El Prensa plegadora con curva en U La técnica de plegado en U es un método clave utilizado en el trabajo de metales, en particular en la fabricación de chapa metálica, donde se emplea una prensa plegadora para crear un pliegue en forma de "U" en una pieza de metal. Este proceso de plegado es crucial para producir piezas con ángulos y configuraciones específicos, que se utilizan a menudo en industrias como la automotriz, la aeroespacial y la construcción. La técnica de plegado en U de la prensa plegadora ofrece precisión y repetibilidad, lo que la convierte en una opción ideal para los fabricantes que buscan crear pliegues de alta calidad de manera eficiente. En esta guía, exploraremos el proceso paso a paso, las herramientas y las mejores prácticas para lograr resultados óptimos utilizando una prensa plegadora para aplicaciones de plegado en U.
¿Cómo entender la curvatura en U de la prensa plegadora?
Conceptos básicos de las prensas plegadoras con plegado en U
El doblado en U con prensa plegadora se refiere a un proceso en el cual la chapa metálica se dobla constantemente en la prensa plegadora dos veces o más para tomar la forma de "U".
Este proceso se logra controlando con precisión los grados de cierre de las matrices y los recorridos superiores e inferiores para cumplir con el tamaño y el ángulo precisos requeridos por el diseño. La curva en U es una de las técnicas de conformado más comunes en las industrias de fabricación de metales.
La curva en U es esencial en diversas industrias, como la fabricación de metales y la ingeniería mecánica. Se utiliza ampliamente en la producción de piezas arquitectónicas y estructurales, piezas de automóviles, carcasas de electrodomésticos y fabricación de diseños que requieren espacio interior, como sistemas de tuberías y armarios eléctricos.
La curva en U no solo puede ahorrar costos de material y mejorar la eficiencia de producción, sino que también garantiza buenas propiedades mecánicas y calidad de apariencia de los productos.
Historia y evolución de la tecnología de las prensas plegadoras
La prensa plegadora se considera un equipo fundamental para el conformado de chapa de precisión y su historia se remonta a los inicios de la industrialización. La prensa plegadora manual inicial dependía de la mano de obra, que presentaba un funcionamiento complejo y una baja eficiencia.
Con el avance de la tecnología, la tecnología hidráulica y CNC mejoran significativamente el desarrollo de la prensa plegadora, haciendo que la máquina sea capaz de realizar plegados precisos y complejos, incluido el plegado en U.
La tecnología de plegado en U se actualiza constantemente con la evolución de la tecnología de las prensas plegadoras, que abarca desde el plegado simple en línea recta hasta el plegado tridimensional. No solo se logra un ángulo de plegado y una precisión aparentes mejorados, sino que también se logra un plegado constante automático en secuencia de varios pasos.
Moderno Prensas plegadoras CNC Incluso se puede integrar con software CAD/CAM, imitando y controlando con precisión el plegado en U general, logrando proyectos de alta precisión y producción en masa. Además, la técnica de troquelado y las herramientas auxiliares, como el tope trasero y el dispositivo de soporte delantero, también enriquecen y mejoran aún más la posibilidad y adaptabilidad del plegado en U.
Aspectos técnicos
Tipos de prensas plegadoras para doblado en U
Prensa plegadora mecánica
Ventajas:estructura simple, rendimiento de alto costo, mantenimiento conveniente, operación intuitiva, adecuado para pequeña escala u ocasiones que requieren menos precisión.
Contras: Probablemente no pueda lograr un control preciso con un gran tonelaje debido a las restricciones de sus vías de movimiento. Además, tiene una menor eficiencia de trabajo que los tipos hidráulicos y no es adecuado para la producción a gran escala y constante.
Prensa plegadora hidráulica
Ventajas: El sistema hidráulico ofrece una presión estable e intensa, que se puede adaptar para doblar con precisión chapas de varios espesores de materiales. También se puede ajustar sin niveles en un rango más amplio, adecuado para la producción en masa y las industrias que requieren alta precisión.
