El herramientas para prensa plegadora Es una herramienta que utiliza la máquina dobladora para formar y procesar materiales en láminas. Esta herramienta se compone de varias partes, y los diferentes moldes se componen de diferentes partes. Realiza principalmente el procesamiento de la forma del artículo a través del cambio del estado físico del material formado. Es una herramienta que se utiliza para convertir la pieza en bruto en una pieza con una forma y un tamaño específicos bajo la presión de la máquina dobladora.
Tabla de contenido
La estructura del utillaje de la prensa plegadora
Herramientas para prensa plegadora Se dividen en punzón y matriz, que se utilizan para la estampación de chapa metálica, la formación y la separación de moldes. El molde utilizado para la formación tiene una cavidad y el molde utilizado para la separación tiene un borde cortante.
Selección de materiales
Generalmente se utilizan T8 o T10, T10A y el mejor material 42CrMo, que requiere principalmente alta resistencia, alta tenacidad y buena resistencia al desgaste. El acero para matrices de trabajo en frío Cr12MoV es un buen material. El rendimiento de uso puede ser satisfactorio y el rendimiento del proceso es bueno, el precio será más alto. 42CrMo es un acero templado y revenido de aleación de alta resistencia con alta resistencia y tenacidad y puede trabajar por debajo de los 500 grados.
Condiciones de uso
1. Encienda la máquina dobladora, gire el interruptor de llave, presione la bomba de aceite para iniciar y la bomba de aceite de la máquina dobladora comenzará a girar. En este momento, la máquina aún no ha comenzado a funcionar.
2. El ajuste de la carrera requiere una prueba de funcionamiento cuando se inicia oficialmente el trabajo de doblado con el molde de la máquina dobladora. Cuando la matriz superior de la máquina dobladora desciende hasta el fondo, debe haber un espacio de espesor de placa. De lo contrario, provocará daños en el molde y la máquina. El ajuste de la carrera también tiene un ajuste rápido eléctrico y un ajuste fino manual.
3. Para la selección de la ranura de la matriz de la máquina dobladora, generalmente se selecciona una ranura de 8 veces el ancho del espesor de la placa. Si dobla una placa de 4 mm, debe elegir una ranura de aproximadamente 32.
4. Compruebe la superposición y la firmeza de los moldes superior e inferior de la máquina dobladora; compruebe si cada dispositivo de posicionamiento cumple con los requisitos de procesamiento. Compruebe con frecuencia la superposición de los moldes superior e inferior; si las instrucciones del manómetro cumplen con las normas.
5. Cuando se dobla la lámina, se debe compactar para evitar que se levante y lastime al operador durante el doblado.
6. Se debe cortar el suministro de energía al ajustar la matriz de chapa metálica y se debe detener la operación.
7. Al cambiar la apertura de la matriz inferior de la máquina dobladora variable, no se permite que ningún material entre en contacto con la matriz inferior.
8. Está prohibido utilizar matrices de máquinas dobladoras para doblar placas de hierro de gran espesor o placas de acero endurecido, aceros de aleación de alto grado, aceros cuadrados y láminas que excedan el rendimiento de la máquina dobladora de chapa metálica para evitar daños a la máquina herramienta.
9. Apague la máquina dobladora y coloque bloques de madera en los moldes inferiores debajo de los cilindros a ambos lados para bajar la placa deslizante superior sobre los bloques de madera. Primero salga del programa del sistema de control y luego corte el suministro de energía.
Ajuste de la instalación
Al instalar las herramientas de la prensa plegadora, asegúrese de verificar el estado del equipo, luego instálelo y depúrelo de acuerdo con los pasos y preste atención a la seguridad personal durante la depuración.
Ajuste de la máquina: al instalar las herramientas de la prensa plegadora, primero debe comprender el rendimiento de la máquina, encender la máquina dobladora, ajustarla y verificarla con paciencia, y ver si la máquina ha usado polvo y virutas de hierro anteriormente. Evite problemas innecesarios para un uso posterior.
