When investing in a sheet metal laser cutting machine, it’s crucial to understand the essential features that will best meet your production needs. The right machine can significantly enhance efficiency, precision, and overall productivity in your operations. With numerous options available in the market, identifying key features such as laser power, cutting speed, bed size, control systems, and additional automation capabilities can help you make an informed decision. This guide aims to highlight these critical features, providing you with the insights necessary to choose a sheet metal laser cutting machine that delivers optimal performance and value.
Table of Contents
Introduction
Choosing the right sheet metal laser cutting machine is crucial for any manufacturing business, as it directly impacts production efficiency, cutting precision, and overall operational costs. A suitable machine can handle various material types and thicknesses, ensuring high-quality cuts with minimal waste. It can also enhance productivity by speeding up the cutting process and reducing downtime. Moreover, the right machine can integrate seamlessly with existing workflows and support future scalability. Investing in the best-fit laser cutting machine ensures that your business stays competitive, meets customer demands, and operates cost-effectively.
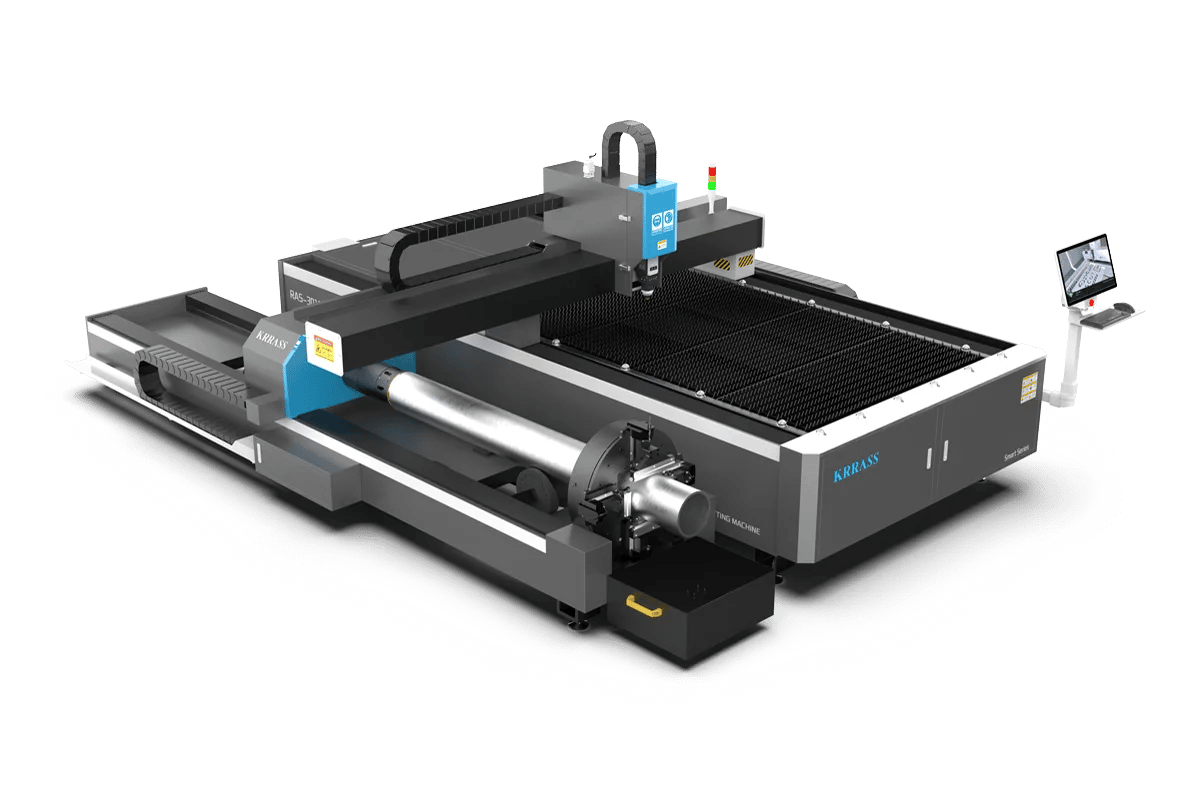
Key Factors To Consider When Buying A Sheet Metal Laser Cutting Machine
1. Laser Power and Type
Fiber lasers use optical fibers doped with rare-earth elements as the lasing medium. They offer higher efficiency, faster cutting speeds, and lower maintenance costs compared to CO2 lasers. Fiber lasers are particularly effective for cutting thin to medium-thickness metals, including stainless steel, aluminum, and brass. Ideal for high-precision cutting in industries such as aerospace, automotive, and electronics. A manufacturing plant producing stainless steel components for the automotive industry implemented a 3 kW fiber laser cutter, increasing their cutting speed by 50% and reducing operational costs by 30%.