Contras: El equipo es complejo y requiere un mantenimiento regular para su correcto funcionamiento. Sus costos de mantenimiento inicial y posterior son relativamente altos.
Prensas plegadoras CNC
- Ventajas:
- El control programable garantiza alta precisión y repetibilidad.
- Minimiza el desperdicio de material, haciéndolos rentables para la producción a gran escala.
- Ideal para producir componentes detallados, como piezas de chasis de automóviles.
- Desventajas:
- Altos costos de compra y operación debido a la tecnología avanzada.
- Requiere operadores capacitados para programación y mantenimiento.
- No siempre es rentable para producciones de bajo volumen.
Prensas plegadoras eléctricas
- Ventajas:
- Eficiencia energética, lo que se traduce en menores costos operativos a lo largo del tiempo.
- Ofrece una precisión excelente y curvas consistentes.
- Requisitos de mantenimiento reducidos en comparación con los sistemas hidráulicos.
- Desventajas:
- Capacidad limitada para plegado de alto tonelaje, lo que las hace inadecuadas para aplicaciones de trabajo pesado.
- Coste inicial más elevado en comparación con las prensas plegadoras mecánicas.
Prensas plegadoras híbridas
Las prensas plegadoras híbridas combinan la precisión de los sistemas eléctricos con la potencia de los mecanismos hidráulicos. Estas máquinas se utilizan a menudo en aplicaciones que requieren un tonelaje moderado, como la producción de componentes aeroespaciales y automotrices. Equilibran la eficiencia energética y el rendimiento, lo que las convierte en una opción versátil.
- Ventajas:
- Menor consumo energético en comparación con los sistemas hidráulicos tradicionales.
- Capaz de manejar una variedad de espesores de materiales.
- Necesidades de mantenimiento reducidas gracias a la tecnología híbrida.
- Desventajas:
- Una mayor complejidad aumenta la inversión inicial y los costos de capacitación.
- Requiere conocimientos especializados para su operación y mantenimiento.
Cómo seleccionar la máquina dobladora adecuada
Para elegir la prensa plegadora más adecuada es necesario tener en cuenta los requisitos específicos del proyecto, como el tipo de material, el espesor de la chapa, el volumen de producción y el presupuesto. Por ejemplo:
- Las prensas plegadoras hidráulicas son ideales para aplicaciones pesadas como la construcción naval.
- Las prensas plegadoras CNC destacan en industrias de alta precisión como la fabricación de automóviles.
- Las prensas plegadoras eléctricas son las preferidas en operaciones que respetan el medio ambiente. Comprender las ventajas, limitaciones y aplicaciones específicas de cada tipo garantiza una decisión informada y adaptada a las necesidades de producción.
Materiales adecuados para curvas en U
Conocer las propiedades físicas y mecánicas de los diferentes tipos de materiales metálicos es vital para el diseño y la implementación precisos del proceso de doblado en U, lo que es beneficioso para evitar problemas de calidad del producto debido al uso inadecuado de los materiales.
Acero con bajo contenido de carbono:Presenta una buena plasticidad de intensidad moderada, es fácil de doblar y es uno de los materiales más comunes para producir curvas en U.
Acero inoxidable: Es bueno, resistente a la corrosión y decorativo. Requiere un cálculo y control precisos de los parámetros de deformación durante la flexión debido a las propiedades de alta intensidad y recuperación elástica.
Aluminio: Tiene una baja densidad y una buena conductividad eléctrica y térmica, lo que lo hace adecuado para piezas ligeras. Al doblarlo, se deben tener en cuenta las propiedades de fuerte ductilidad y pequeño módulo elástico para evitar rebotes excesivos que afecten la calidad del producto.
Aleación de cobre: Presenta buena conductividad eléctrica y resistencia a la corrosión. Debido a su alta solidez, debe procesarse con matrices y condiciones de proceso adecuadas.
Consideraciones de diseño para curvas en U
Radio de curvatura: Generalmente es mayor que un cierto múltiplo del espesor del material para evitar generar grietas o tensiones internas demasiado grandes durante el plegado, asegurando la integridad de la estructura de la pieza.