Ajuste de la carrera del deslizador: Primero verifique si la relación entre el espesor del molde de la máquina dobladora y los módulos superior e inferior es normal. El deslizador general debe controlarse en el punto de conmutación de la línea de carrera. Se debe prestar atención a esto, de lo contrario, el molde no se usará con normalidad, pero algunas personas aún cometen este tipo de errores a menudo.
Ajuste del módulo de carrera: después de ajustar el estándar de carrera del deslizador, el siguiente paso es ajustar el punto límite superior del módulo. En términos generales, cuando el módulo está en el punto más alto, se deben ajustar el módulo y el interruptor. De esta manera, se puede hacer fluir la posición de reposo del módulo y, a través de algunas de las operaciones anteriores, se puede aumentar en gran medida la eficiencia de producción. En este proceso, también es necesario reducir la velocidad del módulo, ya que debe desacelerarse cuando se encuentra en el punto muerto inferior, lo que protege la máquina y el molde.
Ajuste de la distancia: Por último, se ajusta la distancia entre los moldes de la máquina dobladora. Primero se mide la distancia entre el módulo superior y el módulo inferior y se debe determinar la distancia razonable en función de la placa doblada.
Ajuste del ángulo: El ajuste del ángulo de doblado también es el eslabón más importante. La selección del ángulo debe estar relacionada con los requisitos del producto. En términos generales, al doblar un molde de 90°, el ángulo debe ajustarse para que sea mayor que el ángulo entre los dos lados. A veces puede resultar ajustado. Se puede solucionar ajustando los tornillos de la máquina. Después del ajuste, si el producto no cambia la demanda, no lo modifique nuevamente. Luego, al doblar, use el manómetro para calcular el número de presión preciso y ajuste la presión. Para no causar astillas en el molde.
Procedimientos operativos de herramientas para prensas plegadoras
Las herramientas de prensa plegadora se dividen en moldes de máquina dobladora manual, máquinas dobladoras hidráulicas y herramientas de prensa plegadora CNC. Las herramientas de prensa plegadora hidráulica se pueden dividir en sincronización de eje de torsión, sincronización máquina-hidráulica y sincronización electrohidráulica según el método de sincronización. Las herramientas de prensa plegadora hidráulica se pueden dividir en el tipo de movimiento ascendente y el tipo de movimiento descendente según el modo de movimiento. Incluye soporte, banco de trabajo y placa de sujeción. El banco de trabajo se coloca en el soporte. El banco de trabajo se compone de una base y una placa de presión. La base está conectada con la placa de sujeción a través de una bisagra. La base se compone de una carcasa, una bobina y una cubierta, y la bobina se coloca en la carcasa. Dentro del hueco, la parte superior del hueco está cubierta con una placa de cubierta. Preste atención a los siguientes puntos durante la operación:
- Cumplir estrictamente con los procedimientos operativos seguros de los trabajadores de máquinas herramientas y usar el equipo de protección laboral según sea necesario.
- Antes de comenzar, debe verificar cuidadosamente si el motor, el interruptor, el circuito y la conexión a tierra son normales y firmes, y verificar que las partes de control y los botones del equipo estén atascados en la posición correcta.
- Verificar la coincidencia y firmeza de los moldes superior e inferior; verificar si cada dispositivo de posicionamiento cumple con los requisitos de procesamiento.
- Cuando la placa deslizante superior y cada eje de posicionamiento no estén en el origen, ejecute el programa de retorno al origen.
- Una vez que el equipo se haya puesto en marcha, déjelo funcionar en seco durante 1 o 2 minutos y muévalo por completo 2 o 3 veces. Si se produce algún ruido anormal o un mal funcionamiento, deténgalo de inmediato, elimine el problema y deje de trabajar hasta que todo vuelva a la normalidad.