CO2 lasers use a gas mixture (carbon dioxide, nitrogen, and helium) as the lasing medium. Known for their versatility, CO2 lasers can cut a wide range of materials, including non-metals like wood, acrylic, and glass, in addition to metals. They are well-suited for cutting thicker materials. Commonly used in industries requiring diverse material processing, such as signage, textiles, and fabrication. A signage company uses a CO2 laser cutter to produce intricate acrylic signs and thick metal letters, achieving precise cuts with high-quality edges.
Importance of Laser Power for Cutting Various Thicknesses of Sheet Metal
The power of a laser cutting machine significantly influences its ability to cut through different thicknesses of sheet metal. Here are some insights into how different power levels affect cutting capabilities, supported by data:
Low Power Lasers (up to 2 kW):
Suitable for cutting thin sheet metals (up to 6 mm). Ideal for applications requiring high precision and speed on thinner materials, such as electronics enclosures and intricate metal parts. A study showed that a 1.5 kW fiber laser can cut 3 mm stainless steel at a speed of 6 m/min, whereas a CO2 laser of the same power cuts at 4 m/min.
Medium Power Lasers (2 kW to 6 kW):
Can efficiently cut medium thicknesses (up to 20 mm). Used in automotive parts manufacturing, metal furniture, and general fabrication where moderate thickness and high accuracy are required. A metal furniture manufacturer switched to a 4 kW fiber laser, allowing them to cut 12 mm steel at 1.5 m/min, improving production rates by 40%.
High Power Lasers (6 kW and above):
Designed to handle thick materials (over 20 mm) with ease. Essential for heavy-duty applications in industries such as shipbuilding, construction, and heavy machinery manufacturing where thick, durable cuts are necessary. In shipbuilding, a 10 kW CO2 laser can cut 25 mm steel at 0.7 m/min, offering the strength and precision needed for constructing durable ship components.
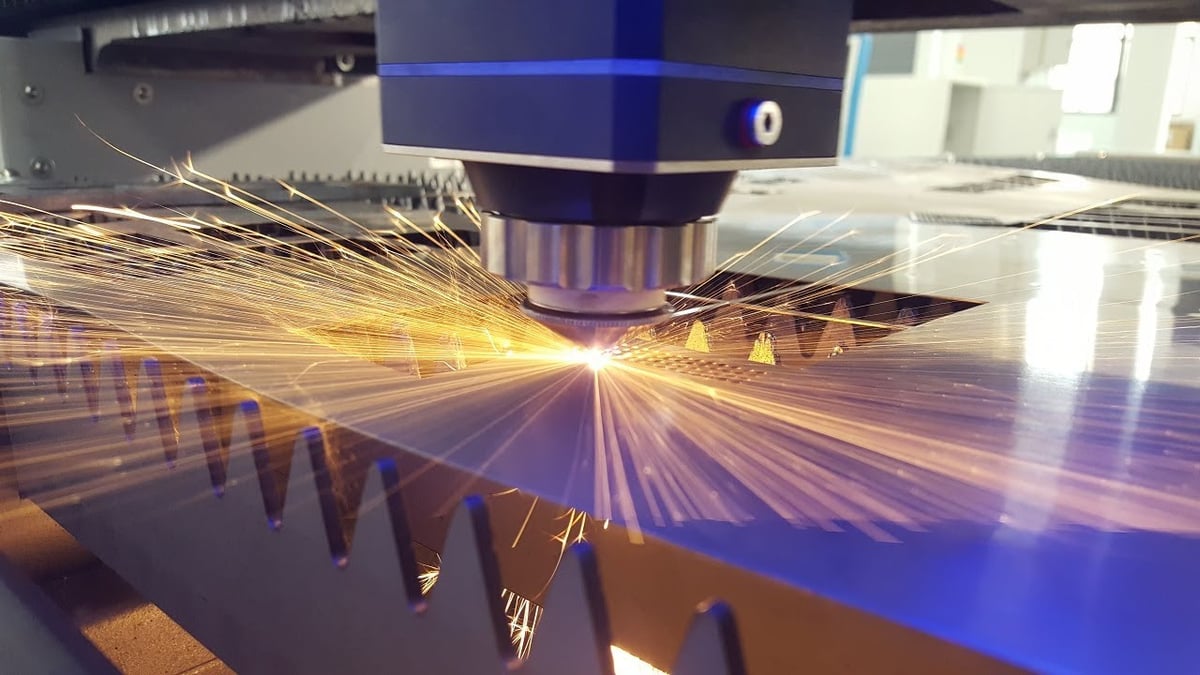
Tips from Krrass Expert
Selecting the appropriate laser type and power is crucial for optimizing performance and cost-efficiency in your operations. By understanding the capabilities and applications of fiber and CO2 lasers, and choosing the right power level for your specific needs, you can achieve significant improvements in production speed, precision, and overall efficiency. Whether you're cutting thin electronic enclosures or thick shipbuilding materials, there's a laser cutting solution tailored to your requirements.
