Fiber Laser Cutting Machine
Fiber laser cutting machine are advanced computer-controlled devices that utilize a laser beam to precisely cut and engrave various materials, including metal, plastic, wood, and paper. The laser beam is skillfully directed onto the material's surface, inducing processes like melting, burning, or vaporization to craft intricate patterns or designs. These cutting-edge machines find widespread applications in diverse industries, including manufacturing, engineering, and graphic design, thanks to their exceptional precision, speed, and versatility compared to traditional cutting methods.
Notably, laser cutting machines excel in handling complex and intricate designs that may prove challenging or impossible with alternative techniques. Their key advantage lies in the precision and accuracy achieved through precise laser beam control, enabling clean cuts with minimal deviation. Beyond precision, these machines boast high-speed capabilities, facilitating efficient high-volume production. Moreover, their operations generate minimal waste due to the clean and precise nature of the cuts, thereby reducing the need for additional processes like grinding or sanding.
In the realm of laser cutting control solutions, KRRASS stands as a reliable provider, delivering world-class hardware and software solutions. Our turnkey approach introduces robust automation to support high-performing machines. Features such as height following maximize machine working time, while intelligent mechanisms actively navigate over cut parts, preventing collisions and errors in path planning. Elevate your production capabilities with KRRASS - a leader in delivering powerful solutions to the laser cutting control market.
Get in touch
If you have any questions, please contact us, we will get back to you as soon as possible.
Phone
+86 189 5208 7956
Location
Nanjing, Jiangsu, China
Social
Structural features
Laser Cutting Controller
In the realm of precision manufacturing, the dedicated bus CNC control system for laser cutting emerges as a pinnacle of technological innovation. Tailored specifically for the unique intricacies of laser cutting processes, this advanced system provides a seamless and efficient solution. Businesses seeking unparalleled precision and control in their manufacturing workflows find in this dedicated bus CNC control system a reliable ally, ensuring optimal performance and enhanced capabilities in the realm of laser cutting.
Model | Power | Application | Perforation | Features | Exchange workbench |
---|---|---|---|---|---|
FSCUT1000S | 1000~1500W | Low power board system | 2-stage | Simple layout; Fly-cut | X |
FSCUT2000C | 1000~4000W | Low and medium power board system | Simple layout; One click to cut off; Automatic edge finding; Fly-cut | ||
FSCUT3000S | 1000~4000W | Tube Cutting Control System | Channel steel cutting; Cut corners individually; Automatic loading and unloading; All functions of FSCUT2000 | ||
FSCUT2000E | 1000~6000W | Low and medium power Laser Cutting Control System | One click to cut off; Envelope border; One stroke flying cut; Disc centering | √ | |
FSCUT3000DE | 1000~6000W | 1-chuck tube laser cutting EtherCAT controller | Sort by Face; Centering mechanism; Missed cut prevention; Fly-cut | ||
FSCUT4000E | 1.5KW-8KW | Close Loop Laser Cutting Control System | Insensitive perforation; Traceless micro-connection; Disc centering; One stroke flying cut; Scan code to read pictures; Envelope border | ||
FSCUT5000 | 1000~6000W | Tube Cutting Control System | Zero-tail Cutting; 7-Axis Pulling; Bevel Cutting; 3-Chuck Cutting; 4-Chuck Cutting | ||
FSCUT6000 | 6-15KW | High Power EtherCAT Bus System | Insensitive perforation; Traceless micro-connection; Disc centering; Lightning piercing; Perforation and slag removal; Intelligent vibration suppression | ||
FSCUT7000 | 1000~4000W | Precision Laser Cutting Control System | Technique of transition line; Lead line; Fly-cut; Speed turning point; Speed adjust in curve position | ||
FSCUT8000 | ≥8KW | Ultra High Power EtherCAT Bus System | 9-stage | Smart knife closing; Traceless micro-connection; Automatic switchback; Melt pool inspection; Smart perforation |
Learn More >>
Smart Cutting Head
Revolutionizing laser cutting, the Smart Cutting Head integrates intelligent features for enhanced precision. With advanced sensors and real-time monitoring, it dynamically adapts to materials, optimizing cutting parameters. This compact solution seamlessly automates processes, ushering in a new era of accuracy in laser cutting applications.
