Un costoso prensa plegadora Podrían sufrir daños irreparables. Las herramientas modernas de prensa plegadora, que alcanzan 75 HRC, pueden explotar bajo presión extrema. Lo peor de todo es que ponen en grave peligro al técnico de la prensa plegadora.