2. Cutting Speed and Precision
Cutting Speed and Productivity
Cutting speed is a critical factor that directly influences productivity in sheet metal processing. Faster cutting speeds translate into shorter cycle times, which significantly boosts overall manufacturing efficiency. For example, modern fiber laser cutting machines can achieve speeds of up to 100 meters per minute for thin materials, allowing manufacturers to produce larger volumes in less time. This increased throughput reduces lead times, enhances production capacity, and ultimately lowers operational costs.
Importance of Precision for High-Quality Cuts
Precision is paramount in achieving high-quality cuts in sheet metal fabrication. Laser cutting machines excel in delivering precise cuts with minimal material distortion or heat-affected zones. This capability ensures that components are fabricated to exact specifications, meeting stringent quality standards across various industries.
Whether cutting intricate designs or structural components, the ability to maintain precise dimensions and smooth edges enhances product aesthetics, functionality, and overall customer satisfaction. High precision also reduces scrap material and rework, optimizing material usage and production efficiency. Industries such as automotive, aerospace, and electronics rely heavily on laser cutting's precision to maintain consistency and reliability in their manufacturing processes.
Tips from Krrass Expert
According to Krrass experts, optimizing cutting speed and precision is pivotal for maximizing the efficiency and quality of sheet metal processing. Their advanced laser cutting machines are engineered to deliver high-speed cutting capabilities with unmatched precision, meeting the diverse needs of industries ranging from automotive to electronics. By prioritizing speed and precision, Krrass ensures that manufacturers achieve operational excellence and maintain a competitive edge in the market.
3. Bed Size and Configuration
Different Bed Sizes and Their Impact on Material Handling
Large Bed Size: Machines with larger beds can accommodate oversized sheets of material, reducing the need for frequent material handling and setup changes. This capability enhances productivity by allowing continuous processing of larger volumes of material without interruptions. Ideal for industries that require batch processing or cutting of large components, such as automotive body panels, shipbuilding parts, and architectural cladding.
Small Bed Size: Smaller beds are more space-efficient and cost-effective for businesses with limited floor space. They are suitable for processing smaller batches of materials or producing intricate, smaller components. Used in industries like electronics and medical device manufacturing, where precision and compact size are prioritized.
Fixed vs. Adjustable Beds
Fixed Beds: The cutting area remains stationary and fixed in size. Simplifies machine design and reduces mechanical complexity. Provides stable support for materials during cutting, ensuring consistent cutting quality. Commonly used in standard production environments where material sizes and cutting requirements are predictable and uniform.
Adjustable Beds: The bed can be adjusted to accommodate different material sizes and configurations. Offers flexibility to handle various material dimensions and shapes without requiring frequent manual adjustments or setup changes. Enhances versatility for batch processing and custom manufacturing. Suitable for job shops and industries with diverse cutting requirements, allowing for efficient utilization of the cutting area and optimizing material usage.