- Durante el trabajo, debe haber una persona al mando, de modo que los operadores y el personal de alimentación y supresión cooperen estrechamente para garantizar que el personal que coopera esté en una posición segura antes de emitir la señal de flexión.
- Cuando se dobla la lámina, se debe compactar para evitar que se levante y lastime a las personas durante el doblado.
- Se debe cortar el suministro de energía al ajustar el molde de prensa de chapa metálica y continuar después de detener la operación.
- Al cambiar la apertura del molde inferior variable, no permita que ningún material entre en contacto con el molde inferior.
- Cuando la máquina herramienta esté en funcionamiento, no se permitirá que nadie permanezca detrás de ella.
- Está estrictamente prohibido doblar la sábana solo por un extremo.
- Si durante el funcionamiento se detectan errores en la pieza de trabajo o el molde, se debe detener y corregir. Está estrictamente prohibido corregirlos con las manos para evitar lesiones en las manos.
- Está prohibido doblar placas de hierro de gran espesor o placas de acero templado, aceros aleados de alto grado, aceros cuadrados y láminas que excedan el rendimiento de la máquina dobladora de chapa para evitar daños a la máquina herramienta.
- Compruebe con frecuencia la superposición de los moldes superior e inferior; si las instrucciones del manómetro cumplen con las regulaciones.
- Detenga inmediatamente la máquina si ocurre alguna anomalía, verifique la causa y elimínela a tiempo.
- Antes de apagar, coloque bloques de madera en los moldes inferiores debajo de los cilindros en ambos lados para bajar la placa deslizante superior sobre los bloques de madera.
- Primero salga del programa del sistema de control y luego corte la fuente de alimentación.
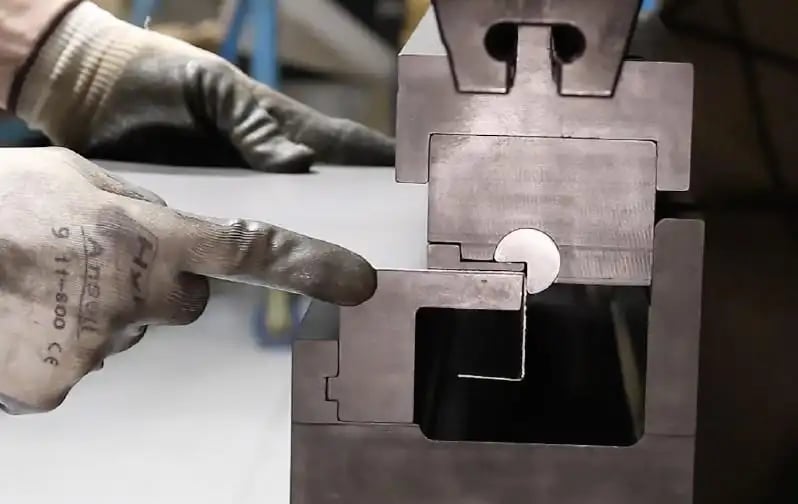
Solicitud
Industria de fabricación de equipos: En el contexto de un suministro de energía global cada vez más limitado y del aumento continuo de los precios del petróleo, la demanda de equipos de generación de energía se ha vuelto cada vez más evidente. En el proceso de fabricación de equipos de generación de energía, el costo que se gasta solo en la parte del molde de la máquina dobladora CNC es muy considerable.
Industria de fabricación de moldes: En el proceso de fabricación de moldes, casi todos los eslabones, como moldes de conformación, moldes de trabajo en caliente, moldes de trabajo en frío y moldes de plástico, necesitan utilizar moldes de máquinas dobladoras CNC. Además, los automóviles, los trenes de alta velocidad, la fabricación de maquinaria en general y la industria de procesamiento de madera, que ha ampliado gradualmente su uso en los últimos años, se han convertido en los principales usuarios de la industria de herramientas para plegadoras CNC.