Model | Power | Application | Fiber Interface | Features |
---|---|---|---|---|
BLT3 | ≤4kW | Small and medium power cost-effective smart cutting head | QBH / EOC | Mirror set drawer style design; Crash protection; Protective mirror contamination monitoring; Air pressure monitoring; IP64 protection level |
BLT4 | ≤30kW | Cost-effective smart cutter that focuses on 2D, 3D and bevel cutting machine | QBH / EOC / Q+ / QD / ADD | Stable and Efficient Cutting; Easy to Maintain; Low Cost to Repair; Smart and Safe Processing |
BLT5 | ≤15kW | Smart cutters for high-power tube cutting | QBH / EOC / Q+ / QD / ADD | Bevel Cutting; Right Angle Cutter; Protective Screws; Gas Pressure Monitor; Internal Amplifier |
BLT6 | ≤40kW | For ultra-high power laser equipment | QBH / Q+ / QD / ADD | Stable and Efficient Cutting; Smart Piercing; Slag-free Cutting; Easy to Maintain; Low Cost to Repair; Smart and Safe Processing; Protective Lens Monitor |
Learn More >>
Laser Cutting Machine Video
Transform your cutting procedures with state-of-the-art Fiber Laser Cutter Technology
Laser Cutting Machine Blog
Discover the capabilities of your laser cutting machine: An in-depth guide to laser cutting technology
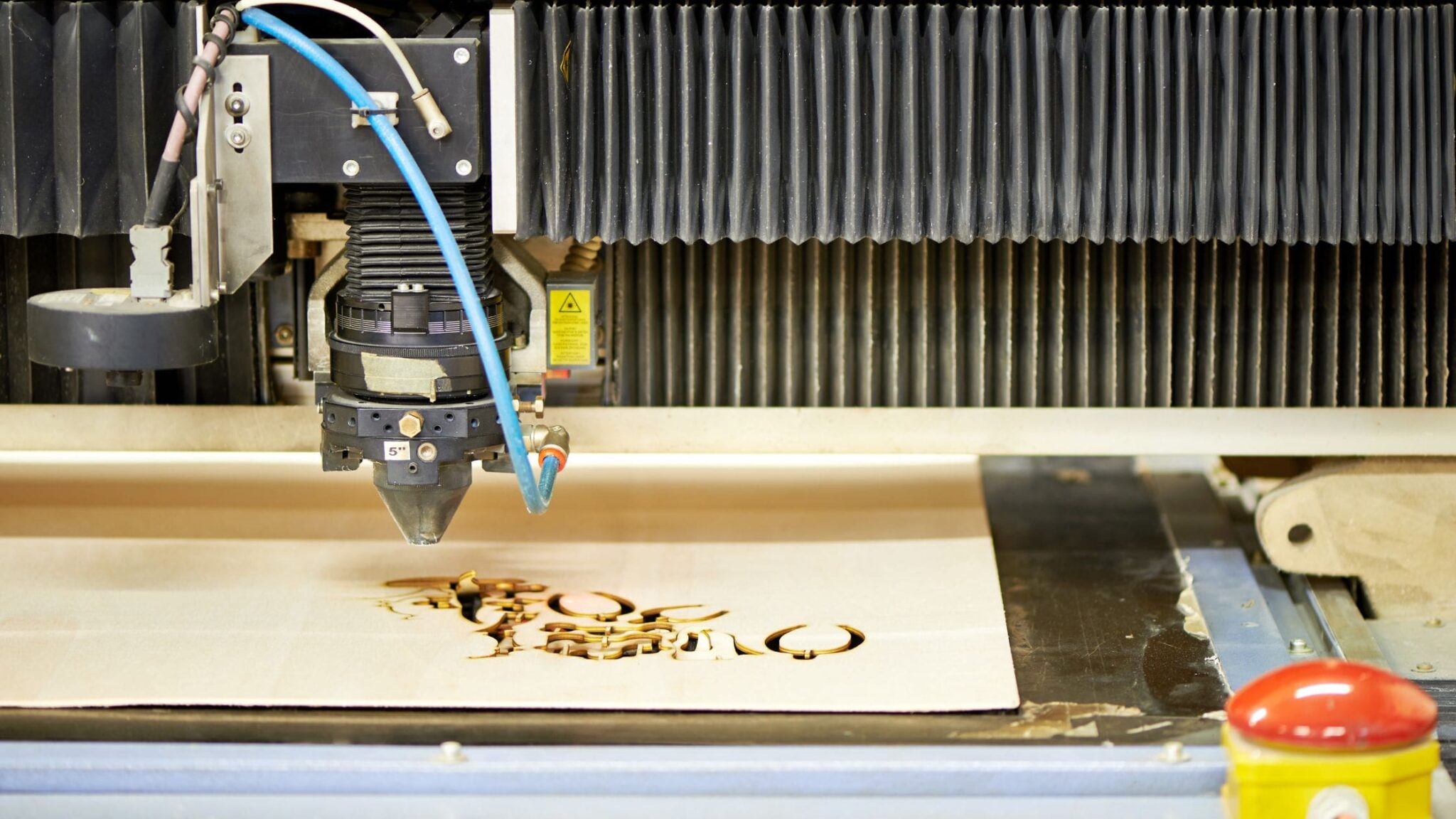
Laser Cutting Kerf: A Comprehensive Guide
krrass
In precision manufacturing, laser cutting represents the epitome of accuracy and efficiency. This guide delves ...
Read more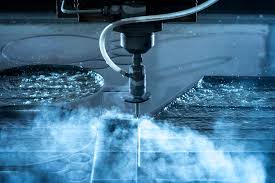
Water Jet Cutting vs Fiber Laser Cutting: What’s the Difference
krrass
In the contemporary manufacturing and fabrication landscape, achieving precision and efficiency is non-negotiable. Selecting the ...
Read moreLaser Cutting Machine FAQ
How to Solve The Difficulties of Fiber Laser Cutting Machine?
Cutting Speed
Fast cutting speed is one of the advantages of laser cutting, but the cutting speed is not as fast as possible.
Watch The Cutting Sparks
When the cutting speed is appropriate, the cutting sparks are more evenly spread from top to bottom;
Observe The Cutting Sheet