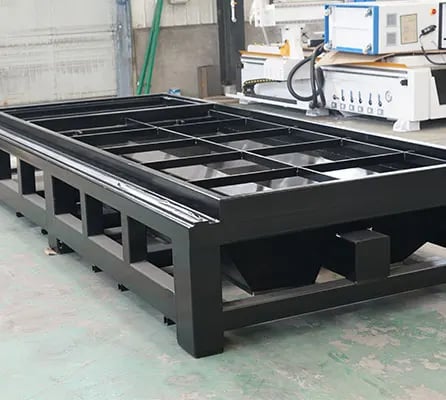
Tips from Krrass Expert
According to Krrass experts, choosing the right bed size and configuration is crucial for optimizing workflow efficiency and maximizing production capabilities. Large beds streamline material handling and support continuous processing, while adjustable beds offer flexibility for diverse cutting needs. By selecting the appropriate bed size and configuration, businesses can enhance operational efficiency, minimize downtime, and achieve higher overall productivity in sheet metal processing.
4. Control Systems and Software
Importance of User-Friendly Interfaces
User-friendly interfaces optimize operator efficiency and reduce training time. Intuitive controls and clear displays streamline laser cutting machine operations, allowing operators to quickly adjust parameters, monitor processes, and resolve issues. This enhances productivity by minimizing downtime and ensuring consistent performance.
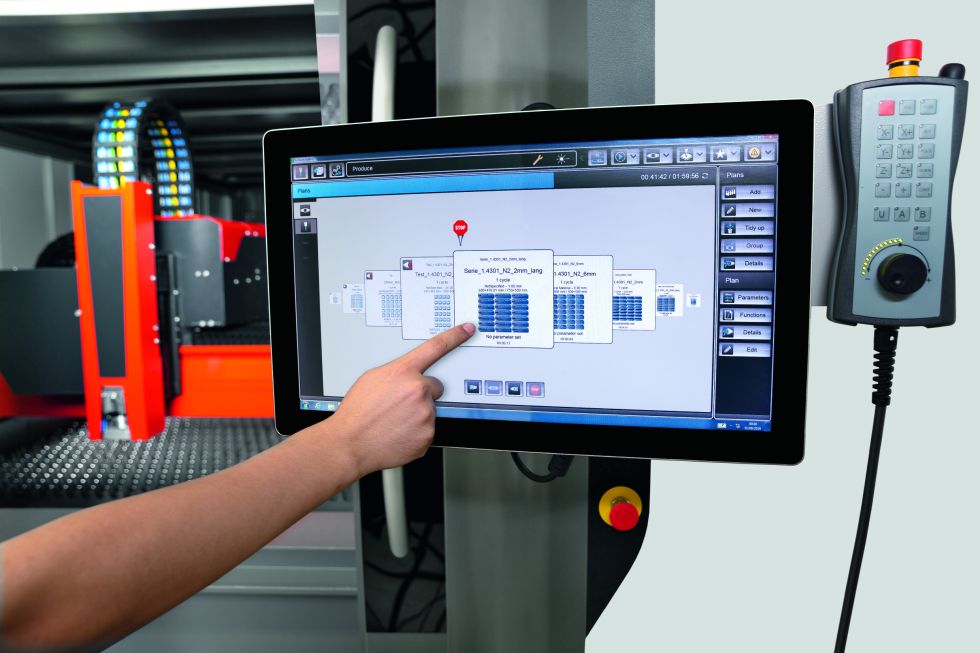
Integration with CAD/CAM Software
CAD/CAM software integration facilitates seamless workflow from design to production. Compatible with industry-standard software packages, it enables direct import of design files, precise part nesting for material optimization, and simulation of cutting paths to validate designs. This integration enhances accuracy, speeds up programming, and allows customization of cutting parameters to meet specific production needs.
Tips from Krrass Expert
According to Krrass experts, prioritizing user-friendly interfaces and CAD/CAM software integration is crucial for maximizing operational efficiency and achieving superior cutting results. A well-designed interface simplifies machine operation and maintenance, while seamless software integration supports precision and flexibility in production planning. By investing in advanced control systems and software, businesses can streamline their workflow, reduce costs, and maintain a competitive edge in the laser cutting industry.
5. Automation and Additional Features
Benefits of Automated Loading and Unloading
Automated loading and unloading systems offer significant advantages in laser cutting operations. They streamline material handling processes, reducing manual labor and minimizing downtime between jobs. By automating these tasks, manufacturers can achieve higher throughput and operational efficiency. This is particularly beneficial in high-volume production environments where continuous processing and quick turnaround times are essential.
