In recent years, fiber laser applications have gained significant traction across various industries, transforming the landscape of manufacturing and material processing. These advanced lasers offer unparalleled precision, speed, and versatility, making them ideal for a wide range of tasks, from cutting and welding to marking and engraving. As businesses increasingly seek efficient and cost-effective solutions, understanding the diverse applications of fiber lasers is essential for staying competitive in today’s market. This article delves into the key uses of fiber lasers, their benefits, and how they are revolutionizing operations across different sectors.
What is a fiber laser?
Fiber lasers utilize optical fibers as their active gain medium and belong to the category of solid-state lasers. The process involves absorbing raw light from pump laser diodes in a fiber composed of silicate or phosphate glass. Subsequently, the fiber converts this absorbed light into a laser beam characterized by a specific wavelength. To get this, the optical fiber is doped with rare-earth elements.
By employing various doping elements, a wide range of laser beams can be generated, each with its own distinct wavelength. The broad spectrum of wavelengths produced by fiber lasers makes them highly versatile for a multitude of applications. These include machine laser cutting, texturing, cleaning, laser engraving, jewelry engraving, drilling, marking, and welding. Consequently, fiber lasers have found utility across diverse sectors such as medicine, defense, telecommunications, automotive, spectroscopy, electrical, manufacturing, and transportation.
How does a fiber laser work?
Fiber lasers harness pump light emitted by laser diodes, directing the emitted light into a fiber-optic cable. Within the cable, optical components are employed to produce a precise wavelength and amplify it. Subsequently, the laser beam is carefully shaped and released for its intended purpose.
Below is how fiber lasers operate through their several components.
Creation of pump light in the laser diodes
Laser diodes, also referred to as the "pump source," convert electricity into photons or light, which is then pumped into the fiber-optic cable. The process of generating light in diodes involves the utilization of two differently charged semiconductors.
The first semiconductor is positively charged and requires an additional electron. Conversely, the second semiconductor carries a negative charge and possesses either an excess or a free electron.
When the positive and negative charges come into contact, they strive to combine. To facilitate this combination, the free electron is released as a photon. As current flows through the semiconductors, the number of photons rapidly increases.
The resulting light is then directed into the fiber-optic cable, where it will be utilized to produce the laser beam.
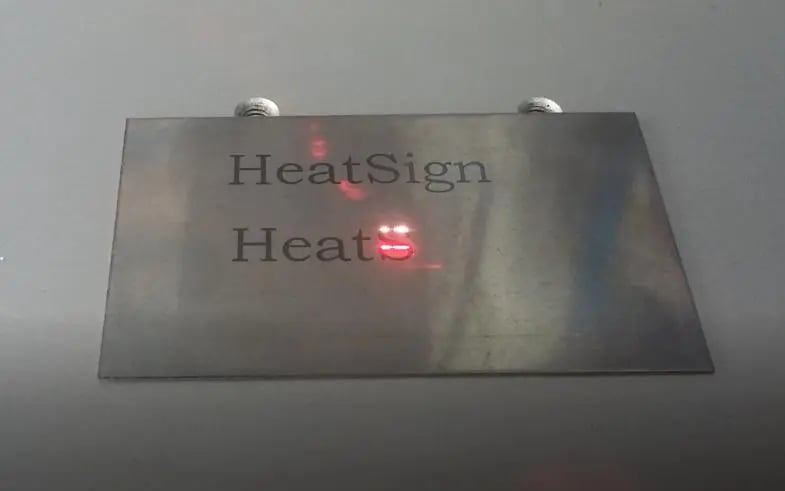
Pump light is guided and passes through the optical fiber
Within the optical fiber system, a coupler plays a vital role in combining the light emitted from multiple laser diodes into a unified good source of fiber. This coupler, integrated into the optical fiber, possesses multiple entry points on one side, each connecting to an individual fiber originating from a laser diode. On the opposite side of the coupler, a single exit point is present, linking to the main fiber. Once the light from all the laser diodes is collected, it travels toward the laser medium.
Subsequently, the light emitted by the diode laser traverses the optical fiber, comprising two primary components: the core and the cladding. The core, constructed of silica glass, serves as the pathway for the light, while the cladding encompasses the core. As the light reaches the cladding, it undergoes total internal reflection, redirecting it back into the core.