Industria aeroespacial: En esta industria, las herramientas de prensa plegadora CNC se utilizan generalmente para cortar piezas estructurales de aeronaves. Estas piezas estructurales son generalmente relativamente grandes y, en el pasado, se utilizaban aleaciones de aluminio en grandes cantidades. Con la expansión de los campos de aplicación de las aleaciones de titanio y los materiales compuestos, los requisitos para el procesamiento de moldes de las máquinas dobladoras CNC son cada vez mayores.
Tendencia de desarrollo
Desde la perspectiva del desarrollo de las herramientas de plegado de prensa CNC, desde finales del siglo XIX hasta mediados del siglo XX, el acero de alta velocidad fue el principal representante de los materiales de molde para las máquinas dobladoras CNC; en 1927, Alemania desarrolló y obtuvo por primera vez materiales de herramientas de plegado de prensa CNC de aleación dura. Ampliamente utilizado; en la década de 1950, Suecia y Estados Unidos sintetizaron diamantes sintéticos respectivamente, y los moldes de las máquinas dobladoras CNC de corte han entrado en un período representado por materiales superduros. En la década de 1970, la gente sintetizó diamante policristalino utilizando tecnología de síntesis de alta presión, que resolvió el problema de la escasez y el alto precio de los diamantes naturales y amplió el rango de aplicación de las herramientas de plegado de prensa CNC de diamante a la aviación, aeroespacial, automóviles, electrónica y piedra. Y muchos otros campos.
La elección del material de la matriz para las máquinas dobladoras CNC es la base para el éxito del proceso de corte. En comparación con el carburo cementado, la velocidad de la matriz de la máquina dobladora CNC PCD puede alcanzar los 4000 m/min, mientras que la del carburo cementado es solo 1/4. En términos de vida útil, las herramientas de plegado CNC PCD generalmente se pueden aumentar 20 veces. Desde la perspectiva de la calidad de la superficie procesada, el efecto del PCD es 30%-40% mejor que el del carburo cementado. Además, el desarrollo de herramientas de plegado CNC de material superduro CBN (nitruro de boro vertical) y de herramientas de plegado CNC con revestimiento de superficies también han contribuido al avance de la tecnología de corte.
Herramientas estándar para prensas plegadoras
Herramientas para prensas plegadoras
Las herramientas para prensas plegadoras son un componente esencial de cualquier proceso de fabricación de chapa metálica. Las herramientas para prensas plegadoras estándar se refieren a los punzones y matrices que se utilizan comúnmente en la industria. Estas herramientas están diseñadas para trabajar con las prensas plegadoras para dar forma y formar chapa metálica en varias formas y tamaños. Están disponibles en diferentes tamaños y formas, y cada una está diseñada para una aplicación específica. En este artículo, analizaremos en detalle las herramientas para prensas plegadoras estándar, sus tipos y sus aplicaciones.
herramientas para prensa plegadora
Introducción a las herramientas para prensas plegadoras
El término "herramientas de prensa plegadora" hace referencia al conjunto de punzones y matrices que se utilizan en una máquina plegadora para formar y dar forma a la chapa metálica. La prensa plegadora es una máquina herramienta que se utiliza para doblar y dar forma a la chapa metálica en diversas formas y tamaños. La máquina consta de un sistema hidráulico que aplica fuerza a un punzón, que luego dobla el metal sobre una matriz. La matriz tiene una forma específica que determina la forma final del metal.
Existen dos tipos principales de prensas plegadoras: mecánicas e hidráulicas. Las prensas plegadoras mecánicas utilizan un volante y un embrague para aplicar fuerza al punzón. Las prensas plegadoras hidráulicas, por otro lado, utilizan un sistema hidráulico para aplicar fuerza. Las prensas plegadoras hidráulicas son las más utilizadas en la industria porque proporcionan un control más preciso sobre el proceso de plegado.