Additional Features like Autofocus, Capacitive Height Sensing
Autofocus:
Ensures consistent focal length adjustment during cutting, optimizing cutting quality across various material thicknesses and surface conditions. This feature reduces setup time and improves cutting efficiency, especially when processing materials with varying thicknesses.
Capacitive Height Sensing:
Allows real-time monitoring and adjustment of the cutting head's height above the material surface. This ensures optimal cutting distance, improving edge quality and preventing damage to delicate materials. Capacitive height sensing is essential for maintaining precise cutting results in applications requiring high accuracy.
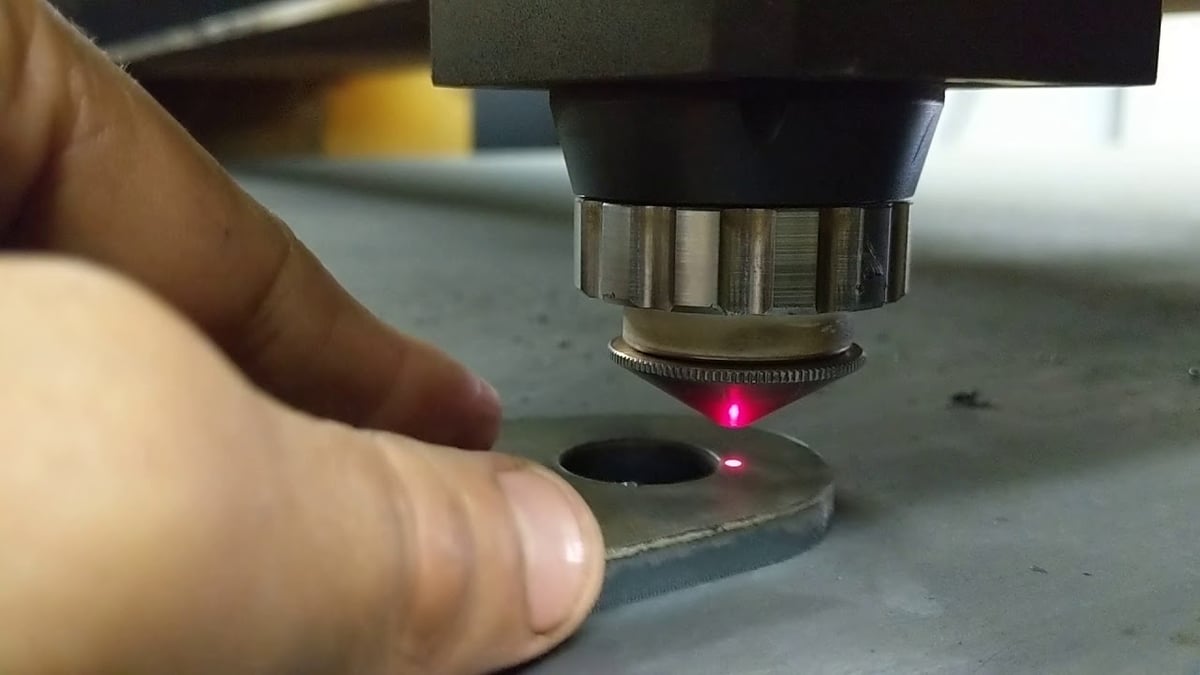
Tips from Krrass Expert
According to Krrass experts, incorporating automated loading and unloading systems alongside advanced features like autofocus and capacitive height sensing enhances overall efficiency and productivity in laser cutting operations. These technologies streamline workflow processes, minimize errors, and ensure consistent cutting performance, ultimately optimizing production output and reducing operational costs. Integrating such features into laser cutting machines enables manufacturers to meet stringent quality standards and maintain a competitive edge in the industry.
6. Energy Efficiency and Operating Costs
Energy Consumption of Different Machines
Energy consumption varies among laser cutting machines based on factors such as laser type, power rating, and operational settings:
Fiber Lasers: Known for their high efficiency, fiber lasers consume less energy compared to CO2 lasers. They utilize optical fibers doped with rare-earth elements to generate laser beams, resulting in lower power consumption per cutting operation.
CO2 Lasers: These lasers use a gas mixture (carbon dioxide, nitrogen, and helium) as the lasing medium, typically consuming more energy than fiber lasers due to their operational characteristics and gas consumption.