Although some power is inevitably lost as heat in fiber lasers, the favorable surface area to volume ratio facilitates efficient heat dissipation, resulting in minimal wear and tear due to thermal effects. During its journey through the optical fiber, the light eventually reaches the doped section of the fiber, commonly referred to as the laser cavity.
Stimulated emission in the laser cavity
When laser diode light reaches the doped fiber, it excites electrons in the rare earth element, resulting in a population inversion crucial for laser production. As these excited electrons transition to lower energy levels, they emit photons of a specific wavelength. Through stimulated emission, these photons stimulate other excited electrons to emit similar photons, creating a cascade effect. The equilibrium between excited and relaxed electrons ensures a continuous flow of raw laser light. However, further refinement is necessary for the light to be utilized in various applications.
Amplification of raw laser light into a laser beam
To prepare the raw laser light emitted from the doped fiber for practical applications, a strengthening process is necessary. In fiber lasers, this is accomplished through the utilization of Fibre Bragg Gratings (FBGs). These gratings serve as reflective mirrors with varying reflectivity, replacing conventional dielectric mirrors.
The laser light within the fiber cavity undergoes a back-and-forth process, interacting with the Bragg Grating. A portion of the light infiltrates the grating in one direction, while the remaining light is reflected back into the laser cavity. The transmitted light that passes through the grating becomes the laser beam. This beam then proceeds through an oscillator, sometimes accompanied by a combiner, to enhance coherence before being delivered as the final output.
Laser light of a specific wavelength is created
The wavelength generated by the doped fiber relies on the choice of a doping element within the laser cavity. This aspect holds significant importance since different applications necessitate different wavelengths. Common doping elements include erbium, ytterbium, neodymium, and thulium, among others. For instance, ytterbium-doped fiber lasers produce a wavelength of 1064 nm, which finds application in laser marking and laser cleaning.
The laser beam is shaped and released
The laser beam formed by the exiting photons from the resonant cavity exhibits exceptional collimation owing to the light-guiding properties of the fiber. However, this high level of collimation may not be suitable for most laser applications. So to achieve the desired beam shape, various components like lenses and beam expanders are employed. Different types of lenses offer distinct advantages, and laser experts carefully select them to optimize the laser for specific applications.
Why use fiber lasers?
With the advancements in fiber laser technology, the range of applications for these lasers continues to expand along with their practicality.
Stable
Typically, when we intend to transmit a laser beam, we often rely on optical fibers to ensure its safe and reliable movement. Another option is to reflect the beam between mirrors, but this method necessitates precise alignment. Achieving efficient coupling of a laser beam into the minuscule core of a fiber is challenging and requires meticulous adjustments. Consequently, conventional lasers are highly susceptible to disruptions from impacts or jolts, and realigning the optics requires the expertise of a specialist. In contrast, fiber lasers generate the beam internally within the fiber itself, eliminating the need for intricate and delicate optics during beam delivery. This inherent characteristic renders fiber lasers highly stable and user-friendly.
High beam quality
The fiber laser generates and confines the beam within the compact core of the fiber. As a result, the beam remains exceptionally straight and can be focused into a minute dot. This quality proves particularly advantageous in applications such as precision fiber laser cutting, where a smaller dot size enhances laser effectiveness. In numerous laser applications, achieving such a focused beam is highly desirable.
Powerful laser
Laser devices can pose a threat to the skin even at relatively low power levels, typically starting at around 1 Watt. Although this amount of power may seem insignificant when compared to everyday appliances like kettles or toasters, the concentrated focus of a laser beam on a single point amplifies its impact significantly. Fiber lasers, in particular, have been advancing in terms of power and can now exceed 1,000 Watts (1kW). This level of power is more than sufficient to penetrate through an inch of steel, highlighting the impressive cutting capabilities of fiber lasers.
Efficient and cools easily
Unlike other types of lasers that have lower power conversion efficiency, a fiber laser has the ability to convert approximately 70-80% of the input power from the pump source. This high efficiency is not only beneficial for power consumption but also results in less power being transformed into heat. In fiber lasers, the heat is distributed along the length of the fiber, which helps prevent excessive heating that could lead to fiber breakage. It's worth noting that the optical properties of most materials undergo changes as they heat up, and these changes can have an impact on the quality of the laser beam.