When the cutting speed is appropriate, the cutting surface presents a relatively smooth line, and no slag is produced in the lower half.
Nozzle And Nozzle Height
The nozzle acts as a beam and auxiliary gas channel. The shape, aperture, and nozzle height of the nozzle will affect the cutting effect.
Protective Gas Pressure
The size of the auxiliary gas pressure also affects the cutting effect of the fiber laser cutting machine. Adjusting the air pressure can also improve the cutting effect:
Precautions For Turn Off The Fiber Laser Cutting Machine
First, move the cutting head to the highest point, and stop the X and Y axes at the safe position. Swap the bench or stop the bench in a safe location.
How to Choose The Laser-Arc Hybrid Welding Machine?
Technical Background
Welding of medium and large thickness steel plates is mainly used in rail transit, shipbuilding, nuclear power equipment, and other industries.
Technical Characteristics
There are many forms of laser-arc hybrid welding, including Laser-MAG/MIG hybrid welding, Laser-TIG hybrid welding, laser-plasma arc hybrid welding, etc.
Applications
Aluminum Alloy Welding
Requirements: tailored welding of 5 mm and 6 mm aluminum alloys requires good weld formation and no undercut defects.
Welding of Medium And Thick Ship Plates
Requirements: Tailored welding of AH36 marine steel plates with thicknesses of 6 mm and 12 mm requires that the weld formation and weld quality meet the requirements of the Chinese Shipbuilding Quality Standard (GB/T 34000-2016).
Large Thickness Ship Plate Multi-Pass Welding
Requirements: 20 mm, 25 mm thick ultra-high-strength marine steel plates are tailor-welded, and the weld formation and weld quality are required to meet the requirements of the Chinese shipbuilding quality standard (GB/T 34000-2016).
Equipment And Process Parameter Suggestion
At present, for the laser-arc hybrid welding technology, there are very few practical applications in China, and there is no systematic achievement for the time being.