Power Rating Impact: Higher laser power ratings generally correlate with increased energy consumption, particularly during intensive cutting tasks and high-speed operations.
Understanding the energy requirements of different laser cutting machines helps businesses evaluate operational costs and make informed decisions regarding machine selection and usage.
Long-term Cost Implications of Energy Efficiency
Investing in energy-efficient laser cutting machines offers significant long-term cost benefits:
Reduced Operating Costs: Lower energy consumption leads to reduced electricity bills, contributing to overall operational cost savings over the machine's lifespan.
Environmental Impact: Energy-efficient machines contribute to sustainability goals by minimizing carbon emissions and reducing the environmental footprint of manufacturing operations.
Maintenance Savings: Efficient machines often require less frequent maintenance and repairs, further reducing operational downtime and associated costs.
Tips from Krrass Expert
According to Krrass experts, prioritizing energy-efficient laser cutting machines not only lowers operating costs but also enhances sustainability efforts and operational reliability. By selecting machines with optimal energy consumption profiles and implementing efficient operational practices, businesses can achieve significant savings while maintaining high productivity and meeting environmental objectives.
7. Maintenance and Support
Importance of Regular Maintenance
Regular maintenance is crucial for ensuring optimal performance and longevity of laser cutting machines:
Minimizes Downtime: Scheduled maintenance prevents unexpected breakdowns, minimizing production interruptions and ensuring continuous operation.
Preserves Cutting Quality: Regular servicing maintains cutting precision and quality, reducing material waste and rework.
Prolongs Machine Lifespan: Proper maintenance extends the lifespan of critical components, optimizing return on investment (ROI) and reducing long-term replacement costs.
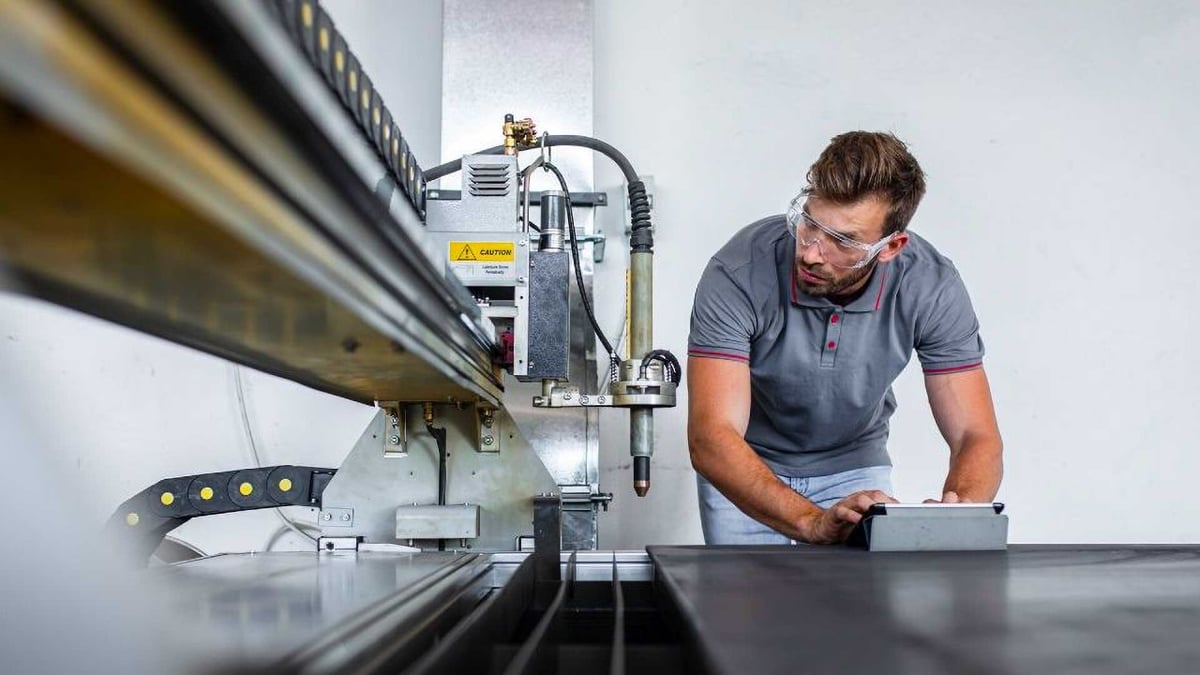
Availability of Support and Spare Parts
Access to comprehensive support and readily available spare parts is essential for maintaining machine reliability and minimizing downtime:
Timely Resolution of Issues: Prompt technical support ensures quick resolution of machine issues, preventing prolonged downtime and production delays.