Ángulo de curvatura: Determina la forma final de la pieza. Se calcula en función de los requisitos de diseño del producto y del efecto de recuperación elástica, compensándose así y llegando al tamaño geométrico previsto.
Fuerza de flexión: La presión se determina por muchos factores, como el espesor del material, el radio de curvatura y la longitud. Una presión demasiado grande o demasiado pequeña puede provocar problemas de calidad. Por lo tanto, se necesitan herramientas de cálculo profesionales y fórmulas empíricas para garantizar el valor de presión adecuado.
Factores que influyen en la precisión de la flexión en U
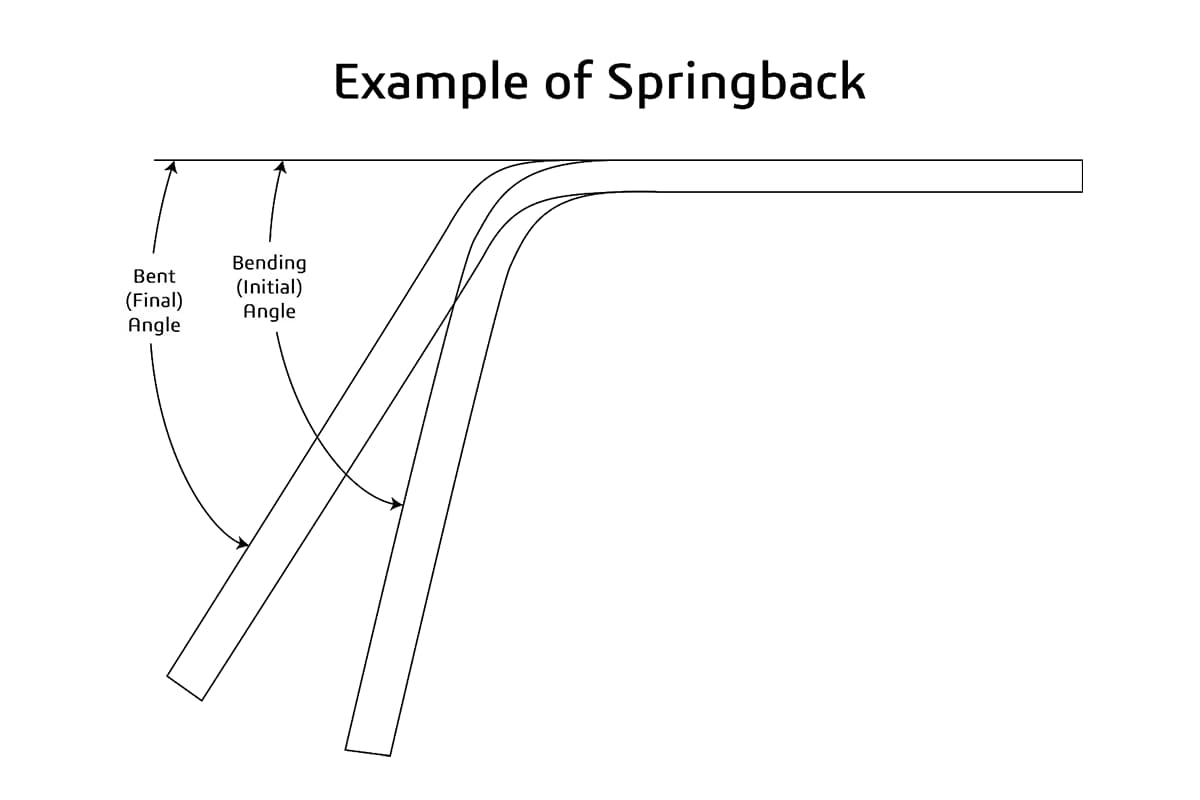
La recuperación elástica se produce cuando el metal recupera parcialmente su forma original después de doblarse. Para solucionar este problema, se utilizan técnicas como el doblado excesivo, el doblado a fondo y el acuñado:
- Sobreflexión aplica fuerza adicional para contrarrestar el efecto elástico.