6 Fiber Laser Applications
Lasers have been around for a few decades and have found use in various settings. Fiber lasers have become increasingly popular in recent years due to their compact size, high efficiency, and versatility. Here are six typical applications for fiber lasers:
1. Fiber Laser Cutting
Cutting is a fundamental aspect of the manufacturing process, and fiber laser applications have revolutionized this domain. Fiber laser machines are capable of cutting various materials, including metals, sheet metals, plastics, acrylics, and composites, with remarkable precision and minimal tolerances. This advanced technology has also transformed the micromachining industry, enabling engineers to create parts as small as one millimeter with exceptional accuracy.
Fiber Laser Cutting Machines have addressed the limitations of traditional cutting methods, which often struggled with precision and incurred higher operational costs, ultimately reducing profitability. In contrast, fiber lasers generate higher yields in less time, leading to increased profits for manufacturers.
Ongoing research continues to enhance laser cutting technology, with cutting capabilities primarily dependent on output power (measured in watts) and the laser source. Key factors influencing performance include pulse energy, peak power, and beam quality. Most commercial-grade fiber laser cutting machines utilize ytterbium (Yb3+) pulsed fiber lasers, known for their exceptional power.
These lasers operate within a wavelength range of 970-1200 nm and can produce over 10 kW of output power. To illustrate their capability, a fiber laser can easily cut through a 25 mm thick sheet of mild steel, demonstrating the impressive potential of this technology.
Are you ready to explore the advantages of fiber laser cutting for your manufacturing needs?
2. Fiber Laser Welding
Fiber laser welding is an innovative process for joining metallic parts in manufacturing, offering significant advantages in speed, cost, efficiency, and reduced deformation. One of the most common applications of fiber laser welding is “fusion type welding,” where two metals are heated and fused together. Additionally, the use of filler electrodes is possible, yielding exceptional results in various welding applications.
Fiber Laser Welding Machines stand out from traditional welding methods by producing less heat, which minimizes the risk of warping and other defects. This technique allows for wider and more precise welding seams without issues like porosity, cracks, or undercuts. Moreover, fiber laser welding is more accessible, requiring less skill than conventional methods. Even individuals with minimal training can learn to handle challenging welding positions effectively.
While the initial investment for fiber laser welding machines can be high, their low power consumption and impressive efficiency—up to four times that of traditional methods—can lead to significant savings in any manufacturing operation. Given the rising demand for welders in the U.S., which is increasing by 2% annually, fiber laser welding machines are poised to play a crucial role in the industry's future.
Eye safety during the welding process remains a vital concern. Unlike traditional welding, which features a visible flame and apparent dangers, laser welding can be less obvious because the lasers used are often outside the visible spectrum. Therefore, experts strongly advise adhering to safety protocols and exercising caution while operating fiber laser welding equipment.
3. Laser Marking and Engraving
Laser marking and engraving is a process that utilizes a high-power laser beam to create text or images by removing or altering the surface layer of various materials without compromising their structural integrity. This technique is gaining popularity, and you may already own items that feature fiber laser markings.
Fiber laser marking is commonly employed to imprint barcodes, serial numbers, product specifications, instructions, and logos on items, enhancing their uniqueness and helping to prevent counterfeiting.
Laser Engraving distinguishes itself from other methods by its ability to engrave a wide range of materials, including metals that CO2 lasers cannot handle. It is estimated that fiber lasers can effectively engrave over thirty different materials, including metal, aluminum, brass, copper, glass, and plastics. In fact, fiber lasers can even engrave organic materials such as wood and leather.
Fiber laser machines are available in commercial-scale options suitable for small to large manufacturing enterprises. Additionally, everyday hobbyists can take advantage of smaller, portable fiber laser machines readily available online. Typically, a laser machine with a power output of 20-30 watts is sufficient for engraving various materials and can even cut through very thin sheet metal.