Genuine Spare Parts: Using authentic spare parts enhances machine reliability and performance, ensuring compatibility and longevity.
Service Network: A reliable service network provides on-site support and expertise, offering peace of mind and minimizing operational disruptions.
Tips from Krrass Expert
According to Krrass experts, prioritizing regular maintenance and reliable support infrastructure is critical for maximizing the performance and durability of laser cutting machines. Implementing a proactive maintenance schedule, supported by knowledgeable technical assistance and genuine spare parts, enhances operational efficiency and prolongs machine lifespan. By investing in quality maintenance and support services, businesses can minimize operational risks, optimize production uptime, and achieve consistent cutting performance, ultimately enhancing overall productivity and customer satisfaction.
8. Brand Reputation and Reviews
Importance of Choosing a Reputable Brand
Choosing a reputable brand for laser cutting machines is crucial for several reasons:
Reliability and Quality: Established brands have a proven track record of manufacturing high-quality machines with advanced technologies and robust designs, ensuring consistent performance, durability, and precision in cutting operations.
Customer Support: Reputable brands excel in providing comprehensive customer support, including timely technical assistance, reliable availability of spare parts, and a widespread service network. This support infrastructure minimizes downtime, enhances operational efficiency, and fosters trust and satisfaction among users.
Innovation and R&D: Leading brands prioritize investments in research and development, continuously introducing cutting-edge features and advancements. These innovations improve machine capabilities, such as faster cutting speeds, broader material compatibility, and enhanced automation, keeping users at the forefront of technological advancements.
Long-Term Commitment: Reputable brands demonstrate commitment to long-term customer satisfaction by offering warranties and assurances that protect investments. This commitment extends beyond the initial purchase, ensuring ongoing support, upgrades, and compatibility with evolving industry needs.