- Abajo Doblado implica presionar el material en el molde para lograr una curvatura precisa.
- Acuñación Crea una deformación permanente a través de la flexión a alta presión, eliminando la recuperación elástica del material.
Propiedades del material
La ductilidad, dureza y espesor del material afectan directamente el rendimiento de doblado. Los materiales más duros pueden requerir mayor fuerza y manipulación cuidadosa para evitar el agrietamiento, mientras que los materiales dúctiles permiten doblados más suaves.
Radio de curvatura
Mantener un radio de curvatura constante es fundamental para lograr formas en U uniformes. El radio depende de la punta del punzón y de la geometría de la matriz; los radios más ajustados requieren herramientas especializadas.
Parámetros clave de la máquina para un doblado en U preciso
Fuerza de flexión
La fuerza de plegado se refiere a la cantidad de presión que aplica la prensa plegadora, que depende del espesor y la resistencia del material. Está influenciada por factores como el espesor del material, el radio de plegado y la longitud de la pieza de trabajo.
La aplicación de una fuerza insuficiente puede provocar pliegues incompletos, mientras que una fuerza excesiva puede dañar las herramientas o el material. Para garantizar pliegues precisos, se debe utilizar el conjunto de herramientas adecuado (punzones y matrices) para que coincida con la fuerza necesaria.
Longitud de curvatura
La longitud de plegado define la longitud máxima del material que la prensa plegadora puede manipular en una sola operación. Esto es particularmente importante para aplicaciones a gran escala, donde es esencial mantener la uniformidad en todo el pliegue. Las longitudes de plegado más largas reducen la necesidad de múltiples operaciones, lo que mejora tanto la eficiencia como la consistencia.
Carrera del cilindro
La carrera del cilindro se refiere al rango de movimiento vertical del ariete durante el proceso de doblado. Una carrera de cilindro más larga ofrece más flexibilidad para doblar materiales más gruesos o más altos, adaptándose a los ángulos de doblado requeridos y ayudando a compensar la recuperación elástica.
Apertura durante el día
La abertura de paso se refiere al espacio entre las vigas superior e inferior cuando la prensa plegadora está completamente abierta. Este espacio determina el tamaño máximo del material y las herramientas que se pueden colocar en la máquina para trabajar metales. Las aberturas de paso más grandes permiten doblar piezas más altas y utilizar herramientas especializadas.
Velocidad y control
La velocidad de la viga superior afecta directamente la eficiencia de la producción. Las máquinas modernas permiten a los operadores de las prensas plegadoras ajustar la velocidad en varias etapas del ciclo de plegado, desde una aproximación rápida hasta un plegado preciso, lo que garantiza tanto la velocidad como la precisión. Los sistemas CNC proporcionan un control mejorado, lo que permite una programación precisa de los ajustes de fuerza, velocidad y ángulo, lo que mejora la consistencia y reduce los errores.
Ventajas de la flexión en U
La flexión en U ofrece varios beneficios notables:
- Versatilidad: Adecuado para una amplia gama de materiales y espesores, lo que lo hace aplicable en todas las industrias.
- Precisión: Las prensas plegadoras avanzadas con controles CNC garantizan resultados consistentes y precisos.
- Rentabilidad: El proceso minimiza el desperdicio de material y es adaptable tanto a la producción a pequeña escala como a la de gran volumen. Por ejemplo, en la industria automotriz, se ha demostrado que el doblado en U reduce los costos de fabricación de los componentes del chasis al optimizar el uso del material.