Las herramientas de prensa plegadora constan de dos componentes principales: punzones y matrices. El punzón es la parte de la herramienta que aplica fuerza al metal, mientras que la matriz es la parte que le da al metal la forma deseada. El punzón y la matriz están diseñados para trabajar juntos para darle al metal la forma deseada.
Tipos de herramientas para prensas plegadoras
Las herramientas para prensas plegadoras están disponibles en varios tipos, cada uno diseñado para aplicaciones específicas. Los tipos de herramientas para prensas plegadoras más utilizados incluyen:
Troqueles en V
Las matrices en V son el tipo de herramienta para prensas plegadoras más utilizado. Están diseñadas para formar pliegues rectos en chapa metálica. Las matrices en V vienen en diferentes tamaños y ángulos, según el grosor y el tipo de metal que se va a doblar. El ángulo de la matriz en V determina el ángulo de doblado del metal. Los ángulos más comunes para las matrices en V son 60 grados y 90 grados.
Matrices de fondo
Las matrices de corte, también conocidas como matrices rectas, se utilizan para formar ángulos agudos en chapa metálica. Están diseñadas para funcionar con una matriz en V para formar una curva pronunciada en el metal. La matriz de corte se utiliza después de la matriz en V para garantizar que la curva sea precisa y uniforme.
Punzones de cuello de cisne
Los punzones de cuello de cisne se utilizan para formar formas complejas en chapa metálica. Tienen una forma curva que les permite doblar el metal en diferentes direcciones. Los punzones de cuello de cisne se utilizan para aplicaciones que requieren múltiples curvaturas y formas.
Matrices de uretano
Las matrices de uretano se utilizan para dar forma a chapas metálicas sin dejar marcas ni rayones. Están hechas de un material blando que se adapta a la forma del metal que se está doblando. Las matrices de uretano se utilizan para aplicaciones que requieren un acabado de alta calidad.
Matrices de radio
Las matrices de radio se utilizan para formar pliegues curvos en chapa metálica. Vienen en diferentes tamaños y radios, según la aplicación. Las matrices de radio se utilizan para aplicaciones que requieren pliegues curvos, como piezas de automóviles y muebles.
Especificaciones de herramientas para prensas plegadoras estándar
Material: Las herramientas de prensa plegadora generalmente están hechas de acero para herramientas de alto grado o de un acero de aleación especial que puede soportar la alta presión y el desgaste del metal doblado.
Dureza: La dureza de las herramientas de plegado se mide en dureza Rockwell (HRC) y normalmente oscila entre 45 HRC y 65 HRC. Cuanto más dura sea la herramienta, más durará, pero también puede ser más frágil y propensa a agrietarse.
Tipo de herramienta: Existen diferentes tipos de herramientas para prensas plegadoras, entre las que se incluyen matrices en V, punzones y matrices. Las matrices en V se utilizan para crear pliegues en chapa metálica, mientras que los punzones y matrices se utilizan para crear diferentes formas y figuras en el metal.Altura: La altura de las herramientas para prensas plegadoras se mide generalmente en milímetros o pulgadas y se refiere a la distancia desde la parte inferior de la matriz hasta el centro del punzón.
Radio: El radio de las herramientas de plegadora se refiere al tamaño de la curva que se puede crear con ellas. El radio se mide generalmente en milímetros o pulgadas y puede variar según la herramienta específica.
Ángulo: El ángulo de las herramientas de plegadora se refiere al ángulo en el que se monta el punzón. El ángulo puede ser recto o biselado, según la aplicación específica.
Recubrimientos: Algunas herramientas de prensa plegadora pueden estar recubiertas con una capa de carburo de tungsteno u otros materiales para mejorar su resistencia al desgaste y extender su vida útil.
Resumen
Las herramientas para prensas plegadoras son esenciales para lograr pliegues precisos y uniformes en chapa metálica y otros materiales. Al seleccionar los punzones, matrices y accesorios adecuados, los operadores pueden producir una amplia gama de piezas con distintos perfiles de plegado y dimensiones en una máquina plegadora.