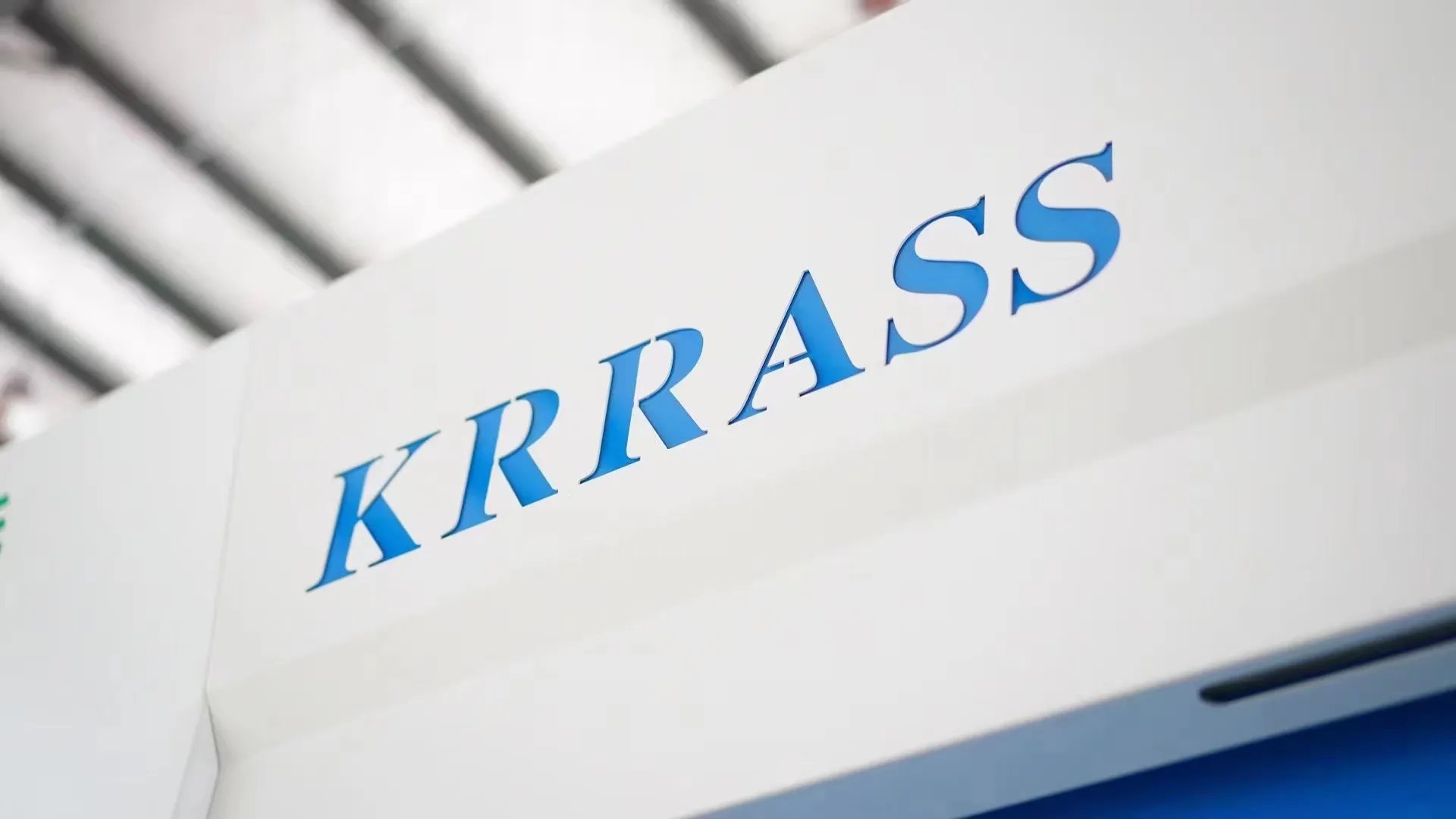
Considering Customer Reviews and Expert Opinions
Customer reviews and expert opinions provide valuable insights into a brand's reputation and product performance:
Customer Reviews: Feedback from existing users offers firsthand experiences regarding machine reliability, performance, and after-sales support.
Expert Opinions: Insights from industry experts and reviewers help gauge a brand's standing, technological advancements, and market competitiveness.
Tips from Krrass Expert
According to Krrass experts, when selecting a laser cutting machine, consider the brand's reputation for reliability, customer support, and technological innovation. Customer reviews and expert opinions serve as essential resources to validate a brand's claims and assess its suitability for your operational needs. Investing in a reputable brand not only ensures quality and reliability but also secures ongoing support and potential for future upgrades. By prioritizing brand reputation and informed decision-making, businesses can confidently invest in laser cutting solutions that deliver consistent performance and operational efficiency.
Conclusion
Making an informed decision involves evaluating these features against specific operational requirements, production goals, and budget constraints. It's essential to conduct thorough research, leverage customer reviews, seek expert advice, and consider long-term benefits such as reliability, support, and technological advancements.
By prioritizing these considerations and leveraging insights from industry experts, such as those from Krrass, businesses can confidently invest in a laser cutting machine that not only meets immediate needs but also supports future growth and innovation in manufacturing.
Choosing the right laser cutting machine is a strategic decision that impacts overall efficiency, competitiveness, and success in today's dynamic industrial landscape.
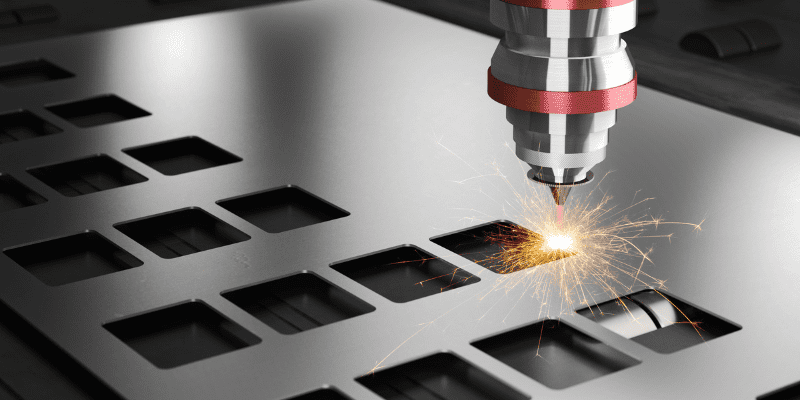