Guía práctica
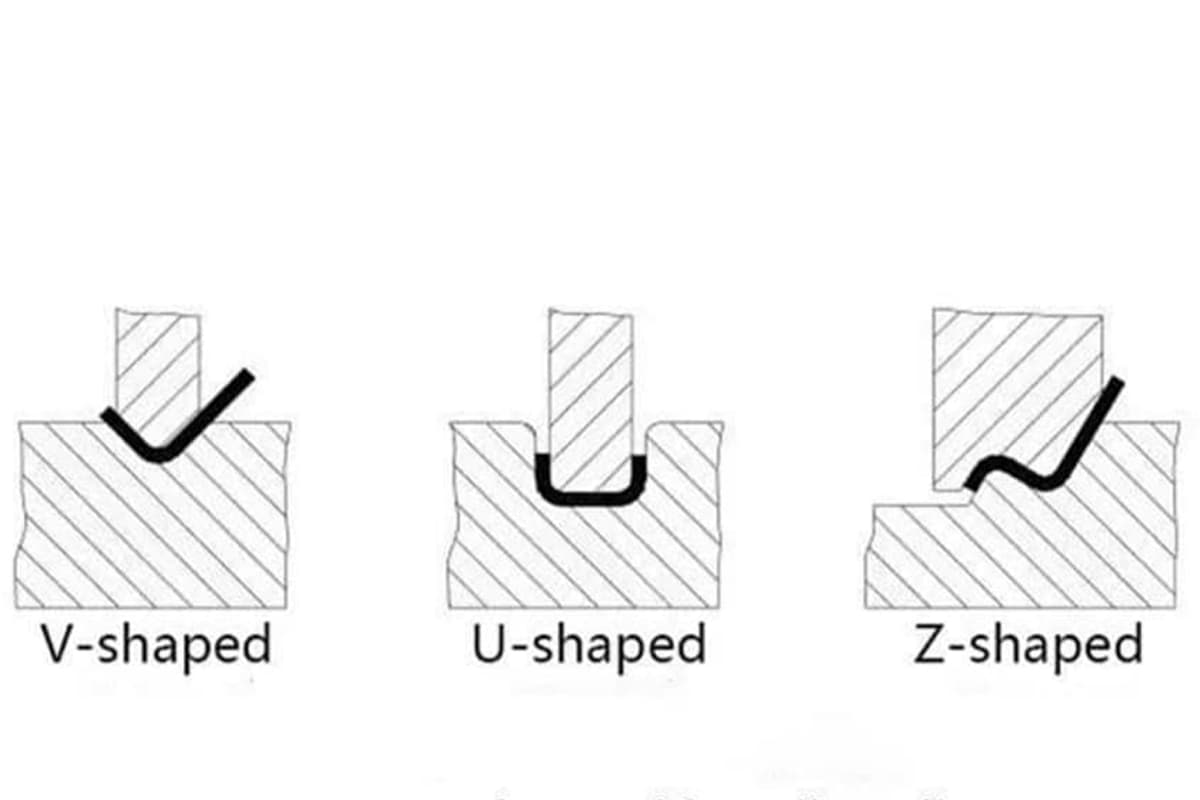
Guía paso a paso para realizar una curva en U
Elija la prensa plegadora y las matrices adecuadas: Elija una prensa plegadora mecánica o hidráulica según el tipo y el grosor del material. Elija la matriz superior e inferior adecuadas según el tamaño y la forma de la curva en U requerida.
Preparación del material: Mida y corte la chapa metálica al tamaño requerido.
Establecer los parámetros de la máquina: Establezca los parámetros razonables de fuerza de curvatura, velocidad y ángulo de acuerdo con el espesor del material y el radio de curvatura.
Operar la flexión: Coloque la lámina de metal en la prensa plegadora, asegúrese de que esté en el medio de la matriz y dóblela de acuerdo con los parámetros decididos.
Comprobar y ajustar: controlar la deformación del material, comprobar la precisión del tamaño y el ángulo, y ajustar oportunamente la presión y el ángulo para compensar el efecto de recuperación elástica. Después de doblar inicialmente uno o ambos lados, realizar la otra parte del doblado de acuerdo con los mismos procedimientos.
Técnica:Utilice herramientas de medición precisas para verificar la posición del troquel y el ajuste del ángulo muchas veces.
En el caso de piezas complejas en forma de U, se puede adoptar el método de conformado paso a paso. Doblar una sección pequeña a la vez y mantener la sección constante y consistente.
Desarrollar procedimientos operativos estandarizados, proceder estrictamente y mejorar la competencia operativa mediante la práctica repetida.