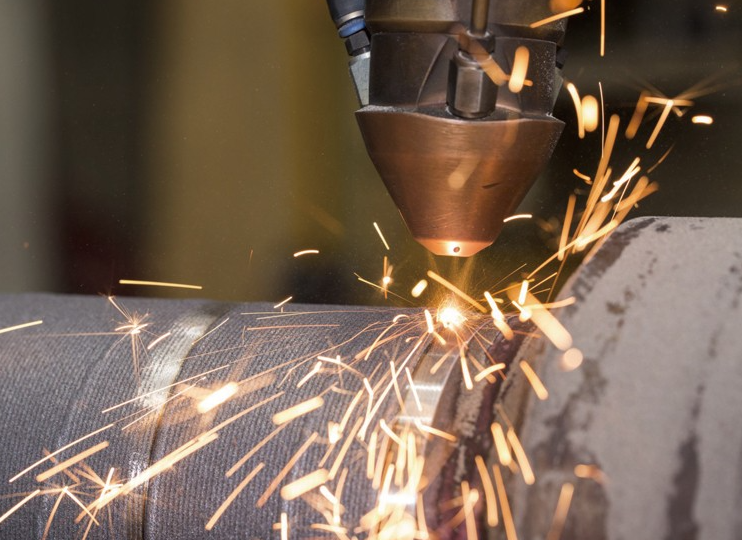
4. Fiber Laser Cleaning
Fiber laser cleaning is a revolutionary technique that effectively removes rust, corrosion, paint, and dirt from metal surfaces by burning and vaporizing unwanted layers. This process, known as “laser ablation,” offers a range of applications across various industries.
When it comes to cleaning, fiber laser technology stands out for its speed, efficiency, and cost-effectiveness. Traditional rust removal methods often rely on oxidation and chemical processes that can be both time-consuming and ineffective. In contrast, fiber laser cleaning is not only effective but also environmentally friendly.
Many people resort to manual rust and corrosion removal using steel wire brushes, a method that is labor-intensive and often inefficient. With fiber laser cleaning, however, any metallic part can be cleaned regardless of its shape or size, making it a highly flexible solution. Plus, the process is visually satisfying to observe as it quickly restores surfaces to their original condition.
Advancements in fiber laser technology have significantly reduced the costs of rust-cleaning units, making this innovative method more accessible than ever.
5. Laser Drilling Materials
While lasers may not be the first technology that comes to mind for drilling, fiber laser drilling is rapidly gaining recognition as a leading solution in the precision drilling industry.
Unlike traditional drilling methods that utilize conventional rotary drill bits, fiber laser drilling employs high-intensity laser beams to create precise holes. This technique has become increasingly popular for drilling printed circuit boards (PCBs) in the electronics sector due to its micro-level precision.
Fiber laser drilling is both highly efficient and cost-effective. One significant advantage of this method is that there’s no need to replace drill bits, which can save time and reduce operational costs. Understanding the impact of process parameters on drilling outcomes is crucial for optimizing performance.
Modern fiber laser machines are capable of drilling through a variety of materials, including alloys, composites, ceramics, silica glass, and metals. However, this cutting-edge technology is still relatively new and is best suited for large-scale production facilities that can invest in its advanced capabilities.
6. Laser Cladding
Fiber laser cladding is an advanced process that involves depositing a material—typically in powder or wire form—onto the surface of another material. This technique serves to coat mechanical components, effectively repairing and protecting them.
In this process, the fiber laser generates a melt pool on the surface of the base material, where the metallic powder is introduced and subsequently bonds with the substrate. The precision of this technique is remarkable, as the laser allows for highly controlled heating and accuracy in positioning.
One of the standout features of laser cladding is that the bond formed between the deposited layer and the base material is at the metallurgical level, resulting in a bond that is often stronger and more durable than traditional methods like spraying or plating. This makes fiber laser cladding an ideal choice for enhancing the longevity and performance of critical components.
Fiber Laser in Various Industrial Applications
1. Electronics and Semiconductors
The electronics and semiconductor industry requires precision, usually on a microscopic level, which is very hard to achieve using traditional manufacturing processes. Fiber laser machines, on the other hand, are perfect for such applications. That’s why we are seeing technology keep shrinking in size while at the same time hosting extraordinary processing power.
2. Automotive, Aerospace, and Marine Industry
Cars, airplanes, ships, and trains are continuously advancing, and the demand for more efficient machines is increasing. With fiber laser’s supreme cutting and welding capabilities, we see technology in such industries boom rapidly. Nowadays, fiber lasers are used for welding the titanium skin of aircraft, which is a necessary process.