¿Cómo calcular el radio de curvatura en una prensa plegadora con curva en U?
- Comprenda los conceptos básicos del radio de curvatura
- El radio de curvatura de una pieza doblada en U es el radio de la curva interior de la forma en U. Es un parámetro crucial, ya que afecta la integridad estructural, la apariencia y la funcionalidad de la pieza doblada. Un radio de curvatura más pequeño puede dar como resultado una pieza doblada en U más compacta, mientras que un radio más grande puede ser necesario para piezas que requieren más flexibilidad o para evitar el agrietamiento del material.
- Factor de espesor del material
- El espesor del material (Rmin) es un factor clave para calcular el radio de curvatura mínimo. Como regla general, el radio de curvatura mínimo () está relacionado con el espesor del material. Para la mayoría de los metales, existe un radio de curvatura mínimo recomendado para evitar el agrietamiento. Por ejemplo, en el acero dulce, el radio de curvatura mínimo suele ser de alrededor de 1 a 2 veces el espesor del material. Es decir, Rmin = (1-2)t.
- La proporción exacta depende de la ductilidad del material. Los materiales dúctiles como el aluminio generalmente pueden tener un radio de curvatura menor en relación con su espesor en comparación con materiales menos dúctiles como algunos aceros de alta resistencia.
- Consideraciones sobre las herramientas
- Las herramientas utilizadas en la prensa plegadora también afectan el radio de curvatura. El radio del punzón y de la matriz desempeñan un papel importante. El radio del punzón (r,) debe ser ligeramente menor que el radio de curvatura final deseado (R). La relación entre el radio del punzón y el radio de curvatura se puede aproximar como , donde es un pequeño factor de ajuste que tiene en cuenta la recuperación elástica. La recuperación elástica es la tendencia del material a volver parcialmente a su forma original después del plegado.
- El radio de la matriz () suele ser mayor que el radio del punzón y está diseñado para acomodar el material doblado y brindar soporte durante el proceso de doblado. Una regla general es que el radio de la matriz es aproximadamente 1,5 a 2 veces el radio del punzón ().
- Fórmula de cálculo basada en geometría y propiedades del material
- Para un cálculo más preciso, puede utilizar la siguiente fórmula basada en el concepto de eje neutro. El eje neutro es la capa dentro del material que no se comprime ni se estira durante la flexión. La fórmula para el radio de curvatura () considerando el espesor del material (), el ángulo de curvatura () y el factor de elongación () es:
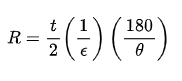
- donde es el alargamiento de la fibra exterior del material durante la flexión y se puede obtener a partir de tablas de propiedades del material o mediante pruebas. El ángulo de flexión se mide en grados.
- En la práctica, también es importante tener en cuenta los márgenes de recuperación elástica. La recuperación elástica se puede calcular mediante ensayo y error o utilizando datos empíricos proporcionados por el proveedor de material o el fabricante de la prensa plegadora. Por lo general, es posible que deba ajustar el radio de curvatura calculado en un cierto porcentaje (normalmente alrededor de 5 - 10%) para tener en cuenta la recuperación elástica, según el material y el proceso de plegado.
Errores comunes y cómo evitarlos
La elección incorrecta de las matrices y el ajuste incorrecto de la distancia entre matrices darán lugar a un mal efecto de plegado o a daños en la pieza de trabajo. Si la fuerza de plegado es demasiado grande o pequeña, esto provocará la rotura del material. La recuperación elástica es demasiado grande, lo que afectará a la precisión del producto. La posición incorrecta del material y la fijación provocarán un desplazamiento durante el proceso de plegado.
Existen algunos enfoques de precauciones basados en las preguntas anteriores:
Obedezca estrictamente el manual de operaciones, elija la matriz integrada con la experiencia práctica, verifique periódicamente y ajuste el espacio de la matriz.
Calcular la fuerza de flexión según las propiedades y el espesor del material, y tomar también en consideración la recuperación elástica, aumentando adecuadamente el volumen de compensación.
Mejore la capacitación del operador y mejore la precisión de sujeción y posicionamiento del material.
Mantenimiento y cuidado de las prensas plegadoras
Mantenimiento diario
Limpie periódicamente los residuos internos y externos de la prensa plegadora, asegúrese de que el sistema de lubricación esté suave y complemente o reemplace el aceite lubricante a tiempo.
Verificar las propiedades de sellado del sistema hidráulico para evitar fugas de aceite, asegurando el correcto funcionamiento de los componentes hidráulicos. Realizar el mantenimiento y la verificación del sistema de control eléctrico, asegurando el funcionamiento estable y seguro de los componentes. Verificar la situación de abrasividad de las matrices, rectificando, reparando o reemplazando las matrices nuevas cuando sea necesario.
Estrategias de mantenimiento a largo plazo
Desarrollar un plan detallado de mantenimiento del equipo, verificarlo y repararlo periódicamente, para evitar que se produzcan posibles fallos de funcionamiento.
Establecer el registro de uso y realizar seguimiento al estado de operación del equipo, para ofrecer evidencia para mantenimiento posterior.
Concientizar a los empleados sobre la importancia del mantenimiento del equipo y desarrollar un buen hábito de operación, para prolongar la vida útil de la prensa plegadora y la eficiencia de trabajo.
Aplicaciones industriales
Curvas en U en diversas industrias
Industria del automóvil
En la fabricación de automóviles, el doblado en U se utiliza ampliamente para producir conductos de sistemas de escape, componentes de suspensión y piezas estructurales de la carrocería. Es estricto en cuanto al material elegido, la precisión del proceso de doblado y la durabilidad de los productos porque estos componentes generalmente deben soportar altas temperaturas, alta presión y vibración.
Industria aeroespacial
La industria aeroespacial tiene requisitos extremadamente altos en cuanto a peso ligero y alta resistencia. El proceso de doblado en U se utiliza generalmente en sistemas de suministro de combustible de aeronaves, estructuras de fuselaje y otros diseños de tuberías internas, lo que garantiza que cada pieza pueda cumplir con estándares estrictos y alcanzar los objetivos de pérdida de peso.
Industria de la arquitectura
En la industria de la construcción, los tubos o aceros en forma de U se utilizan ampliamente en el soporte de estructuras, sistemas de escape, tuberías de HVAC, etc. Especialmente en la arquitectura de estructuras de acero, las vigas en forma de U precurvadas pueden mejorar la eficiencia de trabajo y la estabilidad de la estructura, lo que es conveniente para el montaje puntual.
Tendencias futuras en el plegado en U con prensa plegadora
Tecnologías y métodos emergentes
Tecnología CNC y los grados de automatización se mejoran constantemente, haciendo que la prensa plegadora sea capaz de realizar tareas de plegado en forma de U más complejas y disminuir el error provocado por la intervención manual.
La tecnología de la máquina y el sistema de producción inteligente se incorporan para hacer que la curva en U sea más eficiente, flexible y adaptada a pequeñas variedades, tipos y necesidades de producción personalizadas.
El desarrollo de la ciencia de los materiales, al igual que el surgimiento de nuevos materiales compuestos, desafiará el proceso de plegado y también brindará a la tecnología de doblado en U la posibilidad de aplicaciones innovadoras.
Anticipación de la industria de fabricación de metales
La futura tecnología de prensa plegadora avanzará hacia una mayor precisión, mayor velocidad y gran flexibilidad para manejar diseños de piezas de trabajo más complejos.
El concepto de protección del medio ambiente verde está profundamente arraigado en el corazón de la gente. Los equipos y tecnologías de bajo consumo y alta producción serán la corriente principal, incluida la aplicación del sistema hidráulico de ahorro de energía, el reciclaje del calor residual y otras medidas en las prensas plegadoras.
La tecnología digital y de redes se integrará aún más en el proceso de conformado de metales. El proceso de producción se mejorará mediante la Internet de las cosas y el análisis de macrodatos, mejorando así la eficiencia y la calidad de la producción en general.