Apart from ytterbium (Yb3+) doped fiber lasers, others like Tm3+ and Ho+3 pump laser diodes also work great on non-metal and transparent material, respectively.
Fiber lasers have increased the machining process’s efficiency, resulting in higher profits and shorter lead times. It also helped reduce the cost of end products for the customers.
3. Medical Industry
Medical equipment manufacturing usually has a minute error because it directly affects human lives. Fiber laser is best suited for such an industry because of its precise and high-quality manufacturing capabilities.
Other than that, lasers are also used to treat cancerous cells and remove stones from human organs. The applications of optical fiber lasers in the medical field are vast and continuously evolving.
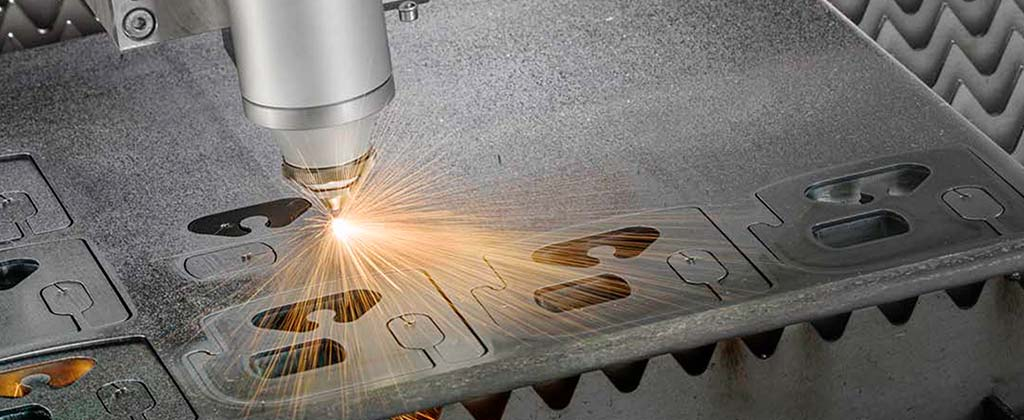
What to Look for in a fiber laser?
Laser source
Fiber lasers exhibit variations based on the material mixed with the laser source. Several examples include ytterbium-doped fiber lasers, thulium-doped fiber lasers, and erbium-doped fiber lasers. These distinct types of fiber lasers are employed for diverse applications due to their ability to generate different wavelengths.
Mode of operation
Various types of lasers emit laser beams in different ways. Laser beams can be generated through pulsed fiber lasers, which operate by pulsing at a specific repetition rate to achieve high-peak powers. This is commonly observed in lasers known as "q-switched," "gain-switched," and "mode-locked" lasers. On the other hand, laser beams can also be continuous, meaning they continuously emit a consistent amount of energy. This continuous emission is typically seen in lasers called "continuous-wave fiber lasers."
Laser power
The power of a laser is measured in watts and indicates the average power of the laser beam. For instance, there are 20W fiber lasers, 60W fiber lasers, and various other power options available. A high-power laser has the capability to generate energy at a faster rate compared to low-power lasers.
Mode
The mode of an optical fiber refers to the size of the core through which light travels. There are two categories of modes: single-mode fiber lasers and multi-mode fiber lasers. In single-mode lasers, the core diameter is smaller, typically ranging between 8 and 9 micrometers. Conversely, multi-mode lasers have a larger core diameter, usually between 50 and 100 micrometers. As a general guideline, single-mode lasers are more efficient in conveying laser light and exhibit superior beam quality compared to multi-mode lasers.
Why Choose KRRASS Laser Machines for Fiber Laser Applications?
The remarkable advantages of fiber lasers are well-known, and an increasing number of manufacturers are adopting laser technology every day. However, the market is also filled with subpar laser machines that could negatively impact your business. Fortunately, KRRASS has you covered.
Our KRRASS laser machines are renowned for their exceptional quality, durability, and cost-effectiveness. Our diverse catalog features a wide range of products, including laser cutting, welding, marking, and cleaning machines.
With a dedicated team of experts, we can help you select the perfect machine to meet your specific needs, ensuring timely delivery of high-quality products within your budget. Request